By Kevin Keogh, Paradigm
The upstream oil and gas industry has experienced significant internal and external shocks and change during the past decade. Ranging from the advent of the US shale industry and its de-stabilizing effect on supply to the more recent policy uncertainties surrounding the pace of the transition to clean energy, changing market dynamics have forced many operating companies to re-evaluate their approach to growth, in order to manage these risks and preserve shareholder value. carbon fiber rods and tubes
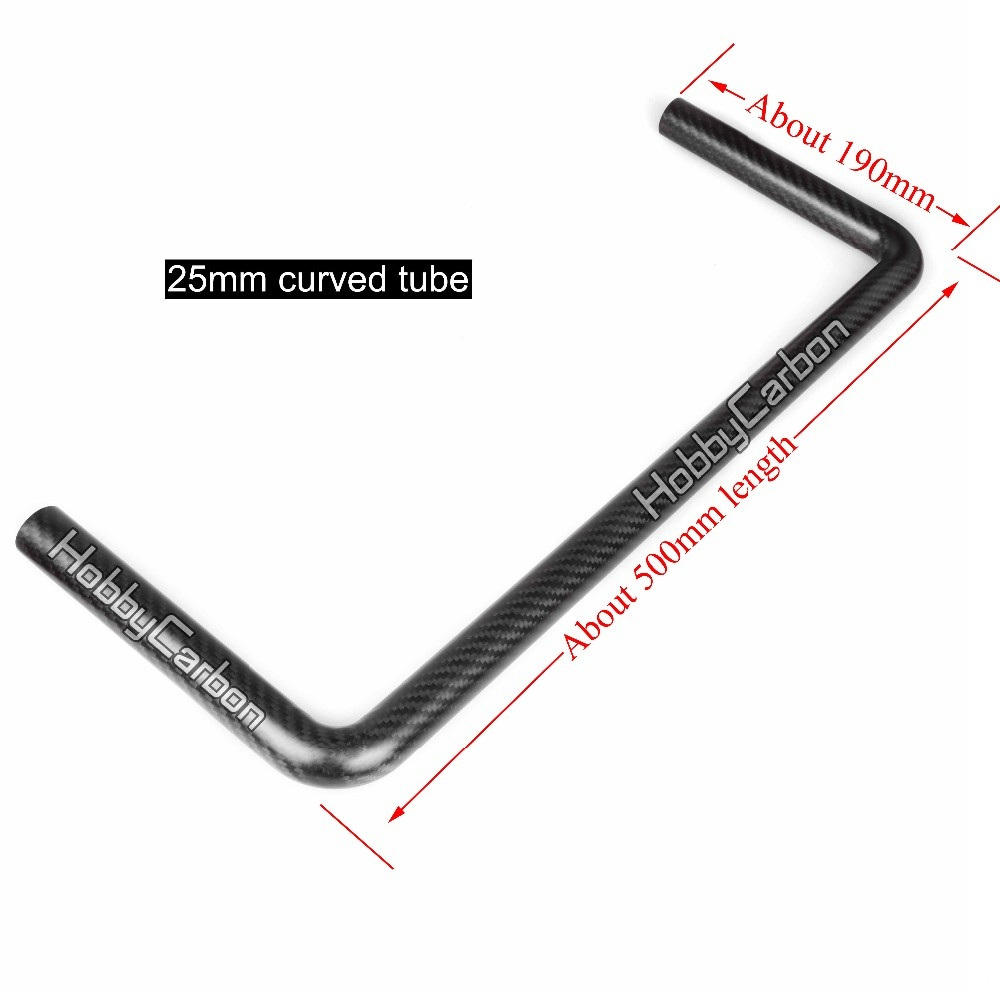
Increased capital discipline has emerged with a shift in focus from the pursuit of growth to reducing debt levels and returning cash to shareholders, which has undoubtedly affected how new fields are developed and how existing fields are optimized. This can be particularly well exemplified in the deepwater sector, where higher upfront capital expenditures and longer payback periods in comparison to more conventional oilfield developments are the norm and where the potential for stranded assets is therefore higher.
