This article provides an in-depth review of the best tennis elbow straps available on the market. Tennis elbow is a common condition that can cause discomfort and decrease performance. Tennis elbow straps are designed to alleviate pain and prevent further injury, allowing athletes to continue playing. The article outlines the criteria used to select the best straps, including materials, adjustability, comfort, and effectiveness. Customer reviews and feedback were also considered. The article also highlights the importance of finding the right fit and incorporating exercises into your routine. The upcoming sections will reveal the top-ranking products.1Bodyprox Elbow Brace 2 Pack for Pain Relief Bodyprox Elbow Brace 2 Pack for Pain Relief View on Amazon 9.8 The Bodyprox Elbow Brace 2 Pack is a must-have for anyone suffering from tennis or golfer's elbow pain. Made with high-quality materials, these elbow braces provide excellent support and pain relief. They are easy to wear and adjust, and can be worn during any physical activity. The pack includes two braces, so you can use them on both elbows or keep a spare. Whether you're an athlete or someone who suffers from elbow pain due to repetitive motions, the Bodyprox Elbow Brace 2 Pack is a great investment in your health and well-being.Rated 9.8 based on 10 JPOST ProsEffective pain relief, Comfortable to wear, Durable and long-lastingConsMay be bulky for some2SS Sleeve Stars Tennis Elbow Brace SS Sleeve Stars Tennis Elbow Brace View on Amazon 9.7 The Sleeve Stars Tennis Elbow Brace is a great solution for anyone suffering from tennis elbow or tendonitis. This elbow strap is designed to provide targeted support to the affected area, helping to relieve pain and discomfort. The brace comes with three forearm support straps, making it easy to adjust to fit any size arm. Made with high-quality materials, this elbow band is durable and long-lasting. Whether you're a professional athlete or just someone dealing with occasional elbow pain, the Sleeve Stars Tennis Elbow Brace is a must-have for anyone looking for relief.Rated 9.7 based on 10 JPOST ProsProvides pain relief, Adjustable fit, Includes forearm strapsConsMay not fit all sizes3SENTEQ Elbow Brace Support Strap Grey SENTEQ Elbow Brace Support Strap Grey View on Amazon 9.5 The SENTEQ Elbow Brace Support Strap is an excellent option for anyone in need of forearm compression and support during physical activity. Designed for both men and women, this tennis elbow brace is perfect for weightlifting, tennis, golf, and other sports that put pressure on the elbow joint. The grey 1-pack compression sleeve is made with high-quality materials that provide effective pressure relief and support for sports injury recovery. Lightweight and comfortable, this elbow brace is a must-have for athletes looking to take care of their elbows during physical activity.Rated 9.5 based on 10 JPOST ProsProvides excellent compression, Comfortable to wear, Versatile for various activitiesConsMay not fit larger forearms4FREETOO Elbow Brace with Removable Pad FREETOO Elbow Brace with Removable Pad View on Amazon 9.3 The FREETOO Elbow Brace is a must-have for anyone suffering from tendonitis or tennis elbow. With its adjustable straps and removable pad, it provides customizable and comfortable relief. Perfect for both men and women, this elbow brace is also great for golfers looking to alleviate elbow pain. Made with high-quality materials, it's durable and long-lasting. Say goodbye to elbow pain and discomfort with the FREETOO Elbow Brace.Rated 9.3 based on 10 JPOST ProsAdjustable and comfortable, Removable pad included, Effective pain reliefConsMay not fit all sizes5POWERLIX Elbow Brace Compression Support (Pair) Black Medium POWERLIX Elbow Brace Compression Support (Pair) Black Medium View on Amazon 9.1 The POWERLIX Elbow Brace Compression Support is the perfect solution for those suffering from elbow pain caused by tendonitis, arthritis, or sports-related injuries. This pair of elbow sleeves provides targeted compression to reduce pain and inflammation, while also improving circulation and promoting faster recovery. Whether you're an athlete, weightlifter, or simply looking for relief from daily elbow strain, these sleeves are a must-have. Made with high-quality materials, they are durable, comfortable, and easy to wear for extended periods. Get back to doing the activities you love with the POWERLIX Elbow Brace Compression Support.Rated 9.1 based on 10 JPOST ProsProvides compression support, Reduces elbow pain, Suitable for various activitiesConsMay not fit all sizes6MOONSMILE Tennis Elbow Braces Pair MOONSMILE Tennis Elbow Braces Pair View on Amazon 8.8 The MOONSMILE Tennis Elbow Braces are a great solution for those suffering from tendonitis or tennis elbow. This neoprene wrap provides support and relief for the elbow and forearm, making it perfect for athletes and those with active lifestyles. This one size fits all brace is easy to use and can be worn comfortably all day long. Say