As the US-based company launches its “adaptive airflow” solution for cleanrooms, CEO Dan Diehl talks about how the team developed the solution and what the response has been in an era pushing for decarbonisation
Dynamic cleanroom control is a game-changer for many highly regulated industries. Providing a cost saving, whilst simultaneously decarbonising the facility’s operations. It’s a win-win on all sides. Temperature and humidity control
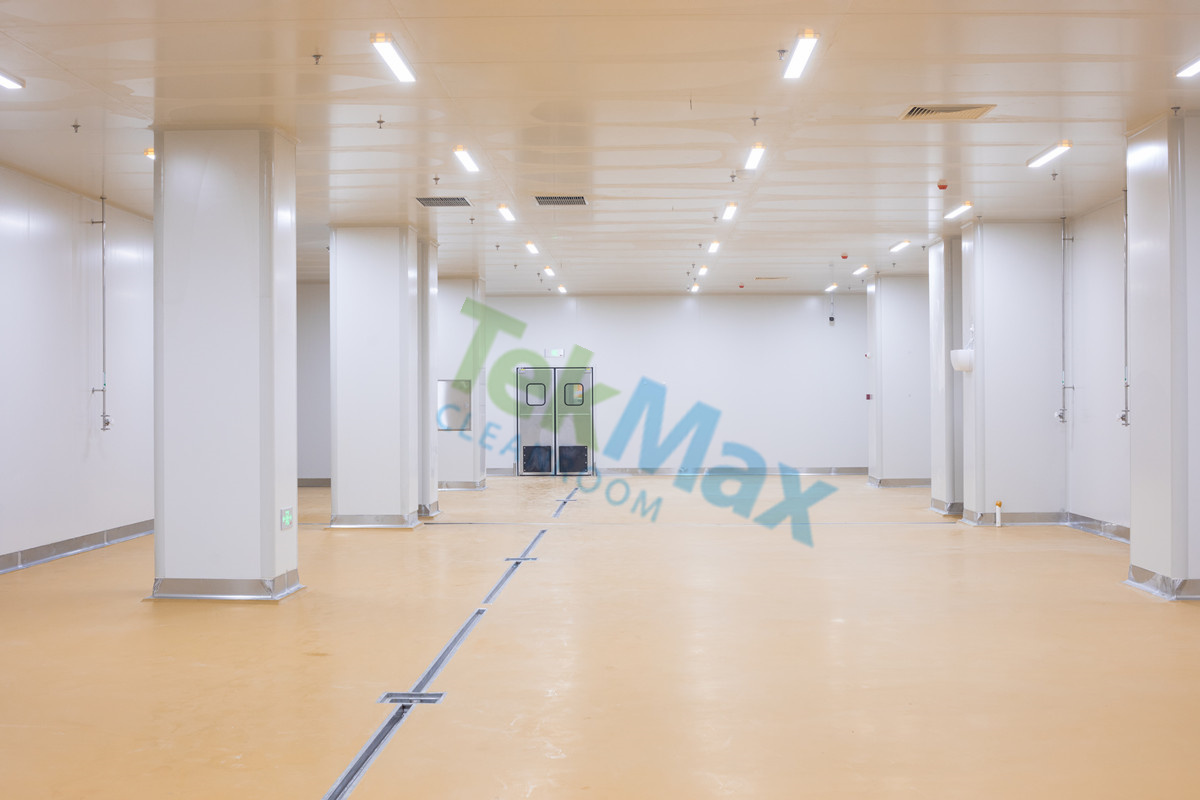
In October 2023, it hit headlines that ventilation and decarbonising specialist, Aircuity, was launching an "adaptive airflow" application for ISO Class 7 and 8 cleanrooms.
This major news for the industry came from a company that had been investigating real-time energy management for over two decades.
CEO of this US-based company is Dan Diehl, a trained mechanical engineer who has now been heading up Aircuity for 15 years.
Sitting down with Cleanroom Technology, Diehl was keen to talk about how the company turned its solution, previously used for labs and vivariums, into one that would work for cleanrooms.
Diehl’s first introduction to cleanrooms came during his time working for HVAC expert Johnson Controls, liaising with many of the larger life sciences firms. “I had a lot of experience back then in most all the various life sciences facility types and their unique requirements,” he explains.