Two development strategies that have become more prevalent are the oversizing of production risers and flowlines and installation of single-flowline tiebacks. Increasing pipe internal diameter (ID) reduces pressure loss and therefore increases production rates in a well’s early-life phase, normally resulting in a shorter payback period. However, as the well enters its mid-life phase and rates decline, the larger ID of the riser-flowline system can exacerbate the effects of increased water production and reservoir pressure depletion. An example of this is the increased frequency and severity of liquid slugging, which can cause topsides process upsets that lead to reduced productivity.
Similarly, single versus dual-flowline developments deliver a significant reduction in capex and can make production from smaller satellite fields economic. However, this approach usually increases the likelihood of a future intervention requirement due to reduced operational flexibility. For example, this reduced operational flexibility can come from the inability to perform certain maintenance and prevention activities such as pigging and circulation, or the inability for flowline re-purposing to enable gas lift.
Composite coiled tubing (CCT) technology is uniquely capable of addressing many of these challenges. The CCT system in reference here can be described as a miniaturized and flexible coiled tubing technology that has been developed specifically for riser and flowline interventions. Its principal application and the majority of its usage history to date has been high-pressure liquid jetting for the remediation of solids deposits – including hydrates, paraffin wax, sand, and asphaltene – that form inside the production flowline and riser, and which lead to reduced or fully occluded system throughput. However, the CCT system can also be used for the installation of tubing permanently inside the production riser (PR).
These ‘in-riser’ installations enable either increased fluid velocity via a reduction in the cross-sectional area (i.e. an in-riser velocity string) or reduced system back-pressure via gas lift at or near the riser touchdown point (i.e. in-riser gas lift). Numerous production and flow assurance challenges often associated with mid and late-life wells, such as slugging and pressure depletion, can be alleviated with these artificial lift techniques.
This solution has been applied extensively as a low-cost, retrofit artificial lift solution on several platforms in the US Gulf of Mexico (GoM), primarily on spar facilities which have the direct vertical access (DVA) into the PR. DVA is required for in-riser steel tubing installation using conventional coiled tubing (CT) systems, where the high minimum bend radius (MBR) of the steel tubing prevents it from being run through the short radius pipe bends that can often be encountered on topsides prior to entry into the PR. Unlike spar platforms, which represent only 13% of the deepwater production facility asset base globally and are concentrated in the US GoM, the majority of deepwater production facilities (i.e. FPSOs and semisubmersible production platforms) do not have DVA to the PR, thus, preventing or greatly complicating the application of the in-riser solution.
A conventional solution might use a temporary riser system (shown in red) connecting a CT system to a vertical tubing hanger that has been installed beneath the waterline at the PR hang-off on the pontoon. The steel tubing is then run from the surface through the temporary riser on a temporary work-string and landed-off in the hanger which holds it permanently in place. If gas lift is required, then piping running from the tubing hanger assembly up the column and to the gas compression system must also be installed, further increasing the subsea construction required in and around the facility’s splash zone.
The CCT technology uses more flexible composite tubing that can navigate all the short radius pipe bends at surface and on the column and pontoon of the semisubmersible TLP prior to entering the PR. Consequently, hang-off at surface versus at the waterline is possible. This eliminates the significant cost and operational risk of the subsea construction activity required when using standard steel tubing and conventional CT systems.
A recent application of this solution was applied in the US GoM in a 32-km tieback to a semi-submersible TLP in 1,370 m water depth. Declining well rates and increased water production led to a severe slugging issue that was causing significant upset and outages of the facility’s process system. Boarding pressure was increased to manage the slugging, but this also reduced production rates from the wells.
The tieback operator initially considered either installation of a gas lift riser (externally connecting to the production riser-base as planned in the original system design for future integration) or a subsea multi-phase pump. However, these would have increased platform load to above the maximum allowable limit and were rejected by the facility operator. In addition, the lead time of each of these solutions was multi-year, compounding the cost of deferred production.
