Through technological advancements, most people have become connected and dependent on real-time data at their fingertips. With just a few taps and swipes on their smartphones and other devices, people can easily text, search, post, and, more importantly, manage their personal and professional lives. The digital solutions transforming nearly every aspect of our world—but reluctantly adopted by the cautious oil and gas industry—can improve well completions by unifying the goals of equipment manufacturers, service companies, and operators.
With well intervention and stimulation, the fragmented industry still relies on legacy standard operating procedures, on-site tribal knowledge, and the ability to deduce downhole conditions with minimal sensor data to monitor operations, Fig. 1. Service companies must follow plans set by operators, who differ in procedures and reservoir targets, yet often only have one representative at the well site. This segmented approach restricts the perspective that service companies bring to well completions. It makes data interpretation subjective, raises costs, increases nonproductive time (NPT), and imposes safety and environmental risks. Coiled Tubing Unit

A digital solution providing a single point of view creates a shared understanding of completions projects and ensures that operators, suppliers, and service companies pursue common goals. This collaborative approach not only lowers delivery costs and increases production but also reduces the number of people on a well site and minimizes emissions.
Evolution of completions data. Data utilization in completions differs from drilling, which is fully integrated across all functions at the wellsite. With completions, service companies and operators use and contextualize data differently. Service companies measure efficiencies on past jobs to implement new procedures to improve performance, while operators want all information concerning all their wells and categorized to drill farther, faster and safer.
Historically, data collection for fracturing, coiled tubing, workovers, and wireline operations has been done only to monitor the current job on location, separate from any other project, service line, or viewpoint. Data are not shared, and interpretation is subjective. All four functions were looked at from a siloed perspective, which meant operators never had a full picture of what was occurring on their wells.
To back up the service tickets delivered to the operator, frac service companies developed internal data collection systems focused on the specific treated stage, rather than the overall well. However, all stages are meaningful and can impact subsequent actions or the next well on the pad. Now, rather than focusing on single-stage data collection to show value to an operator, frac service companies can deliver treatment, with overall pad production efficiencies as the target.
Coiled tubing data collection was not designed to provide job context to the company representative, office, or even the coiled tubing unit operators. Its primary purpose is to monitor the required variables for coiled tubing string failure calculations to determine when the string needs to be replaced, Fig. 2. As the course evolves, more data collection and algorithms will provide information to make actionable insights.
Workover data collection is reserved for high-profile operations and uses repurposed rig sensors, resulting in minimal effectiveness. Until recently, the industry has been in the proverbial dark regarding workover and snubbing operations. Now, these operations are used for completions drill-outs. Wireline operations typically collect data only from the tools used to produce well logs but not from the actual operation or time spent on location.
In addition, field data transmission was, and remains, poor. Even when effectively transmitted, the data do not provide the context of previous or planned operations after the specific service provider leaves the location, as most service companies use homegrown or non-connected applications, resulting in disparate data focusing on their services alone.
To achieve the same connectivity and related benefits that users expect and experience outside the workplace, completions data must be integrated into one central hub that allows standard views to be shared with all parties, including those in the field, at the service company, and in the operator’s office. These data should provide real-time alarm states while connecting the engineering tools—from not only sensor data but also manual channels that the expert can enter on the ground, witnessing and measuring difficult-to-sensor critical metrics, such as return rate.
Also, by enabling the most informed experts to access critical operational data and guide multiple projects remotely, the industry can decrease headcount on location, improve safety and reduce emissions by lowering travel.
Integrated operations data platform. NOV developed the Max Completions data platform to provide a holistic view of the entire operation and modern workflow connectivity, Fig. 3. Aggregating and aligning data from across the completions site provides quality operational insights with context to improve efficiency and financial performance. From sensor to squiggle, the cloud-based solution removes all subjectivity from the completions operation and equipment performance—frac, coiled tubing, workover, wireline, jointed pipe, and thru-tubing tools—and provides real-time access to the same data in the field and office, enabling fast adjustments before potential failures—all while prioritizing well delivery.
In addition, the completions data platform features a mobile application for real-time viewing of live jobs, Fig. 4. As they do when posting to social media platforms, users can view all job-related data and add comments, photos and videos from their fingertips. This capability provides more contextualized and higher-quality insights. Empowering field users improves data quality, because humans are the most powerful sensors on location.
Coiled tubing use cases. Viewing operational data during horizontal well interventions is customary in North America. However, combining engineering analysis with real-time viewing is not. With Max Completions, the interactive tubing force analysis (TFA) models with real-time data overlays provide coiled tubing operators with the information they need to increase drill-out efficiencies (hour/plug), decrease mechanical failures, such as stuck pipe events, and reduce NPT. Instead of following predetermined processes, the operators make more tailored, data-driven decisions.
In the following historical examples, Max Completions would have made the coiled tubing drill-outs more efficient, avoiding cost overruns and stuck pipe.
Case 1: Identifying equipment issues. In the first example, the coiled tubing reached either a friction lockup or a hard tag, Fig. 5. The coiled tubing was pulled out of the hole, and the bottomhole assembly (BHA) was function-tested. However, after tripping in at a normal speed, the coiled tubing experienced the same issue at the same depth. After the coiled tubing returned to the surface, the operator changed the BHA. On the third run with the new BHA, the coiled tubing made it to the bottom and completed the job. If the operator had used the cloud-based application, it could have identified the BHA causing the deviation and eliminated multiple trips by changing the tools on the first trip.