Diehl then spent time at sustainable built environment expert Lutron Electronics. “I often look to lessons learned from both of those great companies; mostly centred around scaling with quality.
The seasoned executive in the building controls and energy efficiency space then took this expertise to Aircuity as a VP and then CEO.
Cleanrooms are the most energy-intensive spaces in the built environment.
Much of this energy is from maintaining air cleanliness levels. Aircuity’s new system’s ability to reduce carbon emissions is “dramatic” the CEO explains. “The return on investment (ROI) will be well under 3 years. In markets with higher utility rates the ROI may be closer to 1–2 years,” he enthuses.
The way this “adaptive airflow” solution works is through a real-time response setup to contamination levels in a cleanroom. “You want to provide more ventilation where and when needed versus just prescriptively applying a set ventilation rate that will be wasting energy & carbon most of the time,” Diehl explains. “In addition, clients are also able to get real-time data and insight versus measurements from periodic ‘spot checking’.”
Aircuity did not begin with cleanrooms, in fact, the company has been working on this technology for a long time. “Our founder Gordon Sharp was championing the vision over a decade ago and did a ton of work to understand and develop this solution,” Diehl says. “[Now] Aircuity does business in nearly 20 countries around the globe and we are able to support our life science clients globally.”
The solution has grown from other markets as Aircuity explores and develops the possibilities with the concept. “[The ‘adaptive airflow’ solution for cleanrooms] is a very natural extension of what we are already doing successfully with our clients across their labs and vivarium spaces,” Diehl shares. “We are taking the many learnings and decades of experience in monitoring and controlling ventilation in these other critical environments and unlike other ‘sensing’ only companies we focus both on the accuracy of the solution over the life of the application AND integrating then controlling the ventilation systems. In this way, we provide a complete end-to-end solution – design through commissioning.”
The adaptive airflow route has been proven to be successful in almost the same manner as labs and vivariums, as well as ORs, Diehl explains. Cleanrooms are a slightly different ball game though.
Diehl further explains that this is because the “requirements” deliverables are different for cleanrooms.
However, as they are well-documented, Aircuity just needed to ensure that the environment met and maintained the required specifications for IAQ (Indoor air quality). “We work with each client to ‘customise’ the solution for their specification, and desired results and therefore understand each client may want slightly different control schemes,” he elaborates.
“While our core system didn’t change all that much we did need to make sure the overall solution would deliver the results,” Diehl says. “Because it is somewhat customisable, we didn’t have to solve to one result; so we were able to maintain flexibility in things like the number of sensed locations, where to monitor, etc.”
This new solution is one thing to do for a new build, but what about retrofits? This is something that Aircuity are keen to work on with clients.
“We expect to be able to install our system outside of the cleanroom itself so there is very minimal if any disruption. Activating control can be done after the collection of data and can also be done in stages so really this should not be seen as a disruptive solution. Many clients might want to go through validation etc. while it is out of operation but that should be a very short time relatively speaking.”
We expect to be able to install our system outside of the cleanroom itself so there is very minimal if any disruption
The life science sector is a big focus for this new solution, being an industry with a lot of ISO Class 7 and 8 environments. “For each project, we need to ensure our platform can meet the ISO classification requirements when integrated into the existing HVAC system. The control system in these facilities is typically more sophisticated (which means easier to customise), so in some ways, there are fewer difficulties compared to a lab or vivarium project.”
So whether in this new cleanroom application, in retrofit projects, or for varying cleanroom levels, Diehl is confident in the new offering. “We firmly believe in the feasibility of this approach and genuinely value collaborating with these forward-thinking, top-tier organisations,” he says.
At the forefront of importance for Diehl and his team is protecting the planet, whilst helping clients meet their goals.
“It is important to note the impact this will have for natural gas mitigation in places like Europe and in parts of the world where energy rates continue to climb and/or where clients are trying to achieve net zero through very expensive clean energy,” he says. "We must tackle these more complex applications to meet what is required for our clients’ goals and our planet.”
