We earn a commission for products purchased through some links in this article.
Remove stubborn stains and dirt from your carpet with these wonder-working machines paper cup machine
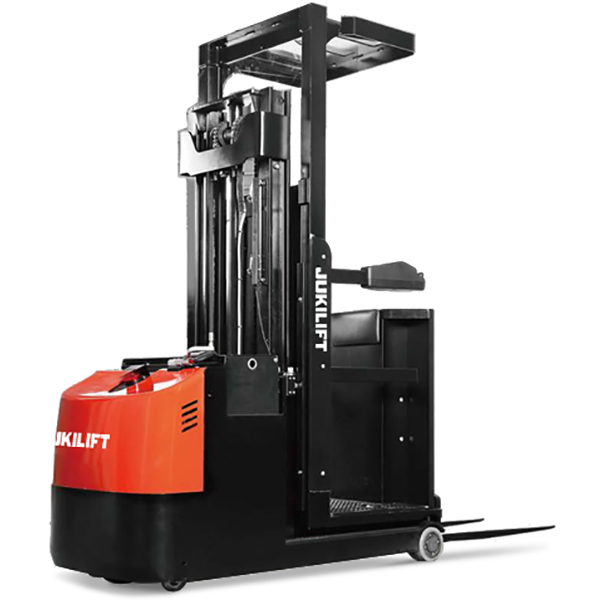
While a vacuum cleaner will get rid of everyday dust and dirt from your home, the best carpet cleaners promise to do so much more.
There are some stains and marks that a regular vacuum simply can't get out, and although steam cleaners can refresh your carpets, you'll need a dedicated carpet cleaner to eliminate tough stains and banish persistent smells.
At the Good Housekeeping Institute, we’ve tested 25 carpet cleaners to find our top performers. Here's an at-a-glance list, but discover why we loved them below.
When testing carpet cleaners at the GHI, we lay out a pre-measured amount of dirt on carpet, hard floor and upholstery. We tread the dirt into the floor and leave it to set overnight. We then use each machine a set number of times to see how well it cleans the dirty area. Then, we assess whether the floor is sodden, damp or completely dry after use.
We inspect the carpet and upholstery pile to see if it has been restored and lifted, then we look at the colour of the carpet and upholstery. We also assess ease of use, considering how simple the machine is to assemble and what extra tools are available.
Dropping just one point overall, this is a true all-singing, all-dancing carpet cleaning machine. It was effortless to use – just two passes were enough to remove tough stains – and only left our carpet a little damp after use, while the pile looked restored and lifted.
Its upholstery attachment was effective, all controls were intuitive to use and its handle was comfortable thanks to a soft silicone coating. It is on the bulky side, so you’ll need enough room to store it, but its carry handle will help with manoeuvring.
Another hit from Vax, there wasn't much we didn’t like about this carpet cleaner; it aced all of our tests. Using the Vax Platinum Carpet Wash, only a few passes over a stain were needed for it to be removed completely. And overall, the carpet looked and felt refreshed.
We found the pre-treatment wand useful too, as it allowed us to target deep stains, while the 4.6-metre hose meant cleaning the stairs was a breeze. A hard floor cleaning tool is also included, which fits easily onto the base of the machine and left our hard floor clean and dry. The upholstery attachment also made light work of cleaning sofas and car interiors.
This large carpet cleaner was hard to fault. From the three settings, we found Express Clean was best suited to everyday dirt as it removed stains after a number of sweeps, while Deep Clean and Max Clean banished them with a single sweep. We’d recommend only using Max Clean once or twice a year though to protect your carpets.
The upholstery and stair attachments were equally useful. The upholstery head cleaned sofas and seat cushions well, applying the cleaning solution evenly and easily reaching corners and crevices. It is loud when in use, and upholstery was left a little more damp than we’d have liked after cleaning. But these niggles aside, it’s a reliable buy — and ideal for cleaning up after pets.
This doesn’t have an upholstery attachment and it can’t spot clean for targeted stain removal, but if you want a more affordable carpet cleaner that will keep your flooring fresh, then this is a great buy. It effortlessly lifted dirt, stains and odours from our carpet, leaving them pristine and only slightly damp. You can use it on hard flooring, too.
It moved smoothly across our surfaces, and testers found it simple to use thanks to its comprehensive instructions. It’s not the quietest carpet cleaner we’ve ever tested, but that’s a minor niggle. This is a great value buy.
