“We cannot overstate the importance of the daily, visual pre-trip inspection to help identify any potential concerns that may need to be addressed,” said Bill Hicks, SAF product manager with SAF-Holland. “This inspection helps to identify issues such as loose fasteners and worn components. The more severe the application, the more frequently the inspections should take place.” Related Articles - Mitchell 1 collaborates with NEXIQ to streamline truck service diagnostic information - Fleet Advantage, FleetNet America by Cox Automotive partner on financing, maintenance solutions - Good News! Parts, labor costs fell slightly Q4 2023
If your drivers and technicians are visually inspecting your suspensions, they have to know what to look for and what it means for the repair. Rear Leaf Spring Bracket
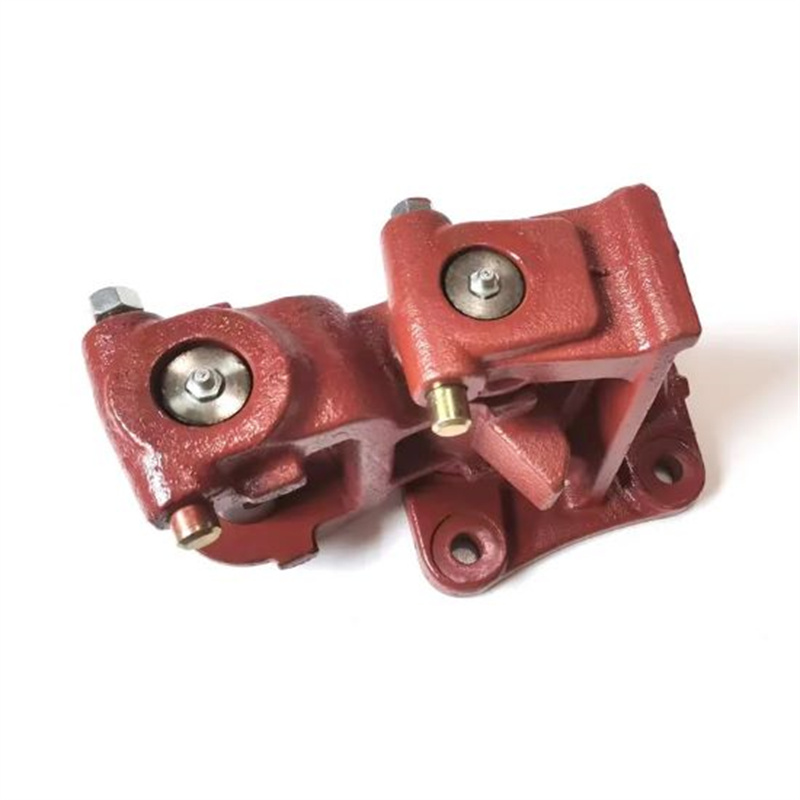
Quick disclaimer! Your specific tractor and trailer manufacturers, and your suspension supplier, are the first line of suspension maintenance. Check with them for the proper repair procedures. It’s advice we followed ourselves. That’s why we reached out to a bevy of suspension experts to pull together general rules of thumb that would give you guidance in your suspension inspections. Here’s what they said.
Sure, leaf spring suspensions typically require less maintenance than air spring suspensions, but to think it’s set-it-and-forget-it equipment is a mistake. Make sure your drivers and techs are giving these a good look.
What are they looking for?
“Fasteners and bushings are the most important items to check on leaf spring suspensions,” said Tyler Bernens, senior suspension product manager for Meritor. “Loose fasteners that are allowed to operate for any period of time will result in irreversible damage. Fastener torque should be checked periodically, especially U-bolts.”
“That’s the first thing: Check the torque on the U-bolts that fasten the spring pack to the axle,” agreed Chuck Boden, technical support specialist with Link Mfg. “The U-bolts often loosen over time and, when they do, allow the axle and the spring to move independently of one another, instead of functioning as a unified system.”
“Most manufacturers recommend rechecking fastener torques 500 miles after repairs,” Bernens added. “Similarly worn bushings that are not replaced will put excess stress on other components, leading to more extensive damage.”
