MetalMiner Insights includes prices for a full range of carbon steel products including adders and extras by mill. Capabilities include: aluminized, galvanized, galvalume, galvanneal, hot rolled coil, cold rolled coil, plate and electro-galvanized, for North America and many carbon steel price points from Europe, China, Japan and South Korea. In addition, the platform also includes: should-cost models, buying signals, price forecasting (monthly, quarterly and annually), sourcing strategy recommendations and 100+ price feeds. MetalMiner Insights shows companies how to buy, when to buy and what to pay.
Depending on whether or not a company buys mill-direct or through service centers, having access to a database of all carbon steel costs remains elusive. The MetalMiner Insights should-cost models factor in all elements of carbon steel costs including: coating and specification adders, as well as thickness and width adders for the North American market. Aluminium Coated Steel
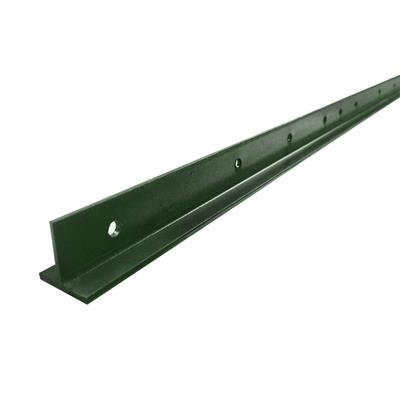
The carbon steel should-cost models contain detailed price adders and extras for a full range of steel grades including: A36, DS, CS 30, 33, 36, 50, 45, 50, 55, 60, 65, 70, 80, 90, 100. The models include the base price and a full range of adders and extras.
US/China/Europe HRC, CRC, HDG and Plate
Korean HRC, CRC, Rebar and Plate
Ignore the noise, but know the trend. MetalMiner’s track record on carbon steel price forecasts, by calling a bullish market or a bearish market means buying organizations can always generate cost savings or cost avoidance.
Some may argue that timing an aluminum buy appears speculative. Spot buying, however, also means speculative buying! Merely having a specific price of aluminum per pound via fundamental analysis (e.g. supply and demand) rarely equates to an actionable buying strategy, particularly with high market volatility. Understanding the aluminum price from a short term and long term perspective allows buyers to alter strategies in falling, sideways, and rising markets – as well as save money by timing the buy.
For new procurement professionals or those that have the exciting responsibility of managing an aluminum category for the first time, this brief on the 5 best practices of metal-based sourcing can help with upcoming supplier negotiations. This brief describes how to use cost breakdowns to separate out the conversion/processing costs from metal prices, why one should buy by the weight vs. the each, the importance of “3” in supply awards and two other best practices all designed to help reduce cost of goods sold.
Have an upcoming negotiation for aluminum sheet or coil? Make sure you know how your service centers will negotiate the aluminum price. Whether you buy 3003 aluminum sheet or 6061 extrusions, a strong understanding of which part of the aluminum price moves with an index and which elements should remain fixed will help mitigate market volatility.
Learn How We Partner With Our Clients
We’re always looking for input, as well as opportunities to expand our offerings to help buying organizations purchasing metal. Interested in steel metal prices and market trends? What about advice on copper prices, negotiations and cost-downs? Reach out to us and let us know!
The goal of MetalMiner is to help manufacturers better manage margins. In addition to this, MetalMiner also assist companies in generating cost savings and cost avoidance, smoothing out volatility and meeting profitability targets. We use data – data science, data analysis, artificial intelligence, statistical analyses as well as technical analysis to provide buying organizations with specific actionable buying guidance. When used consistently, MetalMiner’s buying guidance affords companies both cost savings and cost avoidance opportunities.
MetalMiner helps buying organizations better manage margins, smooth commodity volatility, generate cost savings and negotiate prices for metal commodities. The company does this through a unique forecasting lens using artificial intelligence (AI), technical analysis (TA) and deep subject matter expertise.

Stainless H Beam ©2024 MetalMiner All rights reserved. | Cookie Consent Settings & Privacy Policy | Terms of Service