An official website of the United States government Here's how you know
Official websites use .gov A .gov website belongs to an official government organization in the United States. Battery Cable Connectors

Secure .gov websites use HTTPS A lock ( LockA locked padlock ) or https:// means you’ve safely connected to the .gov website. Share sensitive information only on official, secure websites.
Epoxy-coated reinforcing steel bars demonstrate long-term performance in heavily salt-contaminated concrete.
For many years, researchers and inspectors have recognized that deterioration of bridge decks caused by corrosion of reinforcing bars can be a major problem. Chloride ions from deicing salts are the main culprit responsible for the premature deterioration of reinforced concrete bridge decks because they can induce corrosion of the reinforcing steel. Voluminous corrosion products exert hoop stress on the surrounding concrete, resulting in cracking and spalling.
According to a Federal Highway Administration (FHWA) Technical Note on Corrosion Protection System, written by the FHWA Infrastructure Inspection and Management Team from the Office of Infrastructure Research and Development (R&D), the average bridge deck subjected to deicers and containing uncoated (black) reinforcing steel shows signs of corrosion approximately 7 to 10 years after construction. In the mid-1970s, corrosion engineers and the coating industry introduced epoxy-coated reinforcing bar (ECR) as a means of extending the service life of highway structures by minimizing corrosion of the reinforcing steel. Currently, 48 State highway agencies use ECR as the most common corrosion protection system for bridge decks.
"We have had nearly 30 years of excellent service life from ECR on concrete bridge decks," says Gerry Anderson, chief structural engineer on the Marquette Interchange Project, at the Wisconsin Department of Transportation (WisDOT). "We are currently constructing the Marquette Interchange megaproject in Milwaukee using an ECR product that offers a 75-year design life and is among the most cost effective on the market."
According to 2003 data in FHWA's National Bridge Inventory, more than 54,000 bridges deck contain ECR, either in the top mat only, or in both the top and bottom mats. A mat is a plane of rebar (reinforcing bar) that is parallel to the top surface. Currently, more than 30 fusion-bonded epoxy coating applicators exist in the United States and Canada, and the cost of constructing decks with ECR averages about 1 percent more than the cost of using black steel.
Indiana has used ECR since the late 1970s, according to Dr. Julio A. Ramirez, professor of structural engineering in the School of Civil Engineering at Purdue University. "Every single bridge built in Indiana in the last 10 to 15 years has been reinforced with ECRs in the deck," he says. "Based on a study we completed in 1999, ECR outperformed all other corrosion protection systems used in Indiana to that date."
In 1986, the Florida Department of Transportation (FDOT) observed premature corrosion of ECR embedded in the substructures of several Florida Keys bridges located in the subtropical marine environment. These substructure bridge components are continuously subjected to salt spray in the splash zone, combined with wetting and drying cycles, high temperatures, and chlorides and moisture, which produce a very corrosive environment. As such, FDOT does not use ECR in substructure bridge components exposed to marine environments.
Because snow is not an issue in Florida, FDOT does not use deicers on its roads and bridges, and therefore, the department has no need to use ECR in its bridge decks to combat corrosion. On the contrary, the midwestern and northern parts of the United States, including Indiana, receive abundant snowfall and use high quantities of deicers. For these States, ECR is often a preferred system for cost effective corrosion protection.
In May 1993, FHWA sponsored a 5-year (1993–1998) research project titled Corrosion Resistant Reinforcing for Concrete Components. The objective was to develop cost effective new breeds of organic, inorganic, ceramic, and metallic coatings for reinforcing bars, as well as metallic alloys that could be used as reinforcement in portland cement concrete. The goal was to achieve a corrosion-free design life of 75 to 100 years when exposed to adverse and corrosive environments.
The research program involved testing epoxy- and other polymer-coated reinforcing bars, as well as ceramic-coated, galvanized-clad, epoxy-coated galvanized-clad, stainless steel-clad, nickel-clad, copper-clad, corrosion-resistant alloy-clad, inorganic silicate-clad, solid corrosion-resistance alloy steel, solid aluminum-bronze, solid stainless-steel, and solid titanium reinforcing bars. Researchers made and tested 141 reinforced concrete slab specimens using these 12 bar types. The results were published in a series of reports between 1995 and 1996 (FHWA-RD-94-103, FHWA-RD-96-021, and FHWA-RD-96-085).
