Options aplenty: last autumn BASF (Ludwigshafen, Germany) introduced a thermally conductive grade of its Ultradur High Speed polybutylene terephthalate (PBT) range, especially suitable for rapid filling of complex injection molds.
The high strength-to-weight ratio, processing ease, corrosion resistance, and other properties of plastics have helped them replace metal in a variety of applications. Metals still beat plastics handily in thermal conductivity, but efforts continue to teach thermoplastics to conduct (more) heat at high speed. Emergency Hammer Window Breaker
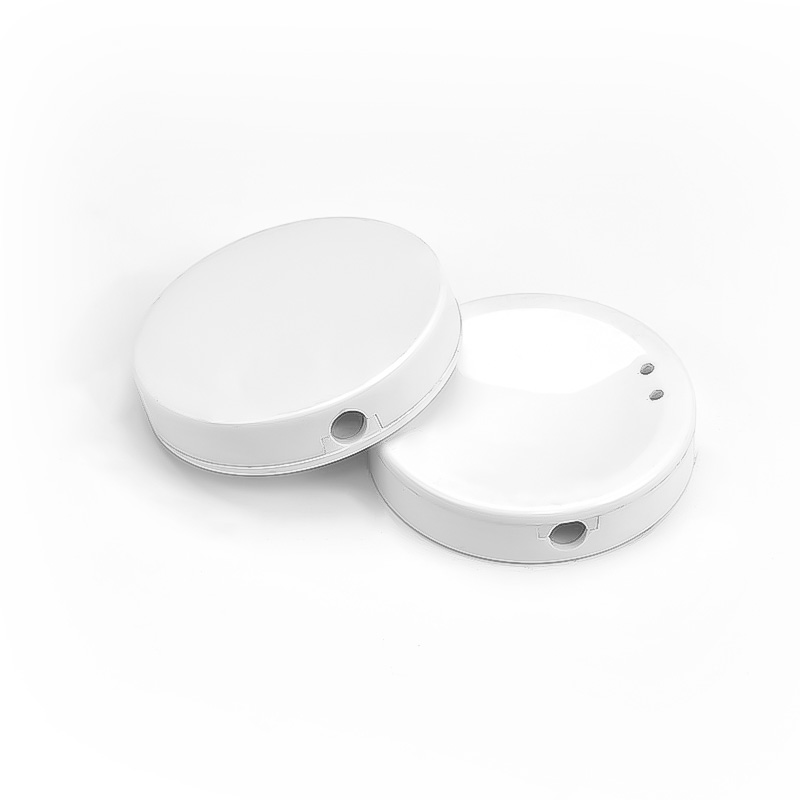
Television screens may be the only home electronic devices that get larger each year; for other applications, small is definitely king. If a device is smaller than its predecessor, it becomes that much more difficult to fit in fans or other heat-removal equipment. Die casting of aluminum, the traditional heat sink material, generally costs more than injection molding, with the latter process also offering more design options. It is little wonder, then, that developments in thermal conductivity are heating up.
The market for thermally conductive thermoplastic compounds is still a niche, but it is large enough that Cool Polymers (Warwick, RI) was formed in January 2000 to focus exclusively on it. The potential market for these compounds is huge, says Jim Miller, product manager, noting, “Heat transfer shows up in practically every part’s design,” one reason courses on it figure so early in an engineering student’s curriculum. He says demand growth has been strong each year, as an increasing number of designers take advantage of plastics’ design flexibility; by adding fins and other structures, a plastic part can prove just as good as taking away heat as an enclosure made of aluminum, other metal, or ceramic, and plastics create no interference problems. “We estimate that about 100 million parts are out there that were made with our materials,” he adds, citing electro-mechanical devices, such as encapsulation of motors, as one major application field.
Cool Polymers offers three product lines: its E-Series of thermally and electrically conductive materials; the D-Series of thermally conductive, electrically insulative ones; and E- or D-Series grades using elastomers as the matrix material. E-Series thermal conductivity extends from about 1.5 W/mK-20 W/mK, D-Series compounds to about 10 W/mK. Conductivity in those ranges is about 10-100 times that of standard thermoplastics. Though it’s not typical of the needs of the market, for some laptop applications the firm has supplied compounds offering thermal conductivity up to 100 W/mK, with molding done on its own machines.
Although many suppliers market at least limited amounts of thermally conductive compounds, different suppliers may measure differently to determine their compounds’ thermal conductivity, says Willem Sederel, global technology leader at Sabic Innovative Plastics (the former GE Plastics; Pittsfield, MA). His firm measures plastics’ conductivity “through the plane”, so that the orientation of the conductive fibers is not such a critical factor. When measured in-plane, much higher conductivity measures are realized, he says. “We’ve seen values to 20 W/mK, but 5 W/mK (for epoxy-based systems, half or less of that for thermoplastics) is what is normal,” he notes. Cool Polymers’s Miller says most of his company’s compounds have in-plane isotropy (flow direction and transverse to flow direction) but have lower conductivity in the through thickness direction.
