STMicroelectronics’ AEC-Q100-qualified L99H92 gate driver is programmed through a microcontroller. Containing two high-side and two low-side drivers, the device can control a single H-bridge powering one bidirectional DC motor or two half-bridges for two unidirectional motors.
Typical applications for the driver include electric sunroof, window lifters, powered trunk, sliding doors, and seat-belt pre-tensioners. Most modern vehicles feature electric window lifters operated using buttons in door control panels. Window lifters are controlled either by body control modules, door control units, or smart motors with integrated electronics. Ethercat Servo Drive
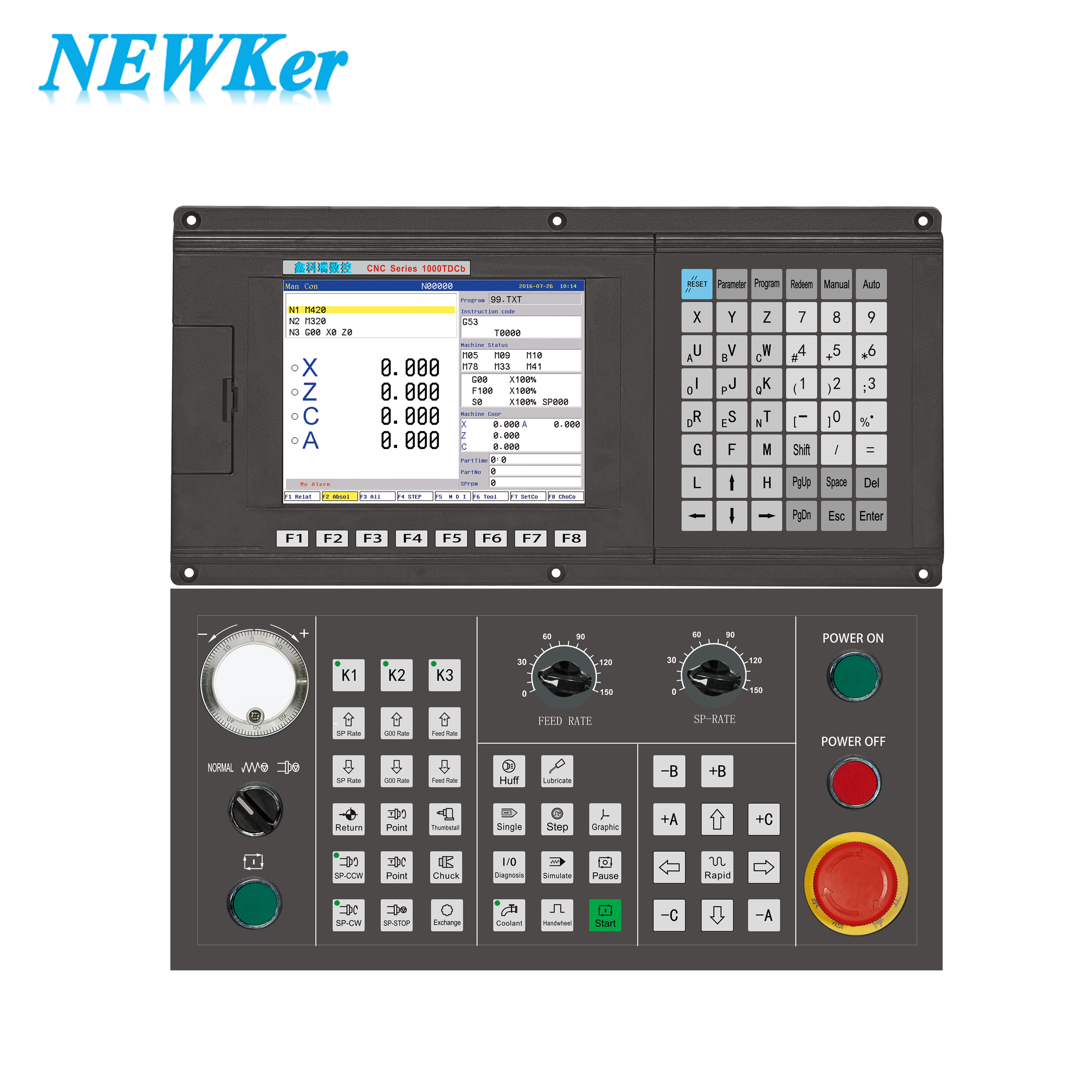
These electric window lifters are fitted with convenience functions and safety functions. For example, an antipinch safety function senses if a motor is running against an obstacle, preventing any injuries to people/objects or damage to the motor itself. Antipinch sensing is usually performed by current monitoring, Hall sensors, or a combination of both.
In the L99H92, gate-driving current is programmed through the SPI port, enabling slew-rate control to minimize electromagnetic emissions and thermal dissipation. According to STMicroelectronics, programming the current saves up to four external discrete components per MOSFET, typically needed for slew-rate setting with conventional drivers.
