During the 2024 AMUG Conference, David Moodie of Foundry Lab and Cameron Peahl from Eaton Additive Manufacturing Center of Excellence discussed using new technology in manufacturing, particularly in diecast metal production.
Moodie shared his experience as a startup founder, highlighting the challenges of producing diecast metal, including the need for a fast and efficient system. The conversation touched on the differences between digital casting and conventional casting, emphasizing the advantages and challenges of each process. Steel Casting
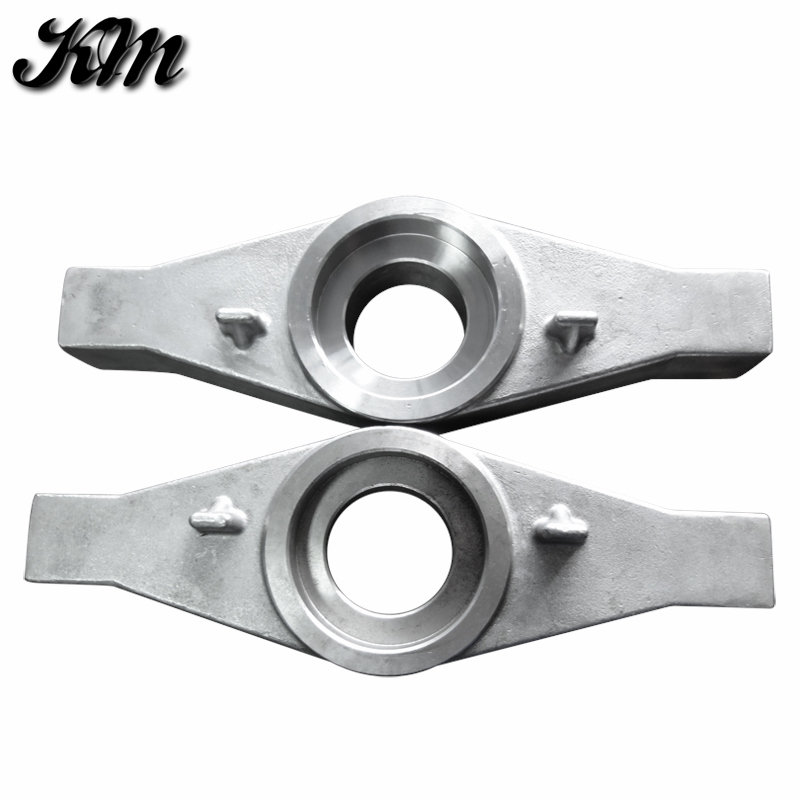
Moodie, originally from New Zealand but now operating in California, highlighted the limitations in traditional prototyping, particularly in die casting. He shared, “Customers wanted either a strength profile or a thermal dissipation profile. The problem was the prototype by casting; it’s too expensive.” His frustration with conventional methods led to a unique solution. Moodie explained, “I took a microwave into my backyard, and I discovered that I could produce die-cast equivalent parts without a furnace.”
This innovation evolved into a more sophisticated system. The process begins with designing molds, which he acknowledged as a significant barrier due to a reluctance to engage in mold design. To address this, Foundry Lab developed a plugin for Fusion 360 that automates mold design from CAD files. The molds are created using a binder jet printer, which lays down layers of ceramic powder and binder.
The heart of the system is what Moodie refers to as the “microwave system,” which heats the powder to set the binder, creating molds that can be as thin as two millimeters. “It’s super fast today,” Moodie stated, showcasing the efficiency of his process. The microwave system melts the metal within the molds, ensuring an even casting. This is followed by a quench system that rapidly cools the casts.
Moodie’s approach significantly reduces the time and cost associated with metal casting. “This is casting for dummies,” he jokes, emphasizing the simplicity and accessibility of his method. It’s adaptable to various metals, with temperatures ranging from 1,100 degrees Celsius to 2,000 Fahrenheit.
Moodie highlighted that their technique results in parts requiring some post-processing, akin to traditional casting. He explained, “When you’re finished, you end up with a sprue on top, which you’re going to need to cut off. You treat the rest of it like a casting because that’s what it is.” The process, as he outlined, allows for the molds to be reused multiple times, depending on the design’s geometry.
Despite the successes, Moodie was clear about the ongoing challenges and the learning curve involved. The technology has begun to attract interest from various companies for evaluation, even for applications not previously attempted, like stainless steel casting.
Cost-effective molding process for diecast parts
Cameron Peahl from Eaton Additive Manufacturing Center of Excellence provided insights into how their large-scale industrial power management solutions company is integrating additive manufacturing across their 300-plus global manufacturing sites. Eaton, which operates predominantly in the electrical and industrial sectors, considers castings crucial in their wide range of products.
Peahl outlined Eaton’s approach to additive manufacturing, which revolves around four pillars: technology, advanced materials and processes, patenting, and supply chain resiliency. He stressed the importance of this integration, particularly in prototyping, stating, “We need our parts in conventional materials to stay in production, and we run into a lot of problems with additive because it is a different process.”
