Ragasco composite cylinders for LPG will become part of Worthington’s Building Products business, while Hexagon/Worthington Enterprises JV will target expanding storage and transport of CNG and hydrogen.
The 19-seat hybrid-electric aircraft was conceived to use composite and metal construction. Aura Aero has signed a PAC with EASA to finalize the framework for its CS-23 category certification. Sound Absorbing Foam
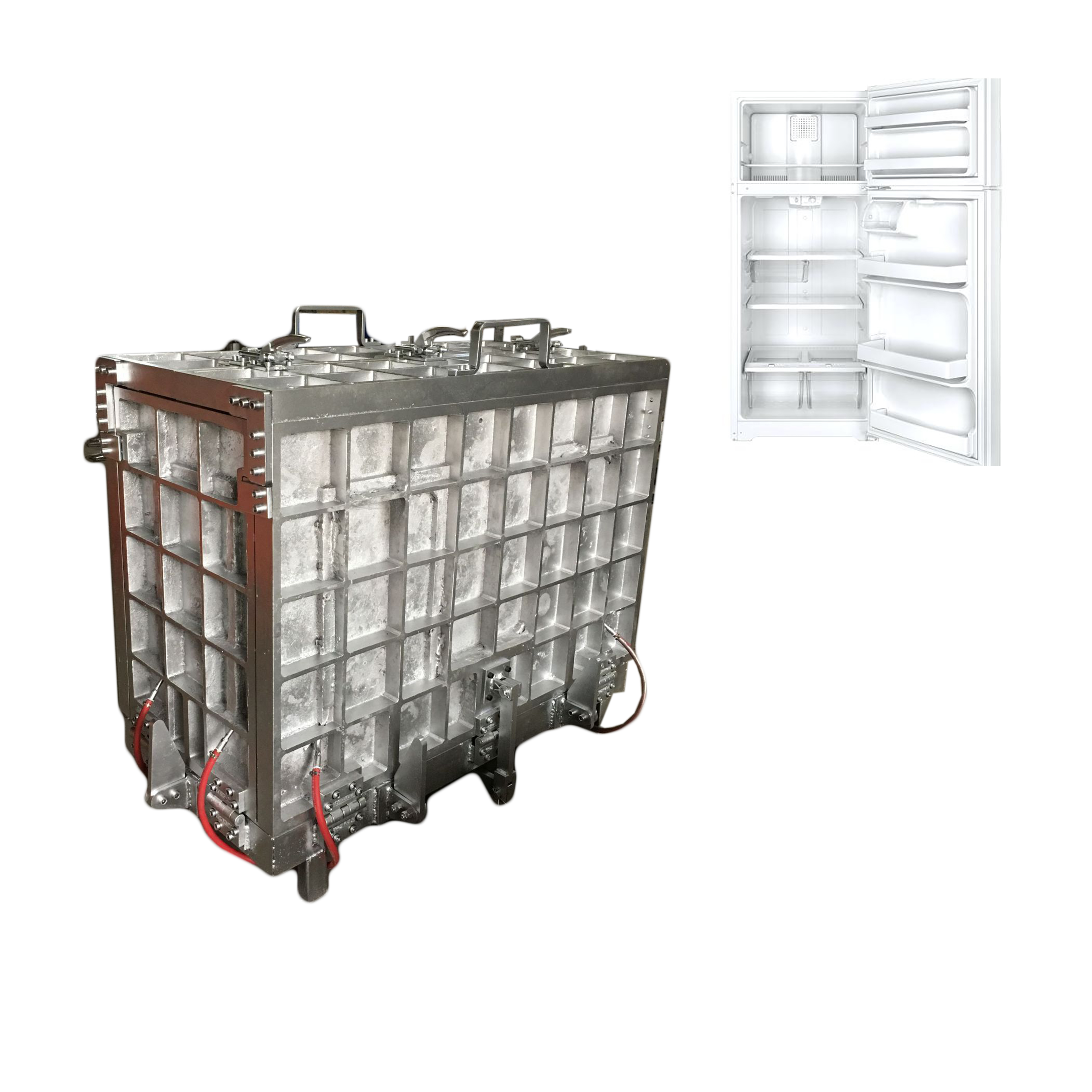
Brudeli’s patented plug-in Powerhybrid technology will use Hexagon Agility CNG/RNG fuel system with Type 4 tanks, enabling Class 7 and 8 trucks to meet ACT and ACF regulations.
