In 1982, the El Niño effect was unusually strong. The water temperature in the equatorial Pacific was 7 °C higher than average. Thermal energy was released into the Earth’s atmosphere and global weather patterns were turned upside-down. In the same year, Robert Bloos Senior revolutionized heating with wood: the resourceful inventor developed a way of automatically charging boilers with wood chips. Today, the Franconian pioneers of Heizomat Gerätebau + Energiesysteme GmbH produce up to 1600 environmentally friendly, customized wood chip heating systems every year. In order to cope with the high order numbers, the boilers are welded using modern Fronius robotic welding cells.
Like many great success stories, that of former truck driver Robert Bloos Senior started in a garage. Even then it was clear that “we have to heat exclusively with wood,” but every time he came home in the winter after a hard day’s work, his apartment was cold. This is because, back in the 1970s, the only wood-burning stoves on the market had to be fired up manually during the day. If you weren’t home, there was no fire. Frustrated by this, he started tinkering around in his small workshop. Bloos wanted to burn the wood from his own trees to create the same level of comfort as a fossil fuel system. That’s why he decided to automate the charging of his stove. The result, after a huge amount of hard work, was a stunning world first: an automatic dispenser system for wood chips. Gantry Robot

As Convenient As Oil Heaters, but Easy to Maintain and Environmentally Friendly While the first wood chip heating systems boasting automatic feeding may have been developed in a garage, the German family business now manufactures them at two sites in Gunzenhausen and Heidenheim. With 330 employees and a real net output ratio of 85%, the company produces customized heating systems rated from 30 to 990 kW, with deliveries sent all over the world. Today, thousands of satisfied customers in over 40 countries use the reliable, low-maintenance systems of the inventive heating pioneer to heat their premises. Only the heat that is actually needed is generated, and from a climate-neutral, renewable source. And it’s not just customers in Europe, the USA, and Canada that trust in German quality: the company’s products can also be found as far away as Malaysia and New Zealand. Heizomat is ASME-certified for worldwide export. The certificate of the American Society of Mechanical Engineers is internationally recognized in over 100 countries. It certifies that the products meet the stringent requirements of the ASME code, including its safety standards.
Innovative and Environmentally Friendly Heating For a long time, wood chip heaters were only of interest to private consumers, local communities, and farmers. Today, however, commercial and industrial companies also benefit from the largely climate-neutral wood heating. Even wooden pallets “contaminated” with nails can be easily burned in Heizomat systems.
The disposal of residual wood costs money, even if it’s just for removal. Heating with wood waste not only saves on disposal costs, but also some of the procurement costs associated with new firewood. The resulting ash contains valuable minerals and can be used as a natural fertilizer, meaning you contribute to the circular economy, exactly in the spirit of the Bloos family: plant wood, harvest wood, burn wood, fertilize wood. In the language of Heizomat, this is affectionately known as the “wood chip cycle”.
As Manuel Vorbrugg, Production Manager at Heizomat, points out: “In addition to heating systems, we are the only manufacturer that supplies all the system components required for harvesting, chopping, and transport systems, including ash application and exhaust gas purification. Our latest innovation is our HeizoCont container system. This is a complete solution that brings the entire heating cycle together in a compact plug-and-play solution, from wood chip storage to ash application: install, connect, heat, without the need for any major conversion work. The container system is of particular interest to industrial and commercial customers, but also to municipal heating cooperatives.”
Always Future-Oriented Even during Welding Increasing skills shortages and continued growth mean that many companies, including Heizomat, require automated solutions. Today, the company uses three Fronius robotic welding cells to weld boilers. The cells are equipped with the Pathfinder offline programming and simulation software.
“Without automation, we would have to take on more qualified welders, but they’re few and far between on the labor market. That’s why we decided to use robotic systems,” Vorbrugg continues. “Fronius quickly reassured us. From the outset, the focus was on the welding challenge. The kinematics were designed on the basis of their solution and not the other way around. Today, we have three robotic welding cells with reversible positioners that do exactly what we want: reliably weld perfect seams.”
For the construction of the wood chip heaters, standard components (boilers) made of 6 mm hot-rolled, unalloyed S235JR structural steel and each weighing 700–950 kg are joined in a gas- and water-tight manner. Depending on the requirements, the number of individual components varies between 300 and 700.
Christoph Stieglitz, welding expert, has no doubts: “The Pulse Multi Control (PMC) process is perfect for welding steel boilers. In comparison to manual welding, we achieve significantly higher speeds of up to 80 cm/min with optimal root penetration. The seams are visually perfect and of a consistently high quality.”
PMC is a modified pulsed arc process that is characterized by a powerful, stable arc and finely controlled low-spatter droplet detachment that delivers a high deposition rate. Even components with tight tolerances and significant variations in wall thickness can be flawlessly welded using PMC. Arc length and penetration stabilizers ensure precise control and high process stability with less energy per unit length.