Highlighting the challenges of requalifying parts for additive processes in the face of supply chain issues, Peahl remarked, “We don’t have the luxury of resources to go and requalify those parts for an additive material process.” To tackle this, Eaton is exploring how additive manufacturing can expedite part production without compromising quality.
Peahl shared Eaton’s evaluation of a new technology, focusing on casting porosity, part tolerances, and microstructure. They experimented with three parts of varying complexity, including cast-in-place steel pins. He noted the distinct surface finishes and multi-shot casting, allowing multiple parts in a single run.
Eaton also utilized CT scanning to examine the castings, revealing significant differences between conventional and digital casting processes. Peahl expressed his surprise at the results, “With the digital casting process, it’s amazingly dense.” This density was especially notable in parts with cast-in-place pins, where the technology allowed for smooth metal flow and even cooling.
Throughout the experimentation, Eaton maintained low porosity in their parts, an important factor in ensuring quality and durability. Peahl’s presentation underscored Eaton’s commitment to leveraging additive manufacturing to enhance efficiency, quality, and resilience in their supply chain.
Using additive manufacturing for industrial parts
Cameron Peahl from Eaton Additive Manufacturing Center of Excellence continued to elaborate on their advancements in additive manufacturing, specifically focusing on the dimensional analysis, surface finish, and microstructural properties of their parts.
Peahl highlighted the process’s potential for achieving precise dimensions. “We have some really nice green surfaces getting really close to nominal dimension,” he noted, acknowledging the need for further tuning to attain repeatability and the desired dimensions. This indicates that while the process is promising, refinement is necessary.
One significant challenge identified was the rougher surface finish of parts produced via their method compared to traditional casting. He recognized this as a possible hurdle for adoption, as the parts may look and feel different, even if their functional impact remains unaffected.
The analysis also revealed a coarser grain structure in the digital casting process, potentially affecting the strength and hardness of the parts. “Based on the grain structure, that’s likely the case,” Peahl remarked, though he couldn’t provide definitive hardness data. However, he noted a significant advantage: the density of the castings might allow for effective heat treatment, potentially not feasible with conventional parts.
Financial viability is a key focus for Eaton. Peahl emphasized the cost competitiveness of their process, stating, “We’re competing with more or less our actual casting costs.” This becomes more pronounced with multi-shot or multi-cavity molds, as the mold cost gets distributed across multiple parts, significantly reducing the cost per part.
Looking ahead, Peahl outlined Eaton’s priorities: refining microstructure control, improving surface finishes, ensuring processing capability, and validating cost model assumptions. “We need to make sure we really, really understand that piece of it,” he stressed.
Moreover, the additive process presents opportunities for Eaton to experiment with custom materials at a scale previously unattainable. Peahl expressed excitement about these prospects: “It opens up some interesting research avenues for us.”
Overall, Eaton sees a path forward with this technology, balancing the need for large-scale part production with the advantages of additive manufacturing. The presentation gave another insight into why Foundry Lab was selected as a winner in the 2023 3D Printing Industry Awards.
Join the Expert Committee for the 2024 3D Printing Industry Awards to help select the winners!
What 3D printing trends do the industry leaders anticipate this year?
What does the Future of 3D printing hold for the next 10 years?
To stay up to date with the latest 3D printing news, don’t forget to subscribe to the 3D Printing Industry newsletter or follow us on Twitter, or like our page on Facebook.
While you’re here, why not subscribe to our Youtube channel? Featuring discussion, debriefs, video shorts, and webinar replays.
Featured image shows digital versus conventional casting. Photo by Michael Petch.
Michael Petch is the editor-in-chief at 3DPI and the author of several books on 3D printing. He is a regular keynote speaker at technology conferences where he has delivered presentations such as 3D printing with graphene and ceramics and the use of technology to enhance food security. Michael is most interested in the science behind emerging technology and the accompanying economic and social implications.
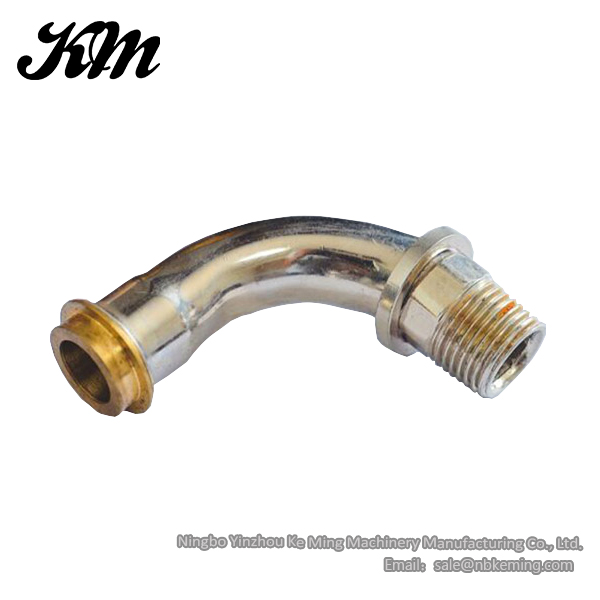
Custom Iron Casting Foundry © Copyright 2017 | All Rights Reserved | 3D Printing Industry