Please refresh the page or navigate to another page on the site to be automatically logged in Please refresh your browser to be logged in
The student driver and her instructor Gisela Chevalier survived the 168-car Louisiana pileup on Monday that killed eight people Salt Fog Chamber
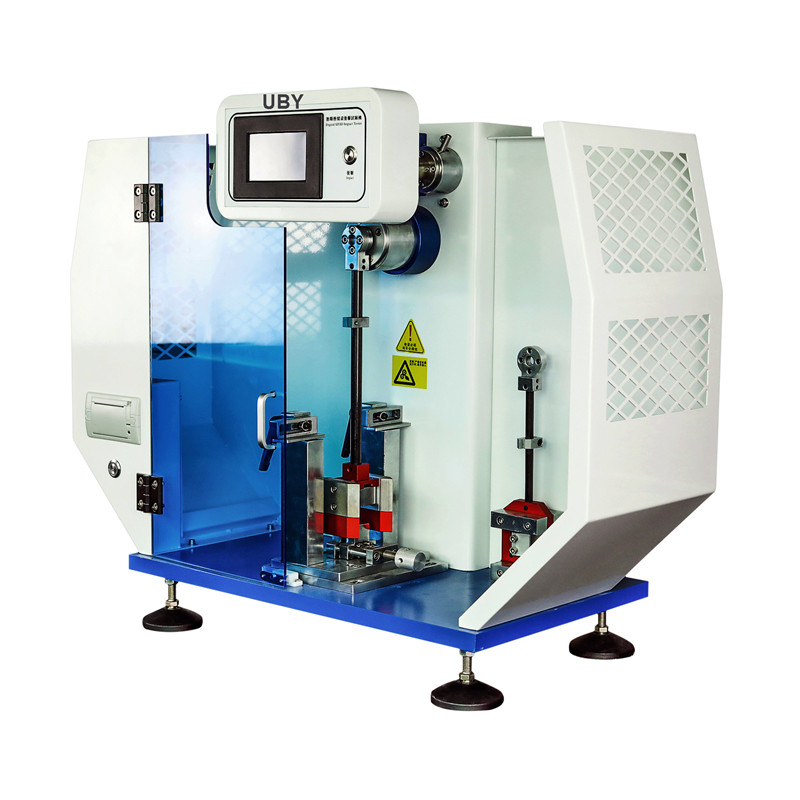
Find your bookmarks in your Independent Premium section, under my profile
A woman taking her driving test passed with flying colours despite finding herself in the middle of a deadly car crash caused by super-fog.
The student driver and her instructor Gisela Chevalier survived an 168-car pileup in Louisiana on Monday that killed eight people, but found themselves trapped on the severely congested bridge for hours.
Ms Chevalier told Fox 8 that their survival was down to the actions of her student.
Their car had become trapped between a flatbed trailer and a double 18-wheeler, she said.
To narrowly avoid an accident, she said that her student quickly slammed on the brakes.
“I’m very proud of her, because she did what we taught her to do. We are here because she handled it really good. Really brave,” she said.
Ms Chevalier described the scene of the horrifying crash, which occurred when fog and smoke from marsh fires burning in the area dangerously lowered visibility.
She said that while the pair were trapped on the interstate, they saw cars that were beyond repair and watched as medical personnel raced to save people.
The duo was eventually able to exit the scene and, when they did, Ms Chevalier said she had no doubt that her student had passed her driving test.
“She was at the wheel when all that happened. When we were ready to leave and turn around, I took the wheel, because I thought it was too much for her, honestly,” Ms Chevalier said.
“She’s a master. She made 100, no doubt about it. She earned it.”
In this aerial photo, responders are seen near wreckage in the aftermath of a multi-vehicle pileup on I-55 in Manchac
Eight people died in Monday’s crash, Louisiana State Police confirmed, while 63 people were injured in the pile-up that stretched along one mile of the elevated interstate.
