Two self-sealing clamps have been delivered to BP by Furmanite UK for deployment in the North Sea. BP wanted to have the clamps available on short notice to repair pipelines in this area that might suffer damage following incidents such as anchor and trawler strikes.
A requirement was that successful installation of the clamp could be proven in advance, prior to re-pressurization of the pipeline. The ability to test the clamp without the application is of benefit where the pipeline in question has been gouged or dented. It is also crucial if a pipeline pressure test is to be avoided in the case of a through-wall defect. Furmanite fulfilled this requirement by providing two complete seal tests, one external and the other with the facility to pressurize the void between the two. Flanged Butterfly Valve
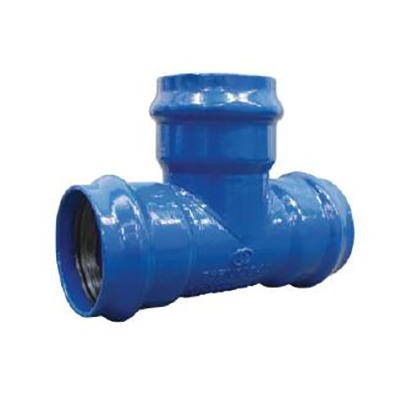
The high design and test pressures placed extreme demands on the structural performance of each clamp. Additionally, the materials for the clamps would need to meet demanding chemical and mechanical test specifications to ensure compliance with BP's sour service requirements. Furmanite was awarded this contract towards the end of last year.
The clamps require no compound injection and achieve a seal at high pressures using compressed Viton rubber seals. Another feature of the design is a built-in allowance for variations in the pipelines' outside diameters. The clamp has been designed to fit 14-in. nominal bore pipes while the other fits 8-in. nominal bore pipes, but with a system of interchangeable inserts and seals to accommodate variations up to 7 mm.
At the higher design pressures specified, the clamp shell thickness and bolting requirements inevitably make weight a critical issue during deployment. Use of finite element analysis software and cast steel bodies allowed the developer to optimize the use of materials to reduce weight. An added benefit was the simplified manufacturing process, which minimized machining time and eliminated structural welds.
Solid modeling software and finite element analysis (FEA) was applied for each design, enabling test pressures to be achieved of 5,920 psi for the 8-in. clamp and 5,560 psi for the 14-in. clamp. The required design pressures were respectively 3,950 psi and 3,700 psi.
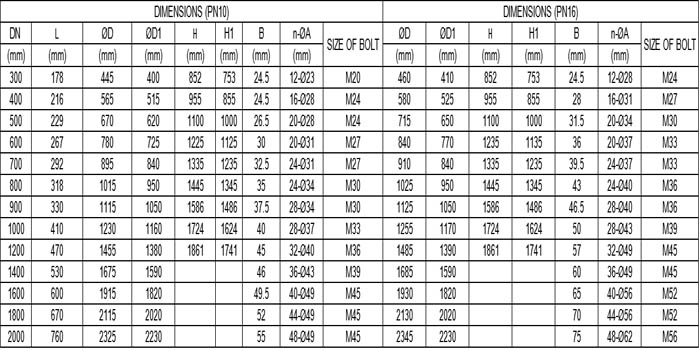
Pvc Pipe Joint FEA was used for an extensive virtual testing program to ensure that both clamps would resist the parting forces generated by the test pressures (about 2,350 tons for the 14-in. clamp), with minimal opening at the half joint. Factory acceptance testing was then conducted on the maximum and minimum pipe diameters to confirm the clamps' performance. The FEA software was used further to validate the design in accordance with API standard 6H, as had been stipulated. This validation was then subject to third party verification.