Don't have an account? Register here today.
International. Friction-free compression technology offers effective performance in air-cooled or water-cooled liquid chiller applications, Copeland company spokespeople said. Tube And Shell Heat Exchanger
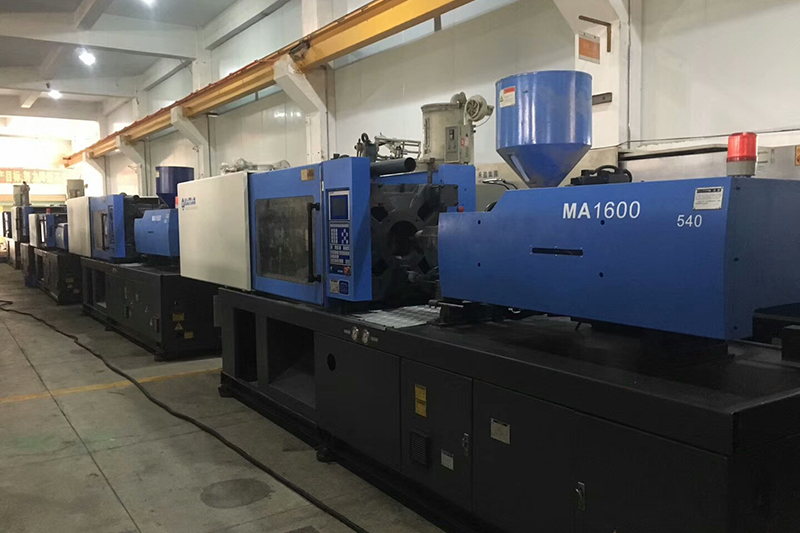
The new oil-free centrifugal compressor features modern Aero-lift technology and is intended to become a viable alternative to magnetic levitation and refrigerant-lubricated ceramic compression technology.
In this way, Copeland hopes to help OEMs and industry stakeholders simplify the application of oil-free compression technologies, while meeting next-generation requirements in terms of high efficiency, system design flexibility, and compatibility with refrigerants characterized by their lower global warming potential (GWP).
Designed for critical applications in data centers, healthcare, large chillers, and heat recovery, the Copeland centrifugal compressor works under full load and partial load conditions, with a wide operating range for high ambient temperature applications.
"After thousands of hours of rigorous and extremely reliable testing, it has been proven to achieve up to 10% higher efficiency at full load compared to other compression technologies in air-cooled applications," said Mike Oakley, director of Centrifugal Solutions at Copeland.
"It also provides an efficiency increase of up to 40% in integrated value at part-load, far exceeding the minimum ASHRAE 90.1 efficiency requirements for a two-compressor, 200-tonne capacity system, compared to existing screw technology," he added.
According to the executive, such efficiency is possible thanks to the integration of critical components, including Aero-lift technology, and numerous patents already granted and patent-pending innovations in the compressor and control.
Innovations Aero-lift technology allows the compressor shaft to levitate and operate independently, without friction or reliance on electromagnetism, complex controls, or proximity sensors, necessary in today's magnetic levitation bearing compressors.
In addition, it provides performance improvements during power outages, allowing the compressor to move smoothly, shut down and restart quickly to minimize downtime. This simplified technology approach also eliminates the need for backup auxiliary bearings and maintains redundancy in these scenarios.
To meet the need for greater design and application flexibility, the Copeland oil-free centrifugal compressor is decoupled from the controls and variable frequency drive (VFD), helping OEMs design systems capable of withstanding application environments in wet and aggressive environments that could damage them.
In addition, its design allows it to adapt to the high speeds needed to support the requirements of modern chillers while maintaining performance. Since the compressor does not rely on oil to lubricate the system, applied cost, complexities, and reliability concerns are reduced.
This new oil-free centrifugal compressor platform is being developed for the range of capacities from 50 to 200 tonnes and is optimised for use with the next generation of lower environmental impact (GWP) A2L and A1 refrigerants, such as R-1234ze, R-515B and R-513A.
This helps to reach the next GWP limits required by the Technology Transition standard imposed by the U.S. Environmental Protection Agency, under the authority of the American Innovation and Manufacturing Act (AIM).
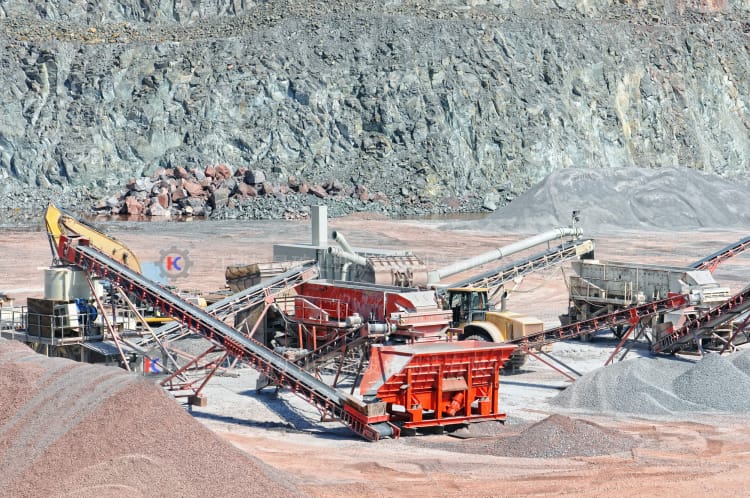
Aluminum Tube Radiator Distribution Copeland plans to progressively expand product availability globally, while actively working with OEMs and consultants to introduce the technology in the U.S., Canada and Latin America.