Siemens teamed up with Solution Partner Think-PLC to bring an exciting advancement to the additive manufacturing industry. This partnership has produced a two-in-one robot controller, specially designed by Think-PLC for implementation at Siemens' Charlotte Advanced Technology Collaboration Hub (CATCH) facility in Charlotte, North Carolina. In June 2023, Think-PLC was asked to design, build and install the robot controller.
“CATCH was launched by a group of craftsmen, engineers, technicians and scientists with a passion for additive manufacturing and a mind for business, who love to answer the hard questions,” explains Zachary Gray, business development manager, additive manufacturing, at Siemens. Teaching Robot
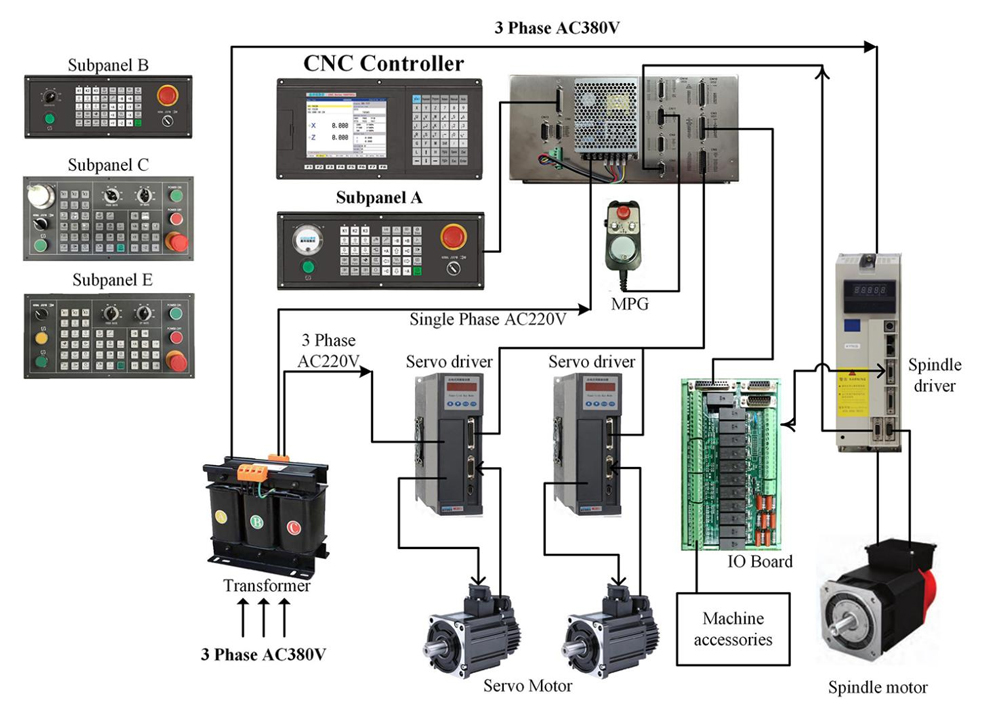
Get your subscription to Control Design's print magazine, free to qualified individuals in North America.
Some of those questions include:
“We created CATCH so that industry leaders outside of Siemens, such as machine builders and machine users, can leverage the deep technical knowledge of Siemens from our software, hardware and research-and-development (R&D) group to approach the challenges that the additive manufacturing industry faces,” says Gray. “By doing this, we are helping to industrialize 3D printing.”
Siemens unveiled a notable advancement in robotic control technology with its product, Run MyRobot, as featured in its new option suite for the Sinumerik One machine tool controller. In the CNC manufacturing space, Siemens has demonstrated a superior integration of its technology for robot control, leveraging its standard machine tool interface (Figure 1).
This innovation isn't the first instance of a CNC manufacturer utilizing its technology to govern a robot, but Siemens has distinguished itself by achieving comprehensive control over the robot's kinematics while incorporating enhanced features. What sets Siemens apart is its commitment to maintaining a technically robust interface, contrary to the trend of simplifying capabilities observed in other solutions.
Siemens' Sinumerik multi-channel control is particularly noteworthy for its profound motion-control capabilities. This advanced control system enables more precise regulation of the tool, resulting in superior outcomes in additive manufacturing processes. The ability to exert full control over the robot kinematics through a standard machine tool interface is a testament to Siemens' dedication to delivering high-performance solutions.
Crucially, Siemens has refrained from "dumbing down" the interface and capabilities. Instead, Siemens has added a user frame control method on top of an already highly capable control system. This strategic decision not only preserves the advanced features but enhances the user experience, allowing operators to leverage the full potential of Siemens' technology.
The introduction of the robot controller marks a leap forward for end users, as it promises benefits that will optimize operations and boost productivity. In order to simplify processes, the robot controller was designed to complete repetitive motions in a nontraditional method. The unified platform provides users with advanced programming capabilities, facilitating the creation of repetitive robotic motions with precision and ease.
With the seamless integration of Siemens Sinumerik Run MyRobot technology, end users now have the power to control robots and machine tools through a unified interface. This streamlined approach enhances operational efficiency and eliminates the cumbersome task of switching between different systems.
“Think-PLC was the partner we selected to have the rubber hit the road,” explains Gray. “Siemens has a lot of great products, but we depend on our solution partners, system integrators and machine builders to apply those solutions in production environments to realize a digital enterprise. In a nutshell, Think-PLC was the partner that designed, built and commissioned an electrical cabinet that integrated a Sinumerik-based six-axis robot with a directed-energy-deposition (DED) end effector.”
Imagine the time and effort saved by having everything accessible from a single, user-friendly platform. End users will enjoy unparalleled programming capabilities, empowering them to effortlessly create repetitive robotic motions.
Siemens looked at five different solution partners to implement this first phase of building the DED-Robot @ CATCH. “It was a very short timeframe and required a lot of flexibility on account of the R&D project environment,” notes Gray. “Along with having a great reputation in industry in both the factory-automation and complex-motion-control arenas, Think-PLC was willing to take the challenging requirements while having a very customer-centric mindset. They hit it out of the park.”
“The DED-Robot @ CATCH will be used as a flexible production cell both for new 3D-printed parts and repair applications,” explains Gray. “We plan to focus on industrial additive-manufacturing projects that leverage the benefit of the digital thread and digital twin, such as in-situ monitoring, closed-loop control of the deposition process, bringing subtractive and additive together and leveraging the Sinumerik digital twin integrated into the Siemens software portfolio.”
Siemens has set a new standard in CNC manufacturing by seamlessly integrating robot control within its standard machine-tool interface. The intricate control provided by Sinumerik One channel ensures a level of precision that significantly elevates the quality of products in the realm of additive manufacturing. Siemens' commitment to maintaining and enhancing the technical capabilities of its control system underscores its leadership in this evolving landscape.

Kuka Robot Arm Leaders relevant to this article: