Fred Whitford, Director, Purdue Pesticide Programs
Brad Peas, Sales Representative, AgroChem Stainless Steel Mix Tanks
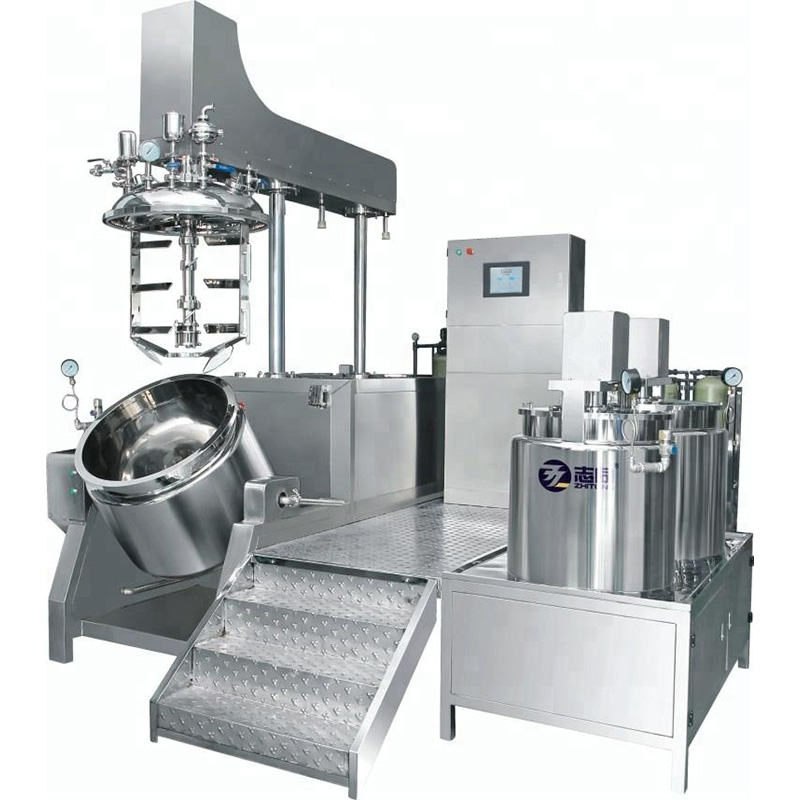
Darrell Oltman, Director of Engineering, Snyder Industries
John Obermeyer, IPM Specialist, Purdue University
Kevin Leigh Smith, Continuing Lecturer and Communication Specialist, Purdue Agricultural Sciences Education and Communication
Introduction ……………………………………………………………………………………………….. 4 Basic Challenges Micronutrients Place on Storage Tanks…………………………. 6 Tank Compatibility — Working from the Inside Out……………………………………… 6 Tank Design — Emptying Tanks of Settled Product……………………………………. 15 Gaskets and Seals — Keeping Product Flowing Instead of Leaking…….. 16 Availability and Pricing — Having Enough Storage Capacity………………….. 17 Tank Height and Diameter — Making Sure Tanks Will Fit the Space……. 18 Installation — Larger Tanks Require Cranes and Forklifts……………………….. 20 Storage Conditions — Preventing Micronutrients from Freezing………….. 22 Needed Now or Later — Giving Yourself Time to Order…………………………… 24 Containment — Planning Ahead………………………………………………………………………. 25 Summing Up The Information…………………………………………………………………………… 26 Conclusion…………………………………………………………………………………………………. 28 Acknowledgments…………………………………………………………………………………………… 30 Disclaimer……………………………………………………………………………………………………….. 30
Progressive farmers have long been early adopters of new technologies to help them get the most economic return from their crops. Some tremendous strides agricultural producers have made in adopting and modifying production practices include:
• Planting cover crops to protect against soil erosion and build soil organic matter • Tiling fields to remove excess water • Precision soil sampling to determine lime and nutrient needs • Purchasing improved hybrid lines • Planting earlier to avoid heat stress during critical crop growth stages • Seeding at higher rates to maximize the capture of sunlight and space • Splitting fertilizer applications to “feed” plants when needs are greatest • Sampling plant tissues to determine nutrient deficiencies • Rotating pesticide classes to combat weed, insect, and disease resistance • Building grain storage bins to take advantage of market trends
Not adapting to new conditions or not adopting proven practices means that farmers could leave yields and profits in their fields. On the other hand, adopting unproven practices can be expensive when the cost of the new practice is more than the extra yield adds to the bottom line.
One practice receiving attention today is applying micronutrients. Farmers are asking whether it is worth the additional $5-$15 an acre to apply secondary nutrients and micronutrients like sulfur, boron, copper, zinc, and manganese.>
Like any new technology, many of the questions farmers and retailers are asking about micronutrients are being investigated by university and industry scientists. However, it seems that a number of commercial retailers and farmers are convinced they are getting economically significant yield gains from using micronutrients. And micronutrient use is increasing.
Never order a tank to store micronutrients without first doing your homework and asking lots of questions. Your effort might just save you from the need to purchase a second tank to replace one that failed prematurely. Questions you should answer before purchasing any tank include:
• How are the micronutrients formulated? • Is the tank material compatible with the specific micronutrient(s) you intend to use? • Is the tank designed to completely remove settled micronutrients? • Can you prevent micronutrient solutions from freezing? • What size tank will you need to store enough for the entire season? • When will you need the tank delivered by? • How much lead time will crane operators need to install large tanks? • Will adding micronutrient tanks put you over bulk storage regulations?
With micronutrient use increasing, and with projections that the market will continue to expand, the question arises of which tank material is best suited for storing these products. Micronutrient formulations may be different enough that the tanks and conditions that store urea – ammonium nitrate (28-32% liquid N) may not be suitable for micronutrient fertilizers.
This publication describes important factors you will want to consider when choosing between poly, fiberglass, carbon-steel, and stainless-steel tanks to store micronutrient fertilizers. Using these guidelines will allow you to select a tank type that will meet your needs over the long-term.
Plant nutrients include macronutrients, secondary nutrients, and micronutrients. Macronutrients include nitrogen, phosphorus, and potassium. Secondary nutrients include sulfur, calcium, and magnesium. Micronutrients include zinc, copper, boron, manganese, iron, and others. While we often consider all of these as “fertilizers,” sulfur and micronutrients form a diverse group of chemistries that can interact in various ways with the materials from which storage tanks are made.
If you’re browsing online, it might seem that there are plenty of tanks you can purchase to store micronutrients. However, the reality is that the material used to construct the tank, its design and shape, the cost to transport and set it up, and its availability will quickly narrow down the choices to just a handful of tank products.
If you want to purchase a tank that will store micronutrients at a retail facility or on the farm, consider the eight points outlined on the next several pages to help you narrow down your options to one or two tanks that will provide the best value over the long-term.
All manufacturers who sell micronutrients have the same elements. In other words, boron is boron, zinc is zinc, and so on. What differentiates micronutrient nutrient products is the way they are formulated. That should not come as a surprise. Nitrogen is formulated as anhydrous ammonia, UAN (both 28% and 32%), aqua ammonia, and urea.
Just like the different forms of nitrogen, manufacturers formulate their micronutrient products differently. The chemical makeup of the unique micronutrient formula can create compatibility problems with some materials used in constructing the storage tanks.
Formulations are important. Plants cannot take up many micronutrients in their pure form, so manufacturers have to place the micronutrient in an acid or alkaline solution so the element is in a form that is available for crop uptake. The range of acidity or alkalinity of the micronutrient solution can range from a pH of 1.2 (equivalent to battery acid) to a pH of 11 (equivalent to bleach). Knowing the micronutrient product’s pH is critical when selecting the types of tanks you can use.
There are four general tank types that have found wide use in agriculture: poly, fiberglass, carbon (mild) steel, and stainless steel. When you select a storage tank, your goal is to make sure the material the tank is made of is compatible with the chemical and physical characteristics of the micronutrient product. We describe the types of tank materials below.
The pH of a solution does not affect poly tanks, which is why people often use them to store highly corrosive materials such as sulfuric acid. What is important when ordering a poly tank is to consider the micronutrient product’s weight per gallon. Manufacturers design poly tanks based on the weight of the materials that will be stored in the tanks. Poly tanks used in agriculture are rated at 1.0, 1.5, or 1.9 specific gravity, and the numbers are calibrated to the weight of water — 8.3 pounds per gallon.
A poly tank with a 1.0 specific gravity rating is designed to hold the weight of any material that weighs about 8.3 pounds per gallon (the same as water). A 1.5 specific gravity rating means the tank can hold a material that is 1.5 times the weight of water (or about 12 pounds per gallon). And a 1.9 specific gravity rating can hold about 1.9 times the weight of water (or approximately 15.7 pounds per gallon). If you store micronutrient products (which typically weigh 10-11 pounds per gallon) in a tank that wasn’t designed to hold that weight, the tank can fail prematurely.
If you are thinking about storing micronutrients in a used poly tank, GIVE THE TANK THE PEN TEST to check whether ultraviolet rays have degraded the plastic.
For details, see Poly Tanks for Farms and Businesses: Preventing Catastrophic Failures (Purdue Extension publication PPP-77) available from the Education Store (edustore.purdue.edu) or Purdue Pesticide Programs (ppp.purdue.edu).
If you need a tank with a higher specific gravity, you can request one from a tank manufacturer. Such tanks are available but less commonly made. Again, it is important to make sure storage tanks meet or exceed the specific gravities of the micronutrient products. In general, poly tanks are made from high-density linear polyethylene (HD). They can also be made with crosslinked polyethylene (XL).
HD is generally compatible with most micronutrients and is the most common tank material used. XL is generally more expensive, but can be beneficial if surfactants are part of the micronutrient blend. If the tag identifying the tank material is missing, then call the manufacturer and ask them to confirm its composition by providing the serial number that is often etched around the lid of the tank.
Fiberglass tanks are also a good choice for storing micronutrients. On their exterior surfaces, one fiberglass tank looks the same as the next one. But the resins used to manufacture fiberglass tanks make them different. For corrosive materials like micronutrients, manufacturers will add an additional protection layer known as a veil.
Carbon (mild) steel is unsuitable for storing most micronutrients because of the corrosiveness of the materials. At a lower pH, the acidity of products like copper and zinc can degrade carbon (mild) steel quickly. Because of these concerns, you should not use tanks made of mild steel to store micronutrients.
Over time, acidic fertilizers will corrode carbon-steel tanks. Ultimately, corroded tanks must be taken out of service.
Most retailers and farmers believe that just because it is stainless, the tank is compatible with all liquids. That’s not necessarily true when you store more corrosive micronutrients. Suitability depends on the grade of stainless used in the tank’s construction.
Most stainless-steel tanks used in agriculture are graded 304 or 316, which is based on the steel’s carbon content. A 304 stainless contains a higher percentage of carbon in its construction, but is less expensive than 316.
Traditionally, agriculture has used the less expensive 304 stainless. Some micronutrient products attack carbon, which makes using 304 unsuitable for storing them. A 316 stainless-steel tank may be able to store most micronutrients, but you will have to discuss with tank manufacturers about the products you plan to store.
The plates on stainless-steel tanks indicate the type of steel used in its construction. The one on the left is 304, the other is 316.
A common mistake is to forget that many fittings and connectors are made from 304 stainless. As these photos suggest, many micronutrient products can rapidly degrade 304 stainless.
When upgrading tanks, make sure to let installers know you will need 316 fittings and connectors.
In general, polypropylene fittings are compatible with most micronutrients.
Micronutrients can affect pumps. You should expect cast-iron pumps to last for fewer years when using some micronutrients. Stainless-steel pumps are available, but are about four times the cost of standard pumps.
Safety Data Sheets can provide important information about micronutrients and the materials they are incompatible with. Some will caution you to avoid fittings made from copper and its alloys, aluminum, and nickel.
The concern is that when copper fittings react with micronutrient products, it can be very destructive to 304 and 316 stainless. Check with the stainless steel manufacturer to see if their tanks and fittings are compatible with the micronutrient products you plan to store.