Maximum drive current of 170 mA gives designers the flexibility to use the driver with a wide variety of external MOSFETs, including high-power devices with large gate capacitance. The device has a low-power mode (standby mode) where the current consumption is less than 5 µA.
Programmable gate-driving current also minimizes EMI. Each gate driver independently monitors its external MOSFET drain-source voltage for fault conditions. Programmable cross-current protection time avoids concurrency of high- and low-side activation for each half bridge. Two off-state diagnostic comparators detect potential short to ground, short to battery, or open load conditions.
An integrated standard Serial Peripheral Interface (SPI) controls the device and provides diagnostic information. And an additional DIAGN output pin alerts the microcontrollers of a fault occurring into the device faster than the SPI communication.
The L99H92 device implements diagnostic and protection features such as supply voltage monitoring, charge-pump voltage monitoring, overcurrent protection, temperature warning, and overtemperature shutdown. Overcurrent protection with a programmable threshold is detected by monitoring the MOSFET drain current.
A fail-safe input can turn off all MOSFETs and a dedicated diagnostic pin provides immediate fault warning without waiting.
The L99H92 includes two additional current-sense amplifiers (CSAs) designed for current sensing in automotive applications, helping to minimize the bill of materials. Suitable for high-side, low-side, and inline sensing, the amplifiers have independently programmable gain, low offset, and low thermal drift. They can be independently disabled to reduce current consumption when not in use.
The CSAs are independent, bidirectional, single-supply differential amplifiers with a wide input common-mode voltage range. The working principle of a CSA is based on Ohm's law. When load current flows through a shunt resistor present on inputs, it generates a voltage drop called VSENSE. This voltage is generally small to limit power dissipation losses.
A charge pump powers the high-side drivers to maintain correct operation as the vehicle battery voltage fluctuates, enabling the outputs to function with a supply as low as 5.41 V. The charge-pump output is also available at an external pin to control a MOSFET for reverse-battery protection.
To help developers reduce design time and costs, a ready-to-use L99H92 evaluation board (AEK-MOT-WINH92) is available. Part of ST’s AutoDevkit ecosystem, it includes useful developer resources on how to configure the L99H92 to drive a full H-bridge configuration or a dual unidirectional half-bridge configuration for driving DC motors with a variable PWM duty-cycle signal.
The board’s key objective is to drive a DC motor for car window lifters, ensuring high safety levels. The board can be connected to any microcontroller, exploiting separate and dedicated connectors for SPI communication, current sensing, and a basic motor commands interface with fault-detection capabilities.
In its literature, STMicroelectronics includes the following warning: The AEK-MOT-WINH92 evaluation board is not to be used in a vehicle, as it’s designed for R&D laboratory use only.
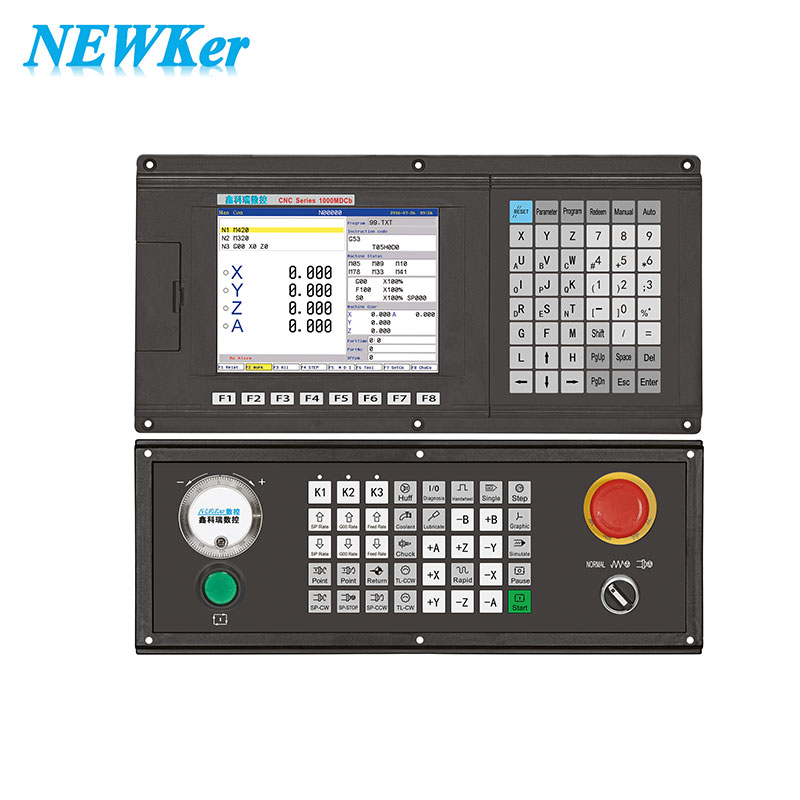
Robotic Arm The devices are housed in TQFP32 and QFN32 packages, both with exposed pads. The QFN32 has wettable flanks for easy visual inspection of the solder joint. The L99H92 is in production now. Pricing starts from $1.7062 in the QFN32 package and $1.7246 in a TQFP32 package, for orders of 1,000 pieces.