In direct extrusion, raw ingredients such as polymers, fillers, and additives are mixed, reacted, and devolatilized in a high-speed, twin-screw extruder and directly made into a final product, bypassing pelletizing. Although high-speed, twin-screw extruders have been used for many years to produce sheet, film, profile, and fibers, only in the past five years has there been a concerted effort to use them to perform direct extrusion. D irect extrusion using twin-screw technology was initially mandated, in desperation, by the need to produce formulations that were adversely affected by the second heat and shear history inherent in the single-screw extrusion step. Once the technical viability of direct extrusion was demonstrated, it became apparent to the marketplace that substantial cost savings were also possible using this technology. Additional benefits include the ability to adjust formulations inline to accelerate development efforts, and to maintain a proprietary in-house manufacturing process. Materials that benefit from direct extrusion include filled olefins, TPE/TPO/TPVs, polyesters, PVB, wood-fiber composites, adhesives, foamed polymers, nylons, and degradable polymers. Corotating twin-screw extruders allow screw rotation up to 1200 rpm, and dominate the high-speed, twin-screw market for applications that require intensive mass transfer. Counter-rotating intermeshing and nonintermeshing twin-screw extruders are also being used for direct extrusion applications. Typical processes performed in the twin-screw extruder, regardless of the mode of operation, include reactive processing, devolatilization, alloying, and compounding particulates into plastics. High-speed, twin-screw extruders are starve-fed devices in which the output rate is determined by the feeder(s), and screw rpm is used to optimize compounding efficiencies. Feeders maintain consistency of the formulation, introduce ingredients in the proper order along the length of the process section, and regulate the extent of mixing. For direct extrusion, the feeding and materials handling system to the twin-screw extruder is critical to maintain front-end pressure stability. Loss-in-weight feeders are typically specified for direct extrusion where the auger speed is modulated up or down to maintain a consistent mass flow to the extruder, based on the rate of weight changes in the hopper situated on a load cell. Twin-screw systems may use up to eight or more feed streams. Volumetrically controlled feeders are generally not acceptable, even for premixes, due to the inherent fluctuations in feedrate that result in pressure fluctuations at the die inlet. If pellets were the end product this would be a nonissue, since ±20 percent dimensional stability for a pellet is often acceptable. Almost all high-speed, twin-screw extruders use segmented screws that are assembled on high-torque hammered and splined shafts. Barrels are also modular and can be configured from feed, plain, vent, side stuff, and liquid addition sections. Each barrel section is electrically heated, and is internally cored for high-intensity cooling near the process melt.
This transparent view of a parallel twin-screw extruder illustrates the structure of the basic hardware that accomplishes compounding and end product extrusion in one step without subjecting the material to interim pelletizing and multiple heat histories. Virtually infinite variations of the hardware can be specified, depending on the desired product. Sjsz Conical Twin Screw And Barrel

The modular nature of twin-screw extruders offers extreme process flexibility. Barrels can be rearranged, the L/D can be increased or decreased, and screws can be modified. For direct extrusion applications, the machine is usually somewhat longer so that the latter part of the process can be dedicated to pumping with a more stable pressure than is mandated for pelletizing (see photo at right). Twin-screw Extruder Function and Design Twin-screw compounding extruders perform these basic functions: feeding, melting, mixing, venting, and developing die/localized pressure. The segmented nature of the twin-screw extruder in combination with the controlled pumping and wiping characteristics allows specific screw and barrel geometries to be matched to the required process tasks. This enables the same machine to perform both dispersive and distributive mixing, which is a major benefit for certain products that are fabricated by direct extrusion. One example of this scenario is the mixing of glass microspheres into an extruded part so that the spheres never experience the high-shear stress associated with plastication in the single-screw extruder. Screw design is the heart of any twin-screw compounding extruder. An infinite number of screw design variations are possible. There are, however, only three basic screw elements: flighted, mixing, and zoning. Flighted elements move material past barrel ports, through mixers, and out of the extruder to the die. Zoning elements isolate two operations within the extruder. Screws can be made shear intensive or passive, based on the elements used in the design. (It is interesting to note that almost all materials that are processed in single-screw machines were compounded on a high-speed, twin-screw extruder.) Mixing in the screws may be dispersive or distributive. The wider a mixing element, the more dispersive it becomes. Elongational and planar shear effects occur as materials are forced up and over the land, and more energy is imparted into the process. Narrower mixing elements are distributive in nature with high melt division rates and significantly less elongational and planar shear (see diagram below). The pressure gradient in the twin-screw extruder is determined by the selection of screws. Since the twin-screw extruder is a starve-fed device, flighted elements are placed strategically so that the screw channels are not filled and there is no pressure underneath downstream vent/feed sections. This facilitates downstream feeding of fillers (e.g., calcium, flame retardants, talc, titanium dioxide, and so on). The zero-pressure feature also facilitates single or multistage devolatilization. The viscosity of melting resin is high, so in the early stages of the extruder the strain rates can produce high stress rates. These may be critical to attain dispersive mixing, but can also cause degradation of shear-sensitive materials. In the latter stages of the extruder the viscosities fall such that high strain rates factored against a decreased viscosity produce comparatively low stress rates that enable heat- and shear-sensitive materials to be mixed with a minimal peak shear.
