Tripled space and capacity to potentially grow composite tank production to 30,000+ tanks/year, equipment investments enable manufacturer to handle larger orders, streamline operations.
Multiple commercial truck-type high-pressure tanks have been extended to maritime applications. Fiberglass Floor Grating
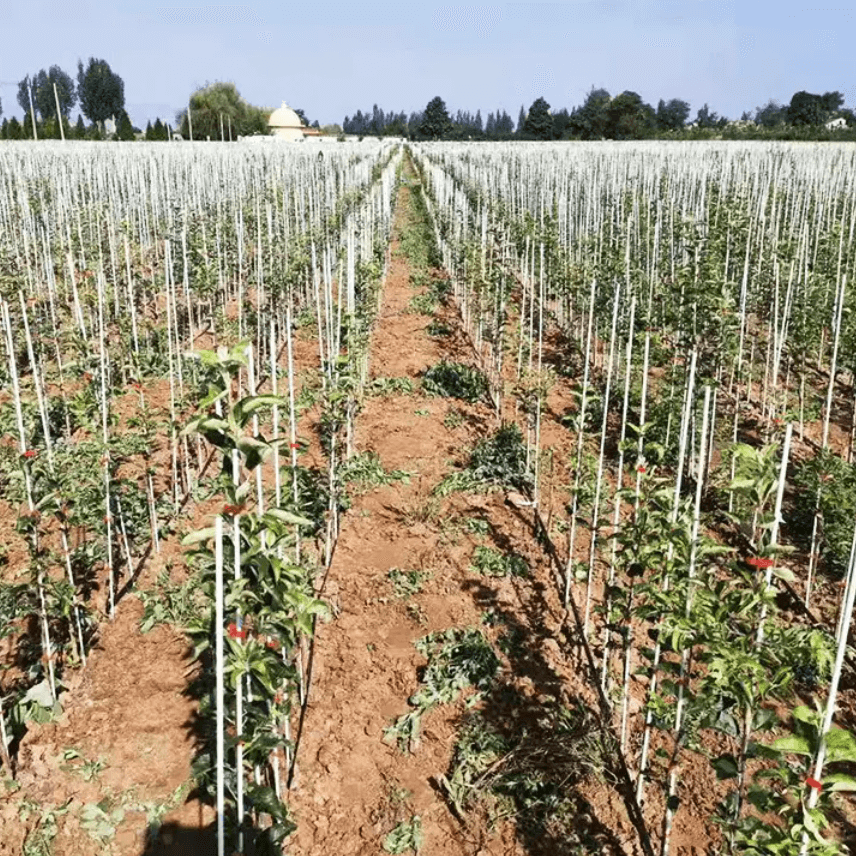
First units off the battery assembly line in Munich will be used for verification testing ahead of first piloted flight, targeted for end of 2024.
DOE MAKE IT prize supports U.S.-based manufacturing of clean energy technology components for a diverse range of market applications.
Pioneer in mandrel-based reinforced rubber and composite products, TANIQ offers TaniqWindPro software and robotic winding expertise for composite pressure vessels and more.
With production, type and standard airworthiness certification under its belt the AAM company is cleared for mass production of the EH216-S.
Pioneer in mandrel-based reinforced rubber and composite products, TANIQ offers TaniqWindPro software and robotic winding expertise for composite pressure vessels and more.
Designer and builder of compression molds for composite structures installs seven-axis CNC deep-hole drilling and milling machine to improve productivity.
Strategic MOU initially introduces SikaBiresin CIM 120 and SikaBiresin CIM 80 to serve crucial composites market needs for 3D printing tooling, prototyping and more.
Through this strategic collaboration, BEAD’s additive and subtractive capabilities for large-scale AM composite tooling production are made more accessible.
Plyable continues to rid composites engineers of workflow bottlenecks through an end-to-end automated system — from mold design to quotation to manufacturing fulfillment.
JEC World 2024: The RAMPF Group is bringing together three of its divisions — RAMPF Composite Solutions, RAMPF Tooling Solutions, and RAMPF Group Inc. — delivering a variety of materials and services to the composites industry.
Salt Lake City state-of-the-art facility and office will enable a high-tech closed-loop ecosystem to recycle and repurpose composites in the U.S.
New funding round supports enhanced production capacity, commercial automotive opportunities and new market support for flax fiber-based composite solutions.