Some micronutrients are formulated as suspensions, which means that the products “float” in the liquid instead of being dissolved in a solution. Without agitation, these suspended micronutrients tend to settle on the bottom of the tank over time. This is why we recommend that you purchase tanks that have a cone-shaped or sloped bottom that drains to a common outlet. Such designs allow you to easily remove suspended materials from tanks.
It is common to add recirculation pumps to tanks that will help keep micronutrient products in suspension. You can add additional fittings to poly tanks to aid in recirculating the product.
You can also add eductor nozzles to poly tanks that will help move the chemicals faster and more efficiently. A recirculation pump pushes material through the eductor nozzle. The nozzle’s shape pulls in additional volumes of material, which causes much greater flow in the tank. Eductor nozzles commonly have a 4:1 or 5:1 mixing ratio. So, flowing 50 gallons per minute (GPM) through the eductor causes a mixing flow in the tank of 200 (4:1) or 250 (5:1) GPM.
Another option for agitating products is available for larger fiberglass and 316 steel tanks. Some of these tanks have a side manway that allows access to the inside. Once inside, you can sweep the bottom debris back into the liquid as a suspension.
A stainless tank (above) and fiberglass tank (below) that have slopped bottoms that drain to a common outlet. This design helps prevent micronutrients from accumulating on the tank bottoms.
It is also important to review the materials used to make the gaskets and seals that will come in the micronutrients. Gaskets are generally constructed of either EPDM or Viton. EPDM generally works well with high-pH (caustic) products, while Viton generally works well with low-pH (acidic) products. You can see why it is important to know the pH values of the micronutrients you plan to store.
You may have to change the gaskets associated with a micronutrient to prevent them from breaking down.
Micronutrients should not affect pumps that are used for multiple products. Pumps are often used to move water, fertilizer, pesticides, and micronutrients. This mixed use allows the micronutrients to be flushed. Just make sure to flush pumps with clean water and antifreeze before storing them for the winter.
Pumps that are dedicated to micronutrient products can have problems if they remain bathed in the products.
While micronutrients are available in convenient 2.5-gallon containers, larger operations prefer to purchase micronutrients in less expensive bulk quantities, which lowers their cost per acre.
It’s also important to note that micronutrients are, like other ag products, subject to market disruptions and availability. If you have enough storage capacity to offload a year’s supply of these products, that can guarantee you will have the micronutrient products on hand, especially in the spring.
Buying larger storage tanks may eliminate poly as a choice. If you decide to use a cone-bottom poly tank, manufacturers may limit the larger sizes around the 11,000-gallon mark. Going above this capacity would require a fiberglass tank or a 316 stainless steel with sloped floors and manways. In that case, you will need to weigh the increased cost for fiberglass and stainless against the benefits of storing these larger amounts for lengthy periods.
When buying larger storage tanks, make sure the height and diameter of the tanks will fit the available space. You may be able to order a tank that has the same storage capacity, but it may require different height and diameter specifications.
A couple of close calls!
When installing a new tank inside, it isn’t enough for the structure to be as tall or taller than the tank you wish to install. You also need to account for the tank’s tipping height.
To calculate the tipping height, think of a right triangle. The tank’s height (A) squared, plus the tank’s width (B) squared will be equal to the tipping height (C) squared. The tank shown on page 19 is 22.375 feet tall (A=22.375) and 12 feet wide (B=12). Its tipping height (C, the height the building’s ceiling and inside space must be in order to position the tank upright) needs to be at least 25.4 feet.
Drawings for a 20,000-gallon tank with a sloped floor.
When considering tank expenses, don’t forget to include the cost of having a semi deliver the tanks, because the driver will require a CDL and the truck will need an Oversize Load permit. For many of the larger tanks, you will need to contact a local company who can provide a crane to unload them from the semi. You also will be expected to have a forklift to move the tanks to the final location.
Cranes must be on-site on the day that tanks are delivered.
