96 per cent of Delhi's unauthorised colonies covered with regular water supply: Economic survey
World Water Day 2023: Theme, objectives, significance of day that calls for action to solve global water crisis Angle Bar
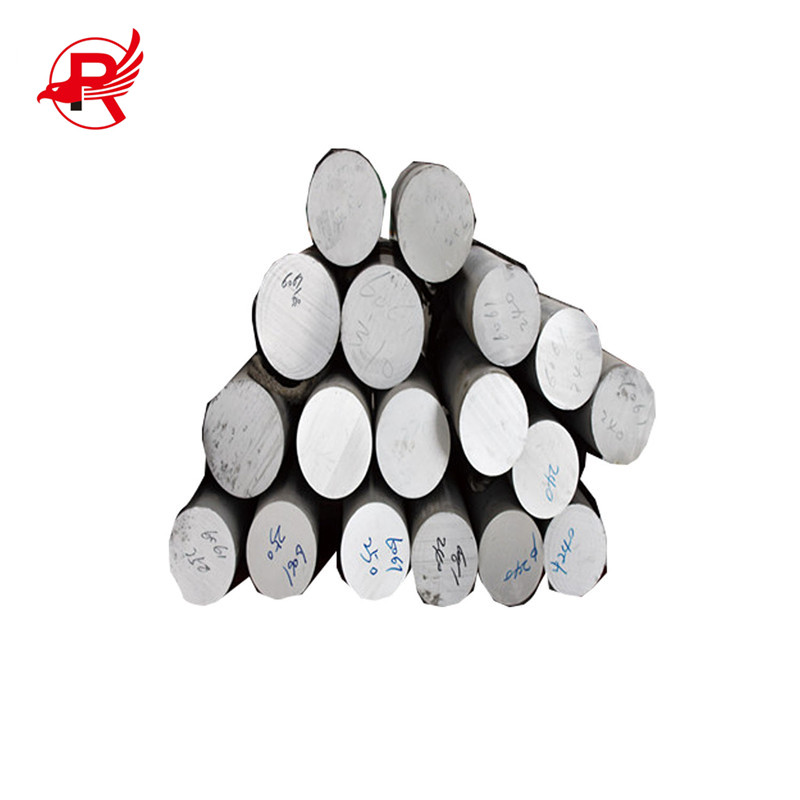
How much water should you drink every day to stay hydrated in the summer season?
10 benefits of having water when you wake up
US Fed Meeting Outcome: FOMC March 2023 Result | TOP POINTS | BIG TAKEAWAYS
US Federal Reserve hikes key interest rate by 25 bps as widely expected to tame inflation
Earthquake update: 13 killed after strong tremors jolt Afghanistan, Pakistan
Redmi Note 12 Turbo spotted on Geekbench ahead of March 28 launch; key specs leaked
WATCH: Bhopal post office deputy director dies of cardiac arrest while dancing-Doctors suggests the best exercise for heart
Bangladesh: Train collides with bus in Dhaka's Malibagh, rail services disrupted | WATCH
Beijing supports India's G20 Presidency, mutual trust crucial to resolve border dispute: Chinese envoy Ma Jia
Kolkata: Man chops wife into three pieces, buries body body parts in garden
Bihar Board 12th Result 2023 HIGHLIGHTS: BSEB Class 12 Result 2023 Declared; Check Step by Step Guide, Toppers
HIGHLIGHTS: BSEB Class 12th Result Declared! List of websites to check marks
Doctors Continue With Surgery Amid Earthquake Tremors In Kashmir
Daily Astro Predictions for All Zodiac Signs Today, March 21, 2023
8 healthy, filling foods to eat for Sehri
Are Home Loan EMI's Turning Into A Debt Trap?|What is the 'Hidden Cost' Of Loan?|Beyond The Headline
BJP Slams Free Speech | 5 Journalists Detained | Where's The 'BBC Ecosystem'? | Newshour
SC Raises Concerns Over Judge Appointments | Fresh Judiciary Vs Centre Faceoff | Beyond The Headline
After Denigrate At UK, Indian High Commission Beefed Up | Has The Message Gone Through? | Newshour
3 Confirmed Boxing Medals For India | 'Punches' Its Way To Bronze | Latest News | Nation Tonight

Stainless Steel Pipe 201 © 2023 Bennett, Coleman & Company Limited