Above is a ZSE-50 twin-screw extruder with gear pump front end and Vulcan downstream profile system. Gear pumps are typically protected by an upstream screenchanger that filters out contaminants. Alternatively, a single-screw pump front end attachment can be specified in place of a gear pump. At left is the ZSE-40 twin-screw extruder with single-screw pump from Merritt. Both the ZSE-50 and ZSE-40 overall extrusion systems are designed and supplied by Leistritz. Some components come from other suppliers, including those noted.
Process Design Combining compounding/devolatilizing with direct extrusion in a high-speed, twin-screw extruder presents significant process design challenges. The system requires high mass transfer in combination with consistent pumping. The selection of screw elements must take into account the mixing requirements, and also provide stable pumping to the die or front-end device. For direct extrusion the machine is longer than a standard compounding extruder. The last sections of the screws are dedicated to building and stabilizing pressure. The vent is normally approximately 10D back from the end of the machine to allow enough process length to build a steady state pressure, as compared to 6D for a standard compounder. Distributive mixers are often used towards the end of the screws for thermal homogenization of the melt stream, which would normally not be required for pelletizing. To maintain dimensional tolerances, a gear pump front-end attachment may be used to build and stabilize pressure to the die. A gear pump dampens out pressure fluctuations by approximately a factor of 10 (i.e. ±200 psi on the inlet of the pump equals ±20 psi on the outlet of the pump). Gear pumps typically have upstream protection provided by a screenchanger. This prevents damage by filtering off-spec substances away from gear teeth (see photo at right). Alternatively, a single-screw pump front-end attachment may be specified in place of a gear pump. The length is approximately 10D, essentially the length of the metering section of a single-screw extruder. This device is more stable than a standard single-screw extruder since plastication and compression are not present, which is the main cause for pressure instability in a pellet-fed, single-screw extruder (see photo below). The twin-screw compounding system for direct extrusion is significantly more complex than a single-screw extrusion line. The feeding system to a twin-screw compounder sets the formulation tolerance and also plays a major role in pressure stability. There may be as many as eight or more feed streams into the high-speed, twin-screw compounding extruder. Typically, a PLC-based master control system is required to manage the system as well as facilitate recipe retrieval and data archiving. The residence time of 15 seconds to 2 minutes for materials in a twin-screw extruder must be taken into account for the pressure control algorithm. A possible control scenario is for the gear pump rpm to be locked to set a constant volumetric rate for the process melt stream to the die. Feeders are adjusted in very small increments every few residence times to maintain a stable front-end pressure over the long term. Screw rpm is continually adjusted, within limits, to maintain front-end pressure over the short term. If a screw’s rpms are allowed to adjust without limit, widely varying degrees of imparted shear might adversely affect the quality of the final product. When sequential feed streams are introduced into the twin-screw extruder at various points in the process, the closed loop control obviously becomes more complicated, as various residence times must be managed. The control software uses an algorithm program to analyze the inputs from key points in the system, make numerical calculations, and apply corrections to the screw rpm and feedrate. The objective of the algorithm is to maintain the gear pump inlet pressure at its setpoint. If this is successfully accomplished, the backpressure in the twin-screw extruder is held constant, which provides for consistent shear and mixing. With a stable melt delivery to the gear pump, the discharge flow and pressure to the die is uniform—the ultimate objective of the entire system.
Mixing can be primarily dispersive, as with the wider element, upper left, or distributive, as with the narrower element, at right.Various elements can be combined in screw design to meet whatever mixing challenge is at hand.