Bossard worked with an OEM and Tier supplier team to meet tight electrical insulation and packaging tolerances while reducing tooling, molding and assembly costs.
Themes at the forefront of JEC World 2024 included solutions for mobility applications and sustainable materials, technologies and processes for composites manufacturing.
Australian composites manufacturer offers a scalable building solution, already established in a pedestrian bridge application, to tackle unprocessed soft plastics waste.
Exel material waste will go through Fairmat’s reconstitution process to produce second-generation CFRP chips, enabling a closed-loop ecosystem.
The new market study identifies key players in a $785 million global market that has grown by 21% year on year.
The Italy-based companies merge technological know-how to develop novel systems for the processing and assembly of light alloys and carbon fiber components.
Patented process technology increases quality, reliability and machine utilization for composite laminate production.
Pioneer in mandrel-based reinforced rubber and composite products, TANIQ offers TaniqWindPro software and robotic winding expertise for composite pressure vessels and more.
ILAuNCH partnership, joined by ANU and New Frontier Technologies, will develop a qualified manufacturing process that will directly contribute to the development of launch vehicle development.
Materialise expands additive manufacturing portfolio with early adoption of new HP PA 12S and integration of PA 11 and PA-CF materials.
Increasingly, prototype and production-ready smart devices featuring thermoplastic composite cases and other components provide lightweight, optimized sustainable alternatives to metal.
CW explores key composite developments that have shaped how we see and think about the industry today.
Knowing the fundamentals for reading drawings — including master ply tables, ply definition diagrams and more — lays a foundation for proper composite design evaluation.
Performing regular maintenance of the layup tool for successful sealing and release is required to reduce the risk of part adherence.
With COVID in the past and passengers flying again, commercial aircraft production is ramping up. The aerocomposites supply chain is busy developing new M&P for an approaching next-generation aircraft program.
Electrification and a focus on sustainability lead to opportunities and innovations in composites, from battery enclosures to structural components and more.
In this webinar, Instron will discuss the different solutions for strain measurement on composite materials, such as: strain gauges, clip-on extensometers, video extensometers and digital image correlation (DIC). It will discuss the advantages and disadvantages of each and when you might prefer one method over another. Agenda: Brief introduction to composite materials and properties Strain measurement techniques for coupon testing Examples of strain measurement for various test types including: in-plane tensile, compression, through thickness and v-notch shear
As part three of the webinar series about composites manufacturing processes, this webinar will focus on the two main processes to manufacture semi-finished goods and the composites resulting from it: sheet molding compounding (SMC) and prepreg technology. This presentation will briefly highlight the advantages and challenges. The main part of the webinars will showcase product recommendations from Evonik's portfolio and how they can be used to enhance the performance of the final composite materials to meet the requirements from the automotive, aerospace and sporting goods industries.
This webinar will cover a range of honeycomb products, how to best select the right honeycomb for particular applications and design guidelines for honeycomb-cored structures. Agenda: Honeycomb overview Configuration and applications General considerations and quality standards Methods and methodology for shaping core Core forming Stabilization CNC machining Case studies Cost progression
After having established a strong foundation in kinetic models in a previous webinar, part two delves into the exciting realm of machine learning and its transformative potential for composite manufacturing. While kinetic models have served the industry well, the growing complexity of composite manufacturing demands more sophisticated approaches. In this session, sensXPERT will explore innovative pathways to supercharge your production efficiency and enhance sustainability beyond the limits of traditional models. See how machine learning empowers composite manufacturers to achieve unprecedented accuracy in predicting key production parameters such as temperature, pressure and cure time. This translates to reduced cycle times and waste while increasing production throughput to maximize efficiency. SensXPERT will provide concrete examples and case studies demonstrating how to bridge the gap between meticulously-controlled laboratory experiments and the realities of the production floor, overcoming the limitations of kinetic models. Agenda: Define machine learning, its applications and their impact on composite manufacturing Explore real-world case studies in diverse composites manufacturing applications and how they exploit integration options Correlation analysis: uncovering hidden relationships between process parameters and product outcomes Time series analysis: forecasting production trends Anomaly detection: identifying irregularities
As part one of the webinar series about composites manufacturing processes, this webinar will provide an insightful overview of liquid composite molding (LCM) processes, including: vacuum-assisted resin infusion (VARI), resin transfer molding (RTM) and wet compression molding (WCM). Evonik will discuss the specific requirements these methods impose on epoxy systems, particularly highlighting the critical role of the curing agents in achieving optimal process performance and final composite material properties. Discover how Evonik's advanced epoxy curing agents are helpful for developing tailored, high-performance composites that meet the stringent requirements of various industries, including: aerospace, automotive and wind energy.