Final airworthiness criteria provides a solidified path for Archer to achieve type certification for its eVTOL aircraft.
Positive progress during eVTOL prototype testing approaches full transition to forward flight, aids in final full-scale aircraft design for completion and testing in 2026.
Lilium is keen to expand its industrial footprint through leveraging of France’s aerospace heritage and vast supplier base in aerospace and electrification, in preparation for the eVTOL aircraft market demand.
An Aurora and Boeing team advances its high-speed, vertical lift concept to the preliminary design phase, which features three lift fans, a more refined composite exterior and an uncrewed cockpit.
Nesting, design, GUI and viewing features have been improved or added to the composites design software tool.
Ingersoll Masterprint LFAM printer will be used to produce and demonstrate 100% recyclable tooling that could cut large composite blade development cycles and tooling costs by as much as 50%.
Key structural elements for a 6-meter section of the Airbus biomimetic wing were undertaken by NCC engineering specialists to produce 28 one-off flying parts.
Pioneer in mandrel-based reinforced rubber and composite products, TANIQ offers TaniqWindPro software and robotic winding expertise for composite pressure vessels and more.
Designer and builder of compression molds for composite structures installs seven-axis CNC deep-hole drilling and milling machine to improve productivity.
Passion for rock climbing leads to durable, 30% lighter cam using Additive Molding.
CAMX 2024: Rishon, which combines RCF Technologies’ elastomer and composite fabrics, bonds to metals and most composites, while providing high-temperature operations, sound and vibration absorption, heat insulation and more.
End-of-life wind turbine recycling efforts are underway after the first REWIND consortium kick-off in May.
Brudeli’s patented plug-in Powerhybrid technology will use Hexagon Agility CNG/RNG fuel system with Type 4 tanks, enabling Class 7 and 8 trucks to meet ACT and ACF regulations.
3D printing materials portfolio now extends from unfilled PVDF to carbon-fiber-reinforced PVDF, adding to the end product’s high performance and chemical resistance.
Envalior 30% glass fiber-reinforced Akulon RePurposed material helps Ahrend achieve lighter task chair with closed-loop value chain and reduced emissions.
VacPuc is expanding its range of global distributors to deliver its vacuum pressure measurement solution to the composites market.
GZero opens another location in West Chester, Ohio, to optimize the production of fiber-reinforced 3D printed parts for service bureau customers.
Ultra-lightweight and made of recycled composites, the Eco Bracket cuts weight and cost in half and reduces CO2 emissions, in addition to providing high performance.
CAMX 2024: ColorForm and long fiber injection (LFI) technologies by KraussMaffei support automotive, consumer and other end markets in their quest for high-performance, lightweight parts with aesthetic qualities.
CAMX 2024: Machine knives and industrial razor blades supplier American Cutting Edge offers composites manufacturers staple and custom cutting options.
3D printing materials portfolio now extends from unfilled PVDF to carbon-fiber-reinforced PVDF, adding to the end product’s high performance and chemical resistance.
Increasingly, prototype and production-ready smart devices featuring thermoplastic composite cases and other components provide lightweight, optimized sustainable alternatives to metal.
CW explores key composite developments that have shaped how we see and think about the industry today.
Knowing the fundamentals for reading drawings — including master ply tables, ply definition diagrams and more — lays a foundation for proper composite design evaluation.
Performing regular maintenance of the layup tool for successful sealing and release is required to reduce the risk of part adherence.
With COVID in the past and passengers flying again, commercial aircraft production is ramping up. The aerocomposites supply chain is busy developing new M&P for an approaching next-generation aircraft program.
Electrification and a focus on sustainability lead to opportunities and innovations in composites, from battery enclosures to structural components and more.
