The key to troubleshooting tooling problems is in understanding the bond.
The bond is one of the most important (but often overlooked) components of diamond tooling. The tools are often categorized into a select few groupings like hard, medium or soft metal-bond, hybrid/semimetal bond, and wet or dry resin bond. In general there is not a good appreciation for the multitude of variations of the bond in each of those overly simplified category classifications. A simple root-cause-analysis of performance problems of a tool from jobsite to jobsite, or on different brand machines on the same jobsite often boil down to the bond (directly or indirectly). For many diamond tool makers the bond often represents a larger allocation of the research and development budget because there is an overabundance of variables that can be tweaked to make huge changes on the performance characteristics of the finished tool. Unfortunately the bond is usually the least understood part of the system and arguably the most important. The bond is an integral part of the complete system, and to understand the bond requires an understanding of how the other parts of the complete system influence the performance of the bond. 6 Inch Diamond Wet 3 Steps Polishing Pad
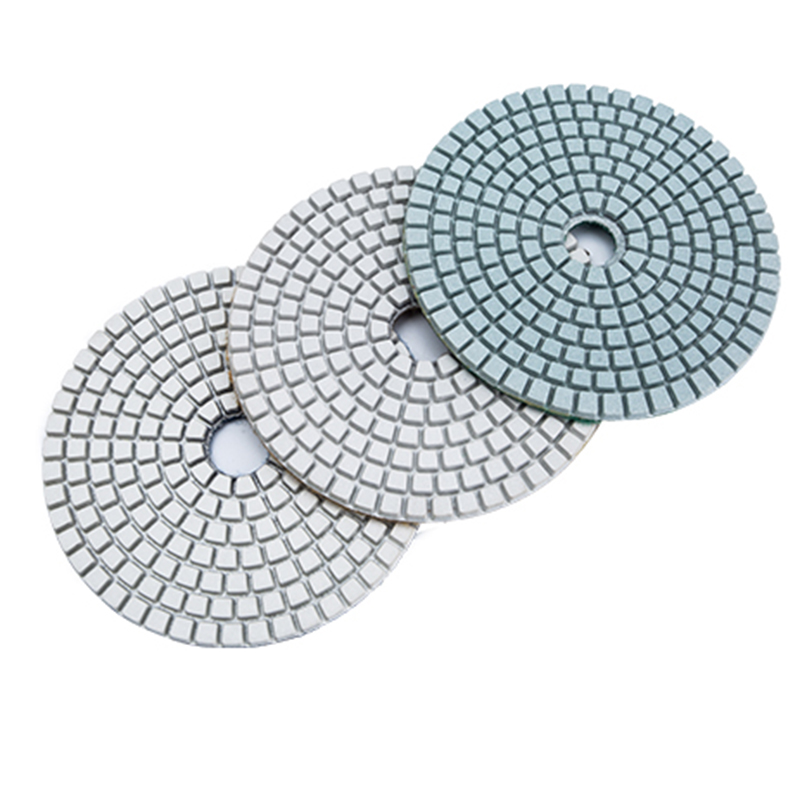
The bond is not the only component or consideration for the design of a diamond tool. In addition to the quantity and quality of the diamonds in the tool and the bond used to hold them in place, it is important for the diamond tool maker to look at the complete system, a holistic approach, to include parameters like the machine, is the grinding performed wet or dry, and the slab hardness and abrasiveness. It is almost overwhelming to consider how many things can change from jobsite to jobsite or from slab to slab that can drastically impact the performance of the diamond tooling. Fortunately in a practical sense, with the same operator using one machine bidding similar jobs (pick one: residential, commercial or big box stores) and grinding the same way either with a dry vacuum or wet, then many times the list is drastically narrowed to basically just the parameters of the diamond tool and how it matches the ‘system’ they defined. Ideally they want to optimize the performance of the diamond tool for their system, but sometimes it is easier to tweak some part of their system to optimize it for the diamond tools available to them for the machine they are using. It is also very important to know about the different tooling for the occasional job that may be very different than the jobs they usually work on.
Pairing the Diamonds with the Bond
The bond holds the diamond crystals in the diamond tool for the abrasive grinding process of the diamond to the slab surface. Grinding is a mutually abrasive process of the tool and the slab surface but with diamonds being extremely hard with respect to the slab surface, the wear rate of the tool is significantly less than the slab surface. The size of the diamond crystal can dictate the grinding speed and effectiveness in penetrating non-abrasive coatings or sealers, and progressively smaller diamond crystal sizes can remove the scratches from the previous step. For the toolmaker, it is important to create a bond based on the quality of the diamond, the size of the diamond and the abrasiveness of the slab surface, so that the bond allows diamonds to wear, fracture to expose new sharp edges, as well as to release old diamonds (pullout). If the bond is softer than an optimum bond, the bond will wear away faster and can cause more diamonds to pullout before those diamonds can wear down or fracture, causing the life of the diamond tool to be very short. If the bond is harder than an optimum bond, the bond will have an excess of diamonds that are rounded and worn out, without enough old diamonds being released and replaced with new diamonds and eventually the surface of the diamond tool will glaze over and lose its effectiveness as a grinding tool.
It is interesting to note that the term ‘diamond’ is derived from an ancient Greek word for ‘Unbreakable’. However, not all diamonds are alike. The diamond in a tool is defined by three basic parameters: the quality, the size, and the concentration. Sorting diamonds by quality is often misunderstood, these are not gem grade diamonds sorted by color, cut and clarity. The synthetic diamonds used in grinding tools are sorted and graded by the shape of the crystal and the impact strength using quantifiable metrics like a the toughness index (TI), thermal toughness index (TTI) or compressive fracture strength test (CFS). The diamonds are also sorted by physical size referred to as a mesh (or Grit) size (As the Grit size increases, the actual size of each diamond crystal decreases). The diamond concentration in the tool is a measurement of the total carat weight of the diamonds per a unit volume of the bonded tool (100CON = 72 carats/cubic inch).
Typically, diamond tool makers do not label the tools with the diamond quality or concentration. The design of the tool involves so many ingredients to achieve very strategic design goals on specific machines, that knowing just a couple of the ingredients without understanding all the variables could confuse more than clarify how it impacts the tool performance.
Bond Hardness – Soft / Medium / Hard
There is no universal hardness designation on diamond tooling, it is a relative scale. There is a big difference in the tooling used on a low horsepower lightweight class of machines versus a high horsepower heavy class machine. So for a medium bond designed for normal grinding conditions on one class machine would be completely different on a different class machine. Frequently the diamond tool makers might mark the low HP lightweight machine ‘medium’ bond tooling as a ‘general purpose’ bond to help avoid confusion.
Metal bonds are good for larger diamonds with diamond mesh sizes up to 400G (practically more likely around 200G). Resin bonded diamond tools have a much softer bond to allow the smaller diamonds to release more freely as the tool is used (up to 6500G buff pads but practically more likely 3000G).
Resin bond diamond tools can be very complicated to fully understand, but for discussion purposes it can be simplified to wet or dry resin tools. The big difference is mainly in the extreme temperatures in dry grinding can melt the resins or polymers or sometimes soften them enough so the diamonds in the bond can wiggle enough to create a socket which leads to diamond pullout. There are many techniques for the diamond tool maker in selecting a resin and using different types of coated diamonds or admixtures in the resin to create more aggressive and longer life tooling. These lead to group of diamond tools called transitionals (sometimes also referred to as hybrids or semimetals).
The data collected using a profilometer to meet the requirements of CSDA ST115 standard have been shown to also provide measurements for the performance of the diamond tooling. The grit size measures the physical size of the diamonds in the tool and do not reflect the strength of the bond which allows the diamond to protrude from the tool as a grinding point that creates a measureable scratch pattern in the slab surface.
Many times when the diamond tools are made, the top surface of the diamonds are covered with the bond. It is important to break-in (also referred to as dressing) the diamond tools to expose a layer of diamonds. Some resin tools burn a fine waffle pattern in the top surface of the tool to speed up the break-in process. Many of the metal bonded tools are dressed at the factory by the diamond tool maker. It is important to certain that new resin bond tools are properly broken-in before making a final production run.