When developing new products and formulations, there are a large number of additive choices to improve a single property you are aiming for: tougheners, plasticizers, flame retardants, the list goes on. One promising additive is graphene and its derivatives, but most organizations don’t know where to begin, so development walls are hit early in the process and therefore projects can be abandoned before success. But your chances of success are drastically increased when you partner with industry experts that know what forms of graphene will meet your needs. In this webinar Mito Materials will discuss how to successfully source, formulate and deploy any graphene material in the world — and do it to your specs and timeline.
The 2nd EuReComp (“European recycling and circularity in large composite components”) Workshop will take place April 24, 2024 at the Aimen Technology Centre in Vigo, Spain. The April workshop is dedicated to fostering innovation and sustainability within the composites recycling sector. It will feature a comprehensive program that includes keynote presentations by leading experts, interactive discussions on the circular economy and hands-on demonstrations showcasing the newest research and technological developments.
ThermHex and Fraunhofer are set to host the third Composite-Sandwich Conference in Halle (Saale), Germany, on April 24-25, 2024. The conference will provide the opportunity for engineers and scientists from across the composites industry to explore new fields of application of sandwich materials and network with some of the leading minds in the sector. Not only will there be lectures from Daimler Truck, Porsche, Audi, Airbus Helicopters, Evonik Performance Foams and more, but both ThermHex Waben and Fraunhofer Pilot Plant Center for Polymer Synthesis and Processing will open up the doors to their facilities for all participants to receive guided tours of both facilities.
Join leaders in the thermoset industry at TOPCON 2024 where you’ll learn about opportunities for thermoset innovative technologies in multiple markets. The event includes keynote speakers, panel discussions, technical presentations, exhibits and a special program dedicated to growing the industry.
The most knowledgeable minds in clean energy join ACP’s CLEANPOWER event to chart the future of this powerful industry and discuss the opportunities ahead. This is the must-attend conference of the year. CLEANPOWER grows businesses by gathering key decision makers and stakeholders across the wind, solar, storage, hydrogen, and transmission industries for discussion, deal making, networking and a whole lot of fun. We’re calling all manufacturers, construction firms, owner operators, utilities, financial firms, corporate buyers and sector members to join our landmark event. Mark your calendar to join us next year in Minneapolis, MN May 6-9 at the most anticipated clean energy trade show of the year.
The Offshore Technology Conference (OTC) is where energy professionals meet to exchange ideas and opinions to advance scientific and technical knowledge for offshore resources and environmental matters. Since 1969, OTC’s flagship conference is held annually at NRG Park (formerly Reliant Park) in Houston. OTC has expanded technically and globally with OTC Brasil and OTC Asia. OTC is sponsored by 13 industry organizations and societies, who work cooperatively to develop the technical program. OTC also has endorsing and supporting organizations
Hosted by the Society for the Advancement of Material and Process Engineering (SAMPE), SAMPE 2024 is North America's premier advanced materials and process engineering conference and exhibition tradeshow. SAMPE 2024 is where the advanced materials community comes together for face-to-face meetings, top-level education sessions and panels lead by the industry’s leaders and innovators.
Thousands of people visit our Supplier Guide every day to source equipment and materials. Get in front of them with a free company profile.
Jetcam’s latest white paper explores the critical aspects of nesting in composites manufacturing, and strategies to balance material efficiency and kitting speed.
Arris presents mechanical testing results of an Arris-designed natural fiber thermoplastic composite in comparison to similarly produced glass and carbon fiber-based materials.
Cevotec, a tank manufacturer, Roth Composite Machinery and Cikoni, have undertaken a comprehensive project to explore and demonstrate the impact of dome reinforcements using FPP technology for composite tanks.
Initial demonstration in furniture shows properties two to nine times higher than plywood, OOA molding for uniquely shaped components.
The composite tubes white paper explores some of the considerations for specifying composite tubes, such as mechanical properties, maintenance requirements and more.
Foundational research discusses the current carbon fiber recycling landscape in Utah, and evaluates potential strategies and policies that could enhance this sustainable practice in the region.
