US cleanroom expert Mecart has completed an ISO 7 semiconductor cleanroom with ballroom-inspired design
Cleanroom MECART has delivered a dual-purpose custom cleanroom in Arizona for semiconductor manufacturing and R&D activities. Production process system
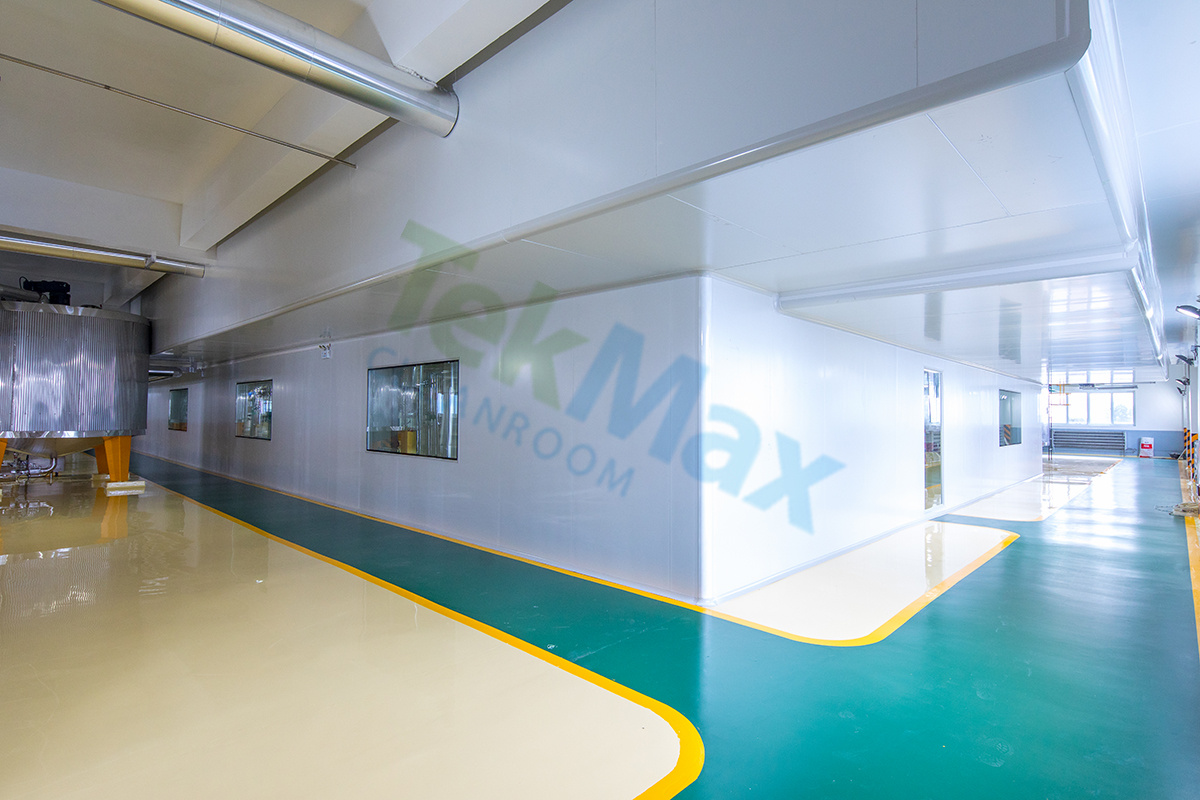
The ISO 7 cleanroom is to help the client deliver quality products and contribute to the technological landscape via their findings.
This case study explores the solutions MECART engineered to create a 10,000 sqft cleanroom facility segmented into 5 spaces, combining innovation with practicality to serve the client’s unique demands.
The cleanroom of the client is designed to serve two distinct purposes. MECART tackled this challenge by designing one of the walls to feature an extensive array of large windows, stretching across its entire length
The semiconductor research and development cleanroom
The customer’s primary requirement is to achieve a Class 10,000 cleanroom cleanliness level to comply with federal 209E standards. The challenge lay in effectively utilizing the 3,700 sqft space while consistently maintaining these stringent standards daily.
