A decade ago, bituminous geomembranes (BGMs) were a relatively unknown player in the landfill and mining industries. Fast forward to the present day, and BGMs have emerged as a significant disruptor, posing a formidable challenge to traditional high-density polyethylene (HDPE) geomembrane manufacturers. The industry landscape has shifted dramatically, with BGMs steadily gaining market share and leaving a lasting impact on the geomembrane market.
The shift in market dynamics Car Damping Heat And Sound Insulation Sheet

Over the last 10 years, BGMs have rapidly gained momentum in the world of landfill and mining applications. What was once considered a niche solution has now become a preferred choice for various projects.
The once-unassailable position of HDPE in the world of geomembranes has started to erode as BGMs gain traction and ascend in market share. Recent industry events, such as the International Geosynthetics conference in Rome, have underscored this shift, with no fewer than seven technical papers dedicated to BGMs. Leading BGM manufacturers like Axter and SiPlast are presenting a united front, united by a common adversary: the HDPE geomembrane manufacturers.
Just last month, a major BGM supplier received a monumental order from a Western Australian mine for over one million square meters of BGM material. This order serves as a testament to the increasing adoption of BGMs over HDPE geomembranes.
Key reason for BGM’s ascendance
Several factors have contributed to BGM’s ascendance and its growing preference over HDPE geomembranes.
One of the primary reasons is BGM’s exceptional ability to resist installation damage and mechanical wear and tear. This characteristic sets BGMs apart, making them an ideal candidate for the bottom liners of landfills, where it allows for trafficability during installation, while the top liner is typically HDPE.
Resilience to installation damage: BGMs are renowned for their robustness during installation. Unlike HDPE geomembranes, which can be sensitive to installation conditions, BGMs are more forgiving. Their ability to resist damage during installation ensures that they maintain their integrity and functionality, even in challenging environments.
Mechanical durability: BGMs excel in mechanical durability, making them an excellent choice for applications that involve heavy foot and machine traffic, such as landfills. Their resistance to punctures and abrasions significantly reduces the risk of damage from heavy machinery and vehicles, thus extending their lifespan and reducing maintenance costs.
Trafficability for bottom liners: BGMs are particularly favored for use as bottom liners in landfills. Their mechanical resilience allows for vehicles and equipment to traverse the surface during construction and installation without compromising their integrity. This trafficability during the initial phases of a project is a distinct advantage, as it streamlines the construction process and minimizes the occurrence of holes and tears in the bottom liner.
Synergy with HDPE: While BGMs have gained traction for their use as bottom liners, HDPE geomembranes continue to be popular choices for top liners. This symbiotic relationship between BGMs and HDPE allows for a cost-effective and durable solution in landfill and mining applications. The combination of BGMs at the base and HDPE on top offers a robust and reliable containment system.
BGMs boast several key properties that have contributed to their growing popularity and pose a significant challenge to HDPE geomembranes:
Low permeability: BGMs exhibit impressive low permeability with a rate of 10-14 m/s, as per ASTM E 96 standard. This makes them highly effective as barriers, preventing the passage of liquids and gases.
Puncture resistance: BGMs are exceptionally resistant to punctures, even when subjected to angular aggregate materials. This resilience ensures long-term durability and minimizes the risk of leaks or damage. BGMs incorporate a strong polyester continuous filament geotextile within the liner, combined with protective bitumen. This design results in exceptional puncture and abrasion resistance, making them well-suited for installation processes and compatibility with aggressive interfacing materials like angular drainage aggregates.
Low thermal expansion: With a low coefficient of thermal expansion (1 x 10-5 mm/m/°C, according to ASTM D1204), BGMs remain virtually immune to thermal wrinkling. Unlike HDPE geomembranes, BGMs lie flat under all temperature conditions, avoiding the formation of wrinkles. This characteristic allows for more controlled welding and placement of cover materials, regardless of the time of day and the surface temperatures.
Extreme temperature tolerance: BGMs have demonstrated their ability to withstand extreme temperature variations, from the freezing cold of Northern Canada and Siberia to the scorching heat of Australia’s Pilbara region and Chile’s Atacama Desert. This adaptability makes them suitable for diverse geographical locations and climates.
Steep slope capability: BGMs offer the advantage of steep slope capability, allowing for versatile design options and potentially more waste storage volume per unit area of the cap. Their high-friction underside, often equipped with a peel-off siliconized release paper, prevents sliding and permits the placement of cover soils at steeper angles, with slopes as steep as 1:1.3 successfully installed in Australia.
