Editor’s Note: This article was derived from a roundtable discussion conducted at Pipe & Tube Lincoln 2015, Lincoln, Neb., on Sept. 23, 2015. The roundtable participants were John Anton, division manager, Independence Tube Corp.; Ron Bochat, application engineer, Innovo Corp.; Dan Jacobs, vice president of sales, SigmaTEK; Phil Meinczinger, business development manager, Magnetic Analysis Corp.; Brian Havlovic, senior engineer, Kawasaki Motors Mfg. Corp. USA; and Brian Kopack, senior sales engineer, Formtek Inc. The session chairman was Mark Prasek, vice president of sales and marketing for Rafter Equipment Corp.
It’s a debate few outside of manufacturing would understand, and one that isn’t likely to be settled anytime soon. It’s one of the most critical issues between tube and pipe producers and their customers: Are typical commercial specifications good enough? Cut Off Saw Machine
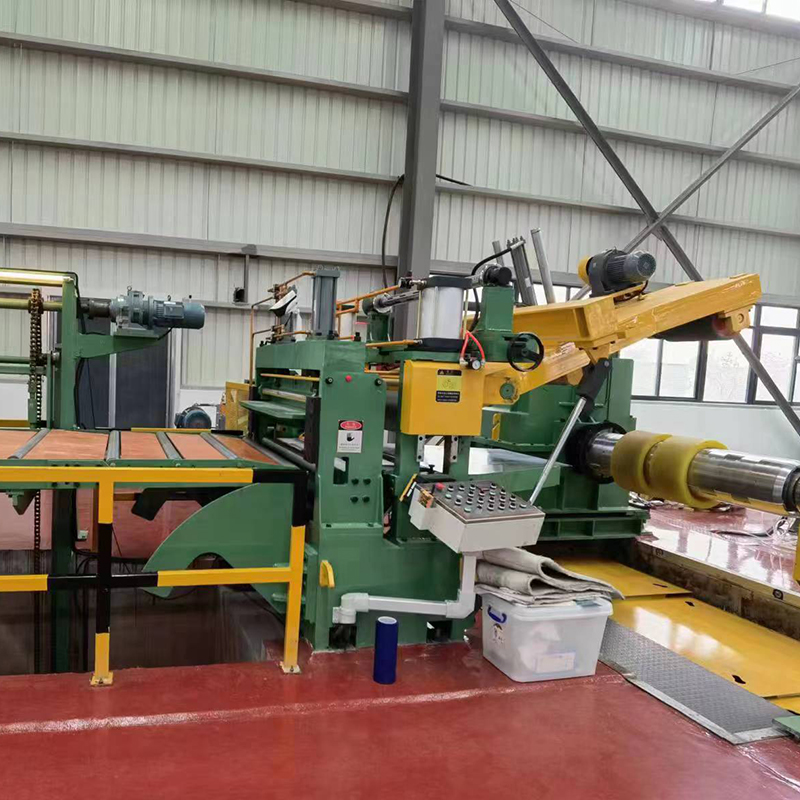
“The same questions were a concern in the sheet metal industry a couple of decades ago,” said Brian Havlovic, senior engineer at Kawasaki Motors Mfg. Corp. USA, Lincoln, Neb. “At that time sheet metal wasn’t as flat as it is today. It often had a slight bow or camber to it, and the equipment used at that time could tolerate it. That changed as lasers became more prominent in manufacturing. Laser heads have very little standoff distance, so to prevent the laser head from making contact with the metal’s surface, fabricators demanded flatter sheet metal, and the industry complied by finding ways to supply flatter product.”
It’s a little more difficult—some would say much more difficult—to tighten up the tolerances on welded tubular products. Welded tube comes from sheet metal, but the sheet metal goes through a great number of additional processes along the way. First it’s coiled, slit to the specified width, then shipped to the tube or pipe mill. There it’s uncoiled, formed, and welded. It also goes through a cooling (or quenching) process, sizing, straightening, and cutoff. If the welding process is electric resistance welding (ERW), the product also is forged as it is welded. In other words, the material is subjected to substantial stresses and heat. Because the roll tooling setup varies from one mill to the next, two similar tubes from two different mills probably are different in how they were formed, the amount of weld heat they incurred, and the severity of straightening they needed.