Delivering a Consistent End Product Providing a usable melt to the die and downstream system is only half the battle. To deliver a high-quality end product, the appropriate die and downstream equipment is required, whether the product is a film, sheet, fiber, or profile. The following examples identify products successfully made by direct extrusion:
Battery separator/sheet. A PE/silica formulation is premixed and fed into the extruder feedthroat and oil is injected into a barrel section in the early stages of the process. The materials are mixed and devolatilized in the twin-screw extruder process section, which is directly coupled to a sheet die. After the die, a high-pressure calendar “squeezes” the extrudate and sets the final dimension, eliminating the necessity for a gear pump and closed loop pressure control.
Foamed profiles. The polymer is fed into the twin-screw extruder and melted prior to gas injection. The polymer is intimately mixed at high pressures with high-division distributive mixers to minimize viscous heating. The latter part of the process section uses low-energy-input pumping elements so that the barrel sections serve as heat exchange devices to cool the process melt. A screw or gear pump front-end attachment may be used, depending on the particular application. Performing this process in a twin-screw extruder provides an alternative to the tandem single-screw systems traditionally used.
Filled film/sheeting. The polymer(s)/rubber/additives are fed into the main feedthroat and melted prior to downstream introduction of fillers (carbon black, talc, calcium carbonate) into the process melt stream via a side stuffer. The materials are mixed/devolatilized in the twin-screw extruder, which is typically mated to a screenchanger and gear pump front-end assembly. Olefins, TPOs, and fluoropolymers all use this system configuration.
Adhesive compounding. Rubbers, tackifiers, fillers, and oils are mixed and devolatilized in the twin-screw extruder with a gear pump front end upstream from a film/lamination die, or a rod die for direct glue stick profile extrusion. In some instances, the twin-screw process has proven superior to separate twin-screw compounding and single-screw extrusion operations, as a demixing effect often occurs as the materials coalesce in the single-screw process.
Wood-fiber/composite products. The primary functions of the twin-screw extruder in this application are to remove water and distributively mix the natural fibers. Because this type of product typically cannot be passed through a screenchanger, a single-screw pump front-end attachment is used. Products include profiles for decking and sheeting.
Direct extrusion from a high-speed, twin-screw extrusion system can improve quality and reduce costs when compared to a two-step compounding/production operation. The downside of this emerging technology is that the intricacies of the overall system increase as the complexity of the upstream materials handling/feeding equipment are now combined with the nuances associated with sizing and cooling an extruded part. In spite of the associated challenges, there are many successful direct extrusion installations of a high-speed, twin-screw extruder, many of which are highly proprietary and confidential. The product mix and anticipated volumes need to be carefully assessed to determine whether direct extrusion is the preferred manufacturing method, based on the prevailing economic and product performance issues.
CONTACT INFORMATION Leistritz, Somerville, NJ Charlie Martin; (908) 685-2333 [email protected]
How to Optimize Your Medical Injection Molding Process
Planet vs. Plastics: Not All Plastic Problems Are the Same
Thermoformer Claims Highest Throughput per Square Foot
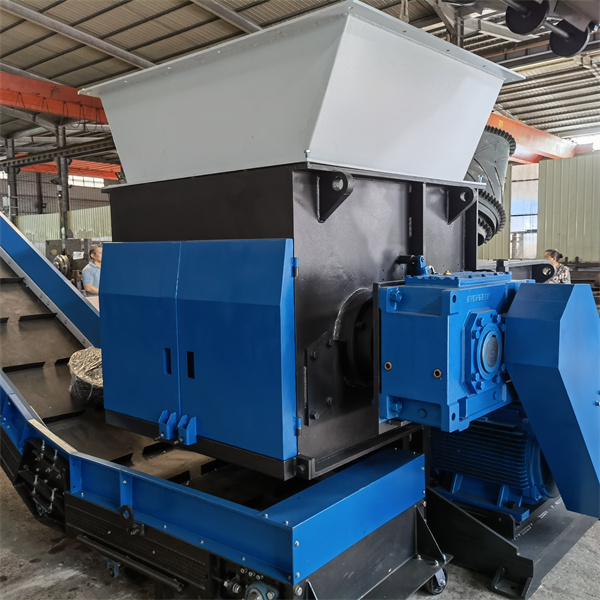
Screw Barrel For Injection Machine Copyright © 2024 All rights reserved. Informa Markets, a trading division of Informa PLC.