Themes at the forefront of JEC World 2024 included solutions for mobility applications and sustainable materials, technologies and processes for composites manufacturing.
As the number of battery and fuel cell electric vehicles (EVs) grows, so do the opportunities for composites in battery enclosures and components for fuel cells.
A second new ASTM-standardized test method assesses the damage tolerance of sandwich composites under flexural loading.
The GBI: Composites Fabricating still contracted in March, though it landed just one point shy of 50, which could eventually lead it into expansion territory.
Pioneer in mandrel-based reinforced rubber and composite products, TANIQ offers TaniqWindPro software and robotic winding expertise for composite pressure vessels and more.
CW senior technical editor Ginger Gardiner discusses some of the developments and demonstrators shown at the industry’s largest composites exhibition and conference.
CW technical editor Hannah Mason discusses trends seen at this year’s JEC World trade show, including sustainability-focused technologies and commitments, the Paris Olympics amongst other topics.
Automotive technology supplier Forvia shares sustainability goals and recent developments aimed at bio-based and recycled materials and ramping up hydrogen tank production for clean mobility.
Customer decarbonization goals demand supply chains with sustainable business practices. Here are four considerations for supporting those goals that will be discussed further at CW Tech Days.
Airbus subsidiary CTC uses new technology to measure energy use in machine components and processes to optimize equipment, production lines and guide decisions for future composites.
Three materials — bio-based carbon fibers, natural stone and biochar — act as an alternative to reinforced concrete in a house wall demonstrator in the DACCUS-Pre project.
As companies strive to meet zero-emissions goals, evaluating a product’s carbon footprint is vital. Life cycle assessment (LCA) is one tool composites industry OEMs and Tier suppliers are using to move toward sustainability targets.
In the Automated Composites Knowledge Center, CGTech brings you vital information about all things automated composites.
This CW Tech Days event will explore the technologies, materials, and strategies that can help composites manufacturers become more sustainable.
Explore the cutting-edge composites industry, as experts delve into the materials, tooling, and manufacturing hurdles of meeting the demands of the promising advanced air mobility (AAM) market. Join us at CW Tech Days to unlock the future of efficient composites fabrication operations.
During CW Tech Days: Thermoplastics for Large Structures, experts explored the materials and processing technologies that are enabling the transition to large-part manufacturing.
CompositesWorld’s CW Tech Days: Infrastructure event offers a series of expert presentations on composite materials, processes and applications that should and will be considered for use in the infrastructure and construction markets.
CW’s editors are tracking the latest trends and developments in tooling, from the basics to new developments. This collection, presented by Composites One, features four recent CW stories that detail a range of tooling technologies, processes and materials.
Closed mold processes offer many advantages over open molding. This knowledge center details the basics of closed mold methods and the products and tools essential to producing a part correctly.
The composites industry is increasingly recognizing the imperative of sustainability in its operations. As demand for lightweight and durable materials rises across various sectors, such as automotive, aerospace, and construction, there is a growing awareness of the environmental impact associated with traditional composite manufacturing processes.
CompositesWorld’s CW Tech Days: Infrastructure event offers a series of expert presentations on composite materials, processes and applications that should and will be considered for use in the infrastructure and construction markets.
Explore the cutting-edge composites industry, as experts delve into the materials, tooling, and manufacturing hurdles of meeting the demands of the promising advanced air mobility (AAM) market. Join us at CW Tech Days to unlock the future of efficient composites fabrication operations.
Thermoplastics for Large Structures, experts explored the materials and processing technologies that are enabling the transition to large-part manufacturing.
Explore the technologies, materials, and strategies that can help composites manufacturers become more sustainable.
A report on the demand for hydrogen as an energy source and the role composites might play in the transport and storage of hydrogen.
This collection features detail the current state of the industry and recent success stories across aerospace, automotive and rail applications.
This collection details the basics, challenges, and future of thermoplastic composites technology, with particular emphasis on their use for commercial aerospace primary structures.
This collection features recent CW stories that detail a range of tooling technologies, processes and materials.
Partnership with Chinese automotive manufacturer will see the implementation of pultruded profiles in various bus models, backed by weight savings, complex geometries and long life.
Source | Foton Bus and Coach Co.
