Champhai, the 22nd March, 2023: Champhai District Bawrhsap Pu James Lalrinchhana today laid the foundation stone for the construction of View Point Tower near NH 06 in Chhungte village under NHIDCL.
The View Point Tower will be constructed by Shri Balaji Construction Company (SBCC), which is constructing NH 06 road package III.The View Point Tower is 5 stories high and 16 meters high.The tower will also have a maintenance quarters, men's and women's toilets and motor parking.NH 06 is scheduled to be opened upon completion. Stone Cage
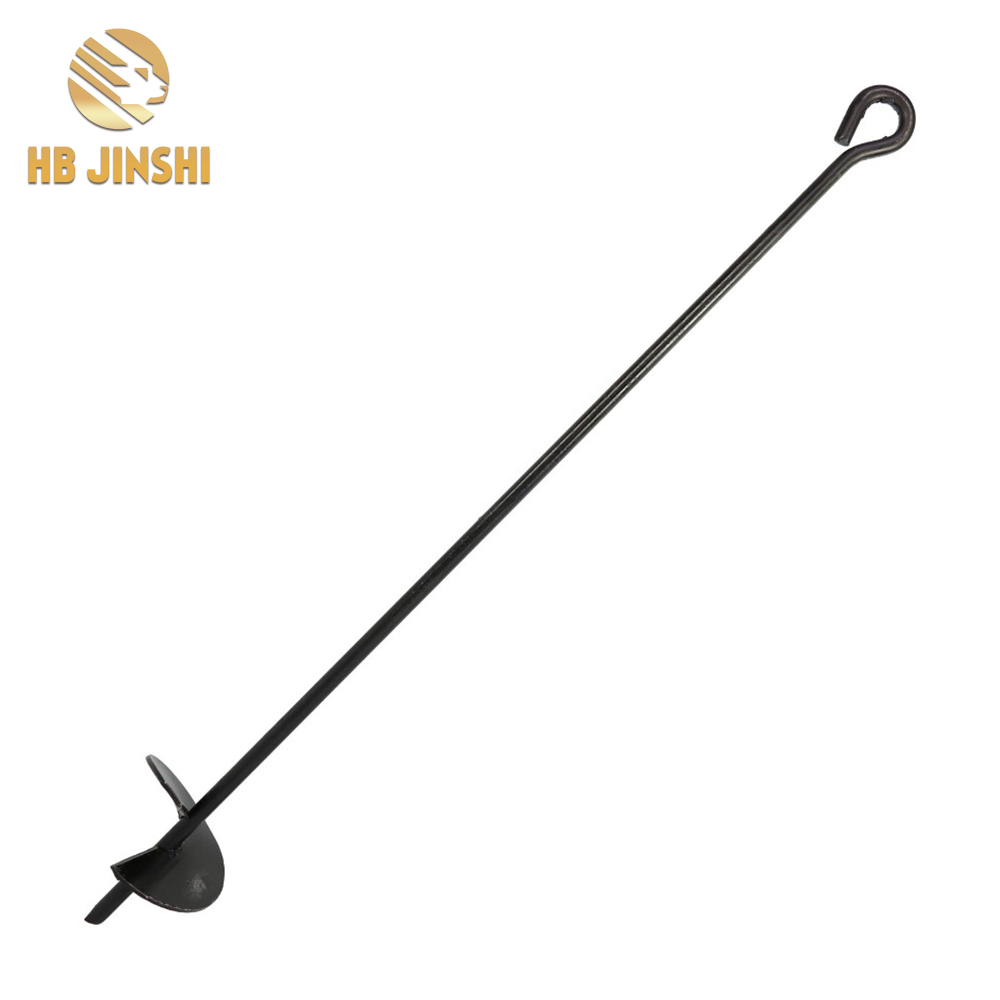
NHIDCL has received the Assistance to Central Agencies for Tourism Infrastructure Development through the Ministry of Tourism for the construction of View Point Towers in six NE States.When completed, the State Tourism Department will continue to manage the project.
