Home » Topics » Energy Management & Lighting » LED Linear Module Retrofit Kit Upgrade
Espen Technology improves performance of VersaLinear™ with more lumens for certain modules Aluminium Extrusion Industries
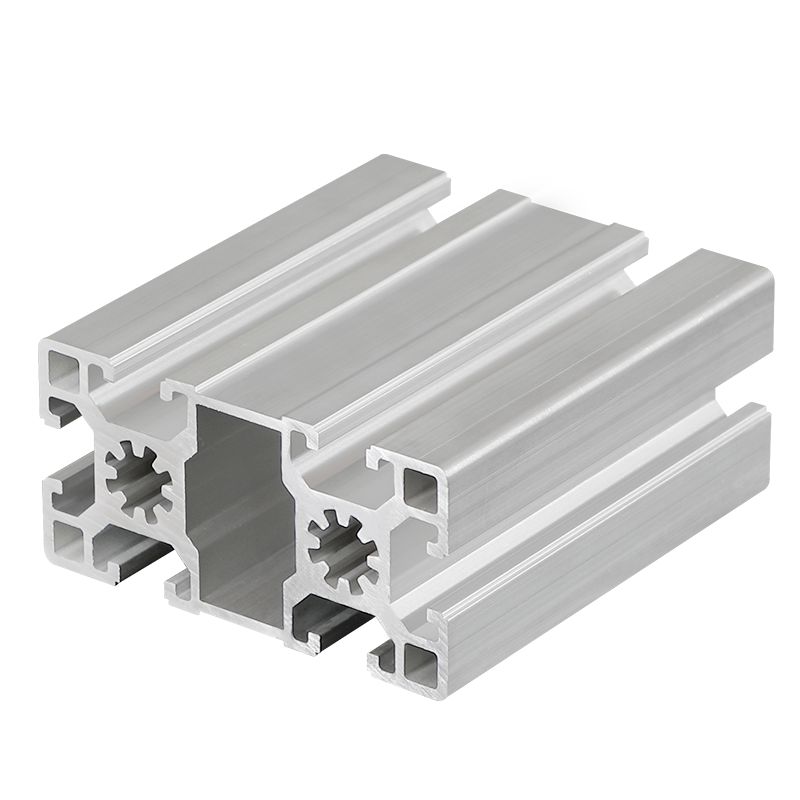
Espen Technology announced a major performance improvement for its LED Linear Module Retrofit Kit family, known as VersaLinear. The linear module kits come in 2′, 3′, and 4′ lengths, suitable to replace both T5 and T8 lamps. There are several one, two, three, and four module / driver combinations. Additionally, the 4′ versions also come in HO (high output) and VHO (very high output) models. Each kit includes LED modules paired with a field-adjustable output LED driver. The recent performance upgrades now give the 4′, four module kits, with no lens, up to 9,250 lumens for the kit, while other configurations attain system efficacies as high as 145 lm/W.
Each LED Linear Module Retrofit Kit is available either with a frosted diffuser lens or without the diffuser. All of the kits are designed to achieve high lumen output from end-to-end, without any dark spots. VersaLinear features a durable aluminum frame containing magnets for easy installation, and eliminates the need for lamp sockets. The LED drivers are field-adjustable, and three different constant current settings—360mA, 300mA, or 250mA—can be selected to create a field-adjustable light output level. For additional control, the driver can be connected to a 0-10V dimmer.
The VersaLinear kits are universal voltage (120-277VAC) with an 84 CRI, 50,000 hour life, and a five year system warranty.
Facility Executive is your one-stop source for information on quality operation, design and maintenance of facilities. Facility Executive offers a shared community of facility management experts who explore and analyze issues that affect your facility and its environment.
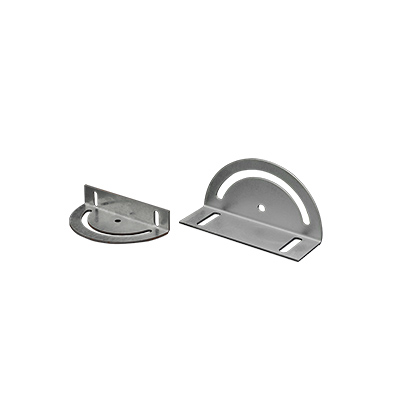
Aluminum Triangle Extrusion Facility Executive is a specialized trade publication written and edited for corporate facility executives in all industry and service sectors whose responsibilities include purchasing, planning and approving products, services and materials for facility operations.