Lab managers specify these designs according to experience and personal taste. Processes that have worked well in water-jacketed incubators are likely to remain in this type of equipment.
Water-jacketed incubators are renowned for temperature stability, but return to temperature set point more slowly, say after opening the door, than direct-heated units. In the event of a power failure water-jacketed incubators remain warm longer, but take longer to return to set point when the power comes back on. They are also larger and heavier for a given work volume due to the water jacket. Ultrasonic Homogenizer
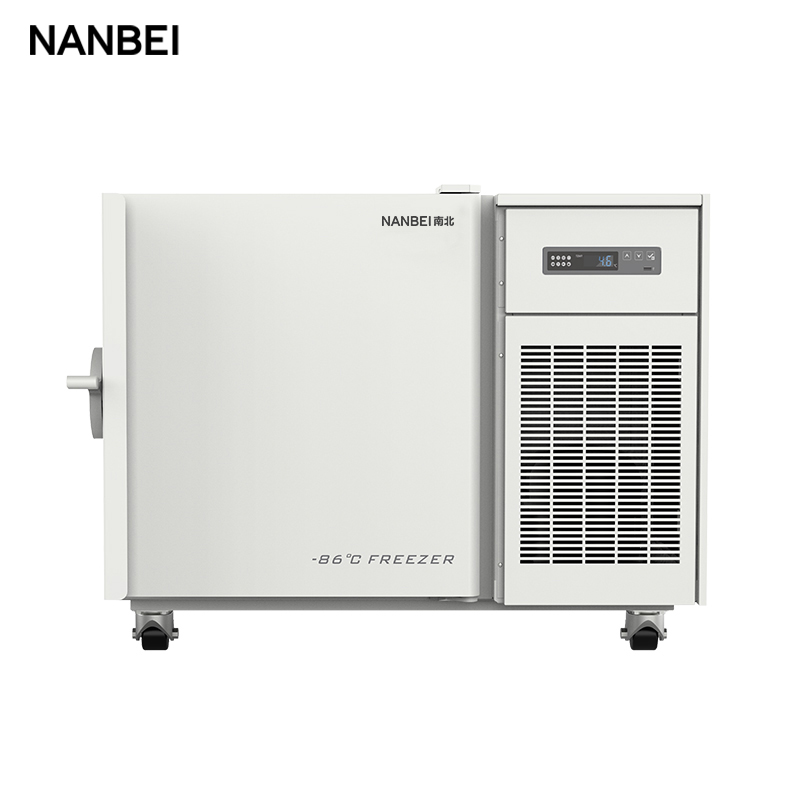
Maintenance of waterjacketed units is also somewhat more complex. Users must add algaecide to the jacketed water, and these incubators cannot employ high-heat disinfection. Regardless, labs tend to stick with what has worked in the past, which guarantees that despite losing some market share to direct-heated incubators, demand for water-jacketed units will not disappear any time soon.
Many direct-heated incubators now are fanless, which imparts several benefits. “Moving air through natural convection rather than forcing air movement with a fan reduces both condensation and cross-contamination,” explains Rick Ellison, business development manager, scientific division at BMT USA (Monroe, WA). Fanless designs also reduce maintenance by eliminating replacement of HEPA filters that cleanse incoming air and thus eliminating any cleaning or contamination issues arising from the fans themselves.
With incubators, the less mechanically complex, the better. “Other designs may be just as effective, but they introduce more variables,” Ellison says. “The fewer variables, the lower the likelihood of something going wrong.”
Physical location is key to ensuring high performance in CO2 incubators. Lynn Philip, product manager at Eppendorf (Enfield, CT) suggests keeping the incubator away from ventilation ports and direct sunlight, both of which create atmospheric variability that stresses incubators and diminishes their lifetime. “Ventilation drafts also carry bacterial and fungal contaminants,” Philip warns.
CO2 Incubator / CellIQ™ / PHC Corporation of North America / www.phchd.com/us/biomedical/ Whether using a central gas system or individual gas tanks, users should install an in-line pressure regulator at the CO2 inlet to ensure that gas is supplied at recommended minimum pressure. Suboptimal pressure could lead to reduced performance and slow recovery, while too-high pressure may damage the gas system, according to Philip. “Also, try to minimize the frequency and length of door openings to conserve optimal cell culture atmosphere,” she says. “Split inner doors can reduce the loss of culture atmosphere during door openings.”
Almost all incubators available today are equipped with self-cleaning technology. The most common uses high-heat disinfection, which is labor-free. For routine upkeep, Philips advises cleaning with 70 percent isopropanol or a manufacturer-recommended disinfectant.
To say that contamination and/or cross-contamination are issues of when, not if, has become cliché. All the more reason for labs to prepare for that eventuality.
Ellison recommends systems that feature “strong sterilization, not just decontamination.” BMT’s sterilization technique of choice is the application of dry high heat, but other methods may be as effective. Whatever method is chosen, it should be as automated (and therefore error-proof) as possible. High heat takes longer than lower-temperature chemical or hydrogen peroxide sterilization but requires practically no user intervention.