Here’s a machine you can use throughout your home. On test, our carpet was left almost sparkling, with just the slightest remnants of mud remaining, while most staining was stripped from our hardwood floor too. Its Deep Clean setting did leave carpet fairly wet, so only use this on heavy soiling. Instead, we suggest opting for the less powerful Quick Clean setting for lighter stains and refreshes.
And while this cleaner looks heavy, we found it easy to move about and carry up stairs. It comes with a great selection of attachments too, including a helpful crevice tool that reaches into tricky corners as well as a bottle of cleaning fluid. These can’t be stored on board but a drawstring bag is included.
Leaving our carpet pile well restored and with zero matting this is another Vax cleaner that impressed on test. Although we noted a little moisture left in the carpet immediately after use, once dry the colour was unaffected and there were no water marks to be seen.
The affordable cleaner was notably user-friendly, thanks to easily accessible controls and thorough instructions, and its crevice tool would make it a great choice for tackling car interiors. Cleaning up mud required some scrubbing, but the results were worth the elbow grease; this machine left our carpets pristine and stain-free.
As with vacuums, having to find a nearby plug socket for your carpet cleaner can be frustrating. But not with this one; its cordless design is powered by a rechargeable battery, making life easier. We found it intuitive to use, with sturdy controls and a comfortable handle. The machine glided across the carpet nicely, too.
There was a little sputtering from the cleaning solution dispenser and we noticed some dampness on both carpet and upholstery after cleaning. But after leaving them to dry, both were restored to a good-as-new state.
Of every form of dirt we tested it on, tea stains proved the most challenging for it to remove, but ultimately it successfully lifted them, proving itself a reliable cleaner.
This is the original model of Bissell’s ProHeat 2x Revolution Pet Pro above, and it made quick work of most cleaning tasks, whether you’re looking to clean the whole carpet or give the sofa a long-overdue refresh.
It earned top marks in the carpet test, with around 90% of stains removed after only a few sweeps. Our carpet was left damp rather than wet and the machine also lifted the carpet pile, making it look as good as new.
It struggled to lift wine stains from hard floors and upholstery, but like the other Bissell carpet cleaners we tested, it has well-labelled and responsive controls, feels stable and sturdy and comes with a great selection of tools for tackling stairs and upholstery.
Standing out for its excellent water pickup, this lightweight cleaner left all surfaces fairly dry after use. It was good at cleaning carpet, with limited dirt remaining, and did an outstanding job on upholstery too.
It’s an easy design to carry around the house and we found it straightforward to remove and fill up the water tanks. Although, given the substantial size difference between the larger clean tank and the smaller dirty water tank, you’d likely need to empty the latter mid-clean to use up the whole clean tank.
Doubling up as a dry vacuum, this is a great multi-purpose machine. Its robust design (with a substantial dirty water tank) proved reliable on hard flooring, with only small areas of trodden-in mud remaining after carpet cleaning. Carpets weren't left too damp either.
Set up is a bit more involved than others listed here, and there’s only one sachet of cleaning fluid included. The large dirty water tank is also difficult to empty when completely full, but the clean water tank can be removed so refilling from the tap is easy.
It’s pretty straightforward converting to a dry vacuum too – you pop in the provided bag, flick the function switch and it’s ready to go.
For an effortless deep clean, you can’t do much better than this Vax. The size and depth of its brush head allowed it to reach a large area in one swoop, and we were impressed with its cleaning power. Removing the tea stain took longer, but in the end, all traces of dirt were removed from both carpet and upholstery on test.
The carpet cleaner was easy to assemble and while the surfaces were left slightly damp after use, the cleaning fluid didn’t cause any discolouration. We found it smelt pleasant too; granted, that’s not an essential requirement, but it’s a definite bonus.
This compact portable spot cleaner did a brilliant job of cleaning carpet and upholstery, but isn't the best option for hard floors. The tanks have generous capacities though, so you’ll be able to clean a large area before running out of water and cleaning solution.
The motorised brush head successfully got right down into the carpet’s pile and we found it removed almost all stains after just a few passes. And after a few more passes, the carpet looked new. The brush handle made cleaning upholstery easy too, and produced excellent results.
If you’ve got a few awkward corners in your home, then this carpet cleaner may suit as we found its petite brush head suitable for reaching the most tricky spaces. Lifting tea stains and mud required some serious scrubbing with this machine, and we had to carry out several cleans to fully eradicate spilt red wine.
Scrubbing aside, it’s fairly easy to use, and we liked how it evenly sprayed the cleaning solution easily across our flooring. You will need to set aside time for your carpet to dry, but afterwards, we were pleased with the results; the colour and pile looked as they should, with no staining or water marks left behind.
