Phuchit/iStock/Getty Images Plus
CAD/CAM updates and features have largely been focused on enhanced productivity and increased digitization. Research and development in the CAD/CAM space is influenced by four main industry trends: the latest machining technology, Industry 4.0, automation and robotics, and the current state of the labour market. Cnc Machining Aerospace
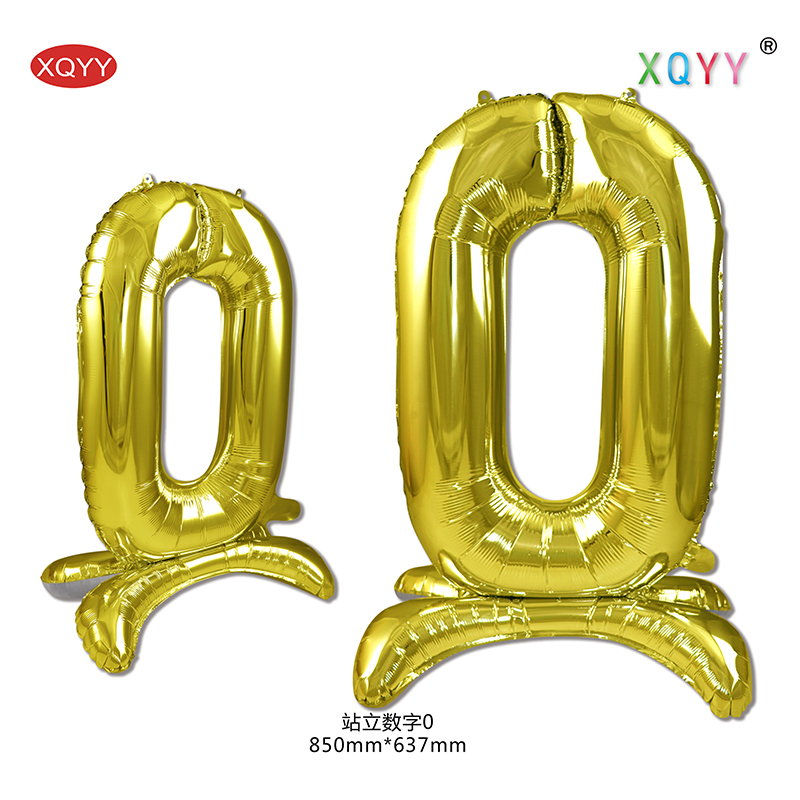
Whether it is a tool and die manufacturer, production machining facility, or small job shop, the market demands have changed significantly over the last few years. Efficiency, productivity, and price are driving manufacturing trends.
“Many [manufacturers] are now facing shorter lead times,” said Dan Marinac, product strategy and marketing manager, Cimatron, Burlington, Ont. “For example, what used to take 16 to 20 weeks is now expected to be delivered in just 10 weeks. [Manufacturers] must find ways to differentiate themselves from offshore companies to stay competitive in this market. One way to do this is to become more efficient and innovative in their design and manufacturing processes.”
To meet these tighter time frames, CAD/CAM developers must create new tools and features to help speed up the time it takes for shops to design and manufacture products.
For example, features like part analysis and repair for problematic geometry, automated parting line/surface, automated core/cavity extraction, smart catalogue component placement, automation for cooling line creation, plastic flow prediction, simulation, warpage analysis and compensation, automated electrode machining, NC template application, and automated gundrilling have all been developed to ensure that mold/die manufacturers are able to shorten the time needed to produce new tooling designs.
Outside of tighter lead times, manufacturers also are seeing a shift in the technology. For example, 5-axis machining has become increasingly popular.
“Five-axis machining centres are being increasingly used because of their ability to access more features of a workpiece and machine more aggressively with shorter tools and a sturdy machine construction,” said Marinac. “This has reduced the need for EDM and hand benchwork.”
This technology trend directly affects the functionality of CAD/CAM. Today’s software has been updated to include modules and features to enable efficient 5-axis machining and material removal simulation for medical, aerospace, and other complex parts. For example, some software offers access to a library of proven posts for any 5-axis machine and controller, including on-machine inspection and probe toolpath creation.
Another significant technology trend involves multichannel machines, like Swiss-type machines or mill-turn machines with a double turret, two spindles, or two channels.
“Even with these machines, it’s important to understand if a shop is taking advantage of the capabilities,” said Andrei Kharatsidi, CEO, SprutCAM Tech, Limassol, Cyprus. “Many users do not use the multichannel feature because it is complex; they play it safe rather than experimenting with complexity and speed. Instead, they opt for sequential programming instead of parallel because it's easier to program and check.”
Today’s software has been updated to include modules and features to enable efficient 5-axis machining and material removal simulation. Cimatron
However, with shorter lead times and productivity in mind, manufacturers need to squeeze all the potential they can from their machines. And one way to do this is to explore CAD/CAM that offers multichannel, automatic synchronization programming options. These types of programs are complex and cannot be done manually. But they tend to be expensive.
There are some in-between options, like those that leverage the capability of just two-channel synchronization.
“While limited to only two-channels, a simple click of a button, rather than a complex interface, allows for parallel processes to be simulated, and then the user can check and change whatever is needed to allow for the part to be processed this way,” said Kharatsidi.
This option is for shops that are transitioning to these types of machines, and it can act as a starting point to help them understand how to maximize capabilities.
Industry 4.0 has many facets that belong under this umbrella category. Right now, artificial intelligence (AI) is one of the big buzz words out in the industry.