After the completion of the foundation stone of the View Point Tower, Champhai District Bawrhsap inspected the NH06 road construction works and visited the 60 meter long northwest Tuipui road.He advised company officials to take action without destroying the soil and in compliance with the law;Spoil Bank-ah chauh paih tur leh gabion wall and other requirements should be taken seriously.He also advised the farmers to plant trees and soil fertile soil.He also urged the workers to do their utmost to complete the work within the stipulated time frame.
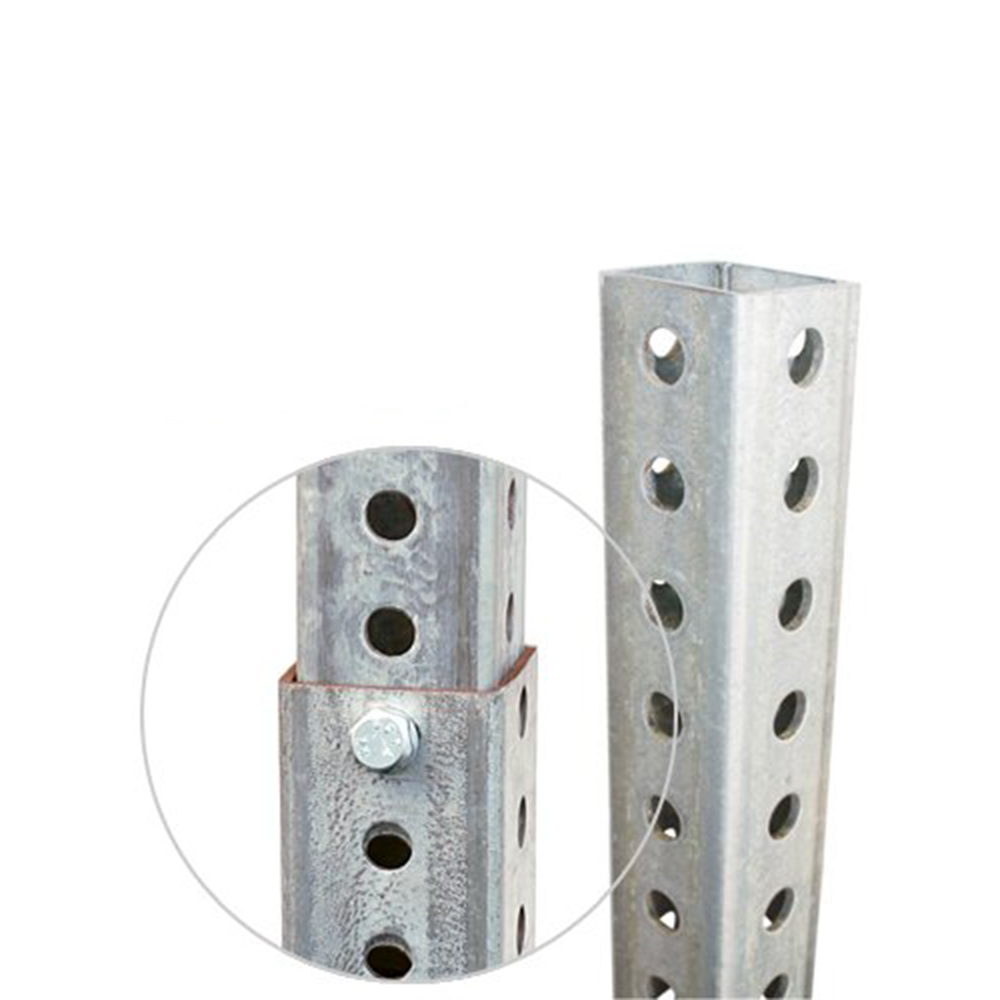
Snake Catching Stick Mr. Ajay Veer, Consultant, Mr. Abhisek Singh, Project Manager and other officials from NHIDCL, Mr. PL Dhiman, Project Manager, Shri Balaji Construction Company (BCC) and other Company officials, NGO and community leaders were present on the occasion.