The secret life of carbon fiber—cycling’s most mysterious material.
Since carbon fiber essentially took over the performance cycling world two decades ago, the bike industry continues to crank out ever-lighter, stiffer, and more impressive designs that were impossible to make in metal. Waterproof Building Materials
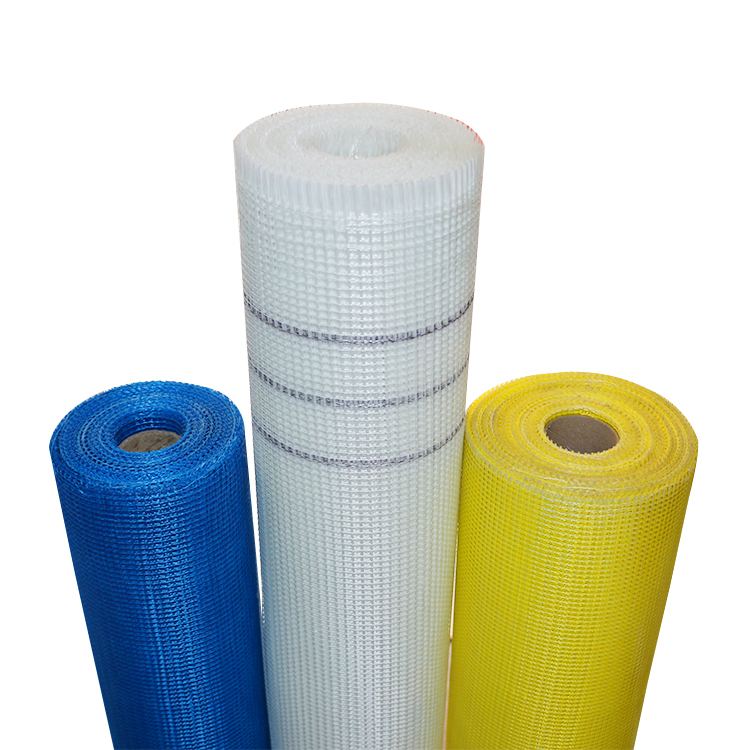
But carbon fiber products are sometimes seen as more obscure and mysterious than their metal counterparts. Here are 11 facts you might not know about the material.
Join Bicycling All Access for more in-depth gear info
It’s true, that most of the cycling industry’s carbon fiber products come from China, Taiwan, and Vietnam (and, increasingly, Indonesia, Cambodia, and Myanmar). But some carbon fiber frames and parts are also made in U.S. bike factories (Allied, Enve, Ibis, and Argonaut), Canada (We Are One, Bridge), and Italy (Sarto, Basso, Colnago's C68).
Despite its reputation as an aerospace material, carbon fiber is actually as easy to work with on a small scale as metal tubes. Smaller American manufacturers and even individual builders can work with carbon. And not just the finished tubes available from companies like Italy’s Dedacciai or Rock West in Utah. Several builders create frames from carbon sheets in much the same way as big frame factories.
[The Differences Between Bike Frame Materials—Explained]
Carbon fiber is typically made of a material called polyacrylonitrile (PAN) fiber. (A less common precursor is called pitch.) The PAN fiber is cooked to extremely high temperatures, which burns off all the non-carbon material and leaves a series of very thin, long fibers. The more processing, the more the stiffness increases.
It’s a sophisticated industrial process, and only a few companies worldwide can make raw carbon fiber. Per a 2010 U.S. Department of Energy report, more than 90 percent of the world’s carbon-fiber supply comes from just six companies: Toray, Zoltek, Teijin (Toho Tenax), Mitsubishi Chemical Corporation, Hexcel, and Cytec. Toray, Teijin, and Mitsubishi account for almost two-thirds of global carbon fiber production. Zoltek, Hexcel, and Cytec are headquartered in the U.S. and make a little less than a third of the world’s carbon fiber.
Carbon fiber comes in various forms: raw thread or sheet fiber (both continuous fiber), and short-tow fiber that can come as either sheets or clumps of chopped, very short-length fiber.
Chopped fiber is used in products like pedal bodies. Sheet style is most common in bike frames, and is what it sounds like: continuous sheets of carbon fiber (called plies), which look like bolts of fabric and are typically about as wide, coming wrapped on giant spools. Raw thread is far less common in the bike industry; only a handful of bike makers have the technical capability to work with raw thread.