According to Kharatsidi, AI is making significant waves when it comes to toolpath calculations, especially for the creation of operation sequences. Rather than an operator selecting one-by-one operations, inputting the machine type and various parameters into the software enables AI to select optimized sequences.
Another area of opportunity comes with cloud collaboration. Many machine shops are taking advantage of cloud-based programs to digitize their business and operations.
While cloud collaboration is not specifically tied to CAD/CAM, it is increasingly being used to help manufacturers transition projects and files more seamlessly.
“Transferring files between different actors during the manufacturing process can be clumsy and inefficient,” said Kharatsidi. “With the goal to reduce the amount of time between the design to manufacturing to part process, a cloud-based collaboration platform within the CAD/CAM software is a way to make the process more effective. It is one space where all chat functions, pictures, and real-time information can be stored without needing an external source of information.”
This push directly deals with an organizational issue of having multiple or different versions of the same project. Manufacturing is an active process, often with many people involved across different locations. Having several saved versions of the same project can lead to mistakes and an elongated process.
Robots now are actively involved in the machining process. A prime example of that is a milling robot. Today’s CAD/CAM software can offer one platform for both CNC machines and robotic programming. SprutCAM
Collaboration and cloud-based tools are being built into today’s CAD/CAM software to make it easier for stakeholders to communicate effectively and for the job to be completed efficiently.
Automation yields several benefits for the manufacturing industry. This is especially true for industries like the tool and die sector that produce complex components. Automation can be used to help workers overcome the challenge of creating complex dies and molds from intricate digital designs and ultimately can free up valuable labour.
“For example, 3-axis deburring toolpath procedures create chamfers or fillet shapes along sharp edges. This eliminates hand polishing thus saving time in mold tool and die manufacturing,” said Marinac. “Other examples include new options for predrilling during roughing operations, preventing cutters from plunging into blind pockets. The software will automatically define the optimum position and depth for predrilling as part of the roughing procedure.”
Outside of automating the programming process, it’s no secret that robots are becoming more commonplace on the shop floor, and there are an increasing number of applications where they make sense, like polishing, grinding, and some contouring applications. In some instances, robots are actively involved in the machining process. A prime example of that is a milling robot.
“There is software available that offers one platform for both CNC machines and robotic programming,” said Kharatsidi. “Most shops work with singular platforms, one for the machine and another for robots. Instead, in the CAD/CAM software, there is the option to unlock robotic programming capabilities.”
Off-line robot programming done within the CAM software allows users to program the robot without actually needing the physical robot. It’s a digital twin in the CAM software, where the programmer makes one program while the robot is working on another.
Online programming often is done by hand with a teach pendant. It can be slow, only simple toolpaths can be created, and the robot must be physically available for programming to take place. This is one way forward for shops that are just starting out with robotics or don’t have someone experienced enough with the CAM software.
“In the future, there needs to be a hybrid robot programming option, which includes online and off-line worlds combined in one solution,” said Kharatsidi. “Real-time simulation also is significant. In the future, it will be the only way to program robots. Both current options have obvious drawbacks.”
Another trend that affects the way CAD/CAM is being developed is the rapidly changing labour force. Over and over, shop owners express their frustration over a lack of skilled workers available for hire. But how does that translate to CAD/CAM?
“This challenge is addressed through an emphasis on machine simulation and verification of toolpaths,” said Marinac. “Machine simulation accurately represents kinematics, workpiece, fixtures, and material removal. Reliable collision and gouge detection is required for all toolpaths for the machine, fixtures, stock, part, tool, and holder. For high-quality embedded material removal simulation, 5-axis toolpaths are even more critical.”
Beyond software functionalities, the current labour market also is affecting the CAD/CAM user interface. With a less skilled workforce, it is more important than ever to ensure that the software has a gentle learning curve so that even the most inexperienced of users can operate it. This is important because experienced CNC programmers may be hard to find, and those with very little experience might find the software’s intricacies intimidating.
“CAD/CAM is particularly feature rich, often containing hundreds if not thousands of features,” said Kharatsidi. “It’s important that the interface is as user-friendly as possible and easy to learn. It’s all about creating a system where someone can go in with a basic understanding, spend some time, and take that knowledge and apply it across the board and have a grasp of how all aspects work. CAD/CAM interfaces have been reimagined with this in mind.”
Associate Editor Lindsay Luminoso can be reached at lluminoso@fmamfg.org.
SprutCAM Tech Ltd., sprutcam.com
Canadian Metalworking / Canadian Fabricating & Welding
Toronto, M1R 0A1 Canada
See More by Lindsay Luminoso
Lindsay Luminoso, associate editor, contributes to both Canadian Metalworking and Canadian Fabricating & Welding. She worked as an associate editor/web editor, at Canadian Metalworking from 2014-2016 and was most recently an associate editor at Design Engineering.
Luminoso has a bachelor of arts from Carleton University, a bachelor of education from Ottawa University, and a graduate certificate in book, magazine, and digital publishing from Centennial College.
Read more from this issue
Find Canadian Metalworking on Facebook
Find Canadian Metalworking on X
Keep up to date with the latest news, events, and technology for all things metal from our pair of monthly magazines written specifically for Canadian manufacturers!
Easily access valuable industry resources now with full access to the digital edition of Canadian Metalworking.
Easily access valuable industry resources now with full access to the digital edition of Canadian Fabricating & Welding.
Lack of manpower causing a bottleneck in your work flow? We have the solution for you: ASTES4 - Fully Integrated Laser Automation System | MC Machinery
© 2024 FMA Communications Canada, Inc. All rights reserved.

Cnc Machining Not yet registered? Sign up