goodbye to elbow pain and discomfort with the MOONSMILE Tennis Elbow Braces.Rated 8.8 based on 10 JPOST ProsDurable neoprene material, Adjustable straps for perfect fit, Provides relief for elbow painConsMay not fit all sizes7Rymora Elbow Support Arm Compression Sleeves Rymora Elbow Support Arm Compression Sleeves View on Amazon 8.7 The Rymora Elbow Support Arm Compression Sleeves provide targeted compression and support for the elbow joint, making them perfect for athletes, fitness enthusiasts, or anyone suffering from elbow pain. Made with high-quality materials, these sleeves are durable and comfortable to wear during workouts or throughout the day. Available in multiple sizes, they come in a sleek slate grey color and are sold in pairs. Whether you're looking to prevent injury or alleviate discomfort, the Rymora Elbow Support Arm Compression Sleeves are a great choice for anyone in need of extra support and protection for their elbows.Rated 8.7 based on 10 JPOST ProsComfortable compression, Breathable fabric, Provides great supportConsMay run small8Aircast Pneumatic Armband Tennis Golfers Elbow Support Strap Beige Aircast Pneumatic Armband Tennis Golfers Elbow Support Strap Beige View on Amazon 8.4 The Aircast Pneumatic Armband is a must-have for anyone suffering from tennis or golfer's elbow. The adjustable strap provides targeted pressure to the affected area, helping to relieve pain and discomfort. Made with high-quality materials, this support strap is both durable and comfortable to wear. Whether you're an athlete or someone who suffers from repetitive strain injuries, the Aircast Pneumatic Armband is an excellent choice for reducing pain and promoting healing.Rated 8.4 based on 10 JPOST ProsEffective for pain relief, Adjustable fit, Comfortable to wearConsMay slip during activities9AGPTEK Elbow Brace 2 Pack for Tendonitis and Tennis Elbow AGPTEK Elbow Brace 2 Pack for Tendonitis and Tennis Elbow View on Amazon 8.2 The AGPTEK Elbow Brace for Tendonitis and Tennis Elbow 2 Pack is designed to provide pain relief and support for those suffering from tennis elbow, golfer's elbow, and other types of elbow pain. Made from high-quality materials, these elbow braces are comfortable to wear and provide compression to help reduce inflammation and pain. The compression pad is strategically placed to provide targeted support where you need it most. Whether you're an athlete, weightlifter, or just someone who suffers from elbow pain, the AGPTEK Elbow Brace is a great choice for anyone looking for relief.Rated 8.2 based on 10 JPOST Pros2 pack for value, compression pad for support, suitable for various activitiesConsmay not fit all sizes10Mueller Hg80 Premium Tennis Elbow Black L/XL Mueller Hg80 Premium Tennis Elbow Black L/XL View on Amazon 7.9 The Mueller Hg80 Premium Tennis Elbow brace is a must-have for anyone suffering from tennis elbow. Made with high-quality materials, this brace provides excellent support and compression to the affected area, reducing pain and inflammation. Lightweight and comfortable, it can be worn for extended periods of time without causing discomfort. Available in black, and in sizes large/X-large, this brace is perfect for anyone looking for relief from tennis elbow.Rated 7.9 based on 10 JPOST ProsPremium quality material, Effective for tennis elbow, Comfortable to wearConsMay not fit all sizesFAQ
The Bodyprox Elbow Brace 2 Pack is a must-have for anyone suffering from tennis or golfer's elbow pain. Made with high-quality materials, these elbow braces provide excellent support and pain relief. They are easy to wear and adjust, and can be worn during any physical activity. The pack includes two braces, so you can use them on both elbows or keep a spare. Whether you're an athlete or someone who suffers from elbow pain due to repetitive motions, the Bodyprox Elbow Brace 2 Pack is a great investment in your health and well-being.Rated 9.8 based on 10 JPOST ProsEffective pain relief, Comfortable to wear, Durable and long-lastingConsMay be bulky for some Pipe Clamp Fittings

The Sleeve Stars Tennis Elbow Brace is a great solution for anyone suffering from tennis elbow or tendonitis. This elbow strap is designed to provide targeted support to the affected area, helping to relieve pain and discomfort. The brace comes with three forearm support straps, making it easy to adjust to fit any size arm. Made with high-quality materials, this elbow band is durable and long-lasting. Whether you're a professional athlete or just someone dealing with occasional elbow pain, the Sleeve Stars Tennis Elbow Brace is a must-have for anyone looking for relief.Rated 9.7 based on 10 JPOST ProsProvides pain relief, Adjustable fit, Includes forearm strapsConsMay not fit all sizes