The cleanroom of the client is designed to serve two distinct purposes. MECART tackled this challenge by designing one of the walls to feature an extensive array of large windows, stretching across its entire length. This feature transformed the space into a versatile setting that serves both as a process development cleanroom and a sophisticated showroom.
This strategic design allows clients and potential investors to observe the R&D process firsthand, enhancing transparency and engagement – all while never having to enter the cleanroom and abide by complex gowning procedures.
Custom-built oversize doors and different ceiling heights
Simultaneously, MECART’s engineering team addresses the client’s concerns regarding the frequent entry and exit of large equipment through conventional doors by manufacturing custom 120″ high by 82″ wide double swing doors.
The ceiling in this cleanroom was raised by two feet to accommodate the larger equipment. As a result, the ceiling height was increased from 9½ feet to 11½ feet, creating two different ceiling heights within the facility.
These solutions seamlessly integrate with the project’s design guidelines, prioritising maintenance simplicity, operational optimisation, and adherence to ISO Class 7 cleanroom parameters.
The adjacent space to the R&D area is a dedicated cleanroom for semiconductor manufacturing, which also meets the ISO 7 cleanroom standards. The 4,500 sqft semiconductor cleanroom is optimised for microdevices manufacturing.
Because this cleanroom environment houses smaller-sized equipment, MECART devised a cost-efficient strategy to restore the ceiling height to a standard 9½ feet to lower initial construction costs.
By reducing the ceiling height in the cleanroom for semiconductor manufacturing, MECART reduces the volume of air required to be filtered and treated by the HVAC system, ultimately enhancing the cost-effectiveness of the operational processes within the space.
Maintenance corridor with custom apertures
The maintenance corridor is a background zone with an ISO 8 cleanroom classification that covers over 1,000 sqft.
The shared corridor provides access to both the cleanroom for semiconductor manufacturing and the R&D cleanroom, with custom openings integrated into the adjoining wall panels to facilitate equipment feeds (mechanical, electrical, and plumbing).
The openings facilitate maintenance tasks without disrupting cleanroom operations.
MECART specialises in providing bespoke cleanrooms that can be adapted to varied surroundings, whether they are in a new building or an older facility that was not originally meant to receive cleanroom environments.
With the assistance of MECART, the customer was able to convert an old data center into a cutting-edge semiconductor fab cleanroom facility.
MECART designed and delivered a ballroom-inspired layout out of custom 13-foot-high modular cleanroom panels.
With the assistance of MECART, the customer was able to convert an old data center into a cutting-edge semiconductor fab cleanroom facility
Half of the panels feature a low-wall air return vent located at ground level, while the remaining panels have their air return vents situated beneath the raised floor, providing for effective air and particle removal in critical zones.
This semiconductor fab clean room‘s design includes numerous other elements that were tailor-made for the customer, such as the clean room’s raised floor and the HVAC system, amongst other things.
MECART integrated a raised floor into the customer’s cleanroom, as is customary in the semiconductor industry. The design of the client’s semiconductor fabrication facility includes a 2-foot-high raised flooring system in the cleanroom, which serves multiple purposes.
Maximising floor space and supplying essential utilities:
It houses essential utilities beneath the floor, facilitating the provision of substantial volumes of water and gas crucial for the equipment and processes. This arrangement ensures the efficient functioning of these systems and eliminates the need for overhead beams or pipes.
Optimising airflows & safeguarding the product:
Moreover, this raised floor design plays a vital role in optimising airflow within the cleanroom. The particles are pushed beneath the raised floor by the laminar airflow and then efficiently evacuated by low-wall air return systems built into MECART’s cleanroom wall panels.
This feature is key to maintaining a contaminant-free environment, as it effectively removes particles at their source, thereby protecting the integrity of production processes within the semiconductor fabrication cleanroom.
The clean room raised floor facilitates convenient modifications and reconfigurations to adapt to new equipment or workflow changes, without requiring significant structural alterations. A raised floor also allows flexible maintenance operations without disturbing cleanroom activity.
MECART’s heating, ventilation, and air conditioning specialist built a custom chilled water HVAC system that will draw air from the hot, dry air of Arizona’s arid desert region.
