With continuing advances in PCD cutter technology and improved bit body stability, PDC bits have become the dominant force in the worldwide drilling theater, practically replacing the venerable roller cone product. Their high ROP potential and unparalleled durability make PDC bits the tool of choice in both high- and low-cost environments. Even in the toughest applications traditionally reserved for roller cones, PDCs have virtually eliminated the situations where operators are forced to fall back on these types of bits. Today’s PDC bit technologies will positively impact performance and drive down the real cost/ft.
Halliburton’s Cruzer rolling element refines depth-of-cut control and yields multiple performance benefits, Fig. 1. The new PDC bit design technology improves depth-of-cut control (DOCC) and reduces the energy loss by the element to enhance drilling performance. It helps maximize ROP while delivering better tool-face control, to consistently provide on-target intervals. H22 Integral Drill Rod
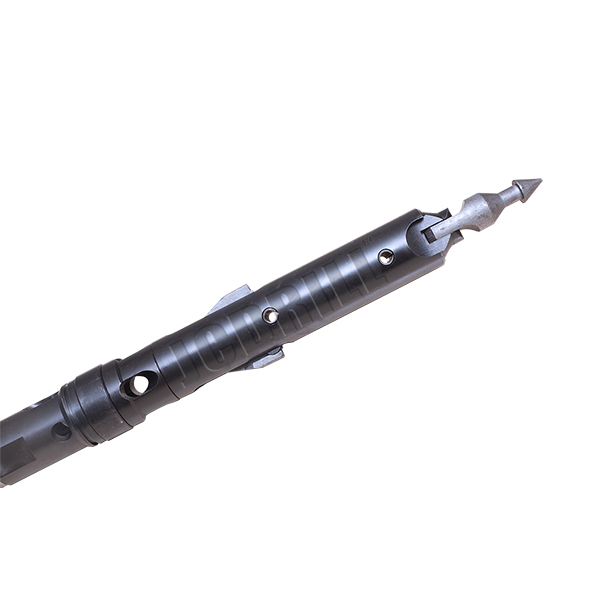
It’s long been recognized that maintaining constant engagement of PDC cutters while drilling helps minimize torque fluctuations, vibration, and impact-induced cutter damage. While these DOCC elements do help reduce changes in cutter engagement and resultant drilling dysfunction, they do so at the expense of energy available for shearing rock.
Because the new DOCC element rolls, it reduces over-engagement, due to formation changes or vibration without compromising cutting energy. Because of its rolling nature, the diamond-and-carbide bearing lowers the coefficient of friction, ensuring low heat and reduced torque generation. As a result, most of the torque available to shear rock can be used by the cutters for more efficient drilling, while tool-face control is enhanced by the consistent depth-of-cut.
The roller bearing design is packaged with a novel retaining mechanism to keep the element in position for the entire run, and provide consistent depth-of-cut control without impeding its rolling action. In addition to its enhanced wear resistance, Cruzer is also easily repairable, so a bit can be reused multiple times for greater cost-effectiveness. A small package size allows the element to be incorporated into both existing and new bit designs, according to application requirements.
To determine the right technology for a given application, Halliburton’s design at the customer interface (DatCI) process begins with input from the operator to guide development. Using an extensive assortment of analytical tools that include simulation, analysis and software programs, the design team can then apply the appropriate technology to help achieve the operator’s specific goals. The continuous improvement nature of the process enables application experts to continually enhance drilling efficiency and lower costs, even in well-developed areas.
Williston basin case study. In North Dakota, the local DatCI team determined that incorporating the rolling DOCC element into a new bit design would resolve directional control issues presented by a challenging curve interval of 935 ft, including 100 ft of vertical section. The drilling engineer was particularly concerned with optimizing performance through the curve, because it was his first attempt at constructing a 3D curve.
Halliburton’s multi-feature bit solution combined the DOCC rolling element with an 8¾-in. MMD55MU MegaForce PDC bit. Using a controlled ROP of 46 ft/hr, the bit drilled the entire 1,035 ft of vertical and curve intervals, and successfully achieved all directional requirements of the complex wellbore design.