High wind resistance: Wind is a critical consideration in geomembrane applications. BGMs, with their specific gravity of 1.27 and thickness of up to 5.6 mm, are heavy and dense, providing resistance to wind uplift. This characteristic enhances safety during installation and reduces the need for temporary ballasting, benefiting both designers and installers.
Intrinsic robust construction: Unlike some HDPE geomembranes prone to stress cracking, BGMs, thanks to their geotextile and bitumen composition, do not suffer from this issue. This allows BGMs to interface with aggressive soils and aggregates without the need for additional protection geotextiles. Laboratory tests have confirmed their ability to withstand extreme pressure without puncturing.
The geomembrane industry has witnessed a remarkable transformation over the past decade, driven by the emergence and widespread adoption of BGMs.
Once a newcomer, BGMs have now firmly established themselves as a significant threat to HDPE geomembrane manufacturers. Their ability to withstand installation and mechanical damage, along with their trafficability during construction, has made BGMs a preferred choice for bottom liners in landfills and mining projects.
As the geomembrane market continues to evolve, it is clear that BGMs are here to stay. Their proven resilience and cost-effectiveness make them a compelling option for industries that demand durable containment solutions. The ongoing competition between BGMs and HDPE geomembranes is likely to drive innovation and ultimately benefit end-users by providing more choices and better solutions for their specific needs.
BGMs offer a compelling combination of low permeability, puncture resistance, thermal stability, and adaptability to extreme conditions, making them an attractive choice for various containment applications.
As BGMs continue to gain ground, the geomembrane industry faces an evolving landscape, one where traditional players must adapt to the changing tide. The competition between BGMs and HDPE geomembranes is not only shaping the industry but also offering end-users a wider array of options and improved containment solutions to meet their specific needs. Information courtesy of ExcelPlas.
U.S. Department of Transportation names newest FAA Management Advisory Council members
Industrial Fabrics constructing $8 million erosion control production facility
How geomembranes are used in disinfection processes and how to select the right one-Part 2
Inland Tarp & Liner names general manager
Webinar - Migrating from the Simplified Method to the AASHTO Stiffness Method for Internal Stability Design of MSE Walls – July 18
Webinar - Sustainable Solutions: Harnessing Shredded Wood for Rights of Way Stabilization – June 26
Geosynthetics Magazine is a publication of the Advanced Textiles Association
Copyright © 2024 Advanced Textiles Association. All rights reserved.
1801 County Road B W, Suite 100 Roseville, MN 55113-4052, USA
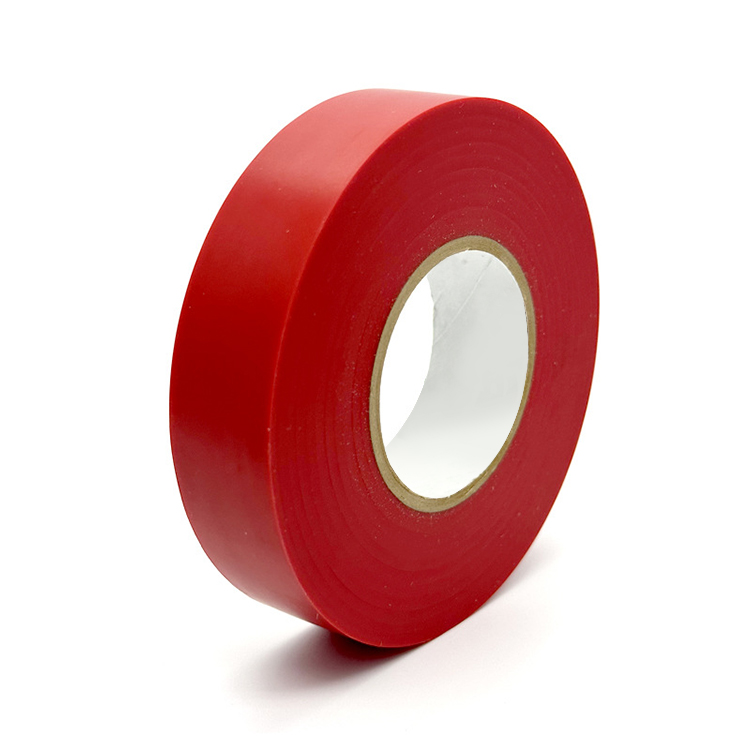
Sealing Putty Tape Terms of Service Privacy Policy