Under intense public and stakeholder pressure, many oil and gas companies have pledged to achieve zero-carbon emission targets by 2050. The energy industry, however, is still in the process of standardizing technologies for site monitoring and measuring the footprint of fugitive emissions, despite the fact that carbon accounting and methane reduction strategies are now considered a must-have for oil and gas companies.
Before becoming a product manager, I spent 15 years developing and implementing technologies that address safety, efficiency, and autonomy for the energy industry. And in my previous role at Schlumberger (now SLB) on the Global Innovation team, I focused on technologies that would infuse intelligence and create digital twins of every oil and gas location. Cable Clamp Joint
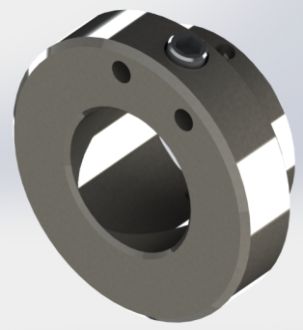
Those very technologies—performing reality capture to generate accurate, interactive digital twins of the sites, structures, and assets we cared about—are precisely the solution needed to detect leaks early and ultimately reduce methane emissions worldwide.
According to McKinsey, about 57% of the oil and gas industry’s carbon footprint is coming from methane emissions, one of the most powerful greenhouse gases. So the US market is hungry for a solution. To incentivize methane monitoring and leak reduction, the Inflation Reduction Act imposes fines on over-emitting entities and provides $1.55 billion in financial incentives for the energy industry to better monitor methane emissions and to help address legacy pollution from the oil and gas sector. The only hiccup in this plan is that there is no standardized method to measure baseline emissions or monitoring protocol.
Now, energy companies must figure out the best way to carry out their methane emissions baseline measurement, leak detection, and repair.
Where Is the Methane Coming From? The energy industry’s methane emissions arise from two main sources: leaks and vents. Leaks, also referred to as fugitive emissions, come from unintended events like holes in pipelines or leaking seals. Vents are deliberate emissions, whether from equipment operated by natural gas or from maintenance activities. Roughly 25% of emissions are considered “unavoidable.” This is because of the operating procedures involved in the ramp-up and ramp-down periods of oil and gas assets and the limits of current technology to completely prevent fugitive emissions.
The remaining 75% of methane emissions, however, can be eliminated with a proactive, preventative approach and the use of technology.
A small number of “super-emitter” leaks—such as open thief hatches, unlit flare stacks, open pilot lines, or open bypass valves—create a disproportionate amount of upstream oil and gas methane emissions. The highest-emitting 5% are responsible for approximately 50% of emissions.
Detecting Methane Emissions Several techniques are used for finding and measuring methane leaks, including satellites, large-scale aerial surveys, drone surveys, handheld devices, permanently installed methane detection sensors, and optical gas imaging cameras. The main difference between all these tools, besides cost, is in inspection frequency and resolution.
With a moderately small detectable leak size, very high resolution, and relatively low cost, aerial survey is an optimal solution for identifying leaks. Commoditizing drone services actually makes this the method of choice for proactive monitoring in a leak-detection program.
Regulations in California currently require final inspections to be conducted using Method 21 “sniffing” detection and quantification of gas leaks. If companies only perform the minimum required Method 21 inspections, a typical midstream facility inspection could take days to perform and unexpected leaks may remain undetected for months.
With hundreds of facilities in California, the California Resources Corporation (CRC) was spending significant time and resources to perform the labor- and time-intensive process to create visual inspection documentation of its equipment.
Starting in 2018, the CRC began using aerial drone mapping to transform aerial data into virtual 2D maps and 3D models of their pad locations, pipelines, processing equipment, and pumping stations, saving the company hundreds of thousands of dollars in time and labor costs over previous processes (Fig.1).
In 2022, the CRC updated its work flow to add an infrared laser methane sensor called a Laser Falcon on a drone to conduct proactive scans of its assets and facilities. The drone operations team now can import the scan data into a reality capture software platform by adding the methane visualization layer to existing maps, which allows them to easily and quickly identify and monitor any unexpected methane leaks. If a probable leak is detected, sometimes it can be fixed right away. For example, issues such as loose connections, an open bypass valve, or an unlit pilot at a flare stack can easily be the cause of the leak. Others, such as a leaking compressor seal or faulty leaking valve, typically require a maintenance request.
The work flow shown in Fig. 2 outlines the typical methane detection work flow using drones.
Luckily, additional data points and digital trace created using a reality capture solution facilitate automated and detailed maintenance information, streamlining the repair process even further.
The Role of Reality Capture Reality capture is the key element that takes the work flow from simply useful to extremely valuable. It does this by adding two crucial tools: process automation and digital trace.
With a reality capture solution, the drone flight plan can be automated using a repeatable flight plan, reducing time spent planning and ensuring that data is captured consistently every flight. The capability to upload data from the field adds another layer of simplicity to the work flow, eliminating trips back and forth from the field and the office and streamlining communication between onsite and offsite teams. Processing also is automated, and the data is conveniently stored in one place, organized by project location and ready to be retrieved and audited when needed.
Storing the data creates a digital trace, which then can be used to further analyze the data on a mobile device or annotate an issue such as a possible leak source and describe the repairs needed. Users then can create automated documentation for the maintenance reports sent directly to the maintenance team or integrate the repair information and history directly with the asset management system.
Scaling Methane Detection Programs The key to scaling a drone-based methane detection program is generating a useful report of the results. Capture and processing are only valuable if reporting is easy and automated and the final output contains actionable data.
Ultimately, the ideal solution will automatically connect reports to the associated asset in the system of record. Referenceable and sharable reports will facilitate collaboration from drone pilots on-site to the asset managers or environmental managers in the office, streamlining decision making and communication of the next steps. Creating a digital trace within an interactive digital twin makes methane inspections faster and more actionable within standard operating work flows. Imagine all your inspection data in one place, visualized on a map for easy reference and connected to the places where your asset data lives.
Autonomous Future of Continuous Inspections Within the reality capture industry, there is a vision of the future of reality capture that moves one step further. To fulfill its potential and truly reduce risk, automate manual tasks, and provide complete, unbiased visibility into companies’ operations over time, reality capture should be fully unified, automated, and intelligent.
Autonomous capture with quadrupedal robots such as Boston Dynamics’ Spot and autonomous drone docks such as the DJI Dock or Skydio Dock can make inspections and monitoring faster, simpler, and scalable. At the same time, it makes operations safer and more resilient by reducing worker travel time and exposure to dangerous work at heights and hazardous areas.
The Bottom Line For oil and gas companies, the ultimate goal of reality capture is to make energy operations cleaner by creating an effective and scalable emissions measurement system and work flow. Reality capture simplifies the process of continuous emissions monitoring. This enables proactive inspections, meaning leaks are detected earlier and repair costs are slashed, all while improving worker safety and efficiency. By taking the work flow to the sky and to the cloud, oil and gas companies can simplify the emissions monitoring process and ensure that methane stays where it is supposed to be, in the pipe.
Maurilio Espinoza, assistant production coordinator at CRC, contributed to this article.
The Journal of Petroleum Technology, the Society of Petroleum Engineers’ flagship magazine, presents authoritative briefs and features on technology advancements in exploration and production, oil and gas industry issues, and news about SPE and its members.

Gyro Inclinometer ISSN: 1944-978X (Online) ISSN: 0149-2136 (Print)