Nishant Negandhi, technology manager at compounder Ovation Polymers Inc. (Optem; Medina, OH), sees the market for thermally conductive compounds as tailor made for small-to-mid sized compounders such as his, which began commercially marketing them last year. “We not only supply thermal conductivity, but can couple it with other functional requirements” such as processability, chemical resistance and heat stability, he notes. Optem’s compounds are all based on thermoplastics, with melt compounding via twin-screw extrusion. Negandhi says competitors using the same process have reported through-plane conductivity for thermoplastic compounds as high as 2-2.25 W/mK; Optem claims it has achieved through-plane conductivity levels up to 3-3.5W/mK in thermoplastics.
Most programs for these materials still are in developmental stages, says Negandhi; by the end of 2008, the volumes for the firm’s Nemcon H thermally conductive compounds should be in the range of 20,000-25,000 lbs/year, he says, for applications in automotive, electronics, medical and aerospace. Non-disclosure agreements prevent him from naming customers. Optem markets its Nemcon H compounds with a variety of polymer matrices.
In answers to questions from MPW , Luca Posca, technical service coordinator at Italian compounder Lati (Vedano Olona, Italy), reports his firm has used “special ceramic fillers” to improve the overall thermal behavior of its compounds. For instance, the Laticonther range offers in-plane conductivity averaging 10 W/mK (evaluation by laser-flash technique), with through-plane conductivity very dependent on thickness and shear during molding, but averaging about 3 W/mK. Another grade in that range, filled with up to 70% graphite, offers in-plane conductivity averaging 15 W/mK and through-plane conductivity of 7 W/mK, he says.
Graphite and other fillers used for conductivity can take a toll on a processing machine, and Negandhi says his firm’s extruders do see screw wear; however, post-compounding, customers have seen no such wear problems.
Though Cool Polymers’ track record of commercial sales extends back almost 10 years, Miller says the firm understands thermally conductive plastics are sill relatively new to many, and so offers a complete set of services—design help, mold design and manufacturing, even prototype production and short-run molding on six presses at the firm. But although there are some minor “tweaks” required, he says designing injection molds for thermally conductive compounds is not rocket science. “There are some basic design rules to follow; you’re molding a material that throws off heat, so the cooling time, and cycle time, is much lower,” but processors also need to design so that this exothermic behavior does not cause freeze-off. Nothing fancy, he says, and processors can be off and processing.— [email protected]
Inteplast Pioneers Mass Balance Certified BOPP Film
Addex to Unveil Auto-Profile for Rotating Dies at NPE 2024
Breaking News in Flexible Packaging March 2024
Woman Engineer Explains Why She’s ‘Sorry, Not Sorry’ for Her Ambition
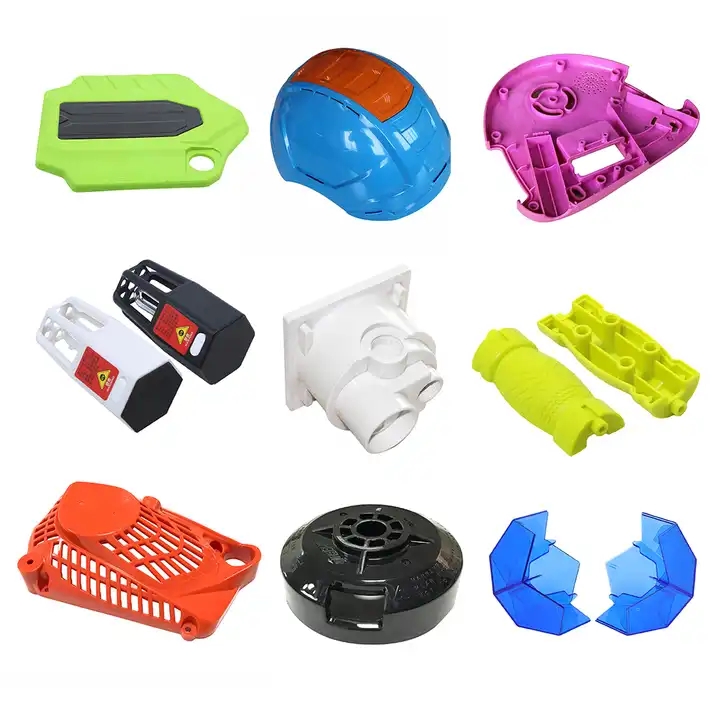
Ejector Rod Injection Molding Copyright © 2024 All rights reserved. Informa Markets, a trading division of Informa PLC.