Doubling down on the importance of bolt torque, Adam Kuiken, validation engineering and warranty manager for Reyco Granning, said, “Bolt torque, especially related to the clamp group and pivot points, is important to check. For example, the clamp group between the spring and axle must,” he stressed, “be torqued within 3,000 miles of being put into service.”
From there, Link’s Boden pointed to pins and bushings.
“Pins should be greased periodically and bushings inspected for wear,” he said. “Spacers and shackles need to be checked and if loose, the spacers need to be replaced. Spring packs should be regularly inspected for fatigued, broken or cracked leaves. Alignment of the leaves in the spring pack is also important and if misaligned, the centering pin may be to blame.”
To name a few more, Hendrickson’s Melanie Elliott, marketing manager, and John Knutson, technical services manager, rattled off a couple often-overlooked leaf suspension bullet points:
Here are the top three maintenance trouble spots courtesy of Link Mfg.’s Boden: The air spring;The air valve; andThe shock absorber.
“Things like bushings are way down at the bottom of the list,” he said, noting that this is due to the complications airbags can present. “The air spring is constructed of a metal bead plate on top, the rubber bellows, or air bladder, in the middle and the metal pedestal at the bottom. The rubber portion of the air spring is often referred to as the air bag by technicians. The integrity of the exterior rubber can most often become compromised by direct contact with a foreign object, excessive mechanical fatigue, high stress or through simple wear and tear.”
Let’s dive into the inspection details.
“Since the air spring is pressurized, visually inspect to ensure nothing rubs against the air cell, which could lead to damage,” SAF-Holland’s Hicks said. “The life of an air spring will vary depending on the type of application. Off-road applications will typically wear out faster than on-highway applications. Therefore, it is important to keep the air spring and lower piston clean of debris, using a mild soap and water solution.
“Periodically check for road gravel or other abrasive debris between the cell and the piston and the bead plates. Removing the debris will help to prevent air cell abrasion and premature failure.”
Large cracks and splits in the rubber will all be readily apparent.
“Road debris, improper ride height and worn shocks can lead to damaged air springs,” Meritor’s Bernens noted. “Check air springs for punctures from road debris, abrasions or internal blind nut punctures. If an air spring has been over extended or suffered a blind nut puncture, then inspect that the vehicle is set for the correct ride height.”
You’ll need to take the overall lifecycle into account as well.
“Over time, the rubber bellows can lose its elastomeric qualities and may start deteriorating,” Boden said. “Exposure to high temperatures can also cause the rubber material to age prematurely. Older air springs can also exhibit weather checking, also referred to as dry rot, and the evidence for this looks like small, fine cracks on the surface of the air bag.”
Boden noted that contaminants like moisture or oil that have entered the system are a top cause of air valve malfunctions. If present, you’ll notice a sticky resident inside the air-handling components.
“The use of air driers in the system can help alleviate the problem with moisture and I would recommend this, particularly for those vehicles that frequently experience changes in climate,” Boden said. “Technicians should look at ride height for indicators of a malfunctioning valve. If the ride height is too high, the valve may not be exhausting air from the bladder properly. If the ride height is too low, the valve may not be admitting air into the bladder.” 3: Shock absorbers
When it comes to air spring suspension shock absorbers, SAF-Holland’s Hicks stressed: “Visually inspect the shock absorbers at least weekly. The visual inspection allows you to easily see when a shock is leaking.”
“Worn out shocks will lead to increased wear on other components to include the air spring. Regularly check the shock to make sure that it is preforming its function,” Meritor’s Bernens said.
“Use caution,” Hicks warned. “The lower shock body could be hot when touching it after the trailer has been operating.”
Your productive shock mileage my vary, but Link’s Boden noted that you should expect to replace shocks approximately every 100,000 miles. Hicks added that the shock absorbers will wear out before typical rolling lobe air springs.
Don’t forget the small stuff, or it can haunt you.
“Replace worn bushings immediately to prevent damage to other components,” Bernens said. “Improper pivot bolt torque will lead to damage to adjacent components. Always ensure your pivot bolts are torqued to the manufacturers’ specifications.”
Hicks noted that required bushing maintenance can vary depending on application.