The concrete slabs measured 30.5 by 30.5 by 17.8 centimeters (12 by 12 by 7 inches) and contained two mats of 29.2-centimeter (11.5-inch)-long, 1.6-centimeter (0.625-inch)-diameter reinforcement. The top mat contained either two straight or two 180-degree bent reinforcing bars and acted as a macroanode where corrosion will initiate after chloride ions penetrate the top concrete cover. The bottom mat was a macrocathode that contained four straight reinforcing bars where the cathodic reaction (oxygen consumption) took place. Each top mat bar was connected to two of the bottom mat bars through a 10-ohm resistor. A clear cover of 2.5 centimeters (1.0 inch) was used in all specimens.
Some of the test slabs contained "precracks" that were introduced by inserting a stainless steel shim directly over a top mat rebar to simulate cracks observed on actual bridge decks. The ECR specimens were produced with six different coating powders and all were intentionally damaged by drilling holes through the coating to introduce artificial coating defects, either 0.004 percent (representing a small defect size) or 0.5 percent (representing a large defect size). Every bent ECR was fabricated after coating was applied.
After the concrete slabs cured for 28 days, they were exposed to the 96-week Southern Exposure (SE) test, which involves four 24-week cycles, with each cycle consisting of 12 weeks of 4-day ponding under a 15-percent sodium chloride (NaCl) solution and 3-day drying at 16 to 27 degrees Celsius (60 to 80 degrees Fahrenheit), followed by another 12 weeks of continuous ponding under the 15-percent NaCl solution. At the conclusion of the SE testing in 1998, the researchers autopsied all but 31 of the test slabs and published the results in an FHWA report titled Corrosion Evaluation of Epoxy-Coated, Metallic-Clad, and Solid-Metallic Reinforcing Bars in Concrete (FHWA-RD-98-153).
The remaining 31 post-SE test slabs were classified into four configuration groups:
The researchers then exposed the 31 post-SE test slabs to long-term natural weathering at an outdoor test yard in Northbrook, IL, from September 1998 to December 2002 and collected test data periodically during that period. The macrocell current density (i, which refers to the current flow between the top and bottom steel mats) is a good indicator of corrosion performance. Researchers measured the macrocell current density by the voltage drop (V) across a 10-ohm resistor (R) connected between the top and bottom mats and a predetermined surface area (SA) of the bars (SA = 145.7 cm2 or 22.6 in2) according to Ohm's law (i = V/(R x SA)). Other data collected include the corrosion potential of top mat bars, the alternating current (AC) resistance between the top and bottom mats, and the impedance modulus (Z) at 0.1 hertz (Hz) of the top mat bars using electrochemical impedance spectroscopy (EIS).
When the test program ended in 2002, the researchers documented the exterior condition of the test slabs and autopsied the samples. They also performed laboratory analyses, including visual examinations of the extracted bars and chloride content and condition evaluations at the bar-concrete interface.
A comparison of the mean macrocell current density versus time over several years for the slabs containing black bars, ECRs with 0.5-percent initial coating damage, and ECRs with 0.004-percent initial coating damage showed that the ECR slabs performed better, especially the ones with the smaller initial defect size, than the black bar control slabs.
The straight black bars had a mean macrocell current density of about 2.4 microamperes per square centimeter, A/cm2 (15.5 A/in2), during the 96-week SE testing. Upon outdoor exposure, the mean macrocell current density of the black bars was somewhat less than 1.5 A/cm2 (9.7 A/in2) and became negative in every specimen after 1,900 days. These negative current readings indicated reversed macrocell current flow that was caused by corrosion of the cathode steel in the bottom mat instead of the usual corrosion initiation in the top mat bars.
The researchers suspected that this happened when sufficient chloride ions reached the black bars in the bottom mat and subsequently initiated active corrosion. Upon autopsy, they confirmed the assumption when they discovered that the chloride contamination at some bottom bar depths far exceeded the chloride threshold for initiation of corrosion in black bars (which is typically 250 to 300 parts per million). The top mat ECRs embedded in slabs with black bar bottom mats were able to suppress deterioration due to their much higher resistance to corrosion. Other studies revealed similar results in real decks where ECR was used in the top mat only.
The macrocell current density data varied significantly depending on bar type and slab configuration. To illustrate the relative significance of slab configuration and bar type on the mean macrocell current density, the researchers presented the ratios of macrocell current density data by dividing them by the highest mean value of the black bar slabs, which was 1.3 A/cm2 (8.4 A/in2).
The stainless steel bars exhibited negligible mean macrocell current density that was only 1 percent of the highest black bar case. For straight ECRs, the mean macrocell current density was influenced by the size of the initial coating damage and whether the bottom mat bars were coated or uncoated. When straight ECRs in the top mat were coupled with black bars in the bottom mat, the size of the coating defect became a factor for controlling macrocell current density. In the case of straight top ECRs containing 0.004-percent initial coating defects coupled with black bottom bars, the mean macrocell current density was 7 to 21 percent of the highest black bar case, depending on the presence of precracks. If straight top ECRs contained the 0.5-percent initial coating defect, the current values increased to more than 40 percent of the highest black bar case, regardless of whether the slab had a precrack.
