Periodic motor testing is a regular occurrence for many plant electricians and electrical and instrumentation (E&I) departments across a multitude of industries. Like many departments within these corporations, the electrical departments have endured staff shortages along with the ever-present business cycle of contracting out maintenance and then bringing it back in-house due to cost constraints.
It is always a balancing act of how much well-trained and capable engineering talent is employed within a maintenance department, along with owning the necessary technology versus what specialized testing companies can offer at a price. As facilities age, motor failures become more frequent, making this issue even harder to balance. Unipolar Motor Driver
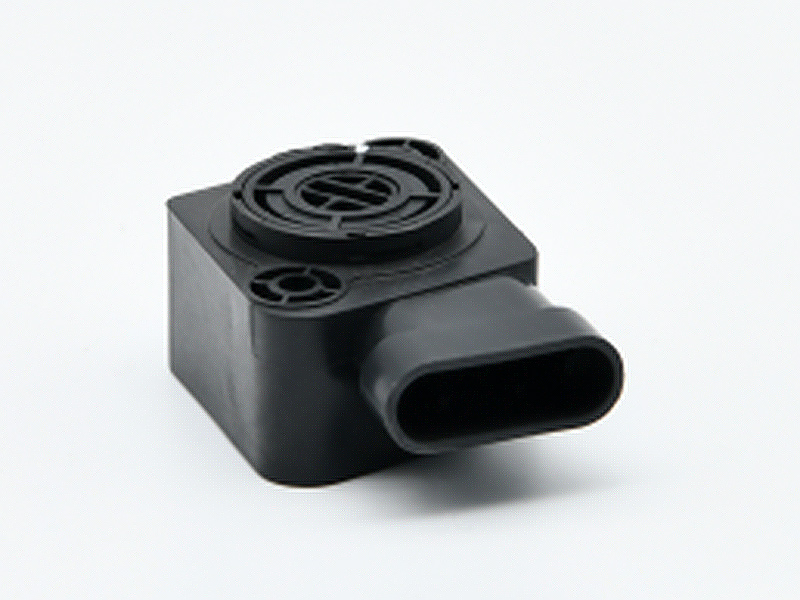
The balance is usually reached with maintenance staff troubleshooting the outage. If their attempts do not eliminate the issue, an expert is called in with more technology to adequately evaluate the motor system and offer guidance on next steps. The example below is an actual case study of the process followed when both plant staff and local contract companies are brought in to solve a critical problem.
Images 1 & 2: Variable frequency drive (left) and motor test set inside motor room behind pressure doors (right). (Images courtesy of EDE Electric Motor Testing) Critical Air Handling in a Colorado Medical Campus
In medical facilities, electric motors play a vital role in the inner workings of many departments. From heating, ventilation and air conditioning (HVAC) and lighting to elevators and patient care apparatus, electric motors keep the facilities’ main objective—patient care—operating. So, what happens when a problem develops in a system that is vital to the objective? Since the continuous operation of medical facilities is necessary, staff maintenance and electricians are employed to troubleshoot and repair.
In the summer of 2023, a 100 horsepower (hp) motor in the HVAC system at a large medical campus in a major metropolitan area in Colorado developed an issue. This motor was one of four variable frequency drive (VFD) operated motors that drive separate fans for air handling to the pulmonary clinic, allowing for cooling and heating during different times of the year. The VFD tripped off for one of these motors and showed various errors such as ground fault and overcurrent.
Since medical campuses operate 24/7, they have outage windows for maintenance to perform testing and troubleshooting. In July, this outage window is between 5 a.m. and 7 a.m., as this is the coolest part of the day. Since the motors run in a pressurized environment, these two hours are the only time the other three units can be taken offline to allow safe access to the air handling unit by personnel. While three motors can provide cooling to the building, it is not an optimal situation for certain areas such as surgical suites that need to be kept at a low temperature for patient safety.
The morning following the motor trip, an HVAC technician came in with standard electrical tools, including a multimeter and megohmmeter. The motor passed the megohm test, and the multimeter showed balanced continuity and resistance readings. Since the motor seemed to be okay, the culprit appeared to be a faulty VFD. This VFD was replaced, and the system started. The motor and drive once again tripped with the same faults.
At this point, the facility’s electricians knew more testing with specialized equipment was necessary. A local testing company came in during the approved time window and performed diagnostic electrical testing on the motor. This included digital low ohm resistance (DLRO), megohms, direct current (DC) high potential (HiPot), inductance and a surge test.
Digital Low Ohm Resistance (DLRO): The DLRO, also known as the micro-ohm meter, measures resistance values in micro-ohms at specified currents. Precision DLROs use the four-wire Kelvin resistance method that helps eliminate contact resistance and reduce errors caused by lead resistance.
Megohms: The simplest of motor tests is the megohm test. Also known as insulation resistance (IR), it is used to diagnose breakdown in wire insulation integrity. In the trade, it looks for “grounded” or defective insulation to ground.