We say “carbon fiber” or “carbon” but what we really mean is “carbon-fiber composite”—it’s not the only material in your frame. That’s because carbon fiber’s incredible stiffness properties come at a price: On its own, it is quite brittle and prone to splitting and cracking. To preserve its abilities, it’s suspended in a glue-like material called epoxy resin before it’s molded, forming a composite material.
Most carbon fiber used in bicycles comes in this form, which is called “pre-preg.”The resin accomplishes two tasks. First, it holds the carbon together—both the individual fibers within a ply and, once cured, the orientation of two plies to one another. Second, resin adds crucial toughness and durability. It’s slightly plastic, deforming under impact to help absorb sharp blows like a crash or a rock strike, without creating a crucial split between the fibers.
Every bike company peppers its marketing with buzzwords like high-modulus or even “ultra high-modulus.” But those terms aren’t the bike industry’s to toss around. Carbon fiber is graded by its stiffness and rated in terms of tensile modulus, or how much a material will deform under load. For carbon fiber, those ratings and the stiffness range each covers are set by the Japan Carbon Fiber Manufacturers Association (JCMA).
Most of the carbon fiber used in the cycling industry is standard modulus or intermediate modulus; on more expensive frames, higher grades do come into play. But that doesn’t sound very sexy, so often companies slip hi-mod and UHM into their copy. Some bike brands moved away from massaging the grading system altogether and simply created their carbon grading system with company-specific marketing terms like FACT or Advanced grade.
A good carbon frame uses a blend of carbon fibers of different types, each applied in different places in a frame for very specific purposes. High-modulus fiber is expensive (thanks to all that processing), so bike companies judiciously use small amounts in key areas like the downtube, bottom bracket, and chainstays to resist pedaling forces and make the bike stiffer. But the high-modulus fiber is placed in the mold along with standard- and intermediate-modulus and high-strength fiber to create a good carbon bike’s durability, performance, and ride quality.
Handbuilt bikes are most often associated with steel and titanium. But every carbon frame, wheel, handlebar, or other part made with carbon fiber sheet requires intensive hands-on work. This is true whether the frame is a custom model from a small builder like Argonaut, or a production model from Canyon or Trek.
The only automated process in the production of carbon frames is often the cutting of dozens of pieces of carbon from a sheet by a computer-controlled machine. These individual pieces of carbon must be assembled in a mold precisely according to the manufacturer’s layup schedule—it’s a process yet to be automated. In smaller facilities, one person may lay up an entire frame. In larger factories, workers create a layup for a specific portion of a frame, like a bottom bracket area, then pass the part along to other workers to lay up around tubes and place it in the final mold for curing.
Even the post-cure process—where a frame is broken out of the mold, cleaned up, and painted—requires close attention. Expert workers examine the frame or part for problems like wrinkles in the carbon, or spots where the layers aren’t smoothly compacted, which could cause a failure.
Carbon fiber is a great material for bicycle frames and parts. First, it’s stiffer at a lower weight than almost any other material. Additionally, unlike metal, carbon fiber’s stiffness can be finely manipulated. Carbon fiber’s stiffness properties apply only unidirectionally (along the long axis of the fibers themselves) so stiffness is tuned based on how the carbon fiber composite is oriented. That’s called anisotropism. Metals, by contrast, are isotropic, exhibiting the same strength and stiffness properties along any axis of the material.
Engineers use sophisticated software programs that account for the grade of carbon, the resin, the shape, size and orientation of the carbon fiber ply, and even where it’s located in the mold. That’s how frames are optimized for extreme lightness and rigidity. But those programs and the graduate-degree expertise to run them are expensive—add in the cost of the high-modulus carbon needed to realize those super light weights, and it’s why the nicest carbon fiber bikes are so much more expensive than their metallic peers.
That classic, cross-woven, carbon-fiber look is actually not much of a performance attribute. A woven layer adds some stiffness, but one of its major purposes is to add a top sheet that’s okay to ding, scratch, and dent, since most of the structural properties of the frame or part come from the unidirectional fiber underneath.
It also provides a cosmetic layer that showcases a builder's craftsmanship, since lining up the edges of a woven sheet in the mold to create a perfect seam requires significant expertise. Increasingly, though, bike and part makers are skipping a woven top layer altogether and just letting the unidirectional fiber serve as the cosmetic skin.