At the end of the run, dull grading revealed only minor wear on the DOCC compared to traditional elements that were considerably worn. Field engineers graded the cutting structure 1-1-WT-S-X-I-NO-TD, indicating that the addition of the DOCC element had enabled the bit to retain the aggressiveness of a sharp cutting structure, even after drilling 100 ft of vertical section.
Operators have continued to seek reductions in cost and increases in efficiency while drilling through multiple formation layers. Advances in cutter technology have enabled operators to drill longer laterals than previously possible. Despite these advances, formations with highly interbedded rock of varying UCS still present a challenge for many cutter technologies. Softer shales, when interbedded with harder sandstones, can cause abrasive wear, while hard dolomite and chert cause excess bit vibration and increases in impact damage. To address the challenges, National Oilwell Varco (NOV) developed ION cutter technology to complement their Tektonic line of PDC bits.
ION cutter technology consists of a high-performance range of PCD cutters that have been designed specifically to overcome critical failure modes in highly interbedded formations. Refined diamond feeds and increased sintering pressures provide a more durable, abrasion-resistant cutter that maintains thermal stability using deep-leach technology. The new cutter underwent extensive testing to obtain performance metrics, with results indicating that the cutters can drill much farther than comparable products, with minimal wear scarring, under difficult drilling conditions. Maintaining the cutting edge provides higher ROP while maintaining durability for the section. Cutter geometry was also optimized using modeled FEA before testing on rock formations under pressure, leading to reductions in drilling torque and MSE, and increases in ROP for the same WOB.
Case studies. In Stephens County, Okla., an operator needed to drill an 8¾-in. lateral section, as quickly as possible, without sacrificing bit durability. After studying the formations, it was determined that the bit frame would need to balance efficiency with performance and that the cutters would need high thermal stability. NOV paired a TK63 bit with the ION cutters to increase ROP. The bit was run, and it drilled 3,967 ft at an average ROP of 90.2 ft/hr. Additionally, the ION-equipped bit exhibited approximately 50% less dulling than the offset average. The previous bit made just 3,329 ft of hole at a much-lower ROP of 31.4 ft/hr.
In the Williston basin, an operator needed to drill a horizontal well from surface casing to TD with a total of five BHAs. ION cutters were paired with the drill bits used to drill the tophole vertical, bottomhole vertical, and horizontal sections. In the horizontal section, performance was exceptional, and the operator drilled 9,715 ft at 196 ft/hr and completed the section in just 49.6 IADC hr, Fig. 2. The run set a record for the fastest lateral drilled by the client. The operator also set a record entry-to-TD time, drilling the well in only 8.18 days. Excluding trip time, the entire well was drilled in 5.04 days, almost 20% faster than the average offset.
Smith Bits, a Schlumberger company, introduced a new type of PDC bit that incorporates ONYX 360 rolling cutters and Stinger conical diamond elements. The design was developed, using the IDEAS integrated dynamic design and analysis platform to optimize the cutting structure to withstand the toughest formations and downhole conditions.
Incorporating ONYX 360 into the cutting structure substantially increases bit durability, because the cutter revolves 360°, enabling the entire diamond edge to contribute to drilling formation. Stinger elements, which have a pointed shape and a thick diamond layer, provide superior impact resistance, compared to conventional PDC cutters. When placed in a position trailing the primary cutting structure of a PDC bit, the elements protect the PDC cutters from impact damage, Fig. 3. By combining the unique cutting elements, Smith Bits was able to develop a unique PDC bit optimized for abrasive/hard and interbedded formations. The combination and strategic placement of these novel cutters maximizes footage and increases ROP.
Egyptian case study. While drilling in Egypt’s Kharita formation, an operator encountered abrasive sandstone interbedded with shale. Unconfined compressive strength in the formation ranged between 18,000 and 25,000 psi, reaching 30,000 psi in some intervals. During a previous run, a PDC bit was able to drill 97 m, but the operator was forced to trip for a diamond-impregnated bit to drill the remaining interval. As a result, the operator developed an initial well plan that called for a rolling-cutter PDC bit to drill 150 m, and then run-in a diamond-impregnated bit to complete the section.
