The Rhode Island Office of Energy Resources recently announced the start of construction on the state’s first two electric vehicle (EV) DC Fast Charging stations located along the Interstate 95 corridor. The new charging stations will be installed at the Ashaway Park & Ride and the Route 117 Park & Ride in Warwick as part of Phase 1 of Rhode Island’s National Electric Vehicle Infrastructure (NEVI) Program.
The Ashaway and Warwick Park & Ride locations will each house two DC Fast Chargers capable of charging an EV up to 80% in 20-40 minutes. The ultra-fast chargers are considered “future proof”, meaning they can charge new EVs coming to market for years to come. With many automakers pledging to go fully electric over the next 10-15 years, Rhode Island officials want to ensure adequate charging infrastructure is available across major travel corridors. Dc Car Charger
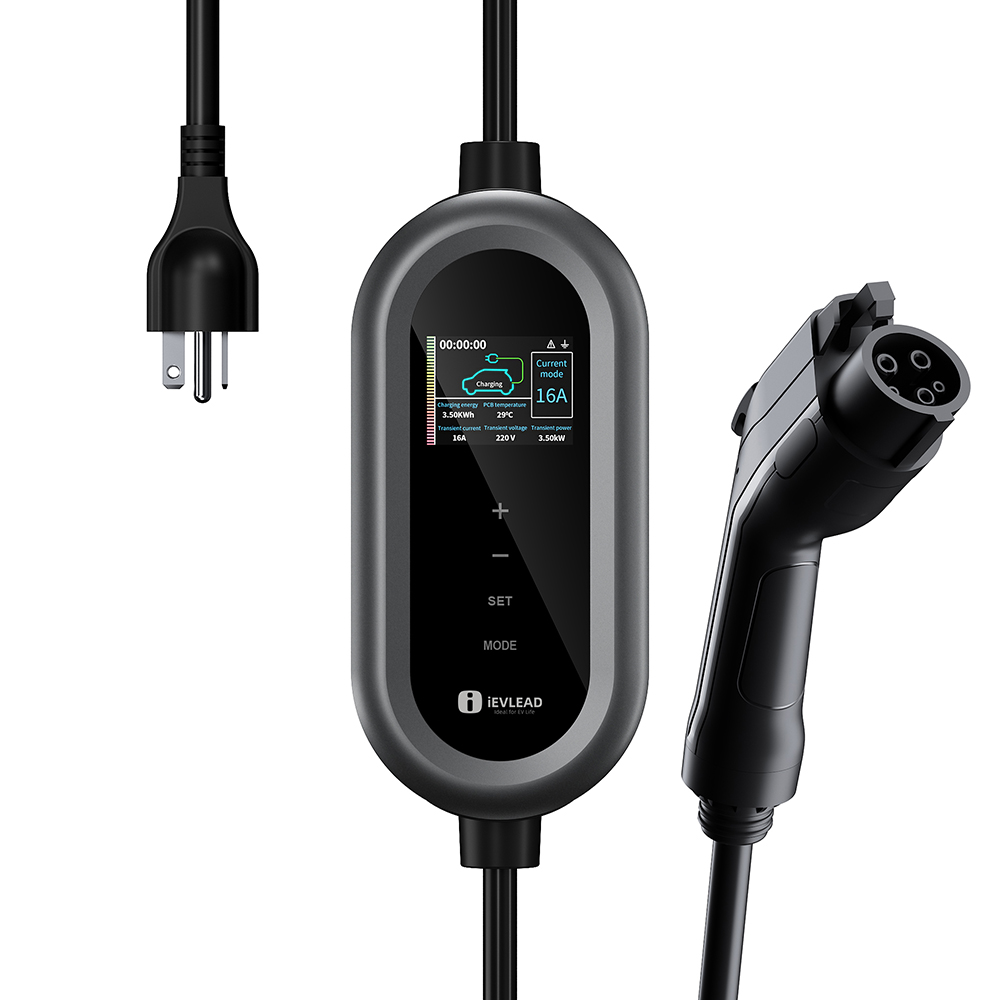
Chris Kearns, Acting State Energy Commissioner, noted the new chargers will complete Rhode Island’s designated Alternative Fuel Corridor along I-95. The completed corridor and convenient fast charging stations are expected to alleviate range anxiety and other concerns residents may have when considering an EV purchase.
The NEVI Program funding comes from the Bipartisan Infrastructure Law passed in 2021, which invests billions nationally into EV charging infrastructure and grid modernization. According to Gabe Klein, Executive Director of the Joint Office of Energy and Transportation, Rhode Island is one of the first states using its initial NEVI funding allotment to target high-traffic areas like Park & Ride locations. Officials believe positioning chargers in strategic areas along I-95 will encourage more drivers to go electric.