Regardless of the obstacles, tube and pipe fabricators are demanding tighter tolerances and better consistency. Just as the increasing use of laser cutting pushed the sheet metal industry to flatter products decades ago, the ncreasing use of technology is behind the ongoing desire for more consistency in tubular products. Many manufacturers are dealing with the vocational skills shortage by incorporating more robots and automated systems, technologies that work only when workpieces they pick up, transport, form, and weld have very little dimensional variation. Consistency is the key in getting automated systems to work. For cases in which automated systems do work, improving consistency further is necessary for improving throughput.
While the common manufacturing standards were a topic of debate—chiefly ASTM A500 and ASTM A513, which apply to structural and mechanical tubing, respectively—the discussion didn’t stay there. Instead, it covered a variety of strategies tube and pipe producers and fabricators can use to make better products.
Every manufacturing process is like a chain—it’s only as strong as its weakest link. When making tube, if everything doesn’t go just right along the way, the mill operator might be able to compensate, but even so, the tube or pipe quality is likely to suffer. The steel’s chemistry and hardness must be consistent from coil to coil, and it must be slit with well-maintained tooling and transported with care so that the coil edges are suitable for welding. Every tool on the mill needs regular inspections and frequent maintenance; every component of the mill, from the infeed table to the Turk’s head (straightener), must be aligned; and every setup must be performed the same way, every time, by every operator. No exceptions.
“Consistency is the key,” said Brian Kopack, senior sales engineer for Formtek Inc., Cleveland. “If you don’t have consistency in the coil chemistry and dimensions, and if you have a 50-year-old mill in a facility with no maintenance department, you’re not going to make good tube.”
Even when all goes as planned, making tube or pipe by the seam welding process is prone to slight variations. The apex of the seam moves back and forth and can wander laterally, the voltage supplied by the welder varies throughout the day, and the metal’s characteristics can vary slightly from one coil to the next. It’s not possible to control all of these variables, which is why it’s necessary to pay close attention to the variables that can be controlled.
“You need persistent and consistent machine maintenance,” said participant Robert Sladky, vice president of tube mill engineering for Roll-Kraft, Mentor, Ohio. “You need good mill integrity—consistency in mill maintenance, tooling maintenance, and setup procedures.”
Figure 1 A tube formed round has a weld seam at the 12:00 o’clock location (far left). A subsequent operation on the mill turns this form into a square and leaves the weld seam in the same location. Depending on the roll tooling setup, the weld seam ends up in the center of a side or in a corner. Another option is to form the square directly from the strip; in this case, the weld seam ends up in the center of one side (far right).
Consistency in mill setup actually does more than help to produce good tube. If the setup is consistent, it’s one of the first causes that can be eliminated when problems arise. Also, consistent upstream processes help downstream processes.
“If the weld seam stays in a consistent position, straightening is easier,” said Mark Prasek, vice president of sales and marketing for Rafter Equipment Corp., Strongsville, Ohio.
Depending on the product and the process, the weld seam isn’t too difficult to deal with. For example, when stainless steel products are made, fusion welding processes such as gas tungsten arc welding (commonly known as tungsten inert gas, or TIG) and laser welding leave a heat-affected zone (HAZ) but little in the way of a weld bead. Participant Bret Molnar, senior technical adviser for Roll-Kraft, mentioned that manufacturers of these products often condition the weld seam with rolls or hammers.
Using ERW to make carbon steel products is a different process altogether. A forging process, ERW causes two weld beads to form, one on the OD and one on the ID. The OD weld bead isn’t too difficult to remove, but cutting off the ID weld bead is a challenge. Cutting too little and leaving a small hump on the ID can wreak havoc on downstream fabrication processes; cutting too deep and removing some of the parent material weakens the tube, making it prone to splitting if it goes through a severe forming process later on.
To remove the ID weld bead, producers have several choices. A mandrel that sits inside the tube, equipped with springs to hold the scarfing tool against the ID, is one such tool. Others are hydraulic or cantilevered, but regardless, this is a blind process; it happens inside the tube after it is closed and welded shut, so the mill operator doesn’t know if it was successful until the tube exits the cutoff station at the end of the mill.
Tube producers charge extra for this to offset the costs associated with the process, largely the downtime and scrap generated every time a scarfing tool, which is made from carbide and therefore brittle, shatters inside the tube. The mill operator has to stop the line, cut open the tube, retract the toolholder, and replace the tool.