The optimal solution was therefore deemed to be installation of a 2.375-in. outer-diameter composite in-riser velocity string (IRVS), inside the 5.23-in. inner-diameter PR using the CCT technology. The goal was to increase superficial fluid velocities by reducing the cross-sectional area of the riser by approximately 20%.
In preparation for the installation of the composite IRVS, the flow-loop was first pigged and then flushed with seawater to allow for removal of the hard pipe spool connecting into the boarding valve (BV). This spool was then replaced with a wye-piece type assembly with one leg connecting to the BV and the other a dead-leg that contains the IRVS tubing hanger.
Available deck space on the congested platform was extremely limited. But the CCT system’s components could be deployed across multiple decks and locations, in contrast to conventional CT packages.
The composite IRVS was then successfully installed via a cumulative total of 523° of pipe bends using the CCT package within a 24-hour period. During steady-state operations, boarding pressure was reduced from approximately 1,000 psi to 600 psi with greatly reduced slugging frequency and severity, while increasing production by approximately 30%.
This application was delivered at a cost of approximately 60% less than the estimated cost of deploying steel tubing using conventional CT and without any recordable weight gain to the facility due to the inherently buoyant nature of the composite IRVS.
The successful execution of this industry-first project within a seven-month period demonstrates that a low-cost, field-proven and rapidly deployable artificial lift solution can be applied on the majority of deepwater production facilities to address the technical and economic challenges that face mature assets.
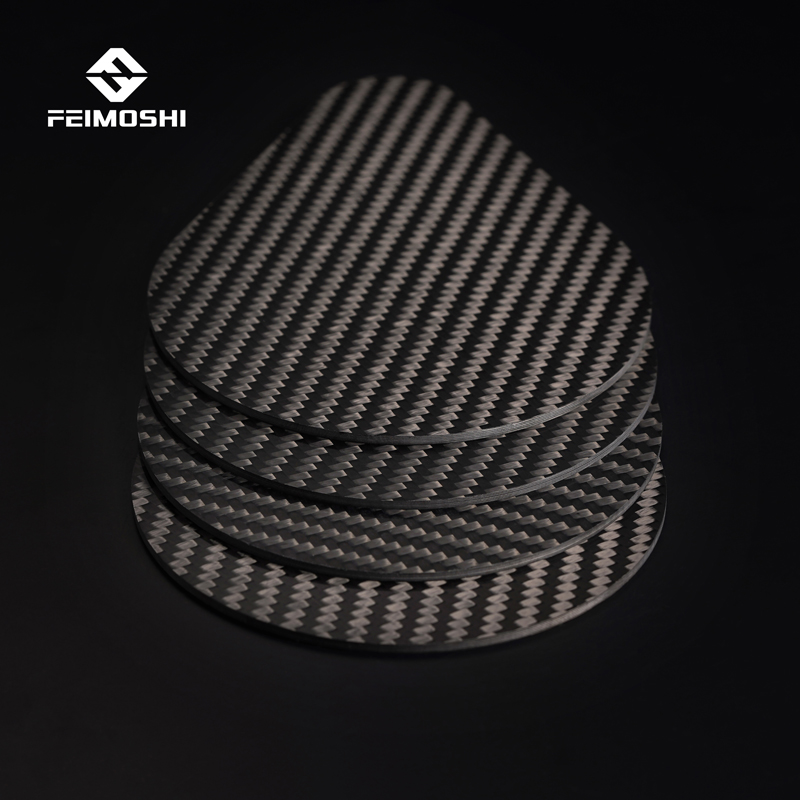
carbon fiber rc parts Kevin Keogh is VP of Commercial for Paradigm’s Flow Services business, based in Houston, Texas, a position he has held since 2016. Keogh has led the efforts to commercialize Paradigm’s ‘Flexi-Coil’ technology, including its diversification from its core application of remediation of solids deposits in risers and flowlines into providing a low-cost retrofit artificial lift solution to improve recovery from deepwater subsea wells, for which he is patent pending.