©2023 GEAPS Media Group. All rights reserved
Georgia Poultry Producer Replaces 1960s-Era Facility with 14,000-tpw Feed Mill Hammer Mill Grinder
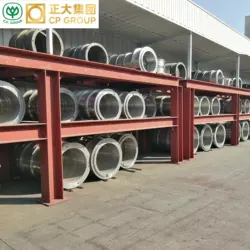
Harrison Poultry, the nation’s 20th largest poultry producer, is best known for its “golden-yellow” chicken products. It’s a color favored by Latino consumers.
“In Mexico, you won’t find any chicken for sale that isn’t this golden-yellow color,” says David Bleth, president and CEO. “It’s highly favored in Hispanic areas in the United States, as well.”
The color Harrison Poultry markets as “Golden Goodness” is no accident. It comes from a feed additive derived from marigold petals, which the company has utilized for more than 40 years, and today, virtually all Harrison Poultry feeds contain it.
Precise formulations is one goal of the company’s new 14,000-tpw feed mill near Crawfordville, GA that began production at the end of 2020. The new slipform concrete mill is replacing a 1960s-era mill 65 miles to the northwest at Winder, GA, which was rated at 6,000 tpw.
“About the only good thing about the Winder site by 2018 was that it was paid for,” Bleth says. “We were outsourcing a lot of our feed production.”
Expanding at Winder or at the company’s Bethlehem, GA headquarters was impractical as the suburbs of Atlanta rapidly grew eastward. After looking at more than 40 properties, Harrison Poultry selected a site an hour’s drive to the southeast on State Highway 22.
The location offered enough level space to build an 8,200-foot loop track off the CSX Railroad and quick access to Interstate 20. And it was in the heart of the company’s broiler houses.
“We broke ground in December of 2018,” says Nick Strange, corporate projects manager. “The 326-acre site was 90% forested, and we cleaned out 58 acres of it.”
Harrison Poultry’s management had been discussing a new mill for some years before groundbreaking. Hogenson Construction Company, West Fargo, ND (701-281-1742), had inquired about building a mill as early as 2015, and after a bidding process, was named contractor and millwright.
“What they gave us was the ability to custom design to our specifications,” Strange comments. “(Feed Mill Manager) Dave Sailors and I already know what works and what doesn’t in a poultry feed mill. They worked with us according to what we wanted, and they gave us more mill for the money, and as slipform concrete builders and millwrights, we liked their level of craftsmanship.”
One demand from Harrison Poultry was the extensive use of variable frequency drives (VFDs), which ended up on 88% of the facility’s equipment.
“That allows us to control the speed of the product flow and boost the accuracy of our mix,” Strange notes. “Direct drive VFDs eliminate belts and guards and make everything easier to operate and maintain.”
Partnering with Hogenson, VAA, LLC, Plymouth, MN (785-559-9100), provided structural engineering on the mill.
The $35 million slipform concrete facility includes 1.17 million bushels of grain storage, nearly all of it delivered by rail from the Corn Belt.
“CSX had been bringing corn in on 90-car unit trains,” Bleth says, “and they asked for 110-car capacity on the loop track. We gave them space for 125 cars and four power units and anticipate that will set us up for decades.”
Grain is delivered through a pair of dump-through mechanical receiving pits feeding a pair of GSI InterSystems 1,400 tph legs featuring double rows of Maxi-Lift CC-MAX 16x8 elevator buckets. Corn is delivered via Hayes & Stolz distributors and GSI InterSystems drag conveyors to a pair of 500,000-bushel slipform concrete tanks standing 75 feet in diameter and 140 feet tall. The tanks have flat floors with Bobcat doors.
In addition, a 30-foot-diameter, 140-foot-tall day bin with 45-degree concrete hopper is situated directly over a pair of CPM hammermills rated at 70 tph. One hammermill has a VFD; the other has a reversible soft start to produce a coarser grind for use in breeder feeds.
The slipform concrete mill building contains 27 ingredient bins holding a total of about 4,000 tons; two mash feed tanks per pellet mill line; and 28 loadout bins, 14 for each of two truck loadout bays. The mill currently contains two 7,000-tpw production lines, with space enough to install an third line when it becomes needed.
All feed mill operations are under the control of a CPM Beta Raven automation system, which interfaces with the company’s Agris accounting system.
Contents from the ingredient bins are mixed in a 12-ton double-ribbon Hayes & Stolz mixer on a three-minute cycle producing 240 tph of mash feed. In addition to the overhead bins, ingredients also can be added from a CPM Beta Raven four-bag tote system or a 20-bin Beta Raven microingredient system.
Feeds are pelleted on a pair of CPM Model 7936-14 pellet mills at approximately 90 tph. An APEC fat coater supplies fat for the pellets. Steam conditioners are located atop pellet mills, with steam supplied by a pair of Cleaver Brooks 500-hp boilers.
Pellets are run through Geelan counterflow coolers, and pellets intended for breeder feeds are run through a CPM crumbler.
Harrison Poultry operates a fleet of 14 trucks, which are loaded in two separate bays with Abel weigh lorries. The mill is averaging 45 to 50 truckloads per day.
While the feed mill is in operation, construction continues on a truck maintenance facility immediately south of the mill.
From the January/February 2021 GRAIN JOURNAL
View this review and more in the Grain Journal January February 2021 magazine.
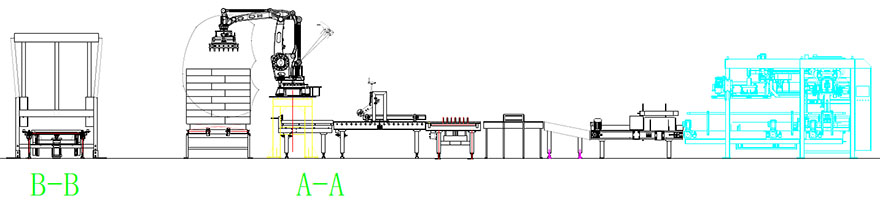
Mixer Shaft Subscribe to our newsletters to get the last update into your inbox!