DC High Potential (HiPot): Using DC voltage, the DC HiPot tests the dielectric strength of the insulation to ground. This is used to determine if the ground wall insulation is capable of handling an overvoltage situation. It impresses a significantly higher and therefore more rigorous test than the megohm test.
Inductance: A low voltage excitation frequency (and the resulting electromotive force [EMF] measurement) is applied to the electric coils inside the electric motor. It can be used as a reference value, or in the case of three-phase industrial motors, each phase should exhibit relatively similar readings. Large differences between the three readings can be an indication of a “hard” short circuit in a coil or phase-phase.
Surge: The surge test focuses on the copper windings in the motor. Surge testing is a technique to test the dielectric strength of the insulation in windings. It finds voltage dependent faults in turn-to-turn and phase-to-phase insulation. It is depicted on the tester screen by a shift to the left of the waveform.
Three of the five tests showed detectable or high-level deviation. The two tests that passed also provided useful information on the insulation to ground. It allowed the testing engineer to focus on the turn or phase insulation and feel comfortable in the integrity of the ground wall insulation.
At this point, the investigation shifted to the turn insulation and determining the likelihood of a turn-to-turn short in one phase of the motor. Because of the protection programming of the VFD, the fault did not propagate into a hard ground fault. Turn-to-turn shorts cause a circulating current inside induction motors, which can cause a hot spot and has the potential to catastrophically burn down the motor.
Higher quality VFDs have two little-known capabilities. One is they protect themselves from the motor when an issue such as a turn-to-turn short happens, and the second is the VFD will protect the motor from the circulating current that happens when shorts within the windings occur. It does this by tripping the motor off and then gives information to the maintenance engineer on what occurred at the time of the trip.
The three tests that showed deviation narrowed down the possible issue significantly and allowed the test engineer to quickly pinpoint the problem. While the DLRO showed a 13.2% deviation within phases, specifically 1-2, the inductance test showed the possibility of a hard short in phase 3-1. The surge test showed issues on all phases but shifted to the left, verifying a shorted 3-1 phase at 100 volts. This information showed the turn-to-turn short in one phase was indeed the cause of the service interruption.
After all the tests were completed and the results analyzed and reported to the plant electricians, it was decided the motor would be pulled and replaced. After this was completed, the new motor operated according to specifications and allowed the set of four fan motors tasked with keeping the pulmonary clinic cool on hot Colorado summer days to work without incident and without overtaxing any of them.
So, when is it truly the time to call in an expert? Is it when something initially happens or when the equipment owned by the facility or plant is exhausted of capabilities and the problem still exists? Sometimes it might even be better to get a second opinion on work done by plant technicians to verify results that have been accumulated. It simply depends on the situation. The critical nature of some systems will dictate the need to move quickly and fix the issue.
No matter what, the E&I department is tasked with keeping a corporate balance and getting the job done in a timely and cost-effective manner. It is not a one-size-fits-all problem that can be taken lightly or easily solved. Users must balance the needs of the future with the costs associated with keeping critical plant operations running smoothly when it comes to electric motors.
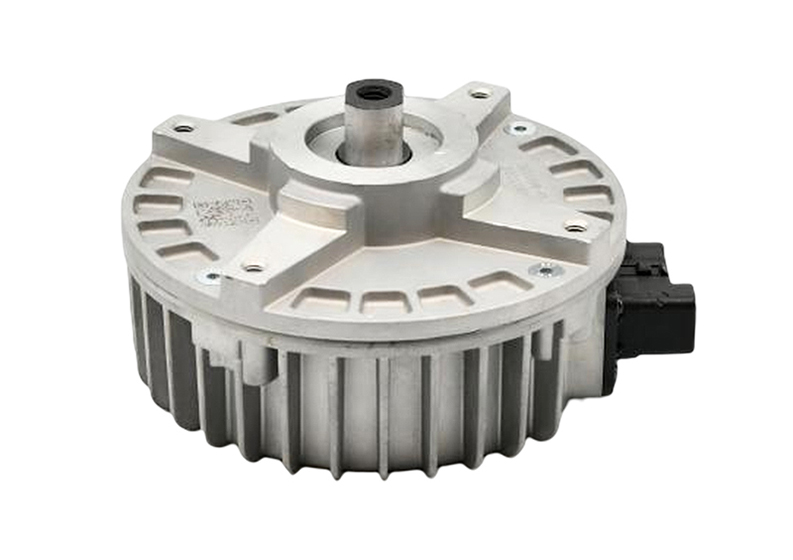
Vibration Motor Amy J. Frey, MS, is co-owner and president of EDE Electric Motor Testing. With 20 years of experience in working with maintenance professionals through new and existing equipment and services, she uses that base of knowledge to make EDE one of the leaders in electrical testing and equipment repair and maintenance. For more, visit www.edeinst.com.