Sawing nonferrous materials can be challenging, but armed with the right band saw blade and plan to cut the material, a manufacturer can expect high-quality cuts and long-lasting blades.
Nonferrous materials (those that do not contain an appreciable amount of iron) are generally chosen because of their various properties. In most instances, they are lightweight, corrosion-resistant, highly conductive, and nonmagnetic. 160mm Circular Saw Blade
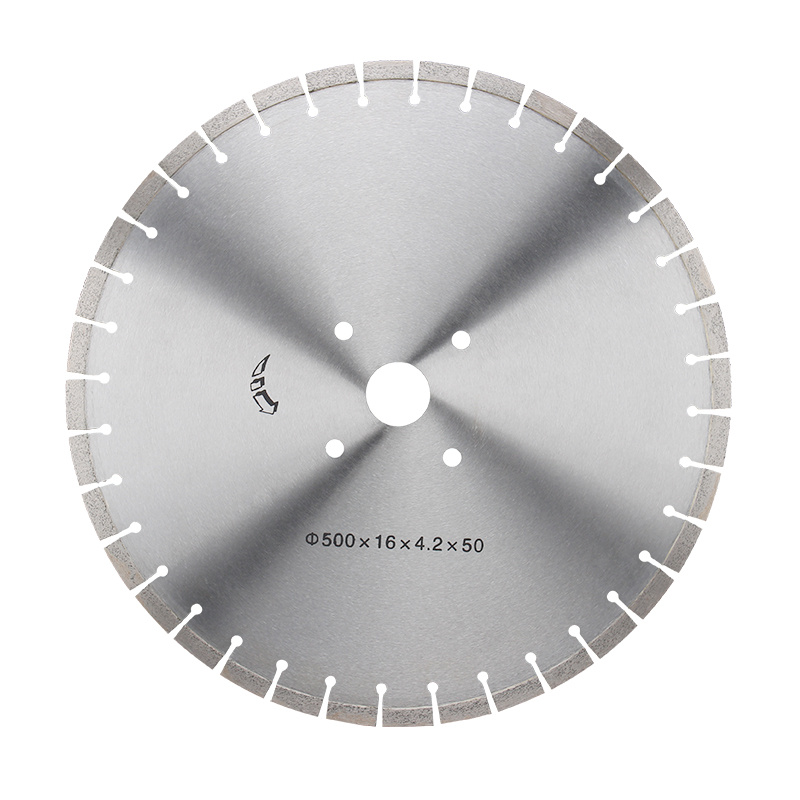
However, these materials present their own set of unique cutting issues. It is helpful to know upfront what you may encounter when sawing these materials. That’s the first step in figuring out how to address and overcome the challenges of cutting nonferrous materials.
The nonferrous material range includes, but is not limited to, aluminum, copper, lead, tin, titanium, and zinc. Copper alloys, such as brass and bronze, also are a part of this family. Depending on their composition, some of these materials may have several grades, so the sawing parameters and considerations will be different.
What are some of the sawing issues that operators are faced with when dealing with these materials? They have to cope with material abrasiveness, gummy characteristics, blade chip loading tendencies, blade gullet capacities, and maintaining optimal blade speed.
In general, soft materials such as aluminum and copper are easier to machine than harder and tougher materials such as titanium, but the soft materials can prove more cumbersome under the teeth of a saw blade.
Nonferrous materials such as aluminum and brass have low melting points compared to harder metals. If you do not take proper precautions, the heat created when sawing can easily result in loading molten aluminum into the gullets and onto the blade’s teeth, rendering it useless and glazed over. Additionally, the operator must consider that while they can get away with a faster feed rate, they must control factors that influence chip load.
Overloading the gullets of the teeth can cause a lot of problems, such as teeth chipping off the backing (also known as strippage), the blade jumping around in the material, and rough cuts. A way to combat this is to use a coarser pitch blade rather than a fine-toothed blade. This allows the gullets to evacuate chips more easily, resist compaction, and hopefully clear out the kerf before being completely filled up. Also, soft material does not require much feed pressure in the sawing process as compared to hard materials because it doesn’t take much pressure for the teeth to engage the material.
When cutting soft materials such as aluminum and copper, the best approach is lower feed pressure, higher feed rate, and much higher blade speed. This will allow for good blade penetration and chip removal in a timely manner.
One more thing to consider is that while soft metals are easier to machine, it can be more challenging to achieve a desirable finish when you consider the actual micro-level mechanics of the material separating from the saw tooth. Choosing the wrong blade, namely one without a positive rake, can compress the material's microstructure, making it harder while cutting it. Softer materials may appear easier to cut, but it’s important to take equal amounts of care when sawing these materials so you do not produce scrap or ruin your band saw blade.
