Thermoformer supplier Harpak-ULMA’s nationwide 3D-printing service permits rapid iterative customization of tray dimensions and detailed design features.
Companies including packaging suppliers continue to leverage the agility of 3D printing to open new opportunities for themselves and for customers. High Precision Turned Parts

One of the latest is Harpak-ULMA, which now offers a nationwide 3D printing service tailored for thermoform tray package prototyping.
Customers can utilize this service at the Centers to easily, quickly, and cost-effectively customize their tray designs to meet specific marketing needs and preferences.
Harpak-ULMA's 3D printing service for tray package prototyping offers merchandisers unmatched flexibility and versatility in prototyping — whether customization requirements call for adjusting dimensions, adding intricate features, or including branding elements.
Customers also have the option of in-person collaboration at Harpak-ULMA’s Customer Experience Center at its Taunton, MA, headquarters.
It’s the first of the company’s three Centers equipped with 3D printing capabilities, Kevin Howard, associate engineer tells us. “We have the proven ability to provide same day or overnight tray samples ensuring that 3D printing services are available to all customers nationwide.”
The company’s other Centers are in Ball Ground, GA, and Irvine, CA.
“Adding additional 3D printing capabilities in the western and southern Customer Experience Centers will be based on customer demand,” adds Howard.
Related: 3D Printing Slashes Unilever Bottle Design Costs
Key benefits of 3D printing prototyping of plastic trays:
Provides custom differentiation. This can make the difference between a tray that’s “so so” and one that’s outstanding.
Standard prototyping to develop customized trays is labor-intensive, time-consuming, and results in long lead times and significant costs. This may prohibit prototyping for smaller businesses or companies with limited budgets.
3D printing dramatically reduces waste associated with legacy prototyping methods, which makes it more environmentally friendly.
"Our new 3D printing-enabled package prototype services eliminates barriers, shortening the prototyping process from weeks to months to hours with commensurately lower costs," notes Joshua Allen, Harpak-ULMA's marketing director. "It also facilitates quick and inexpensive iterations. Feedback from testing and evaluation is easily incorporated into successive prototypes. That kind of iterative approach leads to better final products.”
Cost- and time-savings are tied to specific projects and requirements “For one-off trays made on the printers, turnaround times are about two days versus two to three weeks done traditionally,” Howard points out.
Prototyping costs are drastically slashed. “Costs have been about 1% to 4% of traditional methods,” he says. “For complete thermoformer tooling, lead times and costs are about half.”
Howard provides additional details about the 3D printing capability in Taunton.
“The workhorse of our 3D printing systems are a pair of Form 3L systems made by FormLabs . These are large-format stereolithography (SLA) printers that use photopolymer, UV-activated resin,” he says. “Thermoforming molds will be produced using FormLabs’ Rigid 10K resin , capable of short-run thermoforming. Most have been clear resins.
“These printers produce durable, high-quality samples with little to no visible layer lines. We also have a pair of Bambu X1-Carbons by Bambu Lab, a fused deposition modeling (FDM) printer that prints thermoplastics such as ABS, PETG, and nylon to name a few. Most trays done thus far on the FDM printers have been made of polylactic acid (PLA) and PETG.
“These systems have been crucial for low-cost, same-day design confirmation and modifications.”
Howard acknowledges that commercialization progress has been “slow but steady. We spent the first few months working on purely internal projects. We had a soft launch mid-February and full launch in March.”
The company notifies customers of the new service at the start of every project.
“They can opt for sample trays/tooling before committing to a final design,” Howard says. “Our goal right now is to accept as many requests as possible in hopes of scaling this department throughout the year.”
Harpak-ULMA remains flexible to customers' needs. For example, the company has responded to requests that go beyond thermoformed trays.
“We have also used the 3D printers to develop testing brackets, mounts, and reusable demo products,” Howard says.
Customers quickly realize the value of 3D printing for prototyping trays.