We’ve had a ton of interest and requests to begin looking at potential projects
Talking about how the launch has gone, Diehl seems to be extremely happy with the results. “We’ve had a ton of interest and requests to begin looking at potential projects,” he enthuses. “Based on our experience we expect this to be an evolution and for clients to begin with testing and validation initially before broadly adopting to all of their applicable spaces.”
He goes on to explain that he knows that there will be unique designs and systems to control so no two projects will be exactly the same. “This is very similar across all our other applications (like labs and vivariums). It is what also makes us unique – we are NOT just providing the platform and saying good luck…we work with our clients from design through installation and commissioning to ensure the end results are delivered.”
This technology is one that is crucial to making the life science sector more sustainable and it cannot be understated how important that is. “We're thrilled that our clients persist in thinking innovatively (not merely outside the box as it truly isn’t),” Diehl says. “However, commitment to realising savings and benefits is crucial, followed by investing time and effort to achieve them.”
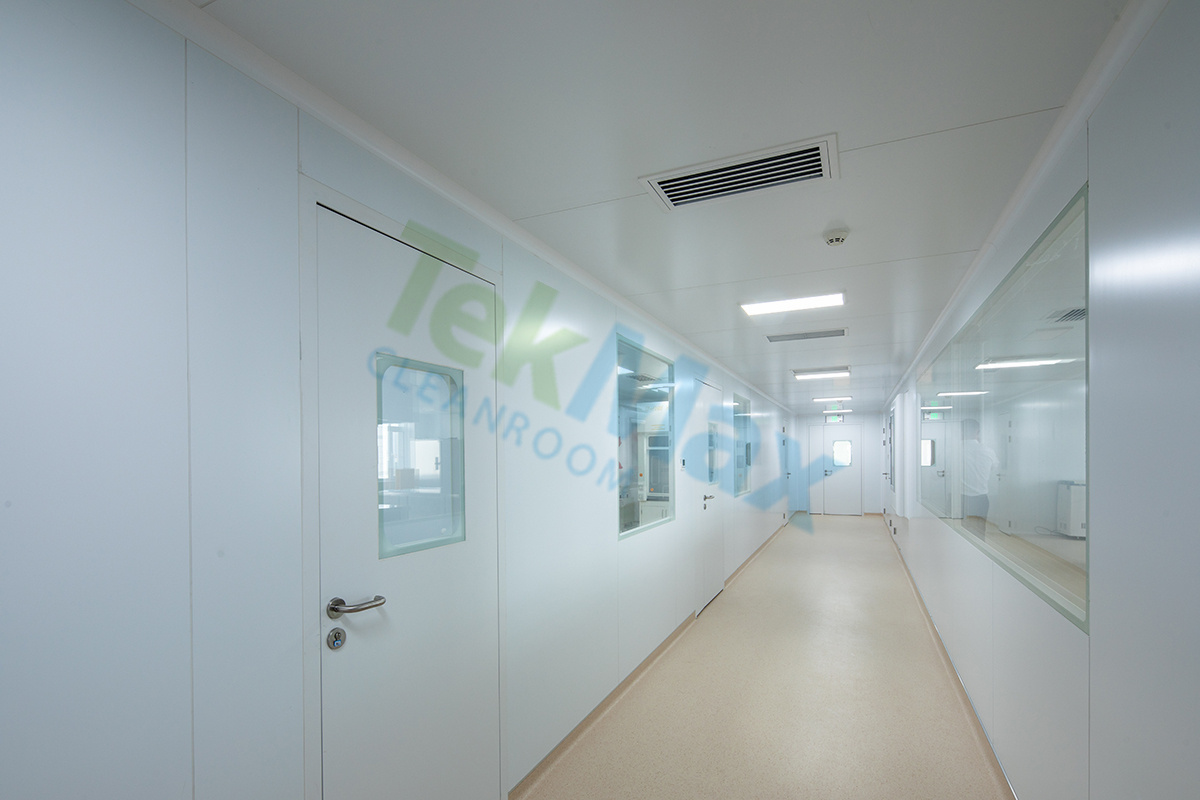
Clean color steel plate Though Aircuity is based in Massachusetts, this is an innovation designed for the entire international industry. “A large portion of the market is international so while we will start here in the US, we fully expect to follow our clients to wherever their biggest opportunities exist.”