Finnish composites manufacturer Exel Composites (Vantaa) has secured a new project with Chinese automotive manufacturer Foton Bus and Coach Co. (Beijing) to supply pultruded glass fiber composite profiles. Per the agreement, signed in February 2024, the glass fiber profiles will be manufactured locally in China, and will be used to reduce the maintenance requirements and weight of Foton’s vehicles, due to composites’ corrosion resistant and lightweight properties. Additionally, the geometric design flexibility of composites will enable wider structural engineering possibilities than traditional metals, such as steel and aluminum.
Foton Bus and Coach Co., a subsidiary of BAIC, manufactures a wide range of commercial vehicles, including trucks, buses, vans and construction vehicles. In line with industry trends, Foton has shifted its focus to electric and hydrogen vehicle manufacturing, particularly in the bus and coach sector.
Exel Composites will produce a series of structural composite profiles for many different bus models. These profiles, including fiber-reinforced plastic (FRP) side panels, skirt panels and fake roofs, are manufactured using pultrusion technology with glass fiber. They offer greater tensile strength and durability while reducing density by 30%, compared to traditional aluminum profiles.
“Exel’s profiles improve our design process in ways that are only achievable with composite materials,” highlights Mr. He, head of group R&D for Foton Bus and Coach Co. “The geometric possibilities are key for complex-shaped structural components, and the weight savings of fiberglass compared to aluminum reduces strain on both the chassis and the battery. What’s more, composite panels don’t rust and can last for decades.”
Kathy Wang, executive VP for industrial solutions business unit at Exel Composites, notes that Exel has refined its pultrusion manufacturing process over many decades, achieving complex geometric profiles that match the strength of traditional aluminum, while remaining light in weight. “At the same time, the finished profile has a smooth surface finish, which eliminates the need for further processing,” Wang says. “Furthermore, unlike aluminum extrusions, which are limited to 0.3 meter in width and require multiple connections for larger panels, our composite profiles can extend up to 1.2 meters wide and 12 meters long. This ensures structural integrity and solidarity.”
Exel Composites can also use pultrusion for applications including interior air ducts, luggage racks, side shields and flooring, as well as pull-winding for small-diameter tubes, further reducing the energy consumption and weight of buses.
For related content, read “Pull-wound fiberglass composite 5G utility poles enable easier, faster installation.”
GKN Aerospace has spent the last five years developing materials strategies and resin transfer molding (RTM) for an aircraft trailing edge wing spar for the Airbus Wing of Tomorrow program.
There are numerous methods for fabricating composite components. Selection of a method for a particular part, therefore, will depend on the materials, the part design and end-use or application. Here's a guide to selection.
Purpose-built facility employs resin transfer infusion (RTI) and assembly technology to manufacture today’s composite A220 wings, and prepares for future new programs and production ramp-ups.
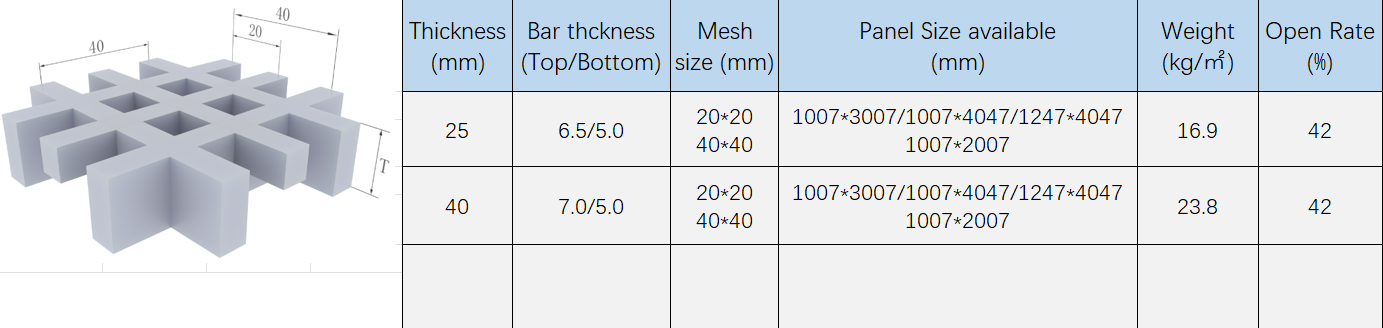
Molded Fiberglass Grating CompositesWorld is the source for reliable news and information on what’s happening in fiber-reinforced composites manufacturing. About Us