Operator Control of the Diamond Tool
Some operators have elevated grinding and polishing concrete to very high competency levels, true craftsman at the art of polishing. It seems like they can feel the machine or hear the tooling scratching the floor and know the progress of the slab refinement. These true craftsman might have machine and diamond tooling preferences but can polish a floor using almost any polishing machine or tooling (within reason) by operator technique. This is where training and experience is so important in learning valuable skills.
Diamond tools are designed for specific slab or slab conditions in a specific class of machines based on the weight pressure forces on the diamonds (not from the overall weight of the machine but the head pressure on the tooling) and the speed of the diamonds (it becomes very complicated in calculating the speed of some planetary machines). Because of these speeds and pressures are driven by a class of machines, sometimes a tool that performs well on one class machine might not do well on a different class. It is not that it is a bad tool, but rather it is not the right tool for the machine and application.
Increasing the speed of the diamonds will act like the bond of the diamond tool is harder. For very abrasive slab surfaces a harder bond will extend the life of the tool. Decreasing the speed of the diamonds will act like the bond of the diamond tool is softer. Many stones in heavy exposed aggregate are not very abrasive and require a softer bond to prevent them from glazing. Hard or critically hard concrete surfaces would also require a softer bond to prevent glazing.
Grinding dry can create higher temperatures which can damage the diamond tooling. Using higher airflow vacuums (high CFM) can sometimes help keep the tools cooler.
Wet grinding is a great way to keep the diamonds cool but it is often misunderstood. If the volume of water is high enough to keep the slurry generated somewhat translucent then the water will act as a lubricant. If the slurry generated is a thicker paste, the slurry will act as an abrasive to help keep the diamonds open and new diamonds exposed by wearing away the bond.
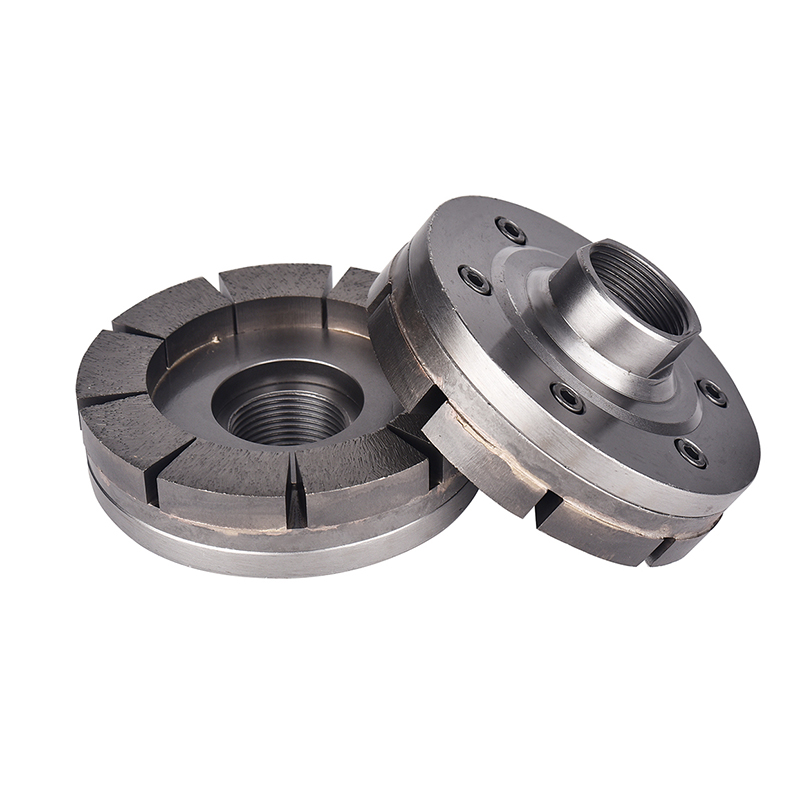
Grinding Disc True craftsman generally have a good understanding of the bond. Often times they do not always effectively articulate why something is happening, but they seem to know instinctively what they need to do to optimize the performance of the tools they have. Do not be afraid to try something new. Use the knowledge in the performance of existing tooling and techniques as metric to compare some new products or techniques to improve and grow.