In addition to the NEVI Program, Rhode Island has its own ambitious goals to tackle transportation emissions under the 2021 Act on Climate bill. The legislation mandates a 45% reduction in all greenhouse gases from transportation by 2030 and net-zero emissions by 2050. Transportation currently accounts for over a third of the state’s total emissions.
Supporters believe increasing EV adoption through charging infrastructure expansion is essential to meet these legal requirements. They also point to the public health benefits of phasing out gas-powered vehicles. DEM Director Terry Gray said switching to EVs will “improve the quality of the air that our residents breathe every day by reducing harmful tail-pipe pollutants.”
The Ashaway and Warwick EV charging stations are expected to be completed over the next few months. In total, Phase 1 of the NEVI program will deliver 8 DC Fast Chargers and 6 Dual-Port Level 2 charging stations along the I-95 corridor. Rhode Island will then focus on Phase 2 of the NEVI Program in 2024, which will fund more chargers around the state. Officials say they are committed to developing a convenient, reliable, and affordable EV charging network accessible to all residents as the transition to electric vehicles continues nationwide.
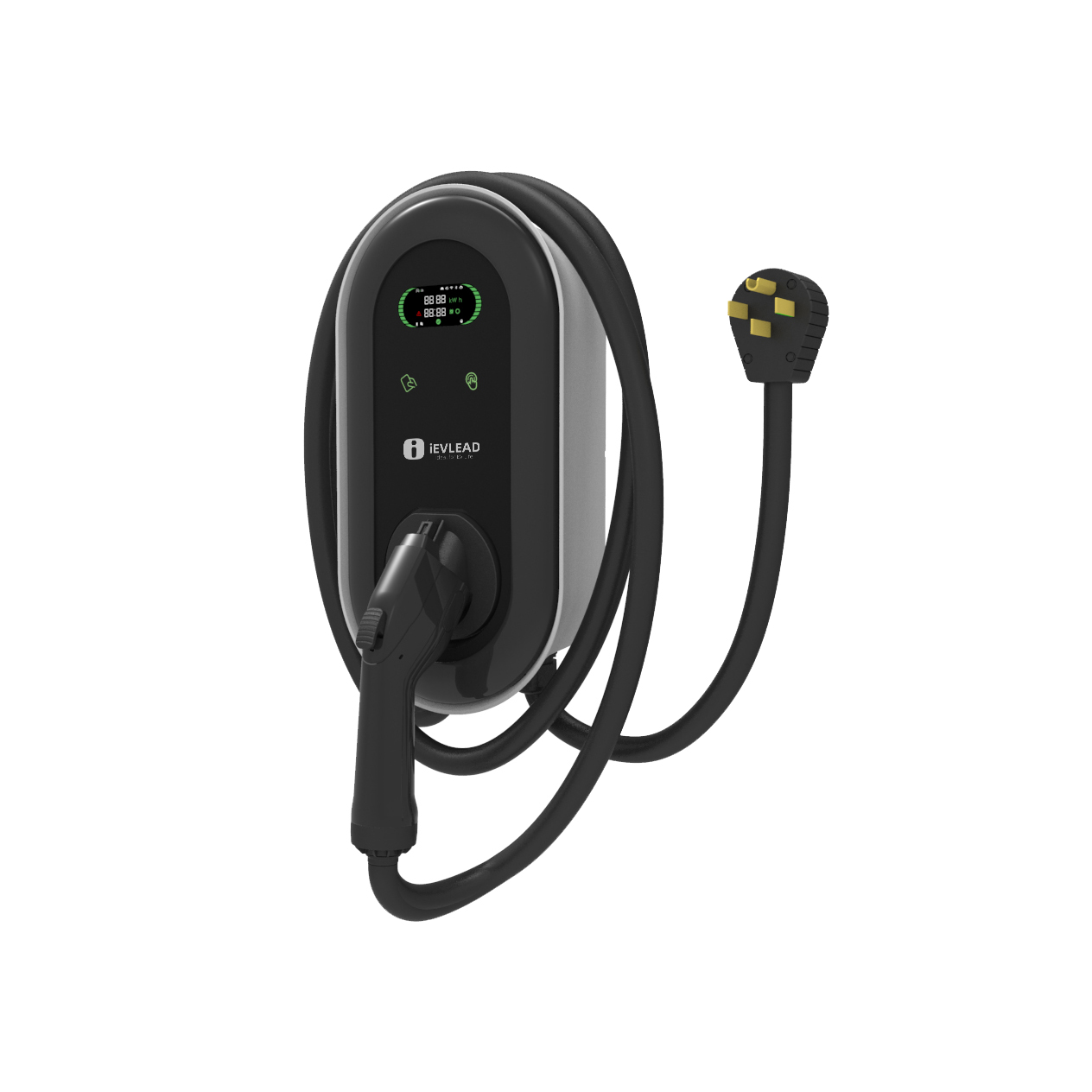
Car Charging Station Copyright 2023 Rhode Island Free Press Co. Designed and hosted by Company 50, a Rhode Island website builder.