Nonferrous structural materials, such as copper tubing or aluminum shapes, compound this issue as they not only suffer from the standard nonferrous cutting issues, the interrupted cuts that result when the teeth move in and out of the material can damage the blade. (It can be difficult to find the perfect tooth pitch when sawing these materials because the teeth are going from larger cross sections to smaller ones during the cutting process.) As with all structural material, special attention must be paid to proper blade selection and tooth pitch.
When sawing through harder and tougher nonferrous materials such as titanium and zinc, gullet loading is a rare concern because the material does not tend to load up the gullets the way soft materials do. This allows more teeth to be used when cutting hard materials, increasing productivity. A major difference between sawing hard and soft metals is that hard metals require more feed pressure, which enables better tooth penetration.
These types of hard materials cannot be cut quickly, so a slower feed rate and a slower blade speed are used to allow the blade to penetrate the material and pull the necessary chip load throughout.
Bimetal band saw blades can offer a fast, quality cut on nonferrous metals and can hold up to the rigors of fast-paced cutting. When used correctly, they also can last a long time.
Blade manufacturers typically use a high-speed steel (HSS) for blade teeth, bonding it with a variety of methods, such as laser beam welding or electron beam welding, to a high-strength carbon steel back. With this combination, operators get the cutting speed they’re looking for as well as the durability that non-bimetal blades lack.
It is generally true that a saw operator can go through more saw blades when cutting hard materials, but it depends on which hard materials and which soft materials are being compared. Bimetal band saw blades can be an excellent choice that may result in increased blade life. For example, M51 HSS bimetal blades can achieve cutting speeds comparable to blades made with M42 HSS and provide longer tool life. M51 is more abrasion resistant than M42 and that can help to increase blade life.
Also, the cutting performance of the HSS is greatly increased through alloying with cobalt and vanadium. These alloying elements substantially increase the heat and wear resistance.
Cutting with conventional bimetal blades can result in heat buildup and can create areas with heat-affected zones (HAZ), which compromises the integrity of the metal. However, one of the latest manufacturing processes being used today for manufacturing bimetal blades eliminates the HAZ, which helps reduce tooth-stripping problems.
This process joins two strips of HSS wires to a backing steel in a solid phase, using the principle of solid-state diffusion bonding. The solid-state process uses only 10 to 20% of the amount of heat that is found in a welding manufacturing process. This bonding process along with the HSS base produces blades that achieve faster cutting speeds without compromising quality.
Another tooth strippage deterrent involves weld contact between the backing material and the saw teeth. The diffusion bonding process, unlike the electron beam welding process, provides 170% more weld contact with the teeth, so blades have a significant reduction in fracture and breakage.
Also, blades manufactured with a diffusion bonding process have an advantageous tooth geometry. For example, HSS wires are bonded to the sides of the strip and the fusion zone (the portion of the metal that has undergone melting) which is parallel to the teeth, creating a grooved-tooth geometry. The grooved-tooth geometry produces two cutting surfaces separated by the blade. Soon after initial blade use, the teeth develop a groove that is U-shaped, 0.001 to 0.002 in. deep between the two HSS edges, altering the blade area engaged in the cut. The groove remains at a constant depth and wears at the same rate as the teeth.
Advancements in band saw blade design can lead to better cutting results. For example, bimetal blades manufactured with a diffusion bonding process develop a grooved-tooth geometry—two cutting surfaces separated by the blade—when put to use. The teeth develop a groove that is U-shaped, 0.001 to 0.002 in. deep between the two high-speed steel (HSS) edges. This tooth design helps to remove chips from the cut, eliminating a large impediment to successful cuts.
Dual chips, also referred to as split chips, are the result of the grooved-tooth geometry. The bonus is that they are easily removed from the cut, which is important because when chips remain in the cut, they run the risk of packing the gullets and bonding to the teeth. Split chips are more easily removed because they’re curled and fall away from the cut. The result is 25% faster cutting than blades made with conventional electron beam welding.
Also, the U groove permits increased coolant flow to the cutting surface, and proper coolant flow not only cools and lubricates the blade, it flushes out chips that are caught in the spaces inside tubes, for example.
When cutting soft materials such as aluminum, some end users prefer to use carbon blades over bimetal because the carbon blades may have larger tooth pitches and are less expensive upfront. However, the disadvantage with carbon blades is that they don't last as long as bimetal.
Carbide grit band saw blades feature a continuous or gulleted cutting edge for high-fatigue resistance. They can make precise cuts in a variety of nonferrous materials, mostly nonmetals, such as steel-belted tires, composites, reinforced plastics, composite graphite, and fiberglass. These blades perform best at much higher blade speeds than typically found on a standard metal cutting band saw.