KraussMaffei will explain in-situ polyurethane (PUR) overmolding of injection-molded and composite parts and the development of this technology over the last decade. Waruna Seneviratne, director of the Advanced Technologies Lab for Aerospace Systems (ATLAS), will discuss how aerospace and advanced air mobility (AAM) markets can capitalize on this high-rate manufacturing solution. Agenda: What is ColorForm: process, equipment and tooling Pros and cons of the technology High technology solution examples: ColorForm automotive Market references in automotive Demand for future commercial aviation and both AAM and urban air mobility (UAM) What aerospace can learn from automotive for addressing demand for high-rate manufacturing Technological advances enabling material and process improvements for the future Role of ATLAS manufacturing innovation center for promoting advanced manufacturing and workforce development Road map for certification through manufacturing demonstrations
Thermoplastic material systems have been used in aerospace for decades. Their use and adoption continues to grow and Trelleborg has been on the leading edge of development for many of these systems. In this webinar, Trelleborg will be presenting a range of topics from the use of in-situ, automated fiber placement of thermoplastics prepreg for structural and functional products to complex injection molding of thermoplastic interior pieces. It will explore some of the benefits these products provide and the potential for future growth and development. Agenda: Current state of thermoplastics in aerospace Thermoplastic composite use cases for high-performance electric motors and torque tubes Injection-molded thermoplastic interior pieces The future of potential for thermoplastic applications for aerospace
Find out how outsourced, costly tooling can be produced in-house to overcome bottlenecks, reduce costs and protect IP. Agenda: Explore durable casting materials that can be 3D-printed in complex designs Discover industry-proven Sika materials now available for high-speed, additive tooling Explore the benefits of thermoset molds that ensure uniform expansion, optimum bonding with the end part, as well as high durability
Explore next-gen composites engineering solutions in this webinar. Uncover the capabilities of Fives' Composite Optical Automated Surface Tracking (COAST) platform and Advanced Composites Environment Suite (ACES) software, optimizing design, production and quality control. Gain insights into how these end-to-end solutions enhance productivity and deliver measurable results. Join Fives to discover the transformative benefits of a fully-integrated digital solution for revolutionizing manufacturing processes. Agenda: Digital suite: CAD, CAM, robotic automated fiber placement (RAFP) and COAST Video demonstration Value propositions: maintenance and root cause analysis Product offerings (price, etc.) Customer use case
In addition to its proven fire resistance as a pure foam and within a sandwich composite system, the new material offers efficient manufacturing of 3-dimensional geometries and opens new possibilities for direct function integration. Agenda: Manufacturing process of thermoplastic particle foams Sandwich composite component requirements of commercial aircraft interior structures (e.g. FST, Heat Release) Function integration into net shape molded foam parts (e.g. inserts) Potential use-cases in fire critical applications
After having established a strong foundation in kinetic models in a previous webinar, part two delves into the exciting realm of machine learning and its transformative potential for composite manufacturing. While kinetic models have served the industry well, the growing complexity of composite manufacturing demands more sophisticated approaches. In this session, sensXPERT will explore innovative pathways to supercharge your production efficiency and enhance sustainability beyond the limits of traditional models. See how machine learning empowers composite manufacturers to achieve unprecedented accuracy in predicting key production parameters such as temperature, pressure and cure time. This translates to reduced cycle times and waste while increasing production throughput to maximize efficiency. SensXPERT will provide concrete examples and case studies demonstrating how to bridge the gap between meticulously-controlled laboratory experiments and the realities of the production floor, overcoming the limitations of kinetic models. Agenda: Define machine learning, its applications and their impact on composite manufacturing Explore real-world case studies in diverse composites manufacturing applications and how they exploit integration options Correlation analysis: uncovering hidden relationships between process parameters and product outcomes Time series analysis: forecasting production trends Anomaly detection: identifying irregularities
The JEC Forum Southeast Asia is an event organised by JEC The JEC Forum Southeast Asia is organised on June 11 and 12, 2024, by JEC, in partnership with the Thai Composites Association (TCA), bringing together the composite materials community in Southeast Asia.
The 14th edition of the Graphene Conference will take place June 25-28, 2024, in Madrid, Spain. The international gathering includes thematic workshops, B2B networking and an Industrial Forum that dives into a variety of topics, including the latest developments in graphene production methods towards wide scale commercialization and examples of graphene in electronics, energy storage, aerospace and barrier applications.
The International Composites Summit (ICS) is renowned as the only solely focused UK event for professionals involved in the composites industry. ICS promises to be a unique platform for knowledge sharing, networking, and exploring the latest advancements in composite materials internationally, bringing people together to do business.