Case 2: Reducing NPT. In another operation, the coiled tubing model data suggested that the plug-back target depth of approximately 19,000 ft could be achieved by reducing the coefficient of friction to 0.26. Once the coiled tubing reached the kick-off point and all rates and pressures were stable, the live data were compared to the modeled run-in-hole (RIH) line.
After milling the initial plugs, the coiled tubing weight deviated significantly from the modeled data. The extended-reach tool’s effectiveness was eliminated as a possible cause of the deviation because of the operation’s shallow depth. The model matched the actual data, eliminating the weight indicator or the model's accuracy. The only apparent cause of deviation was debris in the hole.
The coiled tubing operation continued in hole, with further deviation from the modeled RIH weight. An attempt to free the pipe resulted in a significant over-pull. After significant downtime, the well was cleaned up, and the job reached the plug-back target depth with no other notable deviations, as shown in Fig. 6.
Case 3: Fully connected operation. Figure 7 shows a fully connected operation and workspace for both the operator and the service company. It enables both companies to work toward the common goal of completing the operation efficiently and safely, while engaging all levels within both organizations.
The dashboard includes live sensor data engineering tools, real-time coiled tubing string fatigue, 3D wellbore with the coiled tubing and survey data, and equipment health metrics. The live sensor data with less than a 3-sec. delay from the field is viewable, just as one would see inside the coiled tubing unit, but the live sensor data now encompass custom warnings and alarms that can be set and shared for all viewers. The warnings provide early detection of high pressure, low annular velocity, overpulls, and equipment threshold limits, but they are configurable to the specific operation. While sensor data are paramount to the live operation, the engineering tools mentioned in the above examples are now viewed within the context of the complete job, to ensure the job operates with the standard operating procedures and within the modeled operation.
Most operations focus on using live sensor data and engineering torque and drag plots to allow subject matter experts to deduce downhole operation conditions. However, when using a fully connected platform, the user can visualize the coiled tubing pipe in the wellbore with fluid metrics and survey data that can highlight potential problem areas associated with the dogleg severity.
To expand on the operation, users are also able to visualize the operation and track the health of the coiled tubing string and equipment on location. Figure 7 highlights a well-maintained coiled tubing string with appropriate utilization for the application. In the last graph, the user’s maintenance department can see the real-time equipment health of the coiled tubing injector performing the work on location. In previous attempts, our industry has pushed real-time equipment information, but the job context was excluded, leaving the maintenance teams searching for causes after reported issues. With equipment health, engineering tools, wellbore visualizations, and sensor data in one interface, all subjectivity is removed from the operation, and both teams can focus completely on the primary goal of completing the well.
Digital solutions and recruitment. The industry will succeed to the extent that it not only integrates aging equipment with modern digital tools but also matches professional connectivity with what workers experience in their personal lives. Today’s up-and-coming oilfield workers grew up in a fully connected, digital world. They expect their work tools to be as advanced and sophisticated as what they use for entertainment. With Max Completions, NOV has created a modern workspace where future engineers and oilfield personnel can see what is happening downhole. One way NOV has built a forward-thinking workspace is by using 3D representations of wells, formations, fluids and tools. This technological sophistication eliminates the need for deduction and enables a clear, real-time understanding of what is occurring downhole.
In addition, by creating a modern workspace, the industry can recruit talent beyond its traditional demographics and skills, including digitally inquisitive and technology-focused individuals who currently only see Silicon Valley companies such as Meta, Google, Amazon and Tesla as their desired career paths. Plus, with a modern platform, the industry can stop training new entrants on decades-old software the world and academic community have long abandoned.
Efficiencies increase and operational risks and failures decrease when operators, service companies and manufacturers collaborate in an innovative integrated digital solution with real-time access to unified data. Also, bringing modern connectivity and digital expectations to well completions improves the oil and gas industry’s appeal to the next generation.
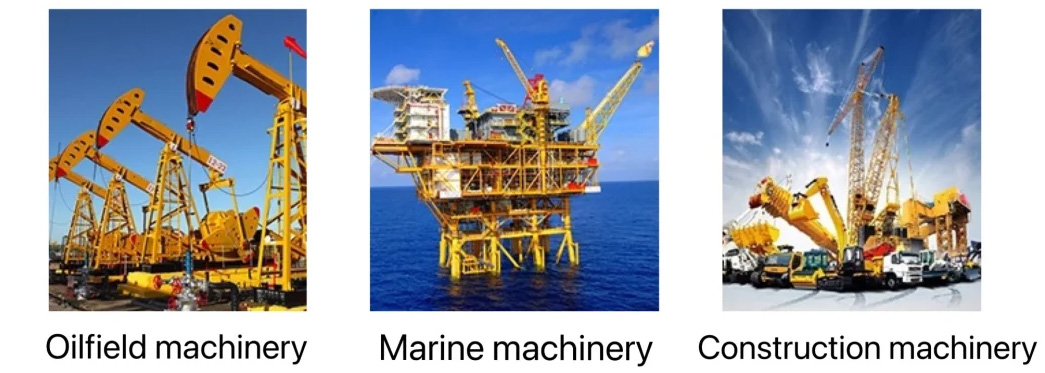
Coil Tubing Oil And Gas Thomas, T.G., N.A. Buck, K.R. Scherer, et al “Optimizing drillouts using live TFA,” SPE paper 208999 presented at the SPE/ICoTA Well Intervention Conference, Woodlands, Texas, March 22–23, 2022. https://doi.org/10.2118/208999-MS