06-Sep-2016 - Last updated on 07-Sep-2016 at 12:22 GMT
The depositing system can produce up to 54 kg/hr (120lbs/hr) of hard candy, lollipops, jellies, gums, caramels, fudge and fondant. Bubble Gum Polish Machine
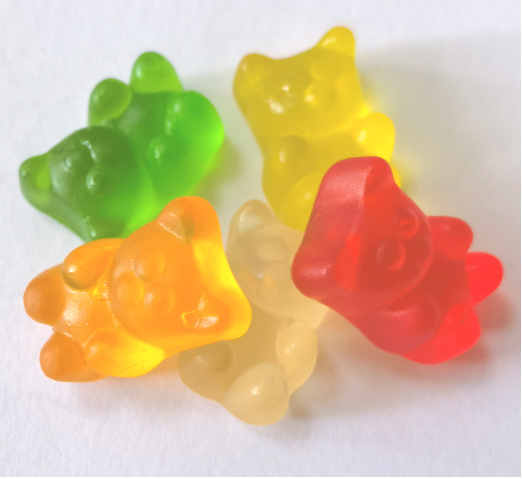
It is also ideal for medicated products such as vitamin and mineral supplements, cough candy and throat pastilles and candies that are made with sugar or sugar-free.
Keith Graham, marketing manager, Baker Perkins, told ConfectioneryNews, ServoForm Mini is a brand new development launched in June.
“There are no installations yet, but we do have an order from a customer in North America for a machine to make a medicated confectionery product,” he said.
“The company is currently making its products using a manual process and this is its first investment in automation.
“It will achieve four things for the customer: Higher output, lower labor costs, improved quality and less waste. The last is important for any confectionery manufacturer, but particularly so in the medicated sector as the active ingredient, and therefore any waste, is very expensive.”
Graham added, as well as applications in low volume production, the machine will be useful for high-volume manufacturers as a test and development machine.
“It has the ability to deposit very small batches enabling many different variants of a new product to be evaluated and it is also capable of much longer runs for test marketing purposes,” he said.
“The depositing process is identical to that used on our high-output ServoForm machines so scaling up to full production is straightforward.
“This is a new addition to our range, so there are no comparisons to be made with previous machines, all of which stay in our range. These include a lab-scale depositor suitable for very short runs as well as full size production depositors. The ServoForm mini fills the gap in between.
“We will be exhibiting it for the first time at ProSweets in January.”
Compared to conventional methods such as die forming, starch mogul or cut-and-wrap, depositing provides a smooth product with accurate weight, size and shape characteristics.
Piece weight range is 3 g to 8 g (0.1 to 0.28oz) for candies and 8 g to 30 g (0.1 to 1.05 oz) for lollipops.
54 kg/hr (120lbs/hr) translates to 10,800 pieces per hour of 5 g (0.17 oz) candies or 5,400 pieces per hour of 10 g (0.35 oz) lollipops.
Baker Perkins said the main benefits of the system are simplicity of operation, flexibility and rapid changeover times.
The control of the depositing process is fully automatic with recipe storage and recall allowing the depositor to be set up at the touch of a button.
Batch or continuous cooking may be used. Molds are loaded manually onto an indexing conveyor that is synchronized with the depositing head to ensure cooked syrup is placed accurately into the mold with no waste.
Cooling can be ambient or refrigerated, using either rack or tunnel coolers. The candies are then demolded by hand and passed to the wrapping station.
Copyright - Unless otherwise stated all contents of this web site are © 2024 - William Reed Ltd - All Rights Reserved - Full details for the use of materials on this site can be found in the Terms & Conditions
Related topics Processing & Packaging Candy Smart Technology Packaging & Packing Materials, Containers
Content provided by Fortress Technology, Inc. | 19-Feb-2024 | Product Presentation
Tackling the unique challenges faced by confectionery manufacturers, the Interceptor DF metal detector surpasses all other systems on the market in identifying...

Chocolate Bean Forming Machine Posted by Hari on October 04, 2016 - 12:28 PM |