Join us at the ACCE 2023 event and learn about how the automotive and transportation industries are advancing with composites playing a key role in the development of electric vehicles and sustainability initiatives worldwide. Lightweight composites are ideal materials for improving vehicle performance, reducing mass, extending range and compensating for battery weight. Polymer composites are enabling lower emission vehicles, reducing the carbon footprint and saving energy to benefit the environment now and in the future. Thermoset and thermoplastic composites are the key to EV, Mobility and Sustainability.
Thousands of people visit our Supplier Guide every day to source equipment and materials. Get in front of them with a free company profile.
Jetcam’s latest white paper explores the critical aspects of nesting in composites manufacturing, and strategies to balance material efficiency and kitting speed.
Arris presents mechanical testing results of an Arris-designed natural fiber thermoplastic composite in comparison to similarly produced glass and carbon fiber-based materials.
Cevotec, a tank manufacturer, Roth Composite Machinery and Cikoni, have undertaken a comprehensive project to explore and demonstrate the impact of dome reinforcements using FPP technology for composite tanks.
Initial demonstration in furniture shows properties two to nine times higher than plywood, OOA molding for uniquely shaped components.
The composite tubes white paper explores some of the considerations for specifying composite tubes, such as mechanical properties, maintenance requirements and more.
Foundational research discusses the current carbon fiber recycling landscape in Utah, and evaluates potential strategies and policies that could enhance this sustainable practice in the region.
In 2018, Teijin broke ground on a facility that is reportedly the largest capacity carbon fiber line currently in existence. The line has been fully functional for nearly two years and has plenty of room for expansion.
Spanish startup Reinforce3D’s continuous fiber injection process (CFIP) involves injection of fibers and liquid resin into hollow parts made from any material. Potential applications include sporting goods, aerospace and automotive components, and more.
Longtime parts manufacturer offers more than composites welding. CW’s conversation with CEO Kjelt van Rijswijk explains KVE’s vision with Daher and where it’s headed.
Steptics industrializes production of CFRP prostheses, enabling hundreds of parts/day and 50% lower cost.
Novel reinforcing patch uses braided sleeve to boost the load-carrying capacity of composite bolted joints.
Workforce pain points and various logistical challenges are putting operations resilience and flexibility to the test, but Industry 4.0 advancements could be the key to composites manufacturers’ transformation.
Brudeli’s patented plug-in Powerhybrid technology will use Hexagon Agility CNG/RNG fuel system with Type 4 tanks, enabling Class 7 and 8 trucks to meet ACT and ACF regulations.
Envalior 30% glass fiber-reinforced Akulon RePurposed material helps Ahrend achieve lighter task chair with closed-loop value chain and reduced emissions.
Hydrogen storage and high-voltage battery system to support Class 8 heavy-duty fuel cell powertrains developed by Toyota.
Future cabin concepts, rCF floor coverings and panels, noise regulation and other efficiencies will be tested this year using a 777-200ER aircraft.
Markus Beer of Forward Engineering addresses definitions of sustainability, how to approach sustainability goals, the role of life cycle analysis (LCA) and social, environmental and governmental driving forces. Watch his “CW Tech Days: Sustainability” presentation.
Themes at the forefront of JEC World 2024 included solutions for mobility applications and sustainable materials, technologies and processes for composites manufacturing.
Closed mold processes have many advantages over open molding. In this knowledge center, learn the basics and vital tools needed to produce parts accurately.
The composites industry is increasingly recognizing the imperative of sustainability in its operations. As demand for lightweight and durable materials rises across various sectors, such as automotive, aerospace, and construction, there is a growing awareness of the environmental impact associated with traditional composite manufacturing processes.
CW’s editors are tracking the latest trends and developments in tooling, from the basics to new developments. This collection, presented by Composites One, features four recent CW stories that detail a range of tooling technologies, processes and materials.
In the Automated Composites Knowledge Center, CGTech brings you vital information about all things automated composites.
CompositesWorld’s CW Tech Days: Infrastructure event offers a series of expert presentations on composite materials, processes and applications that should and will be considered for use in the infrastructure and construction markets.
