For many years people have conceived and built mechanical devices to make the job of spray foam and coatings faster, safer, easier and better. Among the many devices created are the new and old robotic applicator machines. These are mechanical assisting devices for the independent Contractor and in plant OEM manufacturing Companies. Over the years the equipment has evolved to become a reliable everyday working tool and in many cases the ultimate necessity. It has not been easy and has taken some time to get to where it is today. With trial, error and a great deal of unique thinking it has started to come together. But even today, it is still evolving, and the perfect machine has not yet been built. So until that time comes we must work with and adapt to the current mechanisms and climb over the hurdles of change from a person spraying to entrusting a machine to do the job right. Not many people like change and the consequences of what trial and error means with new gadgetry, and not to mention the cost of the equipment. In recent years success has been far greater with some mechanical devices than others. What has generally driven the development and sophistication of machines has been two basic things, (Market demand and Capitalism). These concepts offer financial as well as other beneficial rewards to the manufacturer, contractor and the ultimate consumer. It is the opportunity to use ingenuity, imagination and skill to challenge and change the way things are currently done and create something new and more useful where the consumer is usually more satisfied. In other words, it works, it makes company money, and the customers are happy. With the evolution of new electronics, design of materials, and good old fashion know-how there have been a flurry of mechanical assisting spray machines called robots introduced in recent years. There have been no less than three robotic spray foam and coating machines built and patented within the last 10 years. Of these, several have been reasonably successful. But why have the thousands of contractors, manufacturers of products and other industries resisted this type of equipment? The answers are numerous and interesting. The best answers for most people are that robots have not proven to be the useful tool that they were thought to be at the time when they were introduced. With great fan-fair each time they have promised to be the ultimate solution when in many cases have turned into the ultimate question mark. But is this the fault of the designer, contractor or operator? Robots have generally been built for only a small specific segment of the spray foam industry and are not as easily converted to be utilized with other spray on manufactured products. They can only be used on large roofs with few penetrations which is one example of how they are narrowly categorized. This leaves out many smaller roofs where the majority of spray on systems takes place. One machine was built to install spray foam and could only use one particular spray gun. With about a dozen different hand-held spray guns and several machine mounted devices for spraying foam, polyurea or coating, how many of these are actually suited for this type of automation? Most people agree that they would seriously consider using a robot if it were easy to set up and operate, installed good looking spray foam/ spray coatings and actually helped them to make money. Part of the problem with machines may be the high expectations of what we perceive a machine to be able to do for us and the immediate results envisioned. Some expectations are that when the robot shows up all of your problems will vanish and the machine will make magic and know what to do. Even then most modern robots do not make the spray foam material, coating, paint or polyurea better. It does not monitor or correct the travel direction or make decisions about the spray gun, spray pattern or product temperature settings. It basically holds and moves the spray gun, drives away from the applied product and has a trigger switch to turn on and off the spray gun. A few spray foam robots have advanced to the point of being able to produce slope by gradually slowing down the travel speed of the unit while the volume output remains constant causing thickness to increase using a PLC electronic control unit. This however is not so important when all we need is for the outcome to be smooth with uniform thickness at least 90% of the time. Some good things about robots are that they hold the supply hose and allow the applicator a free hand to monitor and inspect the material being installed. They carry a wind screen attachment for reduced overspray, don’t get tired, and show up for work every day. Most robotic units do require some degree of daily maintenance. So, it goes where we steer it and produces what we set it up to produce from the foam or coating supply pumping machine that is controlled by you the applicators. If you speak to a contractor that has been successful using one of these machines, what do you think the response might be? The answers might surprise you. In spite of the learning curve, occasional setback, repairs and assorted other things that happen at times, perseverance and commitment is what pays off. Just like with any other equipment item used today. Those who realize that it takes these measures in the beginning are the ones that are succeeding with mechanical robotic technology. There are many applicators convinced that they can install products faster than a machine and besides machines can’t work at the edge of a roof or around penetrations, that robots are only good for large wide open roofs. These opinions are also valid and mostly true. But given the advancement in reduced size and turning rate, small roofs and small sections are made easy to do these days with robots. There are plenty of times that it is not practical to use these machines and sometimes a human can go faster and better than a machine. But to think that this type of automation is not good and won’t work for you is being blind toward what the future has in store for us all. Eventually all things change and improve by invention otherwise we would still be working with the same equipment that our grandfathers used. And ask yourself, did you know everything about your spray machines and other equipment the first time that you used them? I think not. The object for using one of these modern machines is clear.