Hydrogen peroxide sterilization may be justified on the basis of reduced downtime. The technique involves introducing peroxide gas into the chamber and then circulating it through an internal blower. A drawback of this technique compared with heat is that surfaces and internals must come into contact with the gas. The final operation involves activation with narrowbandwidth ultraviolet light. Manufacturers claim that autoclaving is not required because all components remain within the enclosure throughout the process. But as Ellison notes, peroxide sterilization leaves behind some residual sterilized water that does not remain pristine for long and requires manual removal. Still, manufacturers claim downtime of about two hours for hydrogen peroxide sterilization, versus 14 hours for high heat.
Uwe Ross, president of Binder, Inc. (Bohemia, NY), likens ongoing discussion of contamination to “beating a dead horse.” But the proliferation of decontamination methods suggests that the problem remains unsolved. “Personally, I believe that hot-air sterilization at 180°C is the only method that really works, but even that technique cannot address what goes on during use, after sterilization.”
Contamination arises from organisms settling on surfaces and growing with the assistance of condensation. This leads to a design approach that reduces working surface areas to an absolute minimum; less surface equals less room for microorganisms to grow.
A CO2 incubator will do its job to protect an experiment or process, but only if operators follow best practices. In its excellent primer on cell culture, Invitrogen suggests the following contamination preventives:
“Review short- and long-term laboratory and cell culture needs [in order] to identify factors critical to the purchase,” says Philip. All incubators capably control temperature, CO2, and possibly O2, but units may differ significantly in design and performance. If contamination is a concern, lab managers should pay special attention to incubator design and time to disassemble, clean, reassemble, and disinfect. “Be aware of future requirements, as CO2 incubators are a long-term investment,” Philip continues. “Total cost of ownership over the first five years—including initial price, installation, gas usage, time and labor for cleaning, routine spares, etc.—must be evaluated to identify the best value for your money.”
CO2 Incubator / Heracell™ 240i / Thermo Fisher Scientific www.thermoscientific.com Manufacturers and end users emphasize temperature uniformity and recovery to set conditions. Mary Kay Bates, global cell culture specialist at Thermo Fisher Scientific (Asheville, NC), encourages buyers to investigate these performance factors. “Ask to see temperature mapping and recovery data.”
In considering recovery, the telling parameters are temperature, atmosphere composition, and humidity. “Humidity is the performance lynchpin, and not everyone appreciates that,” Bates adds.
Humidity prevents water evaporation from culture media, which causes nutrients, minerals, and other media components to become more concentrated. “This may result in poor performance or even cell death,” Bates notes.
Evaporation is four times higher at 80 percent humidity than at 95 percent humidity, which illustrates why humidity is king. The low-humidity, air-conditioned ambient air found in most labs exacerbates this effect.
Precise oxygen control has become another must-have for modern incubator work, particularly with hypoxic (low-oxygen) cultures. Oxygen levels inside organisms are much lower than the 21 percent level in the atmosphere. Moreover, all cells have unique oxygen requirements. Liver, kidney, and cardiac cells function optimally within organisms at unique oxygen levels, which may change even within organs. For example, liver cells require between four percent and 12 percent, depending on their proximity to oxygen-containing capillaries. Nerve, breast cancer, and immune cells will migrate away from an oxygen gradient, but Chinese hamster ovary cells used in biomanufacturing won’t. As researchers increasingly work with cells that require almost no oxygen to survive, the need for fine-tuning oxygen levels has never been greater.
iPSC Derived Neural Cells / AMSBIO / www.amsbio.com “Hypoxic cultures require oxygen uniformity throughout to ensure that cells on the bottom shelf receive the same concentration as cells on middle or top shelves,” Bates says. “You want to duplicate physiologic conditions as closely as possible.”
In addition to temperature uniformity and recovery of critical culture conditions, Bates advises purchasers to consider automated disinfection to save time and costs related to manual cleaning and autoclaving. Large cell culture reactors, for example, use automated clean-in-place or steam-in-place techniques; incubators employ chemicals and/or heat. Some designs require users to remove internal components and clean or autoclave them separately, while in others components are sterilized in place. Regardless of the disinfection protocol, it should not in itself introduce risk of contamination or harm to cells.
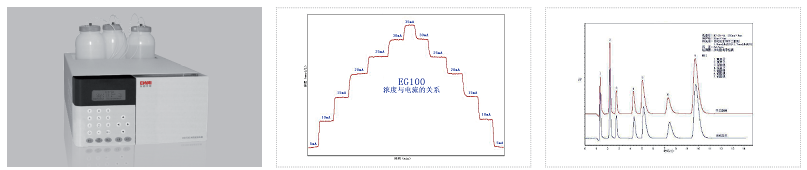
Graduated Pipette © 2024 Lab Manager. All rights reserved.