Temperatures are expected to drop into the teens this weekend in the Harrisburg area.
And frozen water pipes in your home could become a concern. Nichrome Wire Used In Electric Heaters
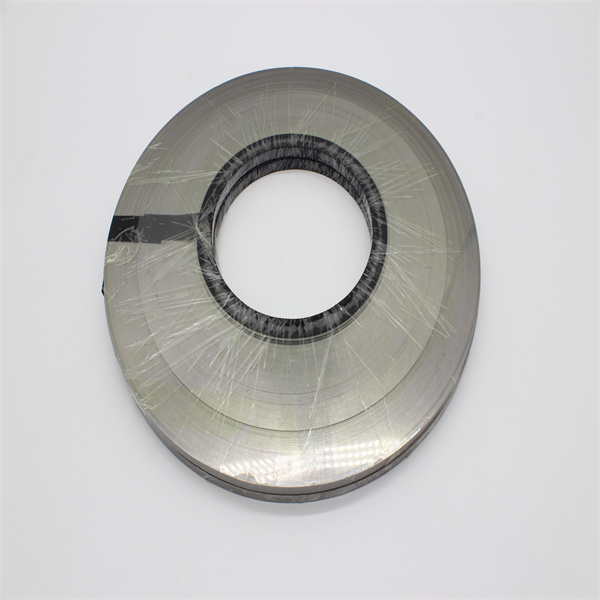
Pennsylvania American Water has offered tips in the past about how to prevent your pipes from freezing and what to do if they freeze. When the temperature is at or below freezing the company advises :
What do you do if your pipes freeze?
If you purchase a product or register for an account through one of the links on our site, we may receive compensation.
Use of and/or registration on any portion of this site constitutes acceptance of our User Agreement, Privacy Policy and Cookie Statement, and Your Privacy Choices and Rights (each updated 1/26/2023).
Cookie Settings/Do Not Sell My Personal Information
© 2023 Advance Local Media LLC. All rights reserved (About Us). The material on this site may not be reproduced, distributed, transmitted, cached or otherwise used, except with the prior written permission of Advance Local.
Community Rules apply to all content you upload or otherwise submit to this site.
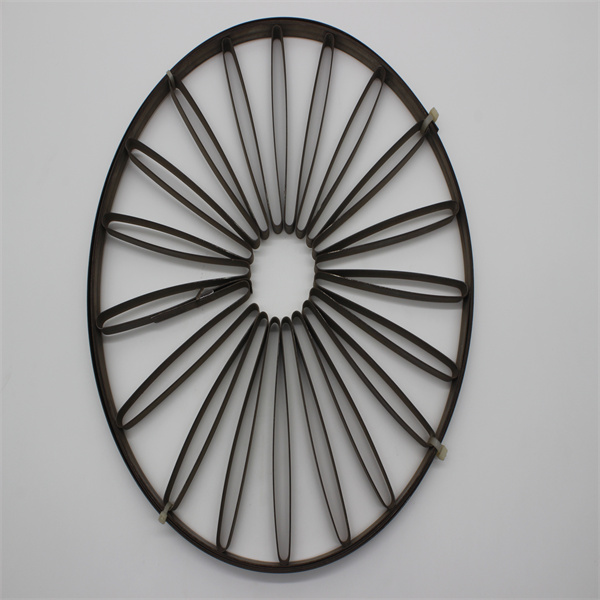
Spark Resistance Wire Manufacturer YouTube’s privacy policy is available here and YouTube’s terms of service is available here.