The SENTEQ Elbow Brace Support Strap is an excellent option for anyone in need of forearm compression and support during physical activity. Designed for both men and women, this tennis elbow brace is perfect for weightlifting, tennis, golf, and other sports that put pressure on the elbow joint. The grey 1-pack compression sleeve is made with high-quality materials that provide effective pressure relief and support for sports injury recovery. Lightweight and comfortable, this elbow brace is a must-have for athletes looking to take care of their elbows during physical activity.Rated 9.5 based on 10 JPOST ProsProvides excellent compression, Comfortable to wear, Versatile for various activitiesConsMay not fit larger forearms
The FREETOO Elbow Brace is a must-have for anyone suffering from tendonitis or tennis elbow. With its adjustable straps and removable pad, it provides customizable and comfortable relief. Perfect for both men and women, this elbow brace is also great for golfers looking to alleviate elbow pain. Made with high-quality materials, it's durable and long-lasting. Say goodbye to elbow pain and discomfort with the FREETOO Elbow Brace.Rated 9.3 based on 10 JPOST ProsAdjustable and comfortable, Removable pad included, Effective pain reliefConsMay not fit all sizes
The POWERLIX Elbow Brace Compression Support is the perfect solution for those suffering from elbow pain caused by tendonitis, arthritis, or sports-related injuries. This pair of elbow sleeves provides targeted compression to reduce pain and inflammation, while also improving circulation and promoting faster recovery. Whether you're an athlete, weightlifter, or simply looking for relief from daily elbow strain, these sleeves are a must-have. Made with high-quality materials, they are durable, comfortable, and easy to wear for extended periods. Get back to doing the activities you love with the POWERLIX Elbow Brace Compression Support.Rated 9.1 based on 10 JPOST ProsProvides compression support, Reduces elbow pain, Suitable for various activitiesConsMay not fit all sizes
The MOONSMILE Tennis Elbow Braces are a great solution for those suffering from tendonitis or tennis elbow. This neoprene wrap provides support and relief for the elbow and forearm, making it perfect for athletes and those with active lifestyles. This one size fits all brace is easy to use and can be worn comfortably all day long. Say goodbye to elbow pain and discomfort with the MOONSMILE Tennis Elbow Braces.Rated 8.8 based on 10 JPOST ProsDurable neoprene material, Adjustable straps for perfect fit, Provides relief for elbow painConsMay not fit all sizes
The Rymora Elbow Support Arm Compression Sleeves provide targeted compression and support for the elbow joint, making them perfect for athletes, fitness enthusiasts, or anyone suffering from elbow pain. Made with high-quality materials, these sleeves are durable and comfortable to wear during workouts or throughout the day. Available in multiple sizes, they come in a sleek slate grey color and are sold in pairs. Whether you're looking to prevent injury or alleviate discomfort, the Rymora Elbow Support Arm Compression Sleeves are a great choice for anyone in need of extra support and protection for their elbows.Rated 8.7 based on 10 JPOST ProsComfortable compression, Breathable fabric, Provides great supportConsMay run small
The Aircast Pneumatic Armband is a must-have for anyone suffering from tennis or golfer's elbow. The adjustable strap provides targeted pressure to the affected area, helping to relieve pain and discomfort. Made with high-quality materials, this support strap is both durable and comfortable to wear. Whether you're an athlete or someone who suffers from repetitive strain injuries, the Aircast Pneumatic Armband is an excellent choice for reducing pain and promoting healing.Rated 8.4 based on 10 JPOST ProsEffective for pain relief, Adjustable fit, Comfortable to wearConsMay slip during activities
The AGPTEK Elbow Brace for Tendonitis and Tennis Elbow 2 Pack is designed to provide pain relief and support for those suffering from tennis elbow, golfer's elbow, and other types of elbow pain. Made from high-quality materials, these elbow braces are comfortable to wear and provide compression to help reduce inflammation and pain. The compression pad is strategically placed to provide targeted support where you need it most. Whether you're an athlete, weightlifter, or just someone who suffers from elbow pain, the AGPTEK Elbow Brace is a great choice for anyone looking for relief.Rated 8.2 based on 10 JPOST Pros2 pack for value, compression pad for support, suitable for various activitiesConsmay not fit all sizes
The Mueller Hg80 Premium Tennis Elbow brace is a must-have for anyone suffering from tennis elbow. Made with high-quality materials, this brace provides excellent support and compression to the affected area, reducing pain and inflammation. Lightweight and comfortable, it can be worn for extended periods of time without causing discomfort. Available in black, and in sizes large/X-large, this brace is perfect for anyone looking for relief from tennis elbow.Rated 7.9 based on 10 JPOST ProsPremium quality material, Effective for tennis elbow, Comfortable to wearConsMay not fit all sizes
Q: What is a tennis elbow strap?