Explore the cutting-edge composites industry, as experts delve into the materials, tooling, and manufacturing hurdles of meeting the demands of the promising advanced air mobility (AAM) market. Join us at CW Tech Days to unlock the future of efficient composites fabrication operations.
Thermoplastics for Large Structures, experts explored the materials and processing technologies that are enabling the transition to large-part manufacturing.
Explore the technologies, materials, and strategies that can help composites manufacturers become more sustainable.
A report on the demand for hydrogen as an energy source and the role composites might play in the transport and storage of hydrogen.
This collection features detail the current state of the industry and recent success stories across aerospace, automotive and rail applications.
This collection details the basics, challenges, and future of thermoplastic composites technology, with particular emphasis on their use for commercial aerospace primary structures.
This collection features recent CW stories that detail a range of tooling technologies, processes and materials.
CAMX 2023: Infinite Hybrid, a technology from Foam Equipment & Consulting Co., enables continuous production without secondary operations.
Photo Credit: Foam Equipment & Consulting Co.
The Infinite Hybrid method, from Foam Equipment & Consulting Co. (Earth City, Mo., U.S.), enables the continuous production of particle foam and sandwich components, offering a multitude of applications across various sectors. Particle foam is based on thermoplastic polymers and consists of over 90% air, which makes it well-suited for lightweight applications. In contrast to conventional manufacturing methods where individual parts are produced separately and then assembled, Infinite Hybrid enables the continuous production of components.
The technology is based on the combination of Atecarma and Teubert continuous compression molding (CCM) technology. The particle foams are treated with Atecarma activator in advance. The materials, with or without sandwich layers, are automatically fed into the CCM machine, where they are compacted, heated, cooled, stabilized and demolded step by step. By employing high precision tools and advanced control systems, Infinite Hybrid can create flat panels and sandwich components in just one production step without the need for secondary operations.
In addition to continuous production, the company says Infinite Hybrid also offers other benefits, including weight reduction, cost efficiency and design freedom. By using particle foam, components with lower density can be produced. This results in a reduction in weight for components, particularly in the automotive and aerospace industries. Through continuous production, costs associated with tool changes and the assembly of individual parts are minimized, leading to more efficient manufacturing processes and reduced production costs. Design freedom is made possible through Atecarma. Complex combinations of different materials are said to be more easily achieved, providing the opportunity for innovative and aesthetically pleasing products.
The company says that Infinite Hybrid technology has the potential to fundamentally transform the way components are manufactured and used. Through the benefits it provides in weight reduction, cost efficiency and design freedom, it can expands perspectives across industries.
Flat tank enabling standard platform for BEV and FCEV uses thermoplastic and thermoset composites, overwrapped skeleton design in pursuit of 25% more H2 storage.
GFRP eliminates risk of corrosion and increases durability fourfold for reinforced concrete that meets future demands as traffic, urbanization and extreme weather increase.
As the need for carbon fiber rises, can recycling fill the gap?
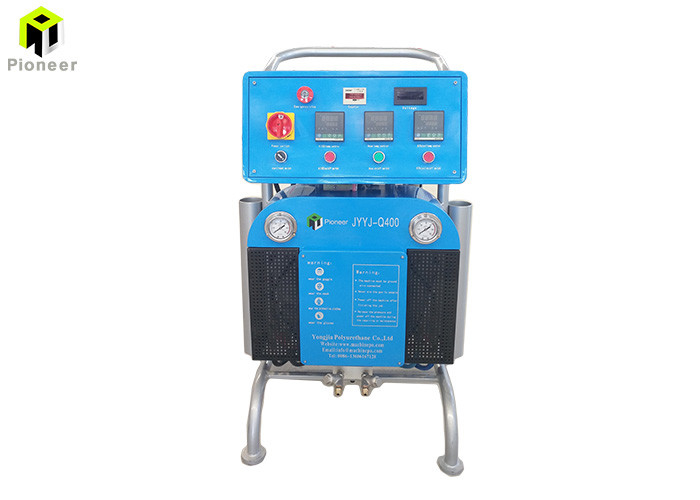
Polyurea Pool Coating CompositesWorld is the source for reliable news and information on what’s happening in fiber-reinforced composites manufacturing. About Us