Rollon has introduced its lightweight MiniRoller Rail linear bearing. Ideal for applications that require moderate loads, it features smooth and silent operation and an adaptive design that is easy to customize and integrate into assemblies.
MiniRoller Rail eliminates the noise, difficult assembly, misalignment and unnecessary weight typically associated with using linear guides with recirculating ball bearings in lighter-duty aerospace, medical, pharma, life science and packaging applications. It also offers machine builders exceptional flexibility with a variety of optional materials, surface treatments and mounting hardware and fasteners, including both metric and inch sizes. Linear Guide Set

The new linear bearing’s induction-hardened and machined raceways reduce noise and deliver a long, reliable lifetime. It’s highly impervious to environmental contaminants that can otherwise cause early failure. MiniRoller Rail also manages misalignment so installers can minimize surface preparation time. And, thanks to end chamfers, customizable mounting holes and optional locking Helicoils — a requisite for aerospace designs — MiniRoller Rail gets up and running fast.
MiniRoller Rail is well-suited for space-constrained designs, as well as designs that require a lightweight guide such as for armrests and trays in aircraft interiors. Each unit comes in the industry-standard size 12 mini-Monorail configuration, with rail lengths up to 2 m standard or longer, if required.
For more information, visit www.rollon.com.
Browse the most current issue of Design World and back issues in an easy to use high quality format. Clip, share and download with the leading design engineering magazine today.
Top global problem solving EE forum covering Microcontrollers, DSP, Networking, Analog and Digital Design, RF, Power Electronics, PCB Routing and much more
The Engineering Exchange is a global educational networking community for engineers. Connect, share, and learn today »
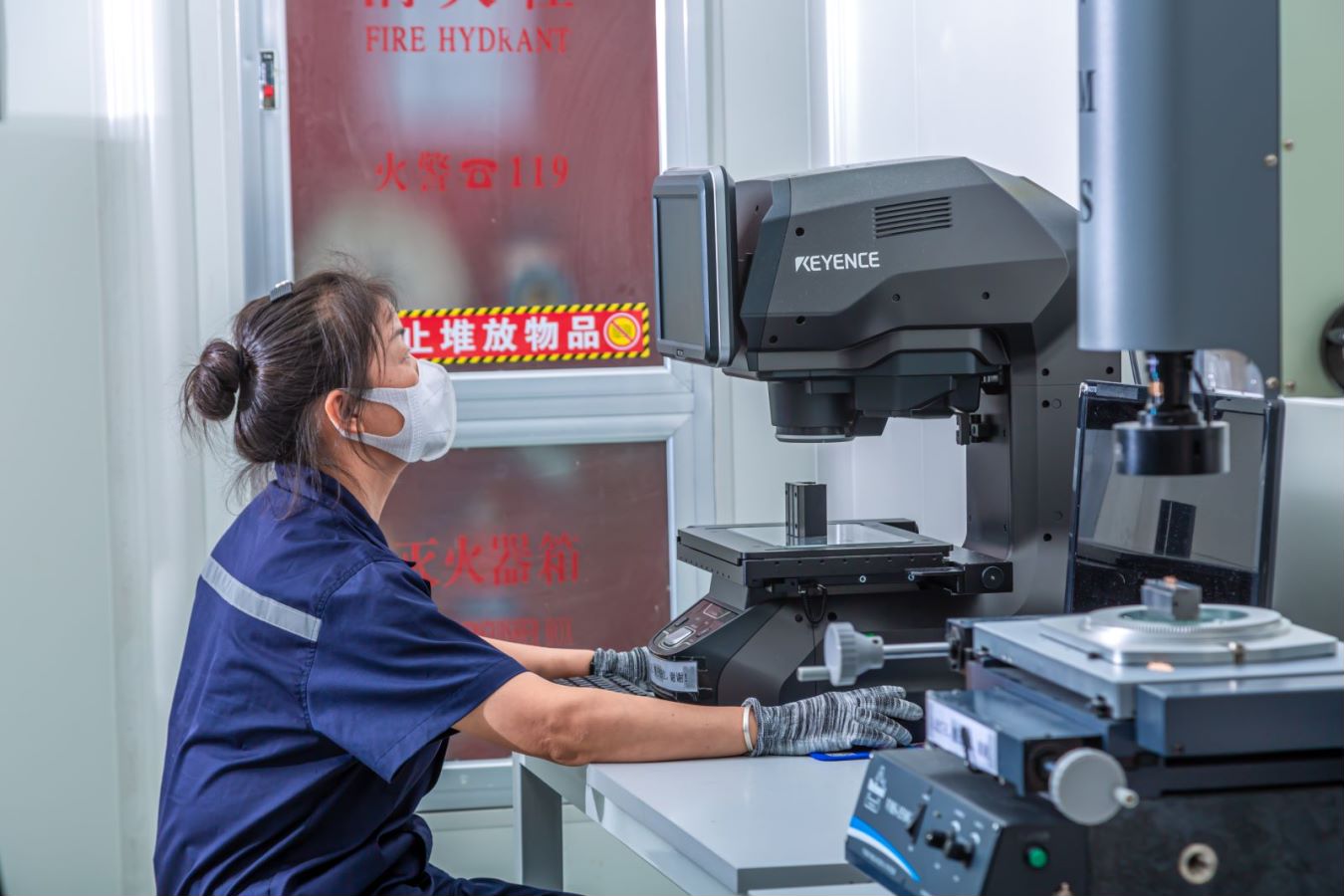
Slide Linear Guide Copyright © 2023 WTWH Media LLC. All Rights Reserved. The material on this site may not be reproduced, distributed, transmitted, cached or otherwise used, except with the prior written permission of WTWH Media Privacy Policy | Advertising | About Us