Space is usually at a premium for machine shops. Now, in addition to overall floor space limitations, CNC machines and other equipment are becoming increasingly sophisticated and smaller, which can create new challenges.
Masters Machine Co., for example, employs several small Swiss-style CNC lathes that can be difficult to work around. “The Swiss lathes have a much smaller machining envelope and less room for tooling,” explained CNC machine programmer and process improvement machinist Zachary O’Connor. Resin Diamond Frankfurt Abrasive
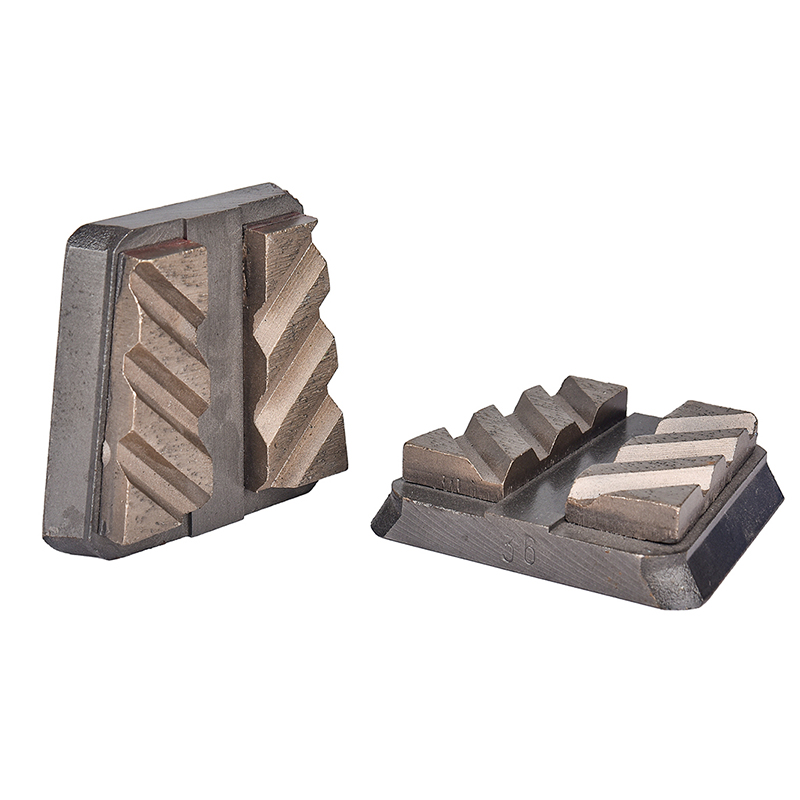
A solution was imminent. The Round Pond, Maine-based shop, which produces precision components for the aerospace, automotive, commercial, and electronics industries, prides itself on upgrading and applying new methodologies to continually improve its processes. Founded in 1957, the company employs about 85 people at its 86,000-sq-ft [7,990 sq m] facility located in a small fishing village in mid-coast Maine.
O’Connor, who joined Masters Machine in May 2021, was eager to contribute to his new team. He brought experience from a previous job with another Maine machine shop where he began working with Brush Research Manufacturing Co. (BRM), which specializes in abrasive disc brushes for finishing, deburring, surface prep, homogenizing part surfaces, radiusing, and edge breaking.
BRM’s new line of smaller ceramic end brushes builds on the qualities of abrasive disc brushes that allow CNC operators to automate the deburring process while delivering an ideal surface finish in the same operation, according to the company. The tools provide machine shops with more precise finishing and deburring options, as well as design improvements to facilitate reaching deeper into workpiece holes, bores, and constrained spaces.
As is the case for many machine shops, one of the goals of O’Connor’s former employer was to achieve the required surface finish and/or deburring while increasing cycle time. Taking this into account, O’Connor sought to improve the speed and quality of the surface finish on a cold-rolled, 4-ft (1.21-m) steel part prior to nickel plating for a semiconductor-related assembly.
“A36 structural steel does not finish well, so you can end up with a matte, torn finish even when all cutting parameters are met,” O’Connor said. “The process left a lot of deburring and finishing work to be performed by the operators of the production cell after machining was complete.”
For another steel part, the machine shop was attempting to debur a slot using a two-flute drill run at a very slow feed rate. Unfortunately, this approach often rolled the burr over, instead of removing it completely. As a result, O’Connor noted, CNC operators were putting in too much time and not getting the desired result.
