Our car experts choose every product we feature. We may earn money from the links on this page.
Driveshaft failure is a relatively rare problem in newer cars, but it is one that has prompted a recall among 2016-17 model year BMW M3 sedans and M4 coupes and convertibles. The National Highway Traffic Safety Administration, or NHTSA, says that a total of 2,661 vehicles are potentially affected by this issue, which breaks down to 269 M4 convertibles, 936 M4 and GTS coupes and 1,456 M3 sedans. Slip Weld Flange

The issue that these cars may face stems from an integral flange for the driveshaft itself that the agency says may not be durable enough over time.
"Recalled drive shafts were produced with an integral flange which does not have sufficient long-term durability compared to other driveshaft flanges which were produced with sufficient long-term durability," the agency said in a statement announcing the recall.
The possible failure of the flange in these vehicles would cause a loss of propulsion, thereby increasing the risk of a crash, the NHTSA points out. (The good news is that no crashes have been reported as a result of this issue.) The agency says that owners may initially become aware of the issue by feeling noise and vibration from underneath the vehicle.
BMW first noticed the problem earlier this summer.
"Drivers of these vehicles reported hearing noise, noticing vibration and, in some cases, experiencing a loss of power. BMW requested the driveshafts for inspection and analysis. Factors such as vehicle age and mileage, engine power/torque and operating and environmental conditions were considered," the NHTSA said.
The automaker isolated the problem to a specific production period during which the integral flange may not have been made with enough long-term durability characteristics and could separate from the driveshaft over time.
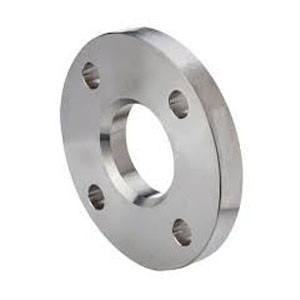
Flange Steel Owners of M3 and M4 cars affected by this recall will receive a free replacement if needed or a reimbursement for driveshafts that have already been replaced.