MECART also provided dedicated air handling units (AHUs) of a total of 62,000 cfm atop both the cleanroom for semiconductor manufacturing and the R&D room to achieve the customer’s requested 71°F temperature and 42% relative humidity.
These AHUs have also been designed to bring enough outdoor air to compensate for the 13,600 cfm of exhaust required by the client’s equipment. A custom design has been provided with multiple small AHUs in parallel instead of bigger ones to respect the short lead time required by the project.
Lowering operational expenses and environmental footprint:
MECART has implemented a cost-saving night mode in their HVAC system, which also helps to lower their environmental footprint.
The night mode keeps the differential pressures between rooms with lower ventilation rates (lower ACH) when the cleanroom is at rest, lowering their HVAC energy bill.
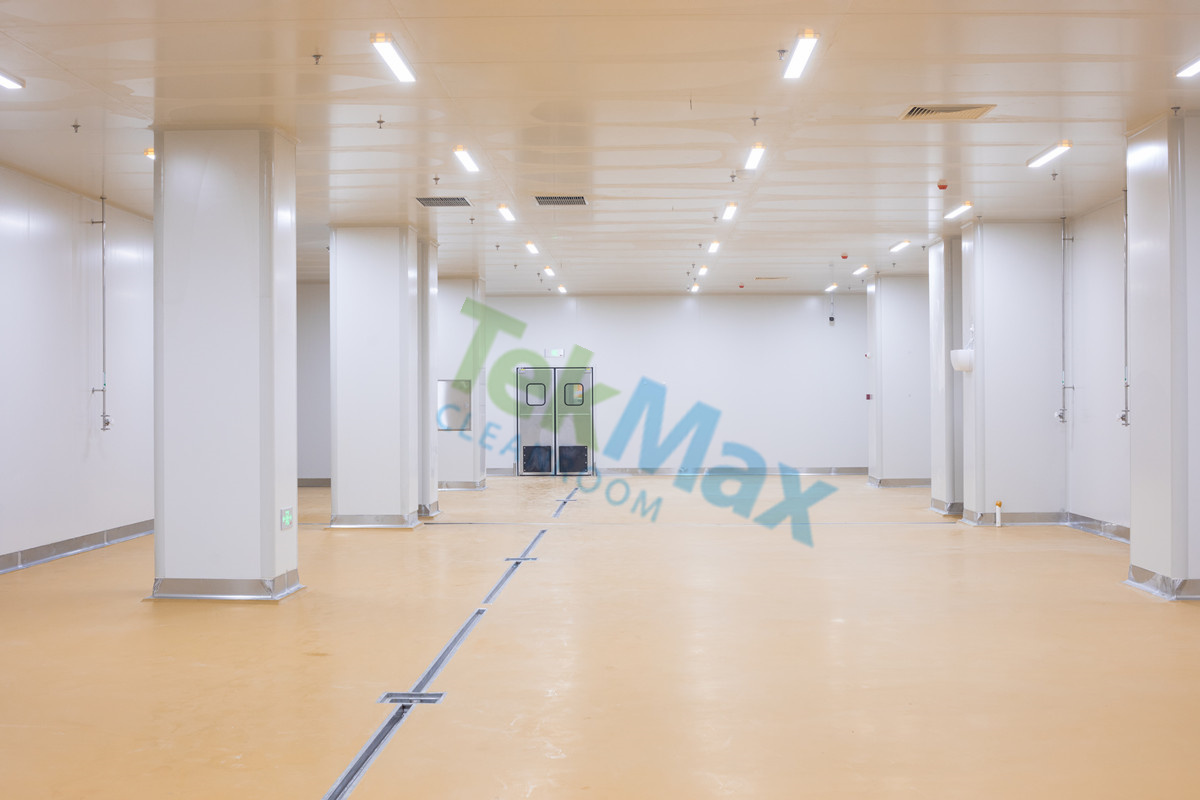
Clean Room Door Manufacturer Cleanroom Technology keeps decision-makers worldwide updated on contamination control via digital, live, and print platforms. Our articles span the cleanroom lifecycle, from design to maintenance, including monitoring and compliance. Editors deliver breaking news, product launches, and innovations, and also commission exclusives on technical trends from industry experts