A linear handling system removes the plastic parts from the injection molding machine and places them in a hot stamping fixture. Photo courtesy Tox Pressotechnik
Hot stamping plastic parts is a dynamic process that must be very precise at vacuum cleaner manufacturer BSH. To finish the components automatically, quickly and with low energy consumption, BSH relies on the ElectricDrive electromechanical servo drives from Tox Pressotechnik of Weingarten, Germany. Hot Foil Die Makers

“With the new, completely automated hot stamping systems, we can define the process much more precisely in advance,” says Andreas Zehe, production technician at BSH Hausgeräte GmbH in Bad Neustadt, Germany. “We work faster and more precisely, have reduced scrap by 60 to 70 percent, and consume significantly less energy than before with the pneumatic drives.”
For a few months now, the vacuum cleaner manufacturer, which produces on behalf of Bosch-Siemens with 400 employees, has been running its second hot stamping machine with two ElectricDrive electromechanical servo drives from Tox. The system was designed and installed by Gebr. Gierlich GmbH & Co. of Bonn, Germany, which specializes in the manufacture of hot stamping systems.
In the system, BSH finishes components for vacuum cleaners with a thin film of plastic under the action of pressure and heat. The process is fully automated. A linear handling system removes the plastic parts from the injection molding machine and places them in a hot stamping fixture. In the first stamping step, foil is heated and pressed onto the component with a stamp. In the second step, a temperature-controlled silicone stamp moves onto the plastic part at high pressure and rests there briefly before moving back again. The film part detaches from the carrier and bonds with the component. A camera then checks the process.
The decorative elements on this vacuum cleaner are applied with a hot-stamping process. Photo courtesy Tox Pressotechnik
For a stable process and an error-free result, the parameters of the individual stamping steps must be set precisely. The pressure with which the stamp moves onto the component is decisive, but the temperature, stroke speeds and stroke lengths of the cylinders are also important.
“This is where the precise adjustment options of the electromechanical servo drives really come into their own,” explains Zehe. “Since we equipped our hot stamping machines with the Tox stamping cylinders, we can automatically measure and readjust the pressure during the stamping process.”
And even after a stamp change, the system readjusts the pressure independently because all parameters have been stored in the software beforehand.
With the old systems with pneumatic drives, this all had to be set manually. Thanks to automation, any number of programs can now be stored, which the plant operator can call up at the push of a button. “Before, we were constantly readjusting and setting the mechanics. Now we specify in advance exactly when we want to have which speed and which stroke,” says Zehe.
He can then read out whether the process has run as planned and correct it if necessary.
A temperature-controlled silicone stamp moves onto the plastic part at high pressure and rests there briefly before moving back again. Photo courtesy Tox Pressotechnik
BSH commissioned the first hot stamping system with Tox servo drives in mid-2020. The second came last year, a third is in the planning stage. “We are very pleased that both the plant designer and the user are so satisfied with our drive systems,” adds Peter Wilhelm, who works in sales at Tox. “The hot stamping project was a special application for us, too, because we normally come into the conversation with our drive units when it comes to processes such as clinching, press-fitting, riveting and punching.”
According to Wilhelm, the fact that BSH holds the stamp for a few seconds at the end and doesn’t retract it right away is also not the norm in classic applications, but it can be implemented easily and quickly through the software parameters.
Two ElectricDrive units are used in each of the hot stamping machines. Each unit consists of a servo press—either a ballscrew or a planetary roller screw are used here, depending on the requirements—a controller, the control cabinet and integrated software. The energy-efficient drive is suitable for applications with an effectively usable press force range of 0.02 to 1,000 kilonewtons.
An added benefit of the servo presses is that they consume less energy than pneumatic presses, and they have a significantly longer service life.
Zehe is certain that the investment will pay for itself after three to four years.
An added benefit of servo presses is that they consume less energy than pneumatic presses, and they have a significantly longer service life. Photo courtesy Tox Pressotechnik
For more information on assembly presses, read these articles: Optimizing Work Cells for Press-fit Assembly Common Mistakes With Presses Assembly Presses: Crimping, Staking, Swaging, Clinching
You must have JavaScript enabled to enjoy a limited number of articles over the next 30 days.
On Demand Connecting shop floor tools to a manufacturing execution system is critical to error-proofing assembly processes, improving quality control, and lowering defect and scrap rates. Join Torrence Williams, Partnerships Manager for Pico MES, and Dan Smith, VP of Sales for Kolver Tools, as they discuss an easier path for manufacturers to start connecting their factory floor.
On Demand This topic is something that challenges each of us every day that we go to work. This talk is about change and why it works and why it fails. It is focused on manufacturing facilities, because that is where the author has spent most of his working life.
Copyright ©2024. All Rights Reserved BNP Media.
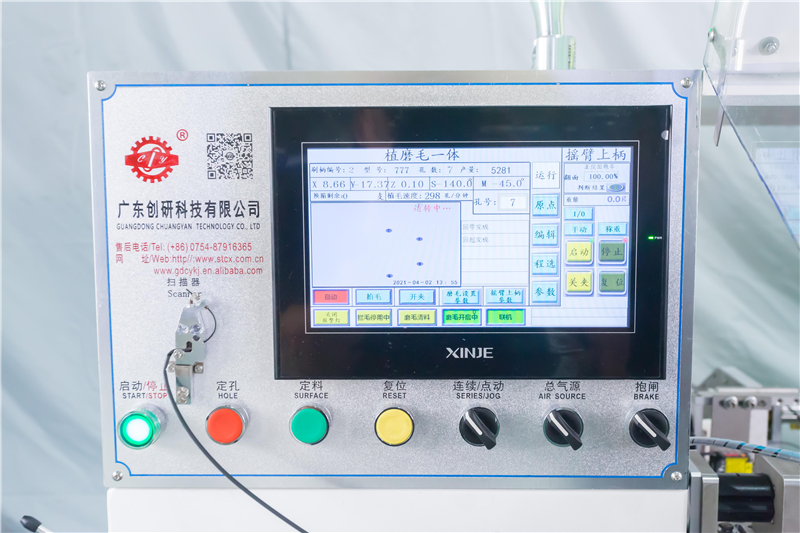
Hot Foil Press Dies Design, CMS, Hosting & Web Development :: ePublishing