Editor's note: This article was not sponsored or supported by a third-party. Images in the gallery showcase the Collina FW 6.0 and FW 6.1 e-bikes.
A bit of a nomad at heart (being born in Europe and raised in several places in the USA), Cristian is enamored with travel trailers, campers and bikes. He also tests and writes about urban means of transportation like scooters, mopeds and e-bikes (when he's not busy hosting our video stories and guides). Full profile Alloy20 Tubes

You will only receive our top stories
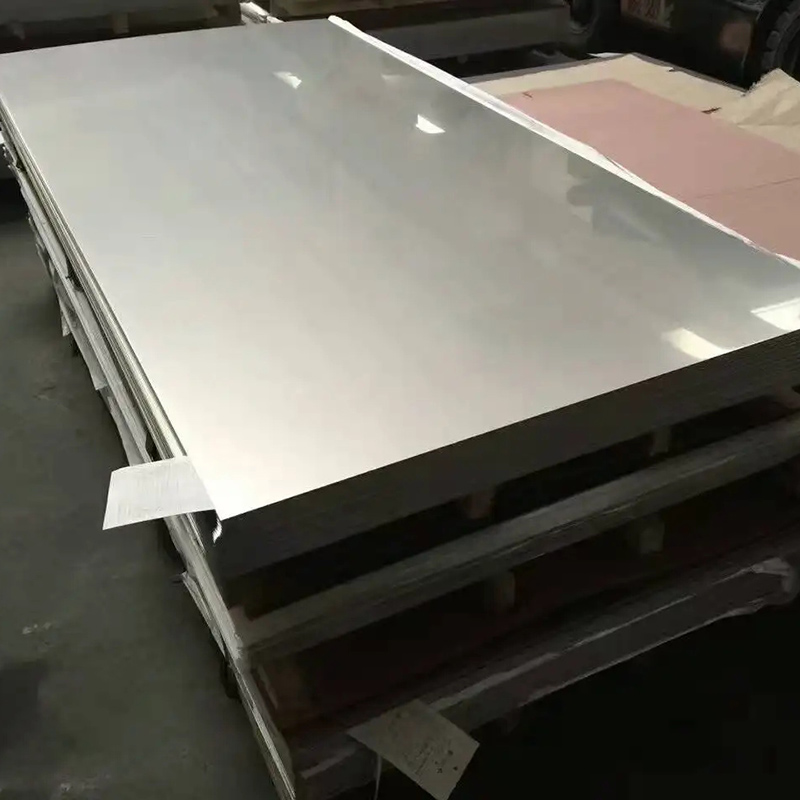
N6 Plate © 2008-2023 SoftNews Net SRL • Privacy Policy • Cookies Policy • Terms of Use All rights reserved. autoevolution® and the autoevolution® logo are registered trademarks.