Carbide-tipped blades are common for cutting both ferrous and nonferrous solid materials in production applications. As mentioned previously, nonferrous cutting with carbide blades does perform best when the band saw is capable of high blade speeds. Depending on the application, that could mean anywhere from 1,000 SFPM to 7,000 SFPM or more if high production is the goal.
That’s not to say nonferrous materials cannot be cut slower than this with carbide blades, but both carbide-tipped and carbide-grit work best in a production setting.
One particular manufacturer was challenged with sawing 15-in. rounds of titanium (6Al-4V). The sawing process was hampered by poor blade life and extremely rough cuts using carbide-tipped blades. It was determined that the gullets were loading, causing a washboard effect on the cut and generating excessive forces on the teeth.
By switching to a coarser tooth pattern while adjusting both the blade speed and feed rate, the customer was able to increase blade life by approximately 40% in addition to increasing production. The cuts themselves were smooth and line free.
Another manufacturer encountered saw teeth gullets that had loaded up with gummy material as well as rough cuts when cutting 8-in. aluminum solids on what could be described as a general-purpose saw. The maximum blade speed was approximately 270 SFPM. In addition, the machine would only take a 1-in. blade, which limited the tooth patterns available in both bimetal and carbide-tipped blades.
In this case, the only viable option was to find a coarser tooth. The solution was a carbon blade with a 1.3 tooth pitch. While one would expect a carbon blade to not perform or last as long as a bimetal blade due to the running conditions, the carbon blade did in fact outperform the bimetal. It lasted longer and cut faster.
In both cases, a band saw blade expert helped these two manufacturing companies find the right blades for the job. Sawing nonferrous materials doesn’t have to be daily challenge. The right band saw and sawing parameters can make all the difference in the world.
North American Sales Manager, Saws and Hand Tools
See More by Jay Gordon
Read more from this issue
Find The Fabricator on Facebook
Find The Fabricator on Twitter
The Fabricator is North America's leading magazine for the metal forming and fabricating industry. The magazine delivers the news, technical articles, and case histories that enable fabricators to do their jobs more efficiently. The Fabricator has served the industry since 1970.
Easily access valuable industry resources now with full access to the digital edition of The Fabricator.
Easily access valuable industry resources now with full access to the digital edition of The Welder.
Easily access valuable industry resources now with full access to the digital edition of The Tube and Pipe Journal.
Easily access valuable industry resources now with full access to the digital edition of The Fabricator en Español.
In this episode, Christian Streu, CFO of The Partner Companies, and Charles Cohen, President of FotoFab, join The...
© 2024 FMA Communications, Inc. All rights reserved.
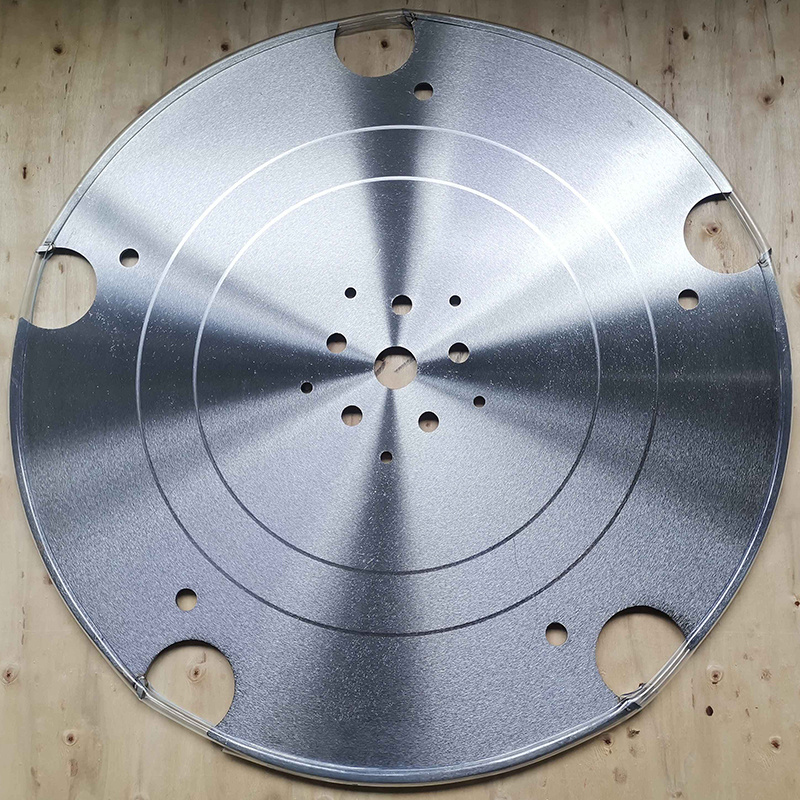
255mm Mitre Saw Blade Not yet registered? Sign up