KONYA, TURKEY — Imas’ research and development and engineering team have developed a new roller mill chassis construction material called Polymer Base Construction, which has been officially released for worldwide customers as one of the first examples of using polymeric composites in the milling industry.
The traditional way of manufacturing a roller mill chassis is to use either welded steel or cast iron. Instead, Imas today presents Polymer Base Construction with the major advantage of better vibration damping properties, which provides higher reliability and extended long-term durability for roller mills. Muyang Ring Die

Most of the roller mill manufacturers in the world still prefer the welded steel method for the production of roller mill chassis. In 2010, Imas replaced the use of welded steel for roller mill chassis with cast iron. With the mission of being an industry leader in research and development, the company has been working on the use of polymeric composites in the chassis construction of Imas machinery since 2020.
After the completion of all product development, real time testing, and patenting, the Multimilla Roller Mill with Polymer Base Construction has been officially released for customers worldwide.
The Polymer Base Construction chassis received “Product Showcase 2023” award by the International Association of Operative Millers (IAOM) during the Annual Conference and Expo April 17-21 in Minneapolis, Minnesota, US.
Polymeric composites are combinations of polymers (i.e., thermosets or thermoplastics) with various continuous and noncontinuous reinforcements/fillers, being a very special material that can be designed and produced for different uses and purposes.
Polymeric composites have been widely used in many fields, including aerospace, marine, and automotive industries. They may be used in many applications.
Effects of vibration on machinery, building
Machinery vibration, which occurs naturally during the operation of any machine, has some important hidden threats.
In the short term, high machinery vibration levels can have a disruptive effect on the sensitive operating adjustments of machines, which may also lead to inconsistency in the process and product quality. For this reason, damping of the vibration and keeping the resonance under critical levels is crucial for both the health of machinery and buildings.
In the long term, machinery vibration can cause failures that may result in shortened machine life, through the continuous effect and damage to the parts and materials (bearings, bearing housings, other moving parts, etc.). In addition, it can even create problems in the static structure of mill buildings, as it might also have impacts on worker health and safety.
Imas’ Multimilla Roller Mill presents higher operational reliability and extended long-term durability with Polymer Base Construction.
According to the tests and measurements carried out by Imas R&D center engineers and scientists from Konya Technical University and Necmettin Erbakan University, polymeric composite material has nearly 10 times better vibration damping ability than cast iron, and even 20 times better than welded steel.
As well as its better vibration damping ability, the polymeric composite chassis material has comparatively lower thermal conductivity, higher rigidity and corrosion resistance properties. It also has better production flexibility advantages with reduced production time, cost and carbon footprint.
“At Imas, we believe that the reliability of our machines is important as much as their technology,” said Murat Apakhan, Imas production and R&D deputy general manager. “For this reason, we continuously develop the structural design of our machines and systems through new engineering standards. Today we believe that we took a leading step with the first use of polymeric composites in the milling industry.’’
As well as Multimilla roller mill, Polymer Base Construction already has been introduced for some of Imas’ feed milling machinery, including the Viteral series flake roller, hammer mill and pellet press machines.
Tests on prototype production at IMAS R&D center.
KANSAS CITY, MISSOURI, US — Part One from A to M of the latest grain and milling technology offered by European-based suppliers to the international market from the May issue of World Grain. Find company profiles that discuss service range, product technologies and research and project developments for each European-based advertiser.
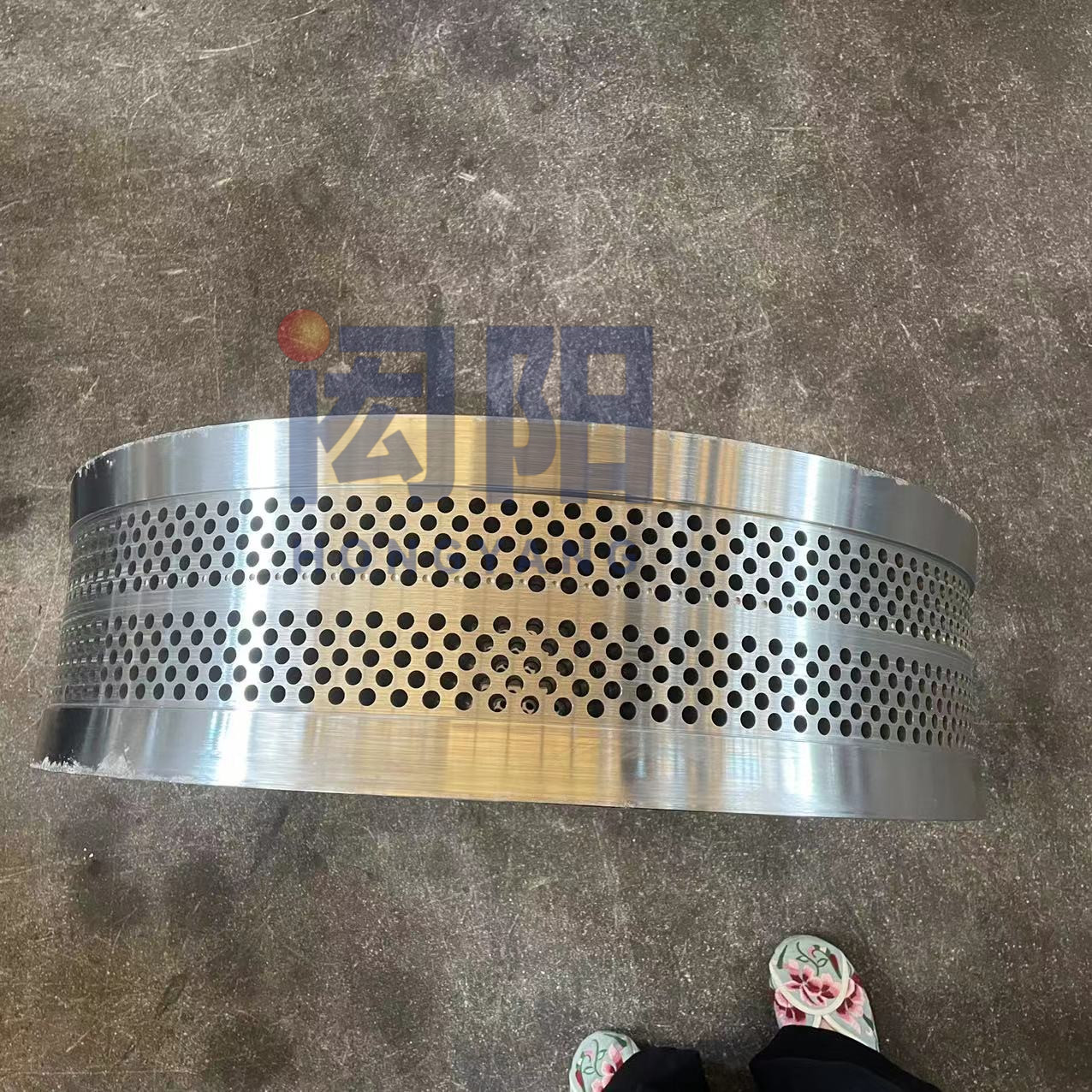
Feed Pellet Mill KANSAS CITY, MISSOURI, US — Part Two from N to Z of the latest grain and milling technology offered by European-based suppliers to the international market from the May issue of World Grain. Find company profiles that discuss service range, product technologies and research and project developments for each European-based advertiser.