Enable Manufacturing/ Continental Engineering Services
A premium automotive manufacturer has worked with Continental Engineering Services and Enable Manufacturing to additively cast an electronics cold plate set to be installed this year. Gravity Sand Casting
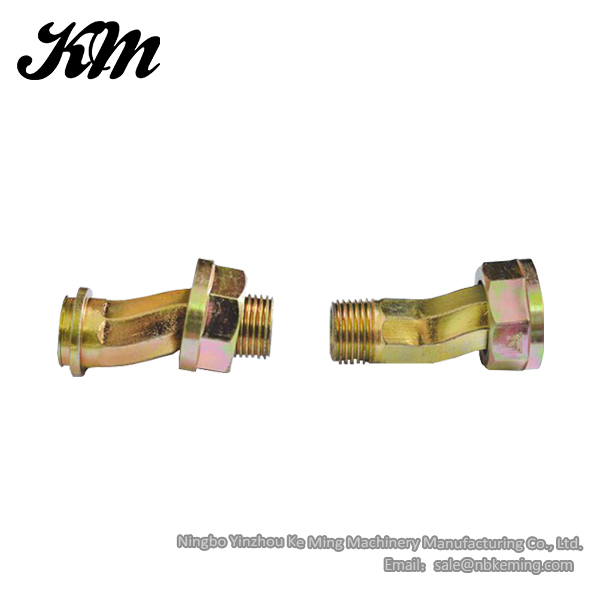
The cold-plate is considered to be a key enabling part of the compact electric motor designed by Continental Engineering Services on behalf of its premium Automotive OEM client, whose key attributes are ‘packaging size and minimising mass.’
Conventionally, the electronics cold plate would be made up of two components brazed together, but in 2022 Enable Manufacturing successfully prototyped two additively manufactured variants of the product and expect it to be on the road by Q1 2024.
Designed by the team at Continental Engineering Services, Enable Manufacturing decided to leverage an additive casting process to develop the component instead of a conventional technique and Direct Metal Laser Sintering. Though these parts can be manufactured with both of those processes, Additive Casting was deemed to be the method that would return the best results on cost and quality. Additive Casting would also allow the partners to implement an organic artery topology onto the part.
"From the outset, it was always planned to be a metal 3D printed part,," Enable Manufacturing Sales Director Phil Kilburn told TCT, "but I think they were struggling to get the cavity in the design criteria that they wanted, they were struggling to get quality that they wanted, and they're struggling to get approval, how do they qualify an additive piece?"
Continental Engineering Services solves technical and engineering challenges within the automotive and industrial sectors, utilising a service portfolio that includes development, product supply, integration and consulting. Its core competencies include Driver Assistance, Interior Electronic Functions, Driveline & Electrification, and Brake Systems.
Enable Manufacturing is a metal 3D printing service provider, offering a ‘full market solution’ for the production of printed technical parts.
In the development and manufacture of the electronics cold plate, a traditional OEM + Tier 1 + Tier 2 supply chain was being relied on. Together, the OEM and suppliers had recognised the opportunity to take advantage of several potential benefits through the utilisation of additive manufacturing. First, there was the prospect of consolidating two parts into one, but then there was also the ability to leverage nTop and Gen3D software to apply a patent-pending organic artery topology that would enable more optimal flow paths and reduce wall thicknesses. Conformal cooling and a water jacket were implemented into the design of the part to help keep the electronics thermally separated from the electric motor and at a consistent temperature.
"With electric vehicles, they're too heavy and everybody's trying to lightweight them," added kilburn. "Most normal castings for an aluminium part, [have] a wall thickness requirement of four millimetres, we can get that to sub two millimetres. That's the motivation, getting the weight down. The secondary motivation was to enable us to cast parts that already were designed with thinner walls."
Get your FREE print subscription to TCT Magazine.
Exhibit at the UK's definitive and most influential 3D printing and additive manufacturing event, TCT 3Sixty .
Binder jet 3D printing technology was used to print complex moulds in furan-silica with a 140μm particle size. The particle size was important not only to ensure the required detail was achieved, but also to land on the correct porosity for outgassing during the casting process. Carabead-phenolic was used to produce a water jacket core, which was very thin and thus needed a stronger material than silica-furan. During the casting step, Aluminium LM25-TF (AlSi7Mg) was used. Since this is a widely used grade in automotive, no special approvals or testing was needed.
Measured against DMLS, the additive cast electronic cold plate components were said to:
The collaborators worked on the development of this additive casting process for nine months before receiving series production approval. Up to 750 units of the additively cast piece had been ordered, with the expectation that they be installed in cars by Q3 of 2023.
Enable Manufacturing and Continental Engineering Services believe this project has proved out Additive Casting’s capacity for the serial production of parts in demanding industries, especially when the components have been designed specifically for the process. By virtue of using an additive casting technique to manufacture the components, the partners estimate that 7kg of embedded carbon are removed since it removes powder atomisation from the process chain. The implementation of the patent-pending organic artery topology then supplements this by removing weight. By reducing the wall thickness down to 2mm, the topology saved an additional 15% weight compared to the original design.
The use of additive manufacturing technology also allowed the companies to consolidate the components, which has a positive impact on the performance of the parts, since there is less risk of leakage than with the originally brazed parts. Having previously tried DMLS to replace the conventionally made parts, Enable and Continental not only managed to remove weight and save on C02 emissions, but they also reported a 50% cost saving vs DMLS. The removal of brazing has also reduced manufacturing scrap.
As the first application of Enable’s patent-pending surface technology, interest has since been piqued in the space and arts industries, while Continental Engineering Services are said to be exploring two additional applications of Additive Casting and the artery topology technology.
"I think [Additive Casting] will help with supply chain issues and help with just providing more complex, high performance components," Kilburn said. "That's one of the differences, I think. Direct metal printing is great, if you want a F1 a car or if you're making a plane where the numbers are so low but performance is so critical. DMLS can be a good solution. But when you want to make 10,000, 100,000 cars, it is Additive Casting. We shown it on an electric motor housing, the break even point against traditional manufacturing is 130,000 units per year. You can get there. So, hopefully, it will help with all that reshoring and supply chain work that needs to be done in the coming years."
Part of Rapid News Group
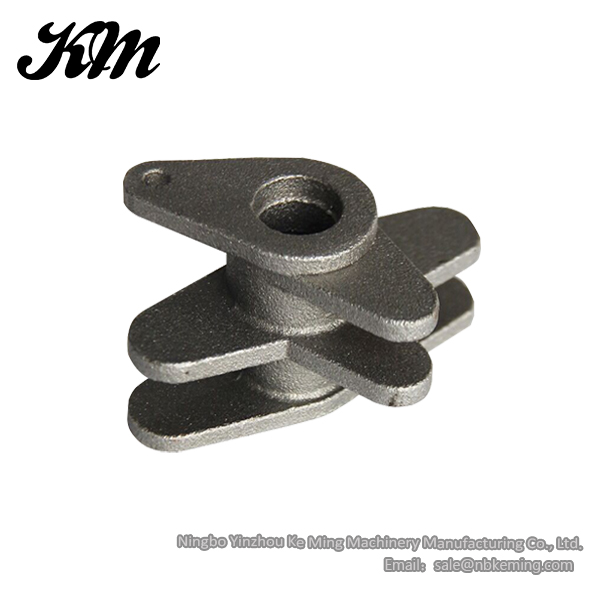
Gray Iron Sand Casting © Rapid News Publications Ltd. A Rapid News Group Company. All Rights Reserved