Do not assume all liquids freeze at 32°F. Some micronutrient products will freeze at different temperatures than water. Be sure to ask the micronutrient manufacturers if their products freeze, whether warming their products will resuspend the products, and whether the micronutrient remains effective after thawing out.
If possible, store micronutrients that you must keep during the winter in a temperature-controlled building or barn. If that is not an option, you can order poly tanks that have heat tracing and insulation. You can keep these custom poly tanks above freezing with electrical heating systems, and these systems can be covered with insulation that will help keep the heat inside the tanks. Don’t forget that you will also have to heat and insulate any hoses or pipes connected to the tanks.
These photos show zinc and sulfur products in heated storage rooms.
Another option for tanks that must remain outdoors is to order poly tanks with insulation and heat tracing like the ones shown here.
The tanks we’ve described may not be available by your local vendors. This means that it could take months to get your specific tank made and delivered. This will require you to plan ahead before the growing season starts, so you can get your tanks delivered and filled with micronutrients. You will also have to work with local contractors who can be standing by to offload the semis.
It’s important to understand the micronutrient product you intend to store. If you plan to store a product that contains zinc in a formulation that largely stays suspended, then you can order a flat-bottom tank from a local vendor instead of waiting for a cone-shaped poly tank to be made and delivered. However, if you plan to store a different zinc formulation or a different micronutrient product, then the flat-bottom tank might not work as well without agitation or recirculation.
The flexibility of cone-bottom tanks may be the best option for your operation, which is why they may be worth the wait to have one custom-made.
These flat-bottom tanks store sulfur (left) and zinc (right).
Indiana considers micronutrients a fertilizer, so storing them could throw you over the limits allowed under the state’s containment regulations. Currently, Indiana requires protective diking for any location that stores more than 7,500 total gallons or a single container greater than 2,500 gallons as bulk storage. Any fertilizer, including micronutrients stored in a container greater than 55 gallons, adds to the total of 7,500 gallons.
Details about bulk fertilizer regulations are available in Bulk Pesticide and Fertilizer Storage on Indiana Farms (Purdue Extension PPP-63), available from the Education Store (edustore.purdue.edu) or Purdue Pesticide Programs (ppp.purdue.edu).
The Office of Indiana State Chemist does not require these three 2,500-tanks to be diked (right), because the total volume does not exceed the maximum 7,500 gallons allowed under the regulations. If the operation added this 250-gallon minibulk of zinc, then they would exceed the 7,500-gallon threshold, so they would be required to be meet the state’s bulk fertilizer storage regulations.
The following table might be an instructive first step in helping you select a tank that meets your specific needs for storing micronutrients.
Farmers and ag retailers are always looking for ways to get more bushels out of every acre. In recent years, Corn Belt farmers have begun using more micronutrients as part of their fertilizer programs to try to improve their crop’s yield potential.
University and industry scientists are researching the answers to many of the questions being asked about micronutrients. That said, many commercial retailers and farmers are convinced that micronutrients will return more in yields than what they cost to purchase, store, and use.
After you narrow down your choices based on what you read in this publication, talk with your tank supplier and micronutrient supplier to get the answers you need about compatibility and other features that may be important in the final selection.
With more farmers using micronutrient products, questions about storing them in larger quantities are becoming more common. Do your homework, so you don’t end up like the person who spent $31,400 only to find out that the corrosive materials turned those expensive tanks into scrap metal (see A Costly Mistake, below). Ask before you spend!
Storing a micronutrient in the wrong tank can be an expensive mistake.
These photos show a 304 stainless-steel horizontal tank that stored a corrosive material. You can see where the caustic material penetrated the welds. Each tank cost $15,700, so the two tanks heading to the scrapheap was a $31,400 mistake.
If a picture is worth a thousand words, then it should be evident that asking a few questions can be worth tens of thousands of dollars before purchasing a tank.
Thanks to Dawn Minns for graphic design and Adduci Studios for illustrations. Thanks also to the following individuals who provided valuable comments and suggestions that improved this publication.