To resolve the issue, O’Connor turned to BRM’s NamPower abrasive brush line. Composed of flexible abrasive nylon filaments bonded to a fiber-reinforced-thermoplastic base, these disc brushes contain a combination of ceramic and silicon carbide abrasive. The filaments work like flexible files, conforming to part contours, wiping and filing across part edges and surfaces to deliver maximum burr removal rates along with an ideal surface finish, according to the manufacturer.
While some other abrasive nylon filament products use silicon carbide or ceramic, the combination of both in one tool makes NamPower unique, BRM pointed out. The two abrasives complement each other: ceramic is responsible for material removal but tends to cut a bit coarse; and silicon carbide acts as a buffer to the cutting action. The combined result enables deburring and finishing in a single operation.
Each brush essentially “self sharpens” over its life as well. Because of its linear construction, sharp new grains constantly come in contact with the work surface and wear off, exposing fresh cutting particles. This provides consistent deburring action throughout the length of bristles.
“We found that the NamPower brushes provided a quality finish as well as superior edge preparation versus chamfering,” O’Connor said. “Chamfering is great when it works, but if there is tool wear it can roll the burr over instead of removing it. We wanted to avoid that.”
The finishing tool can be used on a variety of materials, such as aluminum, carbon steel, stainless steel, brass, bronze, titanium, cast iron, and high nickel alloys.
At Masters Machine, O’Connor heard about the expansion of BRM’s product line to include smaller, re-designed ceramic abrasive end brushes designed to work with smaller parts and in more constrained spaces. Naturally, he wanted to try them out on the Swiss CNC lathes.
“I was dealing with a tricky deburring application in a high-production scenario,” he noted.
Like the NamPower brushes, the new Abrasive End Brushes are designed to enable efficient, precision deburring and finishing in a range of applications and materials. However, the end brush incorporates several design changes that allow them to be used on smaller, more complex parts or in smaller CNC machines.
“The aluminum, hard-coat anodized cups that hold the ceramic filaments are now a thin-walled design that allows the filaments to be aligned close to the outer edge to reach inside edges of a part, or hole,” said BRM Product Manager Elysha Cole. “The end brushes also have a longer shank so the tool can reach deeper into tight spaces or pockets in the workpiece.”
The ‘fill’ on the brushes is also very dense to provide more cutting points, a factor that allows the tool to cut more efficiently, while lasting longer. According to Cole, the ceramic filaments last 3-5 times longer than the other alternatives, based on initial testing. The tool is designed to be loaded directly into automated machining centers with no special adaptors.
In June 2021, O’Connor purchased an 80 Grit, 1” (25.4 mm) Abrasive End Brush that he could mount in a gang of tooling to be used for deburring and precision finishing operations on a variety of parts. “If you are working on a small, half-inch (12.7 mm) part, you may not want to utilize a brush that is 2 or more inches (50 mm) in diameter,” said Cole. “There are also times a more precise finish is required, or the tool needs to reach into tight spaces, which the smaller sizes provide.
Since their installation in September 2021, the end brushes have saved Masters Machine considerable production time. O’Connor estimated the shop previously could machine 300 parts in 24 hours for parts that required deburring/finishing. Cycle times have been cut nearly in half with the new BRM abrasive tool and adjustments to the programming.
“I was able to increase the spindle rpm and feed rate to run faster surface footage, while producing the quality finish required,” O’Connor said. “The ability to reduce cycle times using the end brushes is also critical, particularly in a high-volume production shop like Masters Machine,” he added. “Because we complete thousands of orders, if we can reduce cycle time by 20 or 30 seconds per part, that provides incredible cost savings.”
The high-density ceramic design prolongs tool life as well.
“The end brushes are performing very well, and we are getting really long life out of them,” O’Connor said. “In the past, we had to change out our spot drills after 300 to 400 parts. Now we are running entire jobs with 2,500 parts with one end brush.”
In addition, automating wear compensation is possible on dedicated equipment. This is accomplished using electronic controls to monitor drive motor load and adjust brushing tool position to maintain a relatively consistent amount of pressure.
O’Connor created a macro “wear equation” to automatically compensate for wear, then triggers an alarm when the end brush reaches the end of its useful life. As a result, he said, the shop can “achieve very long production runs without any operator input.”
Masters Machine also has begun using the new ceramic end brushes for other applications. In addition to turned parts, the high-volume shop provides milling operations and can handle a wide variety of shapes and sizes.
“As far as finishing and deburring goes, the sky is the limit,” O’Connor said. “The end brushes are very adaptable to each application. A machine shop is essentially only limited by its own creativity.”
For more information about Masters Machine Co., visit https://www.mastersmachine.com or call 207-529-5191.

Polishing Plate For information about Brush Research Manufacturing visit brushresearch.com or call 323-261-2193.