It’s a common misconception that a carbon-fiber frame or part is destroyed if it gets damaged. But like a steel or titanium frame, a carbon-fiber frame can sometimes be repaired. The process isn’t much different: The damaged section is cut out and then bridged with new material that’s cured, sanded, and painted to match. With the most expert carbon repairs, you may not even be able to see the affected portion.
However, this is a job for experts. There are DIY carbon-fiber repair kits, but they’re primarily intended for products like kayak paddles. Bicycle frames are complex, load-bearing structures that have to take the stress of forces like sprinting and high-speed cornering. If your carbon-fiber frame is damaged, the manufacturer may have an in-house repair process, or you can go with a reputable third party like Ruckus Composites or Calfee Design. But under no circumstances should you attempt a repair yourself.
Joe Lindsey is a longtime freelance journalist who writes about sports and outdoors, health and fitness, and science and tech, especially where the three elements in that Venn diagram overlap.
As Deputy Editor, Tara Seplavy leads Bicycling’s product test team; after having previously led product development and sourcing for multiple bike brands, run World Championship winning mountain bike teams, wrenched at renowned bicycle shops in Brooklyn, raced everything from criteriums to downhill, and ridden bikes on six different continents (landing herself in hospital emergency rooms in four countries and counting). Based in Easton, Pennsylvania, Tara spends tons of time on the road and trail testing products. A familiar face at cyclocross races, crits, and bike parks in the Mid Atlantic and New England, on weekends she can often be found racing for the New York City-based CRCA/KruisCX team. When not riding a bike, or talking about them, Tara listens to a lot of ska, punk, and emo music, and consumes too much social media.
Shop These Electric Bikes for Less Right Now
The Best Beginner Mountain Bikes
How to Fix Your Electronic Rear Derailleur
The Best Valentine’s Day Gifts for Cyclists
The 10 Best Indoor Cycling Trainers
Wahoo Kickr Core Zwift One Indoor Trainer Review
Smoother and Faster: The New Pivot Switchblade
The Best Presidents’ Day Deals on Cycling Gear
The 6 Best Garmin Watches for Cyclists
Tested: Hunt's new SUB50 Limitless Wheels
Great Time to Buy, Terrible Moment in Business
The 10 Best Mountain Bike Saddles to Buy Now
A Part of Hearst Digital Media
We may earn commission from links on this page, but we only recommend products we back.
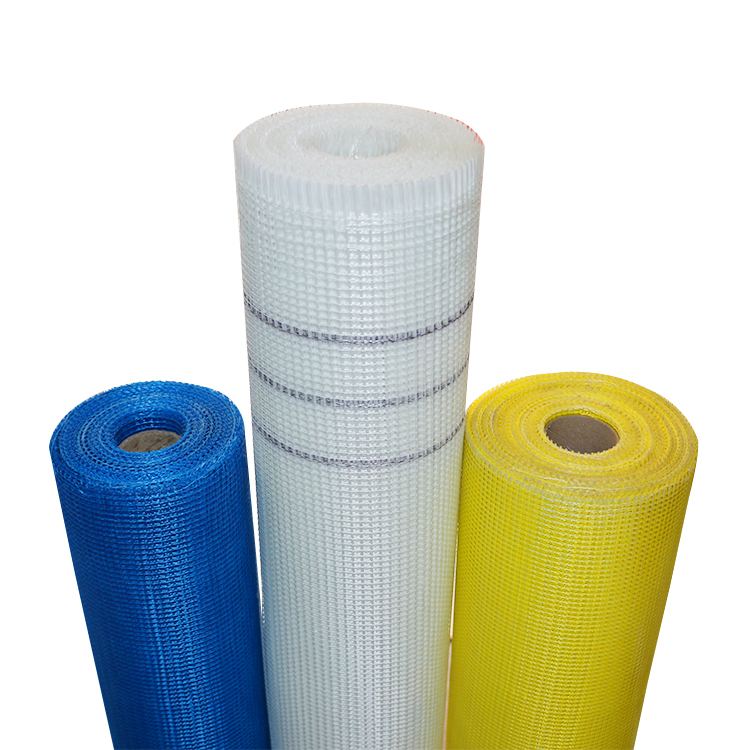
Woven Glass Fabric ©2024 Hearst Magazine Media, Inc. All Rights Reserved.