“This week alone we’re developing prototype tooling for two customers,” says Howard. “We anticipate the growth will be exponential this year as our sales and marketing departments get the word out to prospective and returning customers.”
Senior Technical Editor, Packaging Digest and PlasticsToday
Rick Lingle is Senior Technical Editor, Packaging Digest and PlasticsToday . He’s been a packaging media journalist since 1985 specializing in food, beverage and plastic markets. He has a chemistry degree from Clarke College and has worked in food industry R&D for Standard Brands/Nabisco and the R.T. French Co. Reach him at [email protected] or 630-481-1426.
As You Sow Hands Out Many Fs in Plastics Promises Scorecard
Resin Price Report: Resin Demand Heats Up as Summer Starts
Small Things Considered at Plastec South
BASF Opts for Sustainable Glass Fiber
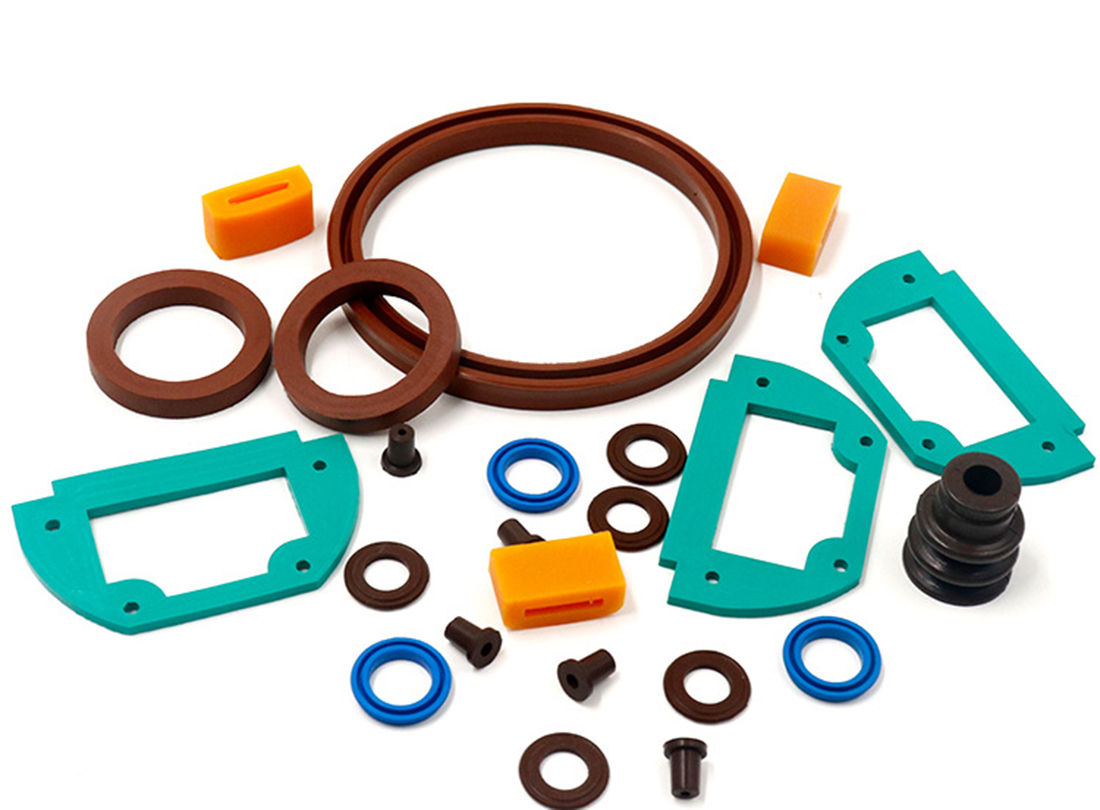
Cnc Milled Aluminum Level Construction Level Frame Copyright © 2024 All rights reserved. Informa Markets, a trading division of Informa PLC.