For the bent ECRs, even ones containing 0.004-percent coating damage produced noticeable corrosion activity when they were connected to black bottom bars, such that the mean macrocell current density increased to 38 and 49 percent of the highest black bar case, regardless of initial size of the coating defect. The researchers concluded that additional coating defects such as cracks and mechanical defects could have been introduced during the bending process.
When top mat ECRs were connected to ECRs in the bottom mats in uncracked concrete, the effect of coating damage on macrocell current density was minor, and the ratio decreased to no greater than 2 percent of the highest black bar data. They behaved similarly to stainless steel bars. The researchers attributed the excellent performance of the test slabs containing ECRs in both mats to the fact that electrical resistance was high between the two mats, and the ECRs in the bottom mat suppressed the corrosion activity by minimizing the area for the cathodic reaction (oxygen reduction).
The researchers then determined that the distribution of mean values (µ) for the macrocell current density data categorized by 12 combinations of test variables. As noted earlier, use of stainless steel bars and ECRs containing 0.004-percent initial coating damage produced the least current density. When ECRs with the 0.5-percent initial coating defect were used in both mats, the macrocell current density slightly increased from zero. This performance was followed by straight ECRs containing 0.004-percent coating defects in the top mat only and other samples with ECR in the top mat only. The black bar cases yielded the highest mean values by a large margin.
The test results agreed with those reported in an October 2003 field study, Service Life Extension of Northern Bridge Decks Containing Epoxy-Coated Reinforcing Bars, prepared for the Concrete Reinforcing Steel Institute. Using ECR, especially in both mats, in northern bridge decks is likely to give high levels of corrosion resistance in environments that rely on deicing salt applications for winter maintenance.
The test slabs then were split into several sections and the embedded bars were carefully extracted using a small chisel and hammer to avoid damaging the coatings. The straight ECRs from the top mat that performed well throughout the severe testing regime showed no signs of corrosion, and the concrete-bar interface appeared to be in excellent condition. On the other hand, those that did not perform well showed a range from minor to severe corrosion.
Examination of the extracted ECRs revealed four different coating conditions. When the ECR performed well, the exposed coating looked new and had a glossy texture. When the epoxy coating reached an advanced stage of deterioration due to corrosion, it exhibited numerous hairline cracks and blisters. On severely corroded ECRs, researchers observed the accumulation of multiple rust layers beneath the disbonded coating.
One autopsied top mat ECR exhibited localized coating disbondment that originated from corrosion at the smaller artificial coating defects (0.004 percent), while another top ECR bar experienced severe corrosion that initiated at the larger artificial coating defects (0.5 percent). With the latter corrosion, the epoxy coating could be peeled off completely.
Earlier FHWA studies, The Performance of Bendable and Nonbendable Organic Coatings for Reinforcing Bars in Solution and Cathodic Debonding Tests (FHWA-RD-94-103) and Degradation of Powder Epoxy-Coated Panels Immersed in a Saturated Calcium Hydroxide Solution Containing Sodium Chloride (FHWA-RD-94-174), showed that the adhesion properties of the coated bars, as tested by solution immersion and cathodic disbondment tests, could not predict the rate of corrosion or the long-term performance of ECRs in chloride-contaminated concrete. Confirming the conclusions in earlier studies, the researchers in this study could not find a consistent relationship between the level of macrocell current density and the extent of coating adhesion loss.
These results indicate that adhesion appears to be a poor indicator of the long-term performance of coated bars in chloride-contaminated concrete, as no direct relationship exists between the reduction or loss of adhesion and the effectiveness of ECR to mitigate corrosion.
Exposure to harsh deicers (with corrosive chloride ions) and natural weather for more than 7 years affected corrosion-resistant reinforcing bars differently depending on the bar and coating materials. The black bars produced the highest mean macrocell current density—indicating the least resistance to corrosion—among the various test slabs. The black bar corrosion resulted in rapid cracking and delamination of the concrete cover and eventual corrosion of the bottom mat of black steel.
In contrast, the stainless steel bars exhibited negligible mean macrocell current density and performed well throughout the severe inconcrete testing.
Bent ECRs in the top mat, coupled with black bars in the bottom mat, performed the worst among all ECR cases, possibly due to additional coating defects that occurred during the bending process, but they were still able to reduce corrosion susceptibility by at least 50 percent of the worst black bar case.
