Injection molding is one of the technologies that makes the world go round. But what does it actually look like to go through the whole process to get a part made? [Achim Haug] wrote up a blog post that does a fantastic job of explaining what to expect when getting plastic enclosures injection molded in China.
Injection molding a part requires making a custom mold, which is then used by an injection molding machine in a shop to crank out parts. These are two separate jobs, but in China the typical business model is for a supplier to quote a price for both the mold as well as the part production. [Achim] describes not only what navigating that whole process was like, but also goes into detail on what important lessons were learned and shares important tips. Emergency Glass Breaking Hammer
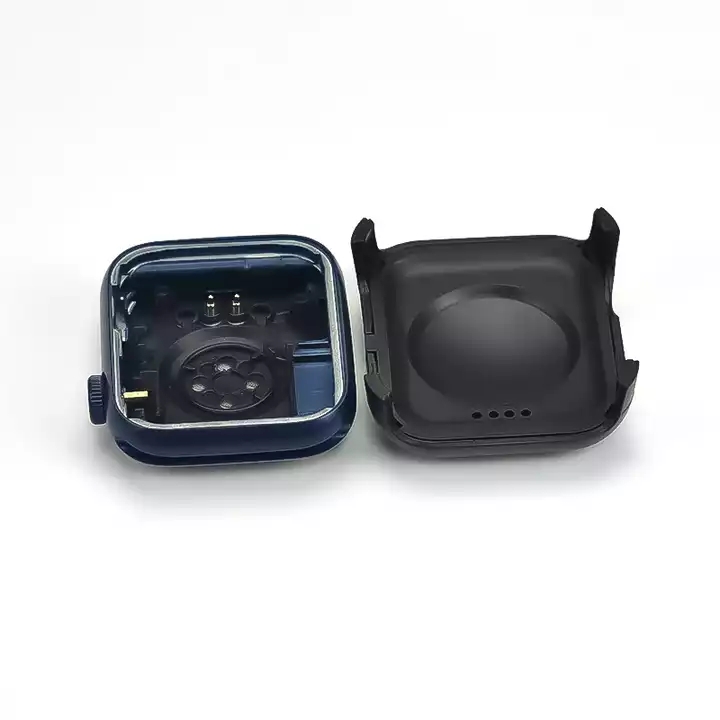
One of the biggest takeaways is to design the part with injection molding in mind right from the start. That means things like avoiding undercuts and changes in part thickness, as well as thinking about where the inevitable mold line will end up.
[Achim] found that hiring a been-there-done-that mold expert as a consultant to review things was a huge help, and well worth the money. As with any serious engineering undertaking, apparently small features or changes can have an outsized impact on costs, and an expert can recognize and navigate those.
In the end, [Achim] says that getting their air quality monitor enclosures injection molded was a great experience and they are very happy with the results, so long as one is willing to put the work in up front. Once the mold has been made, downstream changes can be very costly to make.
[Achim]’s beginning-to-end overview is bound to be useful to anyone looking to actually navigate the process, and we have a few other resources to point you to if you’re curious to learn more. There are basic design concerns to keep in mind when designing parts to make moving to injection molding easier. Some injection molding techniques have even proven useful for 3D printing, such as using crush ribs to accommodate inserted hardware like bearings. Finally, shadow lines can help give an enclosure a consistent look, while helping to conceal mold lines.
Had this in my Bachelor as a class. It was in a university of applied sciences (in German Fachhochschule). We had Draw in CAD and had to Made Test Samples in the injection milder.
I was involved with the design of injection molded parts. I found the entire process fascinating. The types of polymers, blends and additives is mind boggling. The tool making process is interesting in its own right. That’s where I first learned what EDM is. And yes an experienced mold designer IS required to help you optimize your design and save money because tools are expensive and complicated tools are very expensive. The first lesson you learn is that turds have taper and molds have draft. 🤣
given the long hours it takes to make molds, it makes sense to have a good selection of Electronic Dance Music on hand!
Terrible music will make you rush things. Very expensive. Worse: The usual method to cope with disco is very hard drugs. Friends don’t let friends operate machine tools when on very hard drugs.
Disco? You’re 50 years behind. Also, anyone who assumes that people who listen to a particular type of music are on drugs, is probably on drugs. (How’s that for a repeat of your logical fallacy?)
Imagine missing the jokes so hard you much reach Bennu.
VNV Nation; perfect injection mold design music!
It was a fun job. Scary hot. Pressurized hoses that flail. Saw a guy saw off his finger in the regrind room. Ran everything from surgical trays to beer pallets.
The term ‘rapid prototyping’ coined by 3Dsystems was to 3dprint parts to iron out problems prior to tool making for production, many companies adopted it, because fixing problems later is expensive.
Yeah, but 3d printed parts don’t have the same weird requirements and kinks as molded parts do, so you’d still need some experience to successfully translate to that manufacturing process
Of course, Cad,RP, simulation are all tools that help, but knowledge and experience are essential for success.
So true. No good designer will rely solely on FE flow analysis. Understanding the subtleties of vents, gates, thermals, materials, cycle times etc. is an art.