The huge crash caused a section of the road to catch fire and destroyed a tanker truck carrying “hazardous liquid,” police said.
At least one vehicle went over the edge and lay sideways in the water below the intersection, as shown in pictures posted by the Louisiana State Police.
St John Sheriff Mike Tregre said that there was a total of 25 crashes, which involved three 18-wheel trucks, of which two went up in flames.
Ms Chevalier said she saw some of the drivers on the bridge speeding at the time of the incident.
The crash killed eight people
“A lot of them with the lights off,” she added. “And that’s why that state trooper was almost going from car to car, in his car, ‘Hey turn the lights on.’”
All vehicles have now been cleared along the I-55, and the debris along with diesel and other chemicals has now been taken off the road, police reported.
Officials believe that parts of the bridge will require repairs, and a testing consultant may start bridge deck scans to see what parts of the concrete are damaged.
Police said on Wednesday that the I-55 will still remain closed in both directions from I-10 to Ponchatoula while crews finish inspecting the roadway.
Join thought-provoking conversations, follow other Independent readers and see their replies
In this aerial photo, responders are seen near wreckage in the aftermath of a multi-vehicle pileup on I-55 in Manchac
Copyright 2023 The Associated Press. All rights reserved.
The crash killed eight people
Copyright 2023 The Associated Press. All rights reserved.
In this aerial photo, responders are seen near wreckage in the aftermath of a multi-vehicle pileup on I-55 in Manchac
Copyright 2023 The Associated Press. All rights reserved.
Want to bookmark your favourite articles and stories to read or reference later? Start your Independent Premium subscription today.
Please refresh the page or navigate to another page on the site to be automatically logged in Please refresh your browser to be logged in
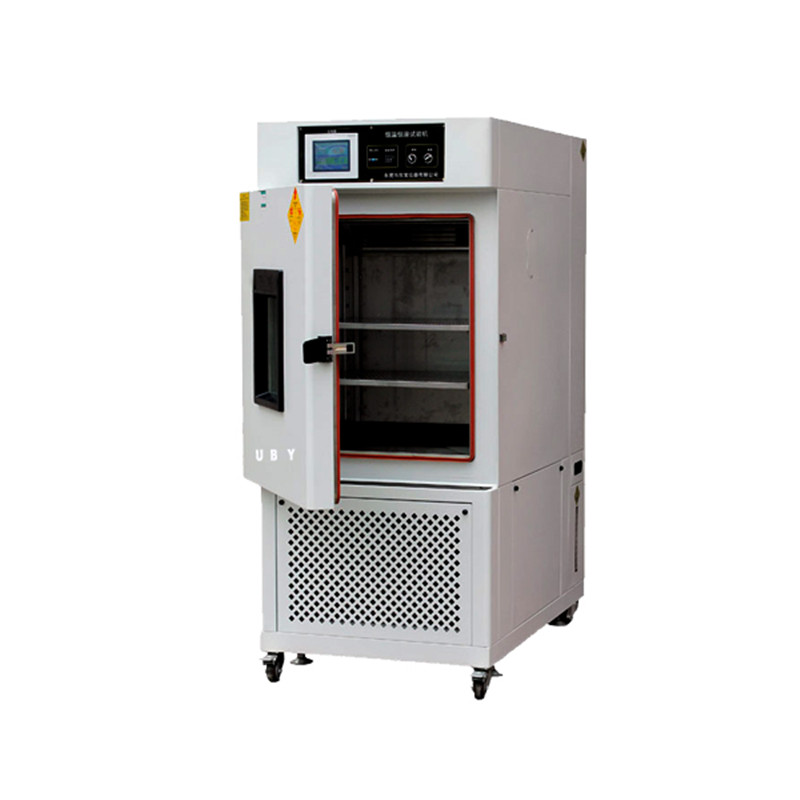
Water curtain Spray Cabinet Or if you would prefer: