A manhole cover was “blown off” the ground Monday morning in Dorchester, damaging a sewer line and a house, according to Boston fire officials.
The explosion happened around 8:15 a.m. in the area of 50 Florida St., officials said in a statement. Electric Riding Lawn Mower

“The manhole cover was blown off and there was fire inside the manhole,” officials said. “The incident caused damage to a building’s sewer line and damage to another house with a broken window.”
No one was hurt and no residents were displaced, officials said.
The Fire Department said Eversource and NStar are working to determine what caused the explosion and “fix the issue.”
Travis Andersen can be reached at travis.andersen@globe.com.
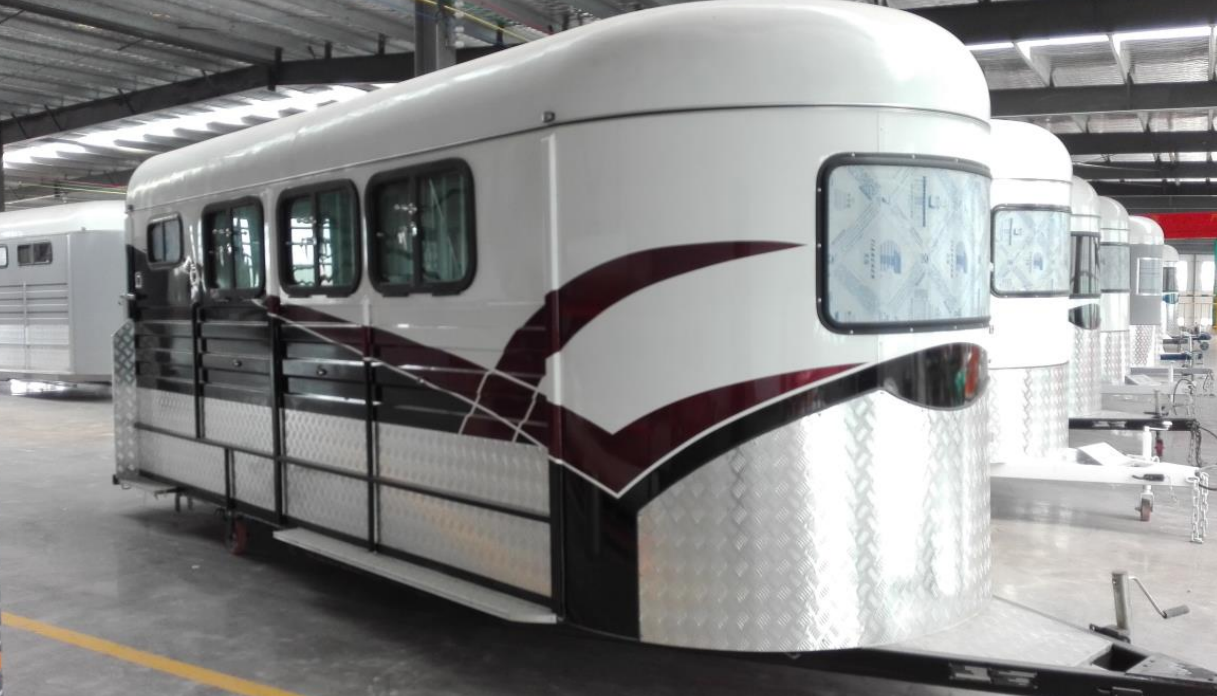
Trade Execution Agent In China Work at Boston Globe Media