A: A tennis elbow strap is a support device that wraps around the forearm to alleviate pain and pressure caused by tennis elbow. It applies pressure to the forearm muscles, which helps relieve tension on the affected tendons.
Q: How can a tennis elbow strap help me?
A: A tennis elbow strap can help you by reducing pain and discomfort caused by tennis elbow. It can also help prevent further injury by stabilizing the affected area during physical activity. It is a non-invasive and affordable solution for those suffering from tennis elbow.
Q: How do I choose the right tennis elbow strap?
A: When choosing a tennis elbow strap, it is important to consider factors such as size, material, and adjustability. Look for a strap that fits comfortably and securely, without restricting movement. It should also be made of durable and breathable materials to ensure long-lasting use. Consider consulting with a healthcare professional to find the best option for your specific needs.Conclusions
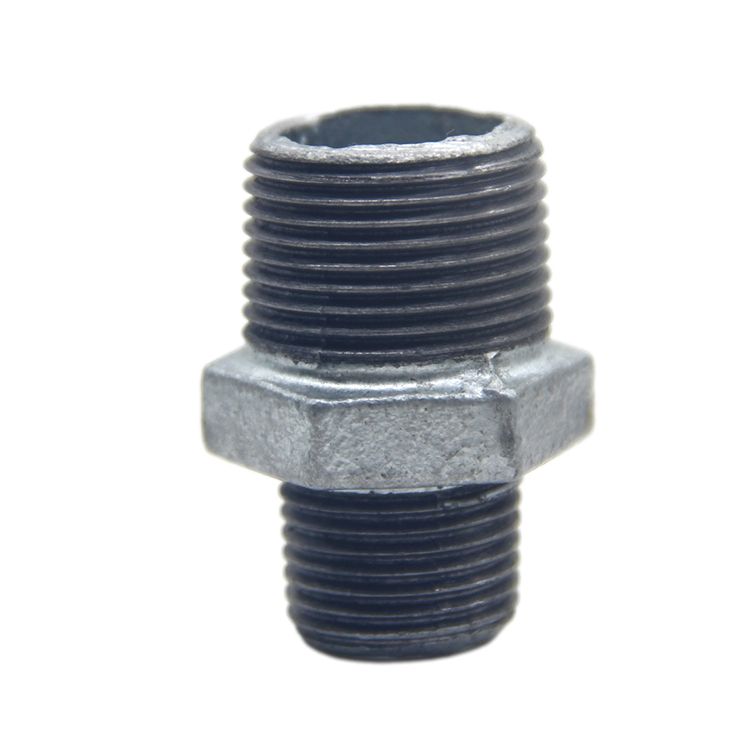
Rubber Soft Connection Joint After conducting extensive research and testing, we have found that tennis elbow straps are an effective solution for those suffering from tennis elbow, golfer's elbow, and other similar conditions. Each of the products reviewed provided varying levels of compression and support, but all proved to be helpful in reducing pain and discomfort. We recommend trying out one of the reviewed products to see which one works best for you and your specific needs. Don't let elbow pain hold you back from doing what you love - take action and try out a tennis elbow strap today.