SLS 3d printing is used in making some mold components. Previously impossible to achieve; placing water cooling paths into the mold, close to the parting line.
Look at the graphic…that’s one cheesy flow simulation.
The cold well is hot!
The term ‘rapid prototyping’ predates 3d printing. All ‘prototypes’ better be pretty rapid, slow iteration sucks…prototype tooling less so.
You can make mold inserts out of aluminum first. Sure the thermals change vs steel final versions, but so much cheaper. Just short lived. Also, hard anodize. Some maniacs even plastic 3d print test mold inserts, then weaker plastic test shots. Vices, buckets and fingers for part extraction.
If you need less than 100,000 plastic parts, aluminum tooling makes all kinds of sense. However: It’s much easier for an idiot to ruin the tooling in production. One screwdriver ‘popping out’ one stuck part. Get 2 sets of aluminum inserts cut and anodized, they’re ‘cheap’…vs the Engineering cost and/or production downtime. Aluminum is great heat conductor! Rapid cycle time. You can get away with no cooling passages in the inserts, might not want to. Will need hard metal gates, pins and sleeves.
Some comments in the thread on HN have some value, worth looking at if you are in the business: https://news.ycombinator.com/item?id=37785513
Saw this a few days ago, and was impressed by the cable run clips not having overhangs
Hi, I used to design car instrument panels and now lead development teams doing similar. As with anything in life experience is key and paying for advice if you have little or no experience WILL be worth it in the long run hiring experienced designers will normally catch most DFM issues before they happen. For a little context to designing an instrument panel moulding we would be looking at a part 1600-1700mm X 1000mm X 1000mm shot wait up to 3kg. To design that I would have a full time very experienced CAD head designing that single part for 12-18 months . You can do it quicker but that would be a completely clean sheet package to workout. Tooling wise we would be looking at between 14-18 weeks tooling to first off parts. Further work would still be required after that although last I heard sourcing the steel was taking about that long as well although it maybe better now. For those starting designing A plastic part two tips would be from day 1 understand your main die line everything else will be based off of it and understand the finish you would like on any customer visible surfaces as that will define you minimum draft requirements.
Ha! Making moulds in China is fun. Masochistic kind of fun, to be sure, if you’re looking for reasonable price. And it ALWAYS pays to have both specialist in injection moulding and an engineer responsible for the final assembly with you when you’re ordering the tooling, and someone who knows how manufacturing in China works is sorely needed as well. No beancounters should be let anywhere near the process because that’s how you get multiple rework on your tooling. Also, the’ll distract you from all the shenanigans going on. And there WILL be shenanigans. We had all kinds of fun: Tooling not produced after two years, tooling working perfect… but only with the mix of waste plastic this particular shop has about half a ton sitting in a corner (and nothing else would produce the desired outcome!), tooling producing perfect items… only when cooling is not connected, and for only first 6 runs. And having someone who actually works with these machines was invaluable (as in ‘saving thousands of dollars and months of time and millions of nerve cells’ invaluable).
At what point do you just establish an in house mould making workshop? sounds like so much less hassle.
Please be kind and respectful to help make the comments section excellent. (Comment Policy)
This site uses Akismet to reduce spam. Learn how your comment data is processed.
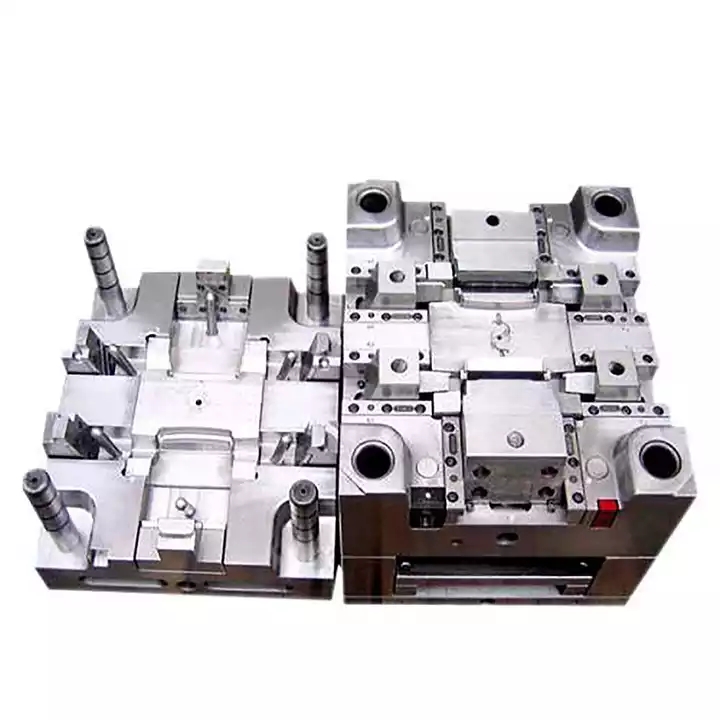
Precision Plastic Injection Moulding By using our website and services, you expressly agree to the placement of our performance, functionality and advertising cookies. Learn more