This smooth-moving carpet cleaner packs up into a compact unit, making it ideal if your storage space is limited. Set-up is simple, thanks to responsive and clear controls, as well as a water tank that doesn’t spill when being filled and reattached.
As for its cleaning skills, it glided easily across all our floor types, sucking up excess water well so that fabrics weren’t left saturated. It removed 85% of stains from upholstery fabrics, including fresh coffee and tea, leaving no marks behind.
It struggled with mud on carpet, though, and wine stains on laminate. This means it may not suit if you have pets, but otherwise, it’s a nifty buy for giving your carpets a deep clean from time to time.
Carpet cleaners use a combination of specially formulated cleaning solutions and powerful brush heads to reach deep into your carpet pile, lifting away grime and ground-in dirt. In many cases, they also restore carpet, leaving it looking refreshed and almost new.
The machines conquer this challenging job thanks to their clean and dirty tanks. Water and any cleaning solution are kept in the clean tank, then after you pull the trigger, this solution is sprayed onto the carpet before being sucked back into the dirty water tank.
Many of the models we tested proved versatile bits of kit, also boasting hard-floor, upholstery and even stair-cleaning capabilities.
Our experts at the Good Housekeeping Institute recommend you deep clean all your carpets once a year. But if you have allergies or pets, deep clean once every six months. If a stain appears on your carpet – especially ones such as wine, mustard or curry – treat it immediately.
Setting you back up to £300, good carpet cleaners aren’t cheap but investing in one should help keep your carpets refreshed and in good condition for longer.
Top brands include Vax, Bissell and Rug Doctor and you’ll notice several from the former on our list. The reason? Well, at the GHI we’ve tested every single carpet cleaner in Vax’s range and the market-leader has a wide range of machines to serve consumers’ differing needs. They cater to a range of budgets too, and its two Spotwash models should cost you closer to £100.
If you don’t have space for the sizeable appliances, you can hire professional cleaners to deep clean your carpets, which costs around £200. Alternatively, you can hire a machine from companies such as Rug Doctor for around £25 (with extra for detergent).
Blossom is our Senior Homes Tester. Passionate about finding the best home products and appliances for our readers, she has tested everything from blenders to pizza ovens. Blossom enjoys delving into the intricacies of products and refining testing protocols for hundreds of items. Innovative items like robot vacuum cleaners and wine coolers are among her favourite tests to date, and her most notable accomplishment is toasting 360 slices of bread in a determined bid to find the best toaster. In her free time, Blossom openly admits to being a music geek and indulges her creative side through crocheting, baking, singing and writing.
10 house rules that will cut cleaning time
6 ways to dry laundry quickly
How to clean a hairbrush
5 ways to stop sheets tangling in the dryer
How to remove heat rings and watermarks
Everything you need to know about bedbugs
How to look after your cashmere
How to sharpen a kitchen knife
Tips to remove static in clothes
Good Housekeeping, Part of the Hearst UK Fashion & Beauty Network
Good Housekeeping participates in various affiliate marketing programs, which means we may get paid commissions on editorially chosen products purchased through our links to retailer sites.
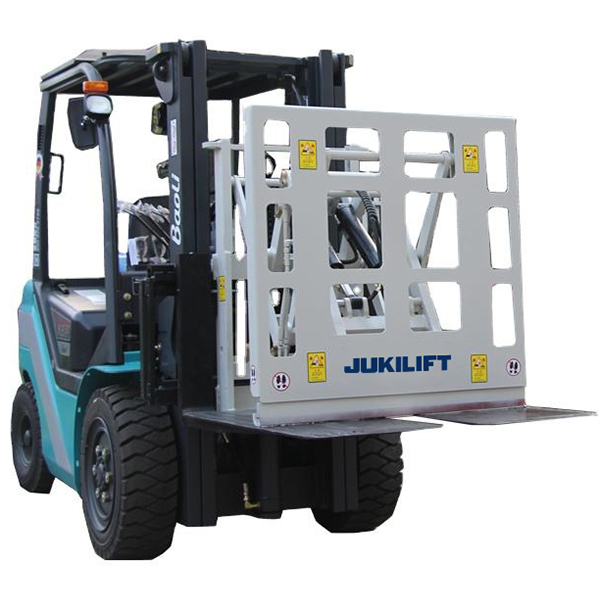
Reach Truck ©2023 Hearst UK is the trading name of the National Magazine Company Ltd, 30 Panton Street, Leicester Square, London, SW1Y 4AJ. Registered in England. All Rights Reserved.