With current prices ranging from $16,000.00 to $20,000.00 for robotic machinery they have become much more affordable than when first introduced. Some of the Contractors have reported saving substantial amounts of money on their first projects and are able to pay for the equipment within a job or two or a few months. Each individuals experience will be different when learning to operate these new and evolving mechanisms, but with perseverance, the end results could be a robotic payday. Biography of the writer Jim Davidson began working with spray foam, coatings and paint in the mid 1960’s with his father and developed a passion for the mechanics of equipment and ingenuity of being a self employed Contractor. Jim is known for the numerous quality awards in roofing that he has achieved over the years. In the late 1990’s he become one of the first spray foam instructors in the nation through the Polyurethane Roof Training Center. Jim is currently providing equipment, on-site training and his own brand of robotic application machines from his shop in Ohio and his Company, SprayWorks Equipment Group, LLC. He is currently working on many new and exciting inventions that will benefit much of the spray-on industries. www.sprayworksequipment.com Small Spray Foam Machine
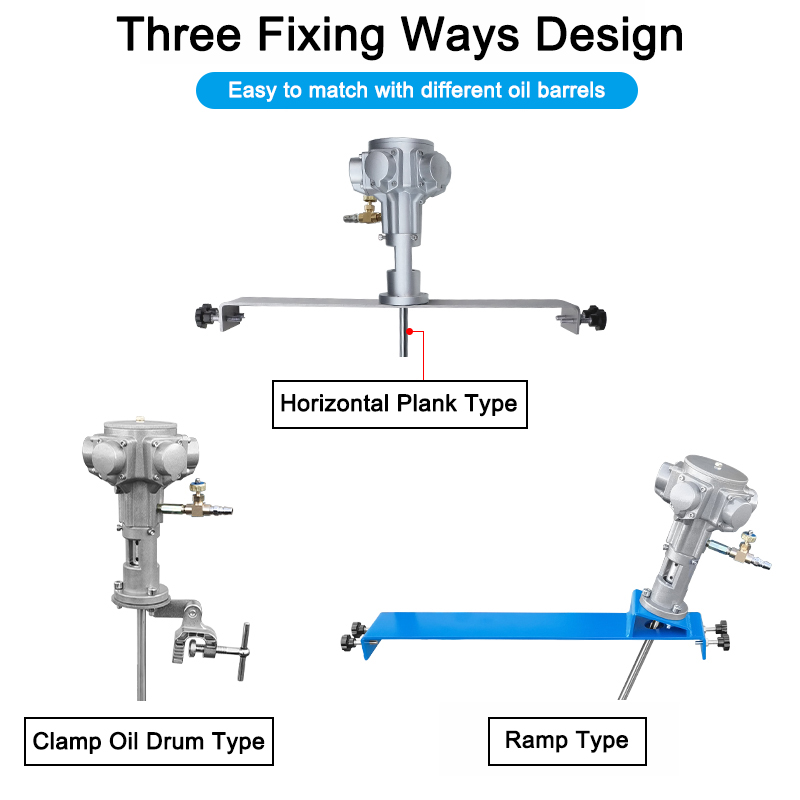
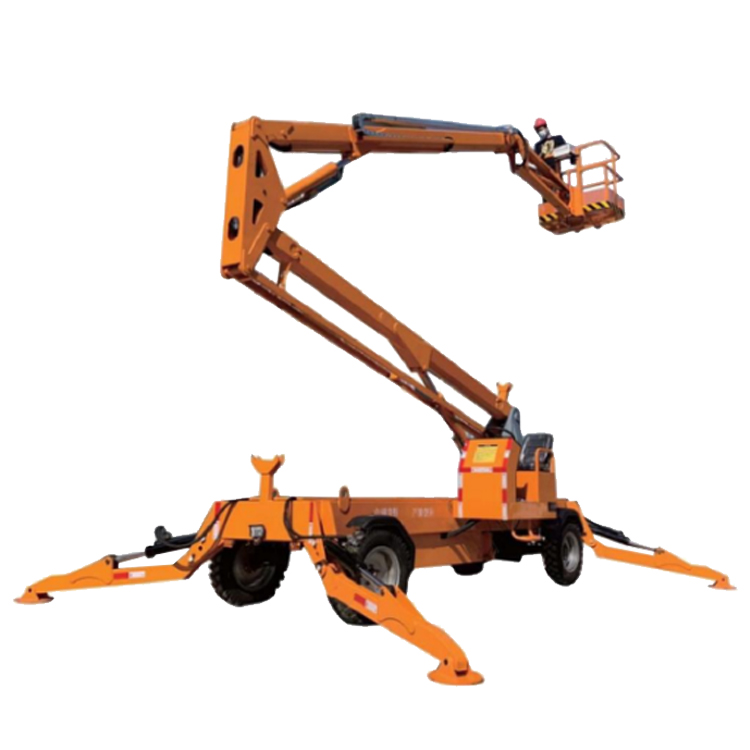
Polyurethane Floor Mats Disqus website name not provided.