Sean Barber, Snyder Industries Chris Berry, Rosen’s Cal Funk, Novid Jeffƒ Hendershot, Rosen’s Jon Reinecker, Norwesco
This publication is intended for educational purposes only. The authors’ views have not been approved by any government agency, business, or individual and cannot be construed as representing a perspective other than that of the authors. The publication is distributed with the understanding that the authors are not rendering legal or other professional advice to the reader, and that the information contained herein should not be regarded or relied upon as a substitute for professional consultation. The use of information contained herein constitutes an agreement to hold the authors, companies, or reviewers harmless for liability, damage, or expense incurred as a result of reference to or reliance upon the information provided. Mention of a proprietary product or service does not constitute an endorsement by the authors or their employers. Descriptions of specific situations are included only as hypothetical case studies to assist readers of this publication, and are not intended to represent any actual person, business entity, or situation. Reference in this publication to any specific commercial product, process, or service, or the use of any trade, firm, or corporation name is for general informational purposes only and does not constitute an endorsement, recommendation, or certification of any kind by Purdue University. Individuals using such products assume responsibility that the product is used in a way intended by the manufacturer and misuse is neither endorsed nor condoned by the authors nor the manufacturer.
Reference in this publication to any specific commercial product, process, or service, or the use of any trade, firm, or corporation name is for general informational purposes only and does not constitute an endorsement, recommendation, or certification of any kind by Purdue Extension. Individuals using such products assume responsibility for their use in accordance with current directions of the manufacturer.
Find out more at THE EDUCATION STORE edustore.purdue.edu
Purdue Agriculture, 615 Mitch Daniels Blvd., West Lafayette, IN 47907-2053 USA, (765) 494-8392
© 2024 The Trustees of Purdue University | An Equal Access/Equal Opportunity University | USDA non-discrimination statement | Integrity Statement | Copyright Complaints | Maintained by Purdue Agricultural Communications
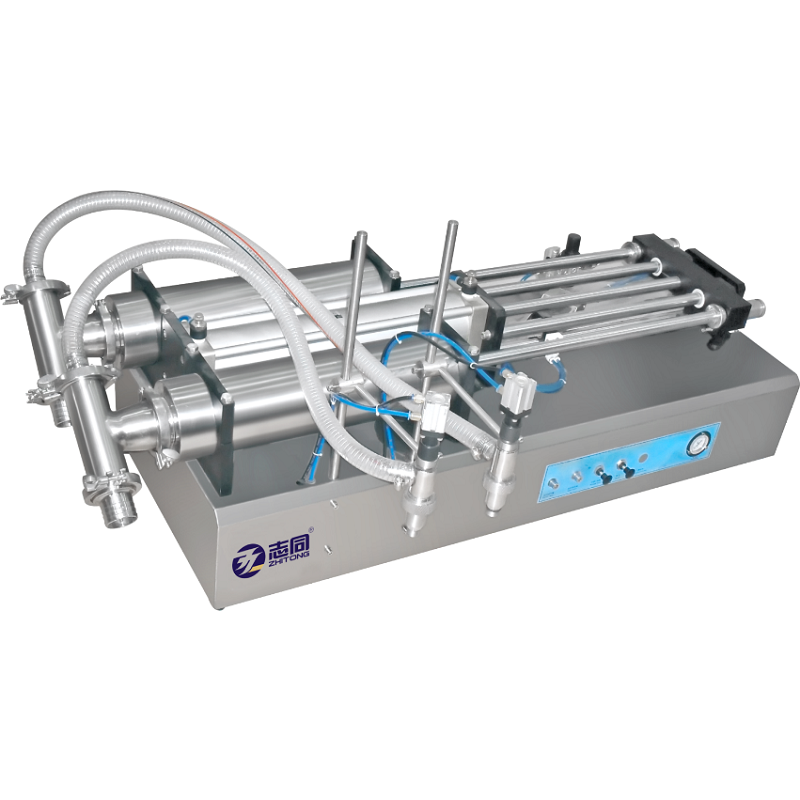
Cosmetics Making Mixer Trouble with this page? Disability-related accessibility issue? Please contact us at ag-web-team@purdue.edu so we can help.