“You need perfect strip width to get perfect results,” Molnar said.
Most nonround tubing goes through two forming stages, first to round, then to the final shape. For squares and rectangles, the most common tooling setups form two horizontal sides and two vertical sides; the weld seam ends up right in the middle of one of the sides. For fabricators that need the weld seam elsewhere, an alternate tooling setup locates the weld seam in a corner (see Figure 1).
A difficulty is getting a uniform square or rectangle. Often three of the corners have good consistency, but the fourth exhibits a thicker wall (known as a lazy corner).
“Theoretically, the material flows evenly into all four corners, but this requires perfectly consistent material,” said John Anton, division manager, Independence Tube Corp., Chicago.
In reality, the material isn’t perfectly consistent. The original sheet material, as it is rolled in the steel mill, doesn’t have a uniform thickness. It’s thicker near the center of the sheet, and therefore the individual coils that are slit from the center of the coil are slightly thicker than those slit from the edges. After the material goes through the tube or pipe mill’s weld box, the weld zone is harder than the rest of the material. Finally, if a producer needs to know just how well the forming passes do their job, it’s possible to install a laser-based measuring system to determine the extent of the tube’s ovality before the tube enters the weld box.
Even when every precaution is taken, perfect consistency is elusive. Although every tube producer denies it, tube fabricators often lament that round tube is never round and the hole is never in the middle. A square tube might be nearly flawless, but it’s difficult to make a perfect square from an imperfect circle.
Forming the strip into a square or rectangle directly, rather than first forming it round, is another possibility, but this isn’t a common process.
“Few mills are set up for this because a mill that forms squares doesn’t form rounds well,” Prasek said. “Also, products made this way need a slightly different chemistry than round-to-square products. They are worked less, so they are hardened less,” he noted.
“It requires more forming stands and tooling, but those costs are amortized over such a large amount of tubing that the per-foot price of the tube is negligible,” Kopack said. A benefit to forming a square directly from strip is the ability to punch holes in the strip before forming, if necessary, Kopack added.
• When sourcing raw material, remember that gauge control is tighter for cold-rolled material than for hot-rolled material.
• Regardless of the forming process, increasing the number of forming passes increases the products’ consistency.
Fabricators are accustomed to asking their customers questions about bends and end forms. Is zero ovality in the bend zone really necessary? Would a deburred end work as well as a chamfered end? Does a hole location need a location tolerance of ± 0.005 in.? Likewise, some have listened to their customers’ concerns and taken these up with the tube producer to work out a solution.
“Even with a weld seam steering device, the weld seam location varies a little bit,” Anton said.
Still, one fabricator reported a successful outcome. It had been purchasing tube with the weld flash removed, but changed to using a mandrel with a relief. The cost of adding the relief feature on the mandrel was more than offset by eliminating the cost of weld bead removal.
It’s a matter of learning what the customer really wants and what the tube producer can provide, and finding the best solution. It might be a lot of work, but the results are better working relationships in the supply chain and better products for the customers.
For more information on tube and pipe production and fabrication, see the offerings at the online bookstore of the Fabricators & Manufacturers Association International® at https://ebiz.fmanet.org/Ebusiness/Store/FMAStore.aspx.
See More by Eric Lundin
Eric Lundin worked on The Tube & Pipe Journal from 2000 to 2022.
Read more from this issue
Subscribe to The Tube and Pipe Journal
The Tube and Pipe Journal became the first magazine dedicated to serving the metal tube and pipe industry in 1990. Today, it remains the only North American publication devoted to this industry, and it has become the most trusted source of information for tube and pipe professionals.
Easily access valuable industry resources now with full access to the digital edition of The Fabricator.
Easily access valuable industry resources now with full access to the digital edition of The Welder.
Easily access valuable industry resources now with full access to the digital edition of The Tube and Pipe Journal.
Easily access valuable industry resources now with full access to the digital edition of The Fabricator en Español.
Jeff Cupples, the president of Jackson, Tenn.-based Cupples J&J Company, discusses his experience with laser cutting machines and...
© 2024 FMA Communications, Inc. All rights reserved.

Pipe Tube Machine Not yet registered? Sign up