“For instance,” he said, “the front pivot connection bushings are critical to the life of the suspension. The pivot fastener must provide sufficient clamp load through the bushing to prevent premature bushing and/or bushing core failure. Therefore, it is a good practice to re-torque the pivot connections every time you do a routine brake job, or every 50,000 to 100,000 miles. In severe-duty applications, where brake jobs are performed more frequently, it is important to check torque more often.”
Click here to read how suspension maintenance differs with tractors and trailers.
Volvo Trucks places safety and sustainability at the forefront of every decision we make. It is our responsibility at Volvo Trucks to protect and preserve the finite resources of our planet. While making our business environmentally and financially sustainable, we will, together with our customers, leave a better world to our future generations.
The company says the newest feature of the PPG AdjustRite commercial estimating system can enhance productivity for vehicle repairs.
PPG announced that it is adding the PPG AdjustRite Repair Management tool to its AdjustRite commercial estimating system. The AdjustRite Repair Management platform offers technicians a time clock system and automated tracking of work hours per repair order.
According to PPG, shop managers and estimators can benefit from a centralized approach to delegate tasks, gain insights from productivity metrics and efficiency data, and utilize dynamic charts for a thorough overview of repair orders and technician activities.
The new facility replaces an old location; Premier Truck Group says customers will notice the improvements.
You have to know where to look for the right video training information that’s safe and accurate.
With this partnership, the companies say customers can arm dispatchers and fleet managers with real-time information to improve decision making.
Kodiak’s first freight transfer point at a Ryder facility enables planned deployment of driverless trucks to and from Houston, TX.
Hendrickson offers versions for self-steerable and non-steerable applications, both of which it says drop-in to replace HAC series air kits.
Demonstrated in a ride-along event at TMC, Grote teamed up with Stoneridge to add a new backup camera to its 4SEE system.
The T/T Pair by Phillips aims to enhance tractor-trailer connectivity, security, and maintenance practices.
Maintenance vs. buying new: We weigh the costly pros and cons of keeping your fleet running.
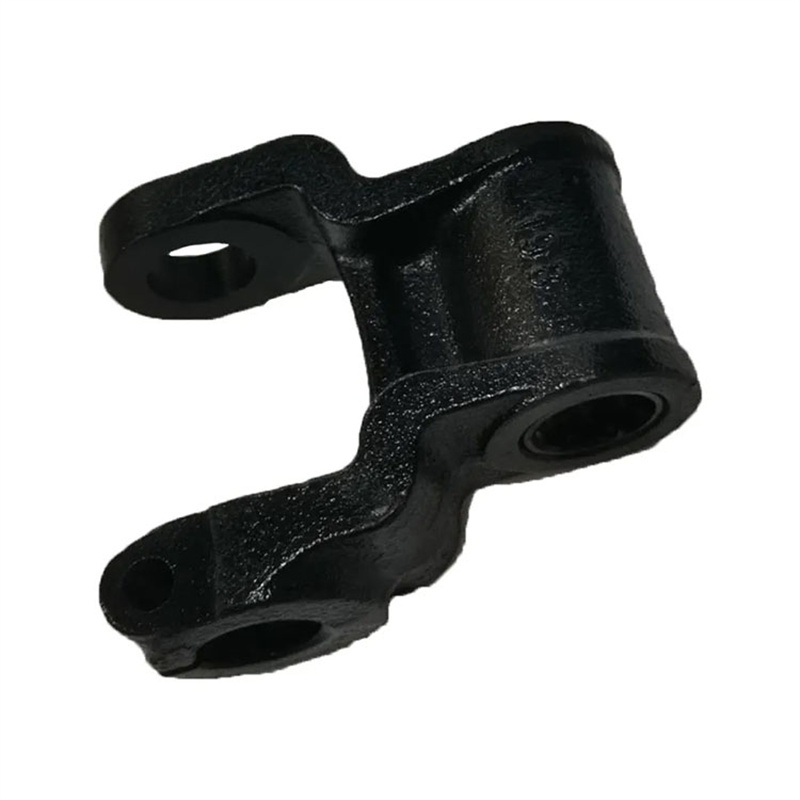
Stainless Steel Spring Pins Truck industry content for fleet owners and managers