Straight ECRs in the top mat showed a macrocell current density varying from 7 to 40 percent of the highest black bar case, depending on the size of initial coating damage and the type of bar in the bottom mat. In cases where straight ECRs in the top mat were connected to ECRs in the bottom mat, the mean macrocell current density was no greater than 2 percent of the worst black bar case, even when the coatings had intentional defects. When ECRs were used in both mats, their performance approached the corrosion resistance levels of stainless steel reinforcement.
This laboratory and outdoor exposure study confirms earlier research findings that the use of ECR in the top mat, coupled with uncoated steel bars in the bottom mat, can reduce corrosion damage but does not provide as effective long-term corrosion protection for bridge decks compared to situations where ECRs are used in both the top and bottom steel mats. The increase in corrosion resistance when ECRs are used in the bottom mats was dramatic. Today, the corrosion resistance of bent ECRs should be much better than that of the ECRs tested in this study because of improved coating technology and quality control practices, as well as greater use of prefabricated ECRs.
"To increase the effectiveness of epoxy-coated reinforcement as a corrosion protection method," says Ramirez from Purdue University, "sufficient cover of high-quality concrete and increased thickness of epoxy coating can be used to limit defects."
Anderson at WisDOT agrees. "Using [American Society for Testing and Materials] ASTM-specified ECR applied by a certified coater in both top and bottom mats as the primary corrosion protection system," he says, "coupled with high-performance concretes and a minimum 2.5-inch [6-centimeter] cover, is the most economical and cost effective method to build durable bridge decks until alternative reinforcements, such as solid stainless steel bars and stainless steel-clad bars possessing excellent corrosion resistance properties, become readily available at affordable costs."
Seung-Kyoung Lee is a research corrosion engineer in the FHWA Office of Infrastructure Research and Development at the Turner-Fairbank Highway Research Center in McLean, VA. Previously, he served as a senior corrosion engineer at Wiss, Janney, Elstner Associates, Inc. He may be contacted at 202–493–3077 or sklee@fhwa.dot.gov.
Paul D. Krauss is a senior consultant at Wiss, Janney, Elstner Associates, Inc. He may be contacted at 847–753–6517 or pkrauss@wje.com.
Y. Paul Virmani is a research chemist in the FHWA Office of Infrastructure Research and Development at TFHRC. He may be contacted at 202–493–3052 or paul.virmani@fhwa.dot.gov.
For complete test results and indepth data analyses, see the FHWA report, Long-Term Performance of Epoxy-Coated Reinforcing Steel in Heavy Salt-Contaminated Concrete (FHWA-HRT-04-090).
6300 Georgetown Pike McLean , VA 22101 United States
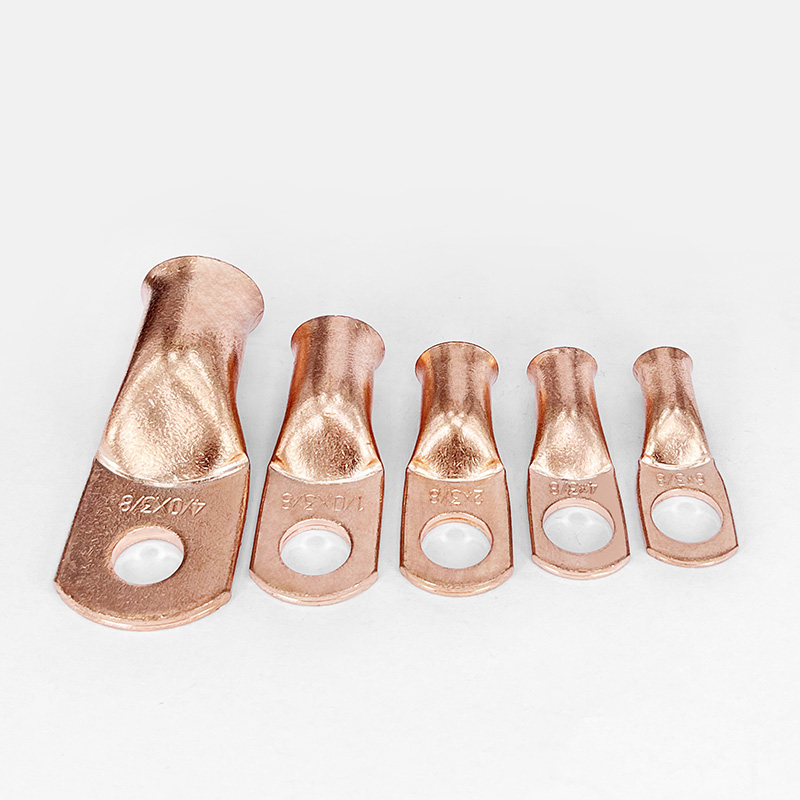
Ring Terminal U.S. DEPARTMENT OF TRANSPORTATION