Swiss geothermal drilling company HammerDrum has reported the first successful deployment of their innovative, fully automated drilling robot.
Innovative drilling company HammerDrum AG has reported the first successful deployment of the world’s first fully automated drilling robot. Although drilling was only done for about 20 meters depth, this is a significant milestone as the company continues to work on the technology to target deep drilling between 500 to 3000 meters. Turning Tool
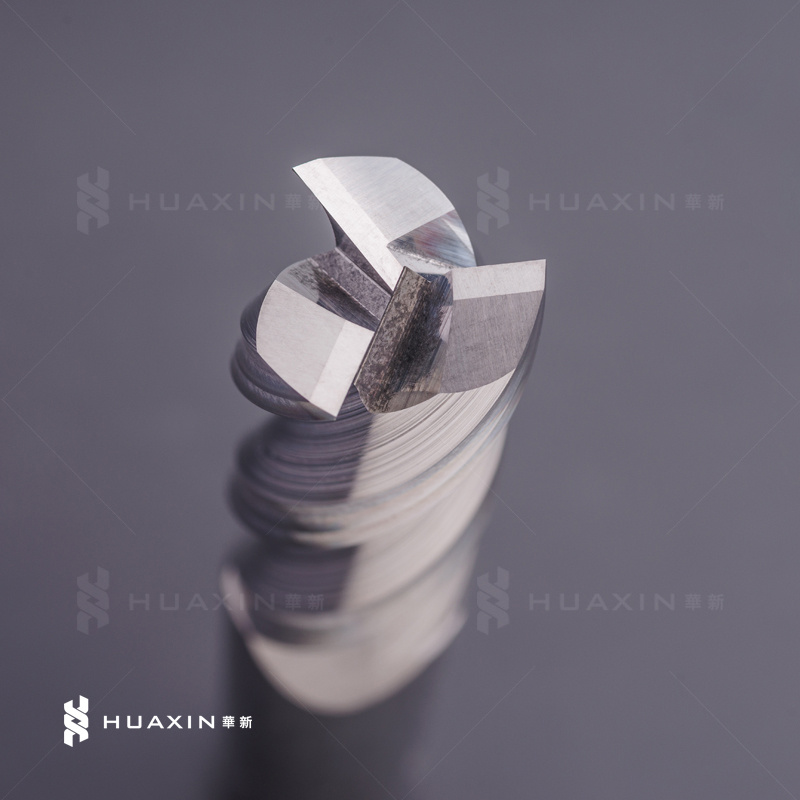
Through the use of a novel, fully automated drilling method, HammerDrum aims to make deep drilling less expensive and at a smaller footprint. “With conventional technologies, deep drilling is often too expensive and requires large construction sites, making it impractical, especially in urban areas. Our drilling robot will provide a solution by enabling deep drilling in small spaces and at a fraction of the cost,” explains Oliver Rau, co-founder of HammerDrum.
The field deployment of the technology comes after twelve month of intensive field testing of each component of the robot. “Brake it till you make it,” laughs Duarte Santos, a former simulation engineer at CERN and co-founder of HammerDrum AG.
In contrast to existing drilling methods, the HammerDrum drilling machine is situated within the borehole, comparable to a vertical tunnel boring machine.
The machine is lowered into a borehole using a steel cable and anchors itself to the walls using a hydraulic gripper system. The drill cuts a predefined distance (between 1 and 3 meters) in each drilling interval. The cuttings are then collected directly in the machine and returned to the surface with the machine at the end of each interval.
On the surface, the machine is emptied and prepared for the next drilling batch. To avoid downtime, a second machine can be deployed immediately. This process is then repeated until the desired depth is reached.
To navigate the challenging subterranean environment, the drilling machine is equipped with an array of sensors designed to facilitate precise control of the drilling process. These sensors continuously collect data from both the machine’s internal components and its immediate surroundings.
The gathered data is transmitted in real-time to the surface through the steel cable, providing on-site personnel with immediate access to information regarding the equipment’s performance during each drilling interval.
Similar to the autonomous systems utilized in modern aircrafts, the machine can operate in automatic mode under ideal conditions. However, the sensor suite remains vigilant, capable of detecting any abnormal conditions. In the event that an anomaly is detected, the system promptly generates a warning signal, allowing surface personnel to respond appropriately.
Placing the drilling machine in the borehole significantly reduces the site size on the surface, allowing for deep drilling even in densely developed urban areas. The batch drilling model also facilitates this, as drilled material is collected directly on the machine and does not require flushing basins or compressors.
Finally, the highly automated process reduces the workforce needed to operate the drilling machine to just two people.
With the field deployment of HammerDrum, the drilling machine would have completed the Proof of Technology phase of development. It would already be possible to drill deeper, but as a start-up HammerDrum cannot yet afford to lose a machine in the ground. Until all the tests are complete, the company will only go as deep as it can recover the drill manually.

Countersinks “From here, it’s all downhill – into the depths,” concludes Santos.