However, Smith Bits designed a specialized PDC by incorporating rolling cutters and conical diamond elements into the cutting structure. The custom-designed PDC was run, and it achieved a record length of 288 m, with ROP averaging 3.7 m/h at an inclination ranging between 5.75° and 1.78°. The bit drilled the hole section to TD in one run, eliminating the trip for a diamond-impregnated bit to finish the hole section. The client saved approximately $30,000 and achieved the lowest cost/meter, compared to offset wells.
Ulterra Drilling Technologies’ latest innovation is the patent-pending SplitBlade PDC bit (Fig. 4 ) that is increasing ROP and reducing drilling time with reconfigured cuttings evacuation, cutter cleaning, and bit cooling.
Typically, with most PDC technology, recirculated rock cuttings become trapped at the toolface, and the build-up clogs the junk slots. Trying to recut old cuttings that should have been evacuated quickly wastes energy, in addition to degrading the bit.
The company’s research team examined the physical restraints of a basic PDC drill bit. The engineers proposed a new pattern that would maintain the cutters in a cleaner, cooler state. The improved thermal management of the bit face would support the goal of extending bit durability and lead to higher performance.
Using CFD, the team created a distinctive bit body, with new blade geometry, nozzle placement, and cutter layout. By splitting the shape of the primary blades with an angular offset, designers created designated flow channels for the fluid and cuttings. Two nozzles are positioned to support the cutters in the critical area to capitalize on this advancement in bit body construction and hydraulic control. While drilling, cuttings from SplitBlade technology can be evacuated up to seven times faster, compared with conventional designs.
Case studies. In the LaSalle County portion of the Eagle Ford shale in South Texas, an operator was experiencing poor cuttings removal and plugged nozzles. To solve the issues, an 8½-in. SplitBlade PDC was run, and it drilled the curve 27% faster than offsets. This run set a company formation footage record of nearly 14,000 ft, MD, for the curve and lateral. The ROP of more than 150 ft/hr was 8% faster than the offset average in wells over 10,000 ft.
In the eastern Eagle Ford, another operator wanted to reduce the instances of nozzle plugging to improve ROP, and selected an 8½-in. SplitBlade bit. The plan was to improve lateral and overall ROP with better directional control and cuttings removal. The bit was run, and it set a rig footage and ROP record, drilling the lateral at 400 ft/hr instantaneously and, overall, just less than 12,000 ft in under 68 hr. The average ROP of 172 ft/hr was 56% faster than the average run on this rig.
Precise, application-specific optimization of PDC bit hydraulics has improved drilling performance in vertical and lateral Permian basin wells. Using curved nozzles, webbed blades, and proprietary design features, Varel Oil & Gas Drill Bits’ HYDRA hydraulics optimization program (Fig. 5 ) has improved ROP and footage drilled in softer clays and shale, as well as sands and limestone. In a Wolfcamp lateral, an optimized bit increased ROP 58% and footage by 98%.
The HYDRA program improves performance with better bit cooling and cleaning, and more effective cuttings removal. The design process applies uniquely curved nozzles, webbed blades, and other features using CFD to match the design to the application. The curved nozzles reduce core-outs, plugged nozzles, and bit balling. The webbed blades limit cuttings recirculation, reduce entrainment, and increase cuttings volume.
Rig capabilities. Cuttings volume, formation types and rig pressure limitations can greatly reduce the hydraulics performance of PDC bits. In these applications, improving cleaning efficiency is difficult without trading a drop in pressure across the bit. Different methods have been used, in an attempt to improve fluid velocity and impact pressure, with varying degrees of success.
Varel’s research led to extensive modeling to reproduce the effect and advantages of various curved nozzle designs that could be applied across an entire size range of bits. This required CFD studies to understand the results of each change in nozzle configuration, and how the nozzle redirects flow and velocity across the bit.
Using results from the CFD modeling, the company optimized a unique set of features, including proprietary curved nozzles, webbed blades, and other design characteristics. The program successfully balances traditional trade-offs to optimize performance in specific applications.
Curved nozzles. The curved nozzles produce several actions that enhance performance. Bit stability is improved, and formation erosion is mitigated, because the fluid stream’s impact on the formation is reduced. Fluid flow is, instead, directed to the cutter surface to improve cleaning and cooling without affecting rig hydraulics. This reduces coring and other problems to extend bit life.