“Automated welding has clear advantages for us,” explains Vorbrugg. “Firstly, we can set up the systems in parallel, which avoids non-productive downtimes. Secondly, we weld much faster than by hand. Instead of 6 hours, the robot only needs 1 hour 40 minutes for each boiler. And thirdly, using the Pathfinder offline programming and simulation software means we spend significantly less time teaching the welding robot.”
Optimal Welding Sequence with Fronius Pathfinder The biggest plus when programming offline with Pathfinder is that all the welding sequences can be created away from the robot systems. Ongoing welding work no longer has to be stopped for programming. Simulators help detect potential errors in advance and optimize the welding sequences. For example, collisions, violations of axis boundaries, or singularities are recorded and visualized. Significant time savings are achieved in the copying, linking, grouping, and mirroring of welds. Welding simulations can be carried out in real time or at an infinitely variable speed with simultaneous cycle time determination (welding speed, gas pre-flow times, end-crater filling, etc.) If the welding robot were to be taught exclusively in the system, the amount of effort involved could be up to ten times greater.
Precise Welds—Gas-Tight Boilers “Our system consistently welds down the center of the weld,” explains Stieglitz. “This is achieved using an automatic weld search feature, which works as follows. The robot moves the welding wire up to the component, remembers the point, and stores its coordinates. As soon as all required points on the X, Y, and Z coordinates have been measured and recorded, they are compared with the virtual component and, if there are any deviations, the welding path is corrected accordingly.”
The exact position of the welds is a basic requirement if gas- and water-tight boilers are to be produced to the expected high levels of Heizomat quality. Each boiler is therefore subjected to a 24-hour leak test at 9–11 bar water pressure before it is installed in one of the world’s most sought-after wood chip heating systems. Visually flawless seams are equally important, especially in the USA, as the ASME standard demands 100% perfect welds even in the hidden parts of the boilers.
Everything under Control In addition to all the welding processes, the HMI T21-RS system control monitors and coordinates each of the components used in the robotic welding cell: robot, power source, reversible positioner, tool center point (TCP) measurement, and torch cleaning. Highlights include the Program Editor for defining all kinetic and welding processes as well as real-time 3D visualization. Since the Heizomat welding specialists need a good overview of the current system status and every part of the system, all modules and protected areas are visualized, depending on the respective status of the welding cell. The range of functions of the controls includes user and program administration, fault indicators, cycle and part counters, language switching, system status displays, and complete power management (supply of media).
“We’ve found the right partner in Fronius,” concludes Vorbrugg. “Just like us, environmentally friendly management is a top priority and problems are seen as challenges. In addition, there’s always someone on hand to help. Communication channels are short, and the collaboration is friendly and congenial. In short, it’s a company we can rely on. I’m convinced that our decision to opt for the innovative Austrian welding experts means we’re well equipped for the future.”
Manufacturing & Engineering Magazine | The Home of Manufacturing Industry News
Manufacturing & Engineering Magazine, abbreviated to MEM, is a leading UK engineering magazine and manufacturing news source, covering a wide assortment of industry news sectors such as: contract manufacturing, 3D printing, structural and civil engineering, automotive manufacturing, aerospace engineering, marine engineering, rail engineering, industrial engineering, CAD, schematic designs and more!
© 2023 MEM Magazine | The Home of Manufacturing Industry News
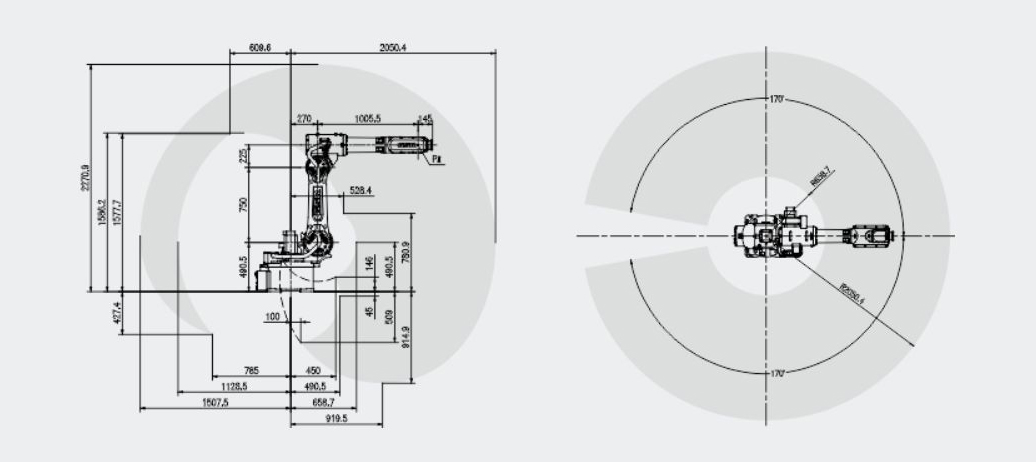
Industrial Robotic Arm © 2023 MEM Magazine | The Home of Manufacturing Industry News