The webbed blade feature blocks fluid flow to adjacent junk slots to prevent cuttings recirculation. It also eliminates fluid entrainment by adjacent nozzles to maximize nozzle efficiency. The unique junk slot geometry results in more efficient cleaning for greater cuttings removal.
Permian basin performance. In New Mexico, interbedded clays, carbonates, limestones and sandstones typically challenge PDC bit penetration rates and footage. Bit hydraulics are particularly important to efficiently drilling the target intervals. An 8¾-in. PDC bit that was optimized for the application significantly improved footage, drilling a 7,001-ft vertical section, compared to an offset average of 6,579 ft. ROP was faster at 133 ft/hr versus the 106 ft/hr average offset performance. These results produced the operator’s fastest one-BHA run to TD.
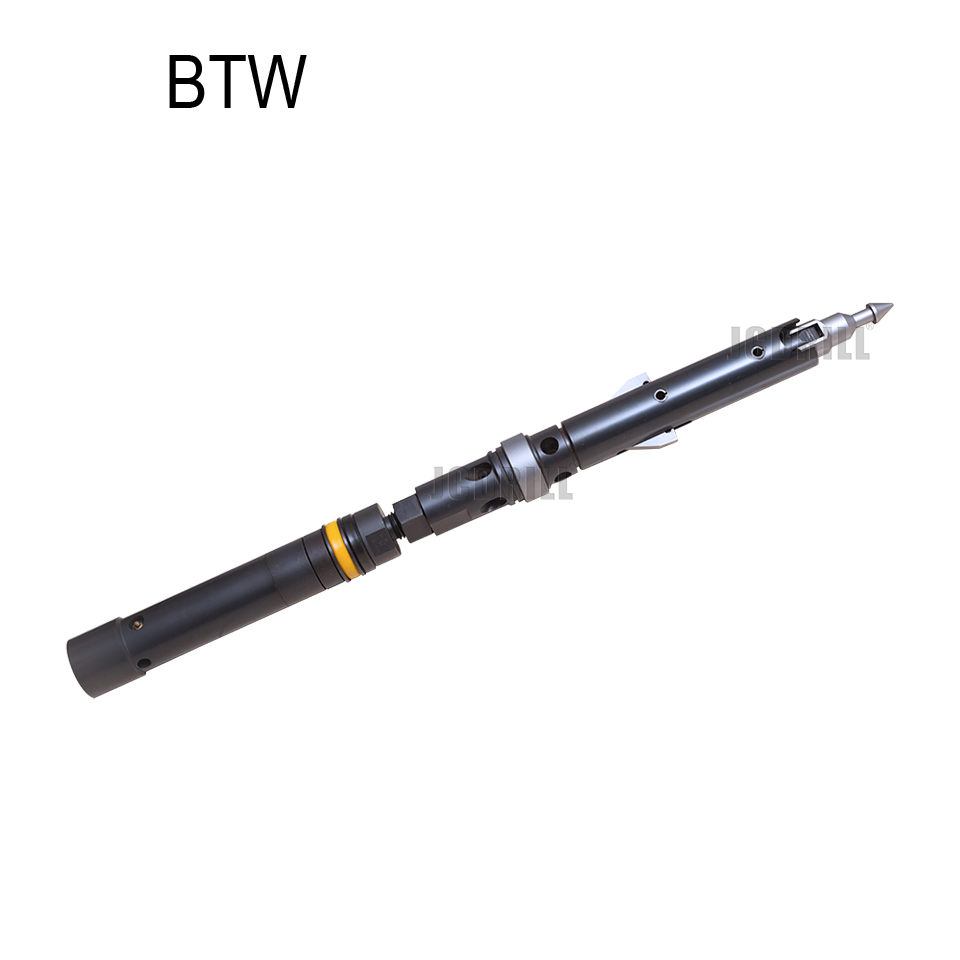
Single Tube Reamer On the Texas side of the basin, HYDRA optimization has cut the number of bits in half. Only two 61/8-in. bits were required to drill a lateral section that typically has required four bits. They drilled 8% more footage at an 8.5% higher ROP, compared to standard PDC